Maintenance is crucial, but a lack of resources remains an issue according to respondents for the 2017 Maintenance Survey.
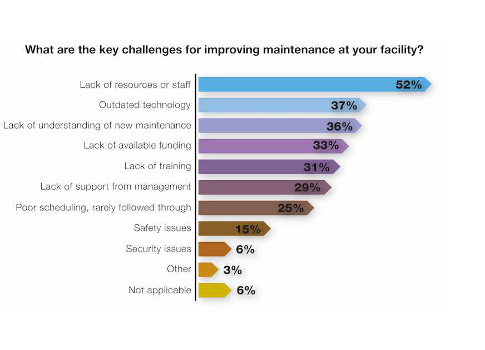
There is a strong message from Plant Engineering readers in the 2017 Maintenance Survey: equipment upgrades and more maintenance training would go a long way to decreasing downtime. But the failure of plant management to address that fundamental issue is seen as a barrier to realizing those improvements.
The 2017 Maintenance Survey, polled Plant Engineering leaders on the challenges and opportunities available in an improved maintenance process. Of survey respondents, 42% said aging equipment was the leading culprit behind unscheduled downtime in their plant; another 19% cited operator error, and 13% said there was not enough time to perform proper maintenance.
Respondents also were clear on how to address these issues:
- 61% said upgrading equipment would decrease unscheduled downtime
- 49% said improved and increased maintenance training would address the issue
- 48% said using a preventive maintenance strategy would lower downtime
- 42% saw an opportunity to improve uptime by expanding monitoring capabilities.
There was pessimism, however, as to whether this issue would be addressed in the near future. The biggest challenge, cited by 52% of respondents, was a lack of resources and staff. Outdated technology was mentioned by 37%, with a lack of training, the needs of new maintenance, available funding and a lack of support of management all called out by about one-third of survey respondents.
"It’s a tight job market, especially when to comes to the skills we’re looking for in high tech," said Jeff Owens, CEO of Advanced Technology Services (ATS), which co-sponsored the survey. "We offer specialized training programs and we’ve outfitted our technicians with tablets and technologies to help them solve complex machine problems."
In the area of maintenance training, safety is the predominant consideration, with 81% of respondents mentioning it. Basic mechanical and electrical skills are covered in about two-thirds of all training. Motors, lubrication and predictive maintenance were cited by more than half of the plant personnel surveyed.
Another area of discussion is the amount of maintenance being outsourced to third-party companies. While 13% of respondents said they do not outsource any maintenance functions, 65% said they outsource at least 30%, and 18% bring in outside help for more than that. Maintenance and plant managers cite a lack of time and manpower, and a lack of in-house specialized skills as the leading reasons their maintenance function is provided at least partially by third-party vendors.
While budget costs are another factor in outsourced maintenance, 30% of managers said skilled maintenance professionals simply were not available for them to hire.
"As factories becomes increasingly automated, maintenance is becoming critical to operations, and more companies are considering it a non-core function," Owens said. "They’re feeling less ownership over it, and instead have begun to focus on things their customers touch and feel, such as product design and features."
What gets maintained?
The Maintenance Survey also found a difference in which areas of the plant get the most attention from maintenance teams. Rotating equipment, such as motors and power transmission, got a lot of attention in 63% of plants, electrical distribution systems only received that level of attention 38% of the time. Automation systems and fluid power equipment also received a high level of attention from more than half of respondents.
While most plant and maintenance managers are using technology to help in their maintenance processes, technology has not been fully embraced in all areas of the plant. A computerized maintenance management system (CMMS) is in use in 53% of plants, and another 52% used in-house spreadsheets and schedules to plan maintenance. But the age of the clipboard is far from over; 39% said they still use paper records as part of their maintenance process.
The benefits of strategy
A run-to-failure strategy in the plant has one distinct advantage over other plant maintenance strategies-its low initial cost, as cited by 61% of respondents. But it gets very low grades for just about every other areas of maintenance benefits, including productivity, downtime and safety. Other the other hand, plant and maintenance managers like preventive maintenance for its impact on decreased downtime (69%), reduced probability of failure (66%), overall equipment effectiveness (63%), improved safety (62%) and overall efficiency (59%). Predictive maintenance ranked highest for decreasing downtime (73%) and reducing failures (73%), while CMMS got the highest mark for overall efficiency (65%).
Those maintenance processes still tend to be a hybrid across a plant, with several strategies in place at once. But in a day where prescriptive maintenance is on the horizon, more reactive maintenance strategies still prevails. Preventive maintenance is used in 78% of plants, while a fully reactive (run to failure) plan exists in 61%. The use of CMMS systems follow, but just 47% of plants utilize an analysis-based predictive maintenance system, and only 28% utilize reliability-centered maintenance.
IIoT and mobility
Two technologies that are being closely watched in maintenance management are the use of handheld devices and the Industrial Internet of Things (IIoT). Plant Engineering’s 2016 Salary Survey released last month found 64% of readers felt that IIoT would improve their maintenance management; the Maintenance Survey found similar sentiments. While 20% felt IIoT would have no impact on their maintenance operation and 24% were unsure what impact it might have, 32% believe it will help understand machine health, 30% said it would change the way plant maintenance is conducted and 27% said it would better help predict and prevent downtime.
Mobility is another area where opinions vary widely. While 29% of respondents said they have no plans to use mobile devices in their maintenance function, 27% are studying such a deployment, 12% use mobility for scheduling, and 9% said mobile devices are fully implemented in the maintenance department.