Phenix Lumber Company has ignored previous 77 citations, ultimately receiving nearly $2 million in fines from the U.S. Dept. of Labor's Occupational Safety and Health Administration.
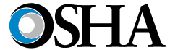
The U.S. Department of Labor’s Occupational Safety and Health Administration (OSHA) has proposed penalties of $1,939,000 to the Phenix Lumber Company and its principal, John M. Dudley, for safety violations, including exposing employees to amputation and fall hazards. Prior to these citations, Phenix Lumber had reportedly been cited 77 times by OSHA for serious safety and health violations since 2007.
“Phenix Lumber continues to put workers at risk by choosing not to implement safety measures that would prevent serious injuries to their employees,” said Secretary of Labor Hilda L. Solis. “Employers have a responsibility to keep their workers safe and healthy. One worker injured on the job is one too many.”
OSHA allegedly began an inspection on December 15, 2010, in response to a complaint that employees working in the planer mill were exposed to amputation hazards while maintaining, cleaning, and clearing jams on pieces of machinery that did not have their energy sources locked out to prevent their unexpected start up. Two months later, OSHA reportedly received a second complaint that an employee had suffered a partial finger amputation while clearing a piece of machinery that had not been locked out. At the opening of an inspection following the second complaint, the compliance officer learned of another employee who had just suffered a severe hand injury while working on unguarded machinery, according to OSHA.
Phenix Lumber is said to have been cited numerous times during the past four years for allowing employees to work on unguarded machinery while it was operating.
“This situation reflects a systemic problem with the way this company approaches safety and demonstrates an egregious disregard for workers’ safety and health,” said OSHA administrator Dr. David Michaels.
OSHA has issued Phenix Lumber 13 citations for 24 willful violations, including failure to properly shut down and lock out 13 pieces of machinery before employees were required to perform tasks such as clearing jams and cleaning. These failures exposed employees to amputation hazards, as well as to the possibility of being caught between or struck by pieces of the machinery and falling lumber.
The employer also reportedly failed to train 11 employees who performed this work on the hazards, covering how to shut down and lock out the machinery so that they could perform their tasks safely.
OSHA proposed the maximum $70,000 penalty for each violation, totaling $1,680,000. Citations for three additional willful violations allege that a worker was exposed to fall hazards while working from the top of a machine, locks were not issued to employees as required by the lockout standard, and the company failed to follow established lockout/tagout procedures. These citations carry additional penalties of $70,000 each, for a total of $210,000. One citation for a repeat violation with a $35,000 fine was issued for failing to place machine guards on seven chains and sprockets. A violation is “repeated” if the employer previously was cited for a substantially similar condition, and the citation is a final, affirmed order of the independent Occupational Safety and Health Review Commission.
This time is the third within three years that Phenix Lumber has been cited for failing to guard this type of equipment, according to OSHA. Citations for two serious violations, each with a maximum proposed penalty of $7,000, were issued for failing to guard a pinch point at a hydraulic pusher plate, which exposed employees to amputation hazards and caused one of the injuries; and to ensure that employees performing lockout/tagout tasks applied and removed their own locks.
– Edited by Kelsey Kirkley, Plant Engineering, www.plantengineering.com