By attaining a clear picture of asset health, facilities can make decisions that reduce downtime, increase output and cut emissions.
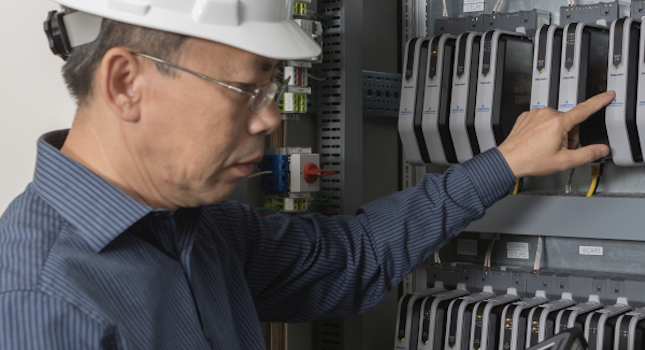
In hydrocarbon processing, refineries and tank farms suffer from inefficiencies that result in serious losses. These losses often take the form of fugitive emissions and downtime due to failure or maintenance. The unplanned shutdowns caused by component failure and unnecessary maintenance decrease a plant’s output, while fugitive emissions contribute to a facility’s carbon footprint.
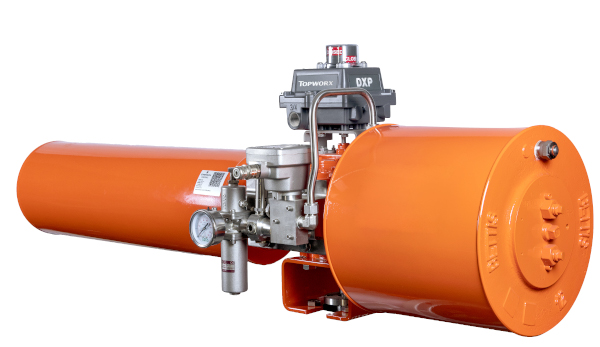
Downtime is expensive in any industry, but the losses refineries experience can be enormous. For every second a plant is down, it could lose up to 14 barrels of possible output, not to mention creating overhead costs. At large refineries, this could be nearly $1,000 per second just in lost output (based on the oil price at the time of publication). Inefficiencies in on-off valve maintenance result in unnecessary downtime and exorbitant costs. Understanding the current condition of on-off valves and performing proactive maintenance is critical to maintaining valves and uptime.
Valve packages typically account for a large percentage of a hydrocarbon processing facility’s fugitive emissions. In addition to contributing to a facility’s carbon footprint, fugitive gas emissions can affect compliance with standards and regulations. Standards such as Senate Bill 19-181 and ISO 15848-1:2015 regulate the leakage and emission of volatile air pollutants and hazardous fluids, which include hydrocarbons. Maintaining compliance makes monitoring tank levels necessary. However, the manual monitoring process is time consuming; it can be difficult for maintenance teams to perform testing often enough to meet regulatory requirements.
Integrating continuous, remote monitoring solutions in downstream applications in refineries and associated tank farms provides operators valuable diagnostics and a clearer, more comprehensive view of their processes and valve package health. Using this clarity, they can quickly make informed decisions that can reduce downtime, unnecessary maintenance and fugitive emissions. In this way, monitoring solutions can improve output, plant efficiency and sustainability (see Figure 1).
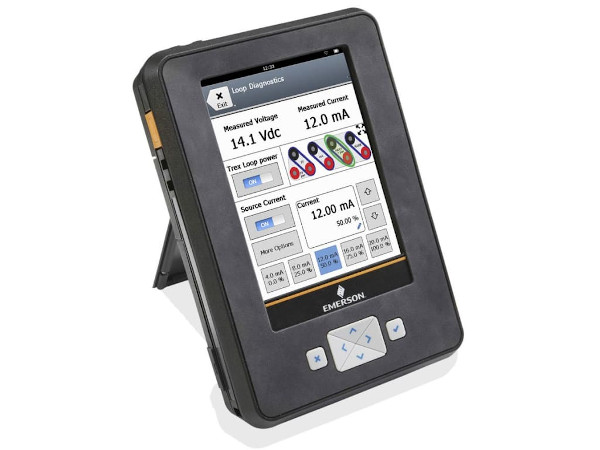
Improve operational processes and increase output
One of the biggest challenges refineries face is they don’t have a way to measure critical parameters. Some have valve packages that are quite old, and there’s no existing infrastructure in place to enable remote monitoring. Turnarounds can provide an opportunity to integrate solutions that start building the infrastructure and shorten these complicated, expensive downtime events.
Many solutions can be used as part of a turnaround to monitor performance or can be connected at a later stage to be implemented into other systems. For example, a discrete valve controller with an integrated HART 7 module can be retrofitted to any existing switchbox solution. The on-off switch can be independent of the HART signal, and a HART 7 solution can be installed for future scope using the existing system’s on-off switch. A hand-held diagnostic communicator can be used to access real-time data from the dormant HART 7 module, since the HART 7 internal memory holds this data under power.
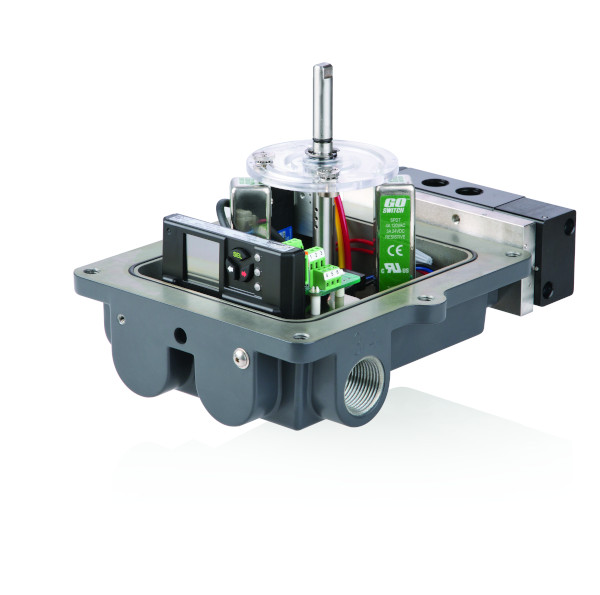
Accessing data with a device communicator allows end users to quickly analyze current valve health and make informed decisions based on that analysis. Confidently knowing valve condition can speed up decision making and action, which can shorten the turnaround.
Mobile device communicators also can help technicians properly diagnose and address problems anywhere within a facility, replacing invasive physical investigation and the potential destruction it causes. Because equipment can continue running during troubleshooting and repair, communicators not only streamline maintenance, they also minimize downtime (see Figure 2).
A discrete valve controller also can be used to monitor parts of a plant. Some manufacturers offer models that use open-source data that allow manufacturers to produce a facility’s graphic data. Facilities can then analyze that data to make decisions that streamline operational processes and increase output (see Figure 3).
By integrating monitoring solutions like these, facilities can increase barrel production by increasing availability. Automated monitoring and measurement make it possible for operators to know the real-time health and condition of critical on-off valve assets. Understanding asset health enables quick, appropriate decision making that can maintain uptime, increase output and improve plant efficiency. By avoiding even a few seconds of downtime each day, refineries can save thousands of additional barrels and hundreds of thousands of dollars in a short time.
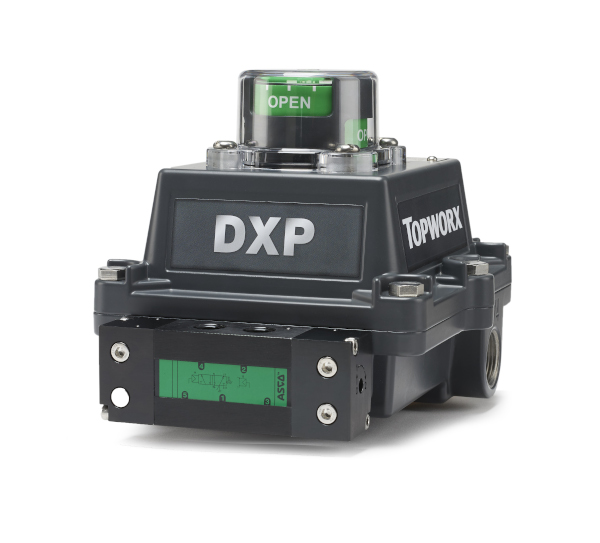
Optimize maintenance and reduce downtime
Shortening the length of turnarounds is one way to improve plant efficiency. Another way is reducing the need for turnarounds and shutdown maintenance in the first place. Yet, on-off valve assets in many plants require frequent maintenance and support to prevent catastrophic failure. Understanding actuator and valve wear through remote monitoring and diagnostics can make this maintenance more efficient, helping decrease downtime and costs.
To do this, facilities can use a discrete valve controller that combines sensing and feedback in a single housing to improve the visibility of valve package condition and deliver diagnostics. This integrated switchbox solution includes a sensor, HART 7 module and other components such as a solenoid valve for piloting. In process facilities, it sits on top of an actuator/valve assembly, where it continuously monitors assembly performance in real time and enables the delivery of preset diagnostics vital to assembly health (see Figures 4 and 5).
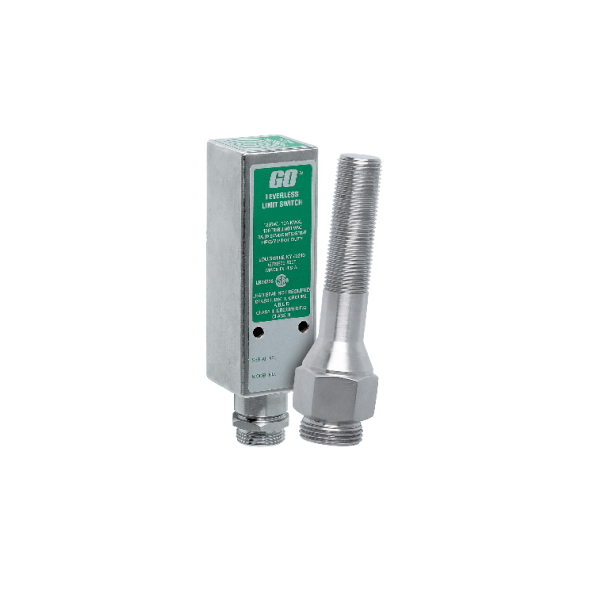
The sensor collects data the HART module then transmits to a control system. The control system then delivers analytics and diagnostic notifications to handheld devices or workstations. There, operators and technicians can see the data in dashboards and receive alerts, make decisions and take appropriate action. Critical parameters that reveal the current state of valve and actuator wear include valve state measured by position percentage, transition dwell time, last open/close stroke time, internal device temperature and cycle count. Operators can continuously observe these factors to assess current conditions, determine remaining life expectancy and maintain assets as they age (see Figures 6 through 8).
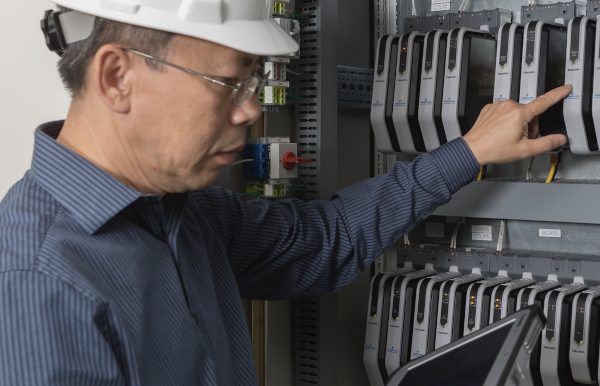
For example, a technician can use the cycle counter function and stroke time monitoring to observe valve performance. Once a valve opens and closes a designated number of times, a preset notification will alert personnel to check the valve during the next routine maintenance run. If an operator notices a valve that took five seconds to open six months ago now takes 10 seconds, the operator can take action that appropriately maintains the valve and prevents failure.
Through continuous remote monitoring and delivery of diagnostics, this type of solution enables facilities to cultivate proactive rather than reactive maintenance programs. Instead of running components to failure or replacing them at time-based intervals, both of which incur unnecessary downtime and costs, personnel can use insights from data and alerts to perform informed routine maintenance. Continuously monitoring the health and condition of the actuator/valve assembly remotely and responding to diagnostics prevents unnecessary maintenance and the removal of healthy components, reducing downtime and costs.
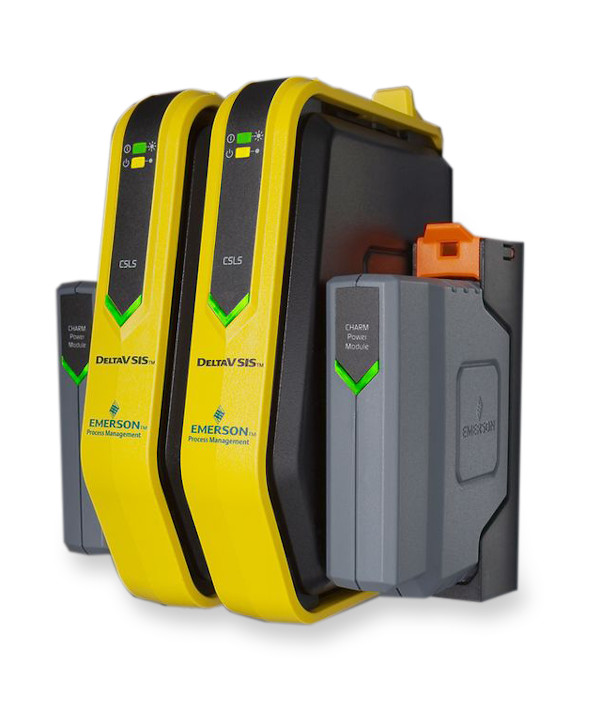
Identify and reduce fugitive emissions
A crucial part of maintenance is identifying leaks. In typical processing plants, worn or misaligned valve packing is a leading source of leakage. Traditional emissions monitoring is a manual process in which a portable analyzer is used to take periodic measurements around all installed equipment. This is a time-consuming process, and, with smaller teams of in-house maintenance personnel available, completing the tests frequently enough to meet regulatory requirements can be challenging.
By enabling proactive maintenance, fugitive emissions also can be identified and reduced by the continuous remote monitoring and diagnostics enabled by a discrete valve controller with integrated HART 7 module. Key variables that serve as indicators of a valve’s condition and can reveal leaks include valve cycle count, stroking speed and time span of travel. Evaluating these trends establishes a nominal baseline that allows operators to perform ongoing comparative analysis. A change in baseline parameters prompts warnings and alarms, usually indicating a broken valve stem or plug, seal leaking, flashing and packing wear that maintenance personnel can repair to seal leaks earlier.
In this way, continuous monitoring and diagnostics allow facilities to identify faulty valves more quickly and make quicker repairs that reduce fugitive emissions.
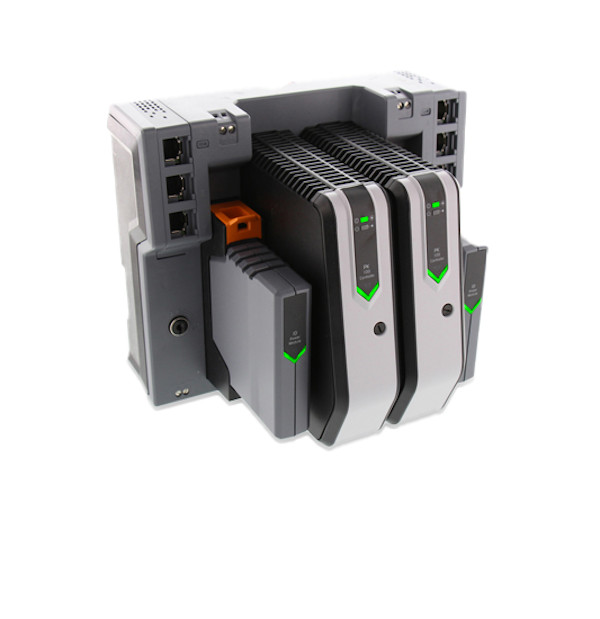
Improving plant efficiency
While integrating monitoring solutions is the first step to improving processing plant efficiency, it’s important that technology is backed by a supplier with extensive hydrocarbon expertise and proven success digitally transforming plants. Expert partners have comprehensive portfolios that include products specifically designed to support the most demanding and extreme conditions.
Continuous remote monitoring of key parameters and valuable diagnostics empowers plants and tank farms to manage and control their operations more intelligently and efficiently. By having a clearer picture of processes and equipment health, operators can make critical decisions and act in ways that significantly reduce downtime, improve output and cut emissions. The efficiency gained drives more profitable and more sustainable operations.