Having the right technology and a safe and smart workplace with competitive wages helps with labor shortages.
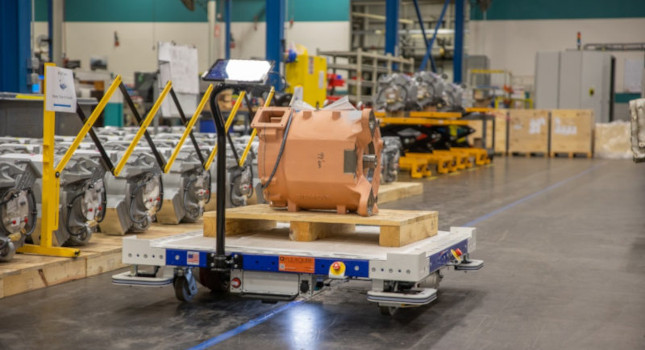
The global warehousing market is on the rise. According to Beroe Inc, the global demand for a warehouse was significantly increased in 2021, and the estimation is that the warehousing market will reach $285 billion in 2022 and $326.3 billion by 2024.
This means that staying competitive within the warehousing industry requires increased efficiency for logistics and operations. One of the main trends that started shaping the warehouse of the future is most certainly automation and usage of advanced technology on the warehouse floor.
Technology is helping that goods are packaged and transported efficiently and safely, and demand for technology driven material handling equipment is also increasing.
Though the warehouse industry was highly dependent (and still is) on human labor – according to Interact Analysis – material handling robots are going to penetrate the market and reduce the need for workers.
Also, by implementing material handling robots like automated guided vehicles (AGVs) or autonomous mobile robots, warehouse managers will be able to cut costs, increase safety and allow workers to focus on more essential tasks.
Consider these five ways in which material handling equipment can impact warehouse efficiency.
1. Warehouse cost savings
Warehouses can leverage automation to enhance efficiency in their operations leading to lower costs. These can be robots, smart machines, automated guided vehicles or lightweight material handling equipment.
A warehouse facility should identify the different types of material handling equipment and devise a plan to identify and use the right one to enhance their operations. A system that coordinates inputs and outputs is the most effective in cutting costs.
According to Inbound Logistics, labor costs make up about 65% of warehouse operational budgets. The suitable material handling equipment will reduce labor costs and, at the same time, enhance safety, reducing costs associated with workplace injuries.
The correct warehouse material handling equipment can reduce costs in the following ways:
- Labor costs: Some material handling operations, such as picking are labor-intensive and costly. Warehousing managers can use automated robots for such activities.
- Floor space costs: Machines, such as forklifts, can optimize your floor space by using the facility’s height to store inventory vertically. Reach truck AGVs and very narrow aisle AGVs eliminate the footprint required to store and access materials.
- Picking costs: Automation facilitates batch picking and enables facilities to process group orders with common items. This is an excellent alternative to humans, who can only fill one order at a time.
- Workplace absences and injuries: Material handling equipment enhances safety and reduces workplace injuries. In addition, machines can work continuously for long hours without breaks or off days.
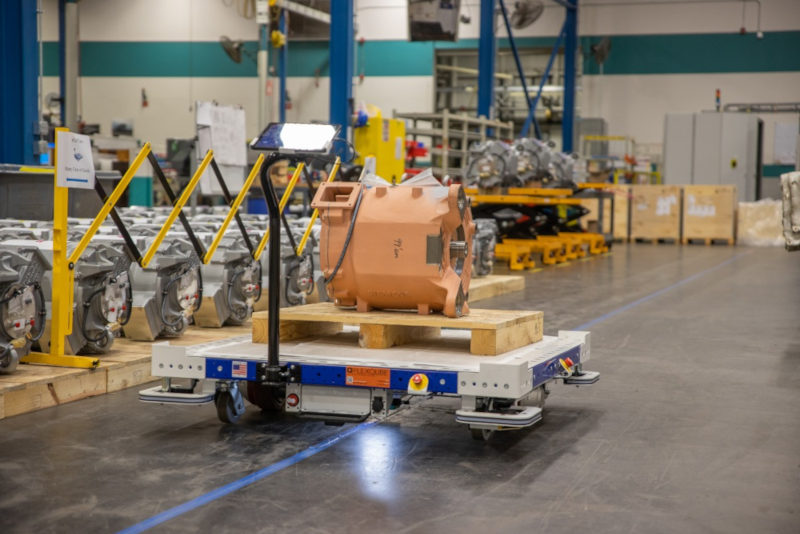
2. Helps in streamlining warehouse processes
It helps when a warehouse is organized to provide the best flow of materials. Ideally, the material should be accessible with few risks and errors in the shortest time possible. But how does someone achieve this when they are handling so much material?
Automation and material handling equipment allow people to streamline their warehouse in several ways:
- Simplify process: It may take a lot of time to get to the shelf, identify what is needed and collect it. However, robots can handle those tasks quickly and accurately.
- Proper labeling: Proper labeling of items within a facility is essential. Bar code labels can be used to identify items. In addition, AMRs equipped with bar code scanners can locate, identify and track the movements of items.
- Record the movement of materials: When materials are properly labeled, it becomes easier to track their movement. This will also eliminate unnecessary movements.
3. Enhances warehouse inventory management
Management of warehouse inventory consists of receiving, storing and tracking inventory. How materials are managed in a warehouse influences efficiency and costs. Here are a few tips to help enhance inventory management in a warehouse:
- Automate inventory systems
- Have regular inventory control checks
- Use demand forecasting
- Train the employees.
Using automated storage and retrieval systems to manage inventory
Material handling equipment allows warehouses to incorporate automated storage and retrieval systems (AS/RS) within their facilities. This system consists of various machine control systems that automatically store and retrieve items from set storage locations.
In AS/RS, inventory is stored on portable shelving, which can easily be retrieved from storage and transported to an employee access area by a fleet of autonomous mobile robots (AMRs).
After the employee picks the required items from the shelf, the AMRs return the others to storage. The AMRs are equipped with sensors, scanners and Internet of Things (IoT) devices to keep track of the items they distribute within the facility. The system works with speed, precision and accuracy, enabling enhanced inventory visibility.
Use of software in inventory management
Material handling equipment is essential in complex distribution environments. The equipment, along with customized warehouse management systems (WMS) that manage them, have enhanced the efficiency of warehousing and distribution. The integration between material handling equipment and Warehouse Execution Systems has enabled accurate and timely reports on inventory levels and forecasting, which are essential in inventory management and control.
4. Improves workplace safety
Most of the material moved across a warehouse floor is bulky and heavy. Moving materials without the right equipment can cause injuries to employees or damage the materials.
According to the U.S. Bureau of Labor Statistics, the average number of injuries per 100 full-time workers in the warehousing industry was 4.8 in 2020. Providing suitable material handling equipment can improve safety and significantly reduce accidents and injuries on the warehouse floor.
Heavy lifting can potentially cause lifelong injuries. Therefore, managers must help reduce the number of materials workers handle manually to reduce potential hand and back injuries.
Some materials, especially chemicals, could be light but potentially hazardous to humans. Warehousing facilities should provide suitable types of equipment that limit human contact with those materials. Automated conveyor belts that use integrated automation systems are ideal for handling hazardous materials.
Material handling equipment can also minimize damage to the facility floor, walls or other machines and equipment within the facility. Heavy and bulk material can easily damage the floor or walls during transportation if they are not handled correctly. Warehouses should provide the ideal equipment for handling materials.
An added benefit of increased safety: Cost savings
It has been estimated that employers pay almost $1 billion per week for direct workers’ compensation costs, including direct and indirect costs. Direct costs include workers’ compensation payments, medical expenses and costs for legal services.
Examples of indirect costs include loss in productivity, employee morale, training new workers, accident investigation and implementation of enhanced safety policies.
5. Motivate employees
As mentioned, implementing the right material handling equipment on the plant or warehouse floor will help workers to perform their tasks faster and more efficiently, which can lead to increased employee morale.
Moreover, by investing in material handling equipment like AGVs, there can be less employees but more skilled workers – employers can offer more competitive salaries and therefore, a much more attractive workplace. Employers should offer a workplace that is safe, where workers are properly trained to work with the latest technology.
In the long run, investing in this way is becoming more and more profitable because one of the greatest challenges plant or warehouse managers face is solved and that is a labor shortage. The warehouse and transportation industry had a record 490,000 fewer workers than needed in 2021 in the U.S. and according to Forbes, this gap will only widen.
Having the right technology, safe and smart workplace and competitive wages is a way to tackle this challenge and be ready for the what future brings.
Material handling’s impact grows
According to Fortune Business Insights, the global market for material handling equipment is expected to reach 300.21 billion U.S. dollars by 2028 at a compound annual growth rate of 5.5%.
The technology continues to improve the performance, design and functionality of material handling equipment, which also impacts warehouse efficiency.
Warehouses will have technologies that allow people to maintain a real-time and accurate digital inventory. The future will have smart warehouses, where automation is seamlessly integrated into all warehousing processes.