Personal protective equipment (PPE) serves as the last line of defense between most hazards and employees and requires innovative strategies to improve PPE program success as companies strive for zero injuries in the workplace.
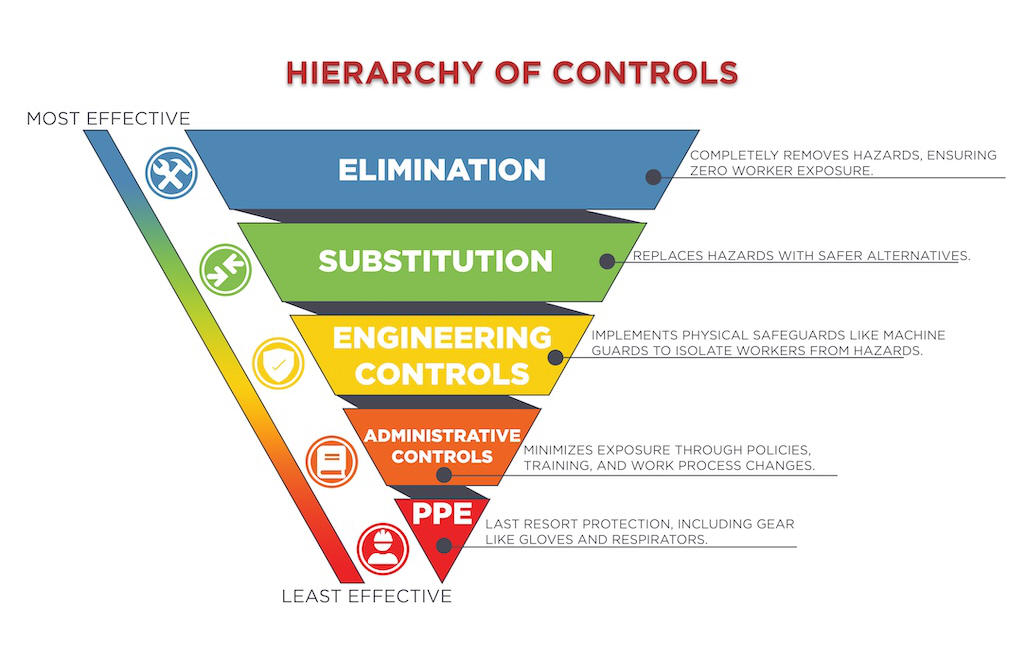
Learning Objectives
- Understand the employer and employee responsibility for PPE & OSHA standard and how to perform PPE assessments.
- Learn about compliance-driven programs and how they can provide positive results as well as understand the potential dangers and unintended consequences of a program.
- Understand how employee-driven programs can be effective with proper communication and training to help ensure long-term success.
PPE insights
- The surge in violations for inadequate eye and face protection, plus increased respiratory protection citations, signals a critical need for more effective PPE programs.
- PPE isn’t just about compliance; it’s a frontline defense. Effective programs involve comprehensive hazard assessment, employee training, and a culture of shared responsibility.
- Contrasting compliance-driven and employee-driven PPE approaches highlight the importance of blending structure with participation for legal compliance and a safety-focused culture.
The Occupational Safety and Health Administration’s (OSHA) top 10 most frequently cited standards for 2023 reveal a concerning trend: there were 2,074 violations cited for inadequate eye and face protection alone, marking an increase of almost 700 violations compared to the previous year. Aside from this, respiratory protection was cited more this year with nearly 300 violations more compared to last year. This sharp rise may indicate a pressing need for more effective personal protective equipment (PPE) programs.
In this article, we will address the challenge of getting employees to consistently wear PPE properly by examining two contrasting approaches to implementing PPE programs: compliance-driven versus employee-driven. As we delve into the dynamics of PPE usage in the workplace, it becomes evident the path to enhanced safety lies not only in strict adherence to OSHA standards, but also in fostering a culture where employees take ownership of their personal safety.
Importance of PPE in the workplace
PPE is more than just a compliance requirement; it is a vital line of defense against workplace hazards, reducing the risk of injuries, and fostering a more productive work environment. PPE includes protective gear such as gloves, respirators, hard hats, goggles, and protective clothing that act as a barrier between workers and potential dangers. Each type of PPE is designed to mitigate specific risks, such as physical impact, chemical exposure, electrical hazards, and environmental elements. The proper selection, use and maintenance of PPE are essential in creating a safe workplace, underscoring the need for effective PPE programs.
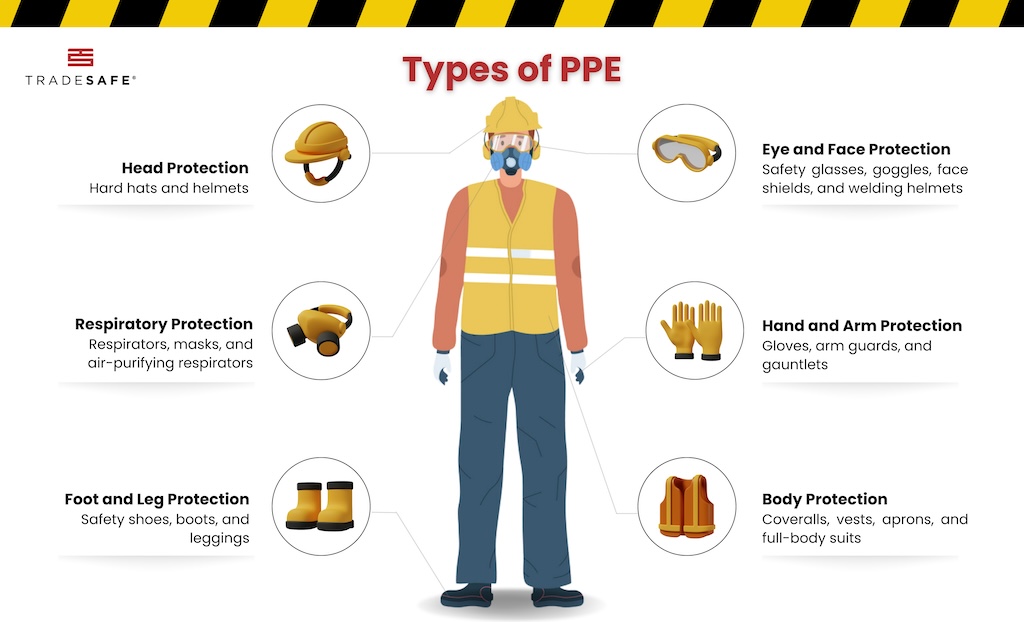
Navigating PPE & OSHA standards
The Occupational Safety and Health Administration (OSHA) requires employers to protect their employees from workplace hazards. Having the hazard eliminated or controlled at its source is the most ideal way to protect employees, however, when these are not possible or do not provide enough protection, employers are mandated by OSHA to provide appropriate personal protective equipment (PPE) to their workers at no cost. This is in line with the hierarchy of controls wherein PPE is placed at the bottom as the last resort for protection against hazards.
Employers are responsible for conducting a thorough hazard assessment to identify and control physical and health hazards, providing appropriate PPE, training on its correct use and maintenance, replacing worn or damaged PPE, and updating the effectiveness of the workplace’s PPE program. Providing PPE is not enough; employers must also enforce its use and evaluate the adequacy of the equipment in relation to the evolving workplace hazards.
While employers are responsible for providing and maintaining PPE, employees also play a crucial role in ensuring their own safety. OSHA standards emphasize that employees must wear PPE correctly to protect themselves from injuries and exposure to harmful substances in hazardous environments. Employees are also required to attend training sessions on PPE use, covering aspects like donning and doffing procedures, and understanding what to do in case of PPE malfunction. Moreover, workers are responsible for cleaning and maintaining their PPE, and informing their supervisors when there is a need to replace or repair the protective equipment.
Although employers and workers have different responsibilities required by OSHA, they are both involved in a critical aspect of PPE programs: the PPE assessment process. This involves identifying potential hazards in the workplace and determining the appropriate type of PPE needed to mitigate these risks. The assessment should be comprehensive, involving employer and employee input, and should be regularly updated to reflect changes in work processes, equipment, and external regulations.
Understanding the distinct roles of employer and employee in PPE programs and assessment sets the stage for a deeper understanding of two contrasting approaches to PPE programs: compliance-driven and employee-driven. While these approaches are aimed at ensuring safety, they differ in their execution and impact on workplace culture and safety efficacy.
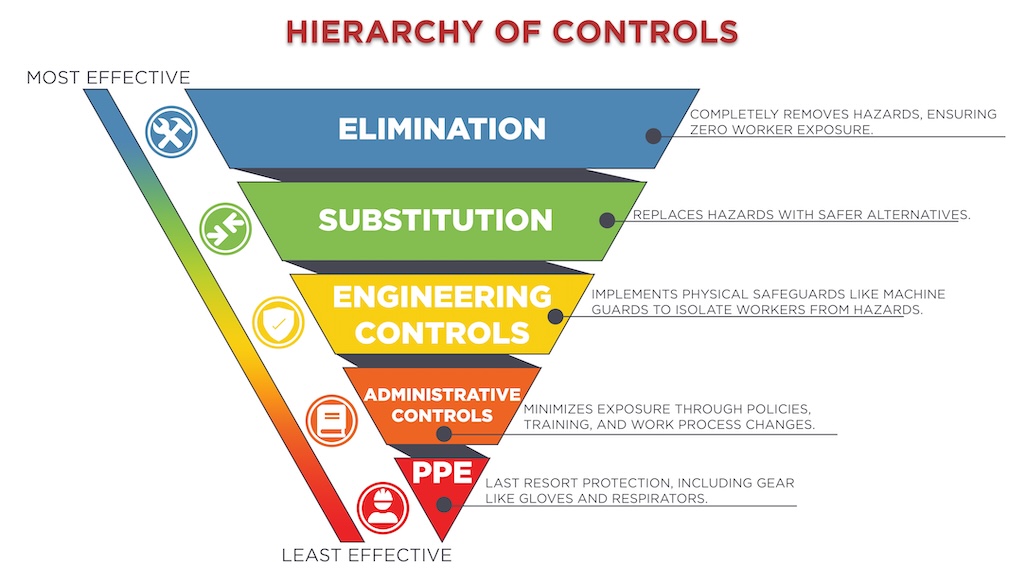
Compliance-driven PPE programs
Compliance-driven PPE programs primarily focus on meeting the set standards and regulations as mandated by OSHA. These programs, governed by strict adherence to rules and guidelines, prioritize legal conformity and a top-down approach to safety management, often centering on the employer’s responsibility to provide and enforce the use of PPE. This approach, while effective in meeting regulatory requirements, brings into question the level of employee engagement and long-term effectiveness in fostering a comprehensive safety culture.
Benefits of compliance-driven programs include ensuring organizations meet the minimum safety standards set by OSHA, thereby reducing the risk of legal penalties and enhancing the basic safety of the workplace. By following these guidelines, employers can systematically address a range of workplace hazards and equip workers with the necessary protective gear. This approach provides a structured framework for PPE management, streamlining the process of hazard identification, PPE selection, and training, which is crucial in large and complex industrial settings.
However, a compliance-only approach to PPE can lead to a superficial understanding of workplace safety, where the focus is on ticking boxes rather than addressing the specific needs of the workforce. Such programs may fail to adapt to unique or changing conditions in the workplace, potentially leaving gaps in worker protection. Furthermore, this approach can cause a complacent attitude towards safety, where the presence of PPE is equated with a safe working environment, even if the equipment is not adequately suited to the tasks or not used correctly by the employees.
While compliance-driven PPE programs are intended to provide a baseline of safety, they can sometimes lead to unintended consequences, such as a disconnect between workers and management regarding the practicality and comfort of the provided PPE. However, an intended positive consequence is the establishment of a clear and consistent safety protocol, which is important in industries with high risks. Yet, the rigidity of such programs can inhibit employee feedback and participation, potentially overlooking innovative and more effective safety solutions employees might suggest based on their on-the-ground experience.
Table 1: Employers’ Versus Employees’ Responsibilities
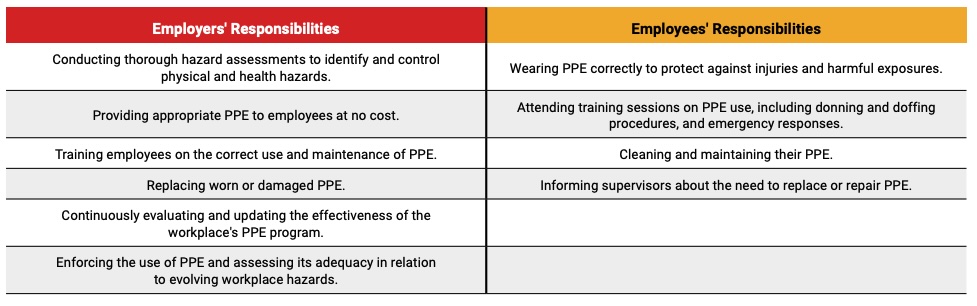
Employee-driven PPE programs
In contrast to the structured compliance-driven approach, employee-driven PPE programs offer a more dynamic and participatory model of safety management. This approach leverages the insights and experiences of employees to create a more adaptable and effective PPE program. By involving employees in the decision-making process, these programs enhance compliance and foster a sense of ownership and responsibility toward workplace safety. Consider these three PPE programs that take on this approach:
-
Participatory PPE selection committees: By forming committees that include representatives from various employee groups, companies can ensure the PPE selected is both suitable for the specific hazards of the job and comfortable for daily use. This inclusive approach leads to higher employee satisfaction and compliance with PPE usage.
-
Peer-led safety training sessions: Utilizing knowledgeable and experienced employees to lead safety training sessions can create a more engaging and relatable learning experience. Peer trainers can share real-world experiences and tips, making the training more practical and impactful.
-
Employee-led safety audits: Empowering employees to conduct regular safety audits allows for continuous feedback and improvement of PPE programs. These audits, led by the employees themselves, can identify unseen hazards and practical challenges, ensuring PPE programs evolve with the changing needs of the workplace.
When it comes to the success of any employee-driven PPE program, effective communication is crucial. Regular, open dialogues between management and employees ensure PPE programs remain relevant and effective. Training, in this context, goes beyond mere instruction on how to use PPE; it involves educating employees about the rationale behind PPE choices and encouraging them to voice their concerns and suggestions. This level of engagement not only enhances understanding, but also builds a culture of safety where employees feel valued and heard.
The long-term success of employee-driven PPE programs lies in their ability to adapt to changing workplace conditions and employee needs. By involving employees in the continuous assessment and improvement of PPE programs, companies can ensure these initiatives remain effective and relevant. This approach also fosters a proactive safety culture, where employees are active contributors to the safety dialogue. This leads to heightened safety awareness, reduced accidents and a more harmonious relationship between management and employees regarding workplace safety.
The challenge of ensuring consistent use of PPE in the workplace calls for innovative strategies that strike a balance between the structured approach of compliance-driven programs and the participatory nature of employee-driven programs. Such a combination approach would include the strengths of both models for legal compliance while also fostering a workplace culture where employees feel involved and invested in their safety.
For instance, a combined strategy could involve setting up a compliance framework based on OSHA standards, within which employees participate in selecting and evaluating the PPE. This could be facilitated through joint committees comprising both management and employee representatives to make sure the selected PPE is not only compliant with regulations as well as practical and comfortable for the workers. Training programs could also be designed to blend formal compliance education with peer-led sessions, where experienced workers share practical tips and insights, making the learning process more relatable and effective.
Table 2: Compliance Versus Employee-Driven PPE Programs
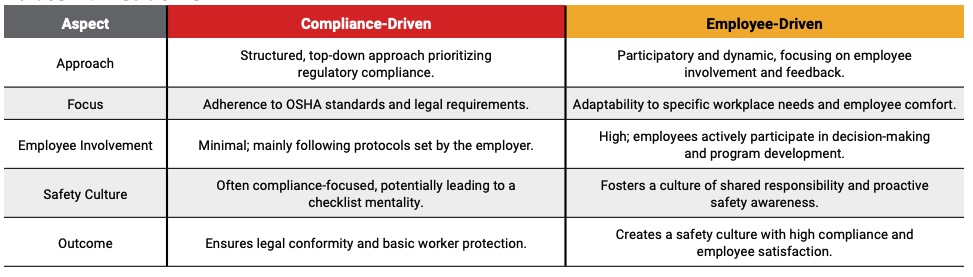
Incorporating technology, such as digital feedback tools or apps, can bridge the gap between compliance and employee-driven approaches. These tools can provide a platform for employees to report issues, suggest improvements, and receive updates on PPE usage and safety protocols. This ongoing dialogue creates a sense of ownership among employees, encouraging them to adhere to PPE protocols not just as a compliance requirement but as an integral part of their daily work routine.
By combining the structure of compliance-driven programs with the adaptability and employee engagement of employee-driven approaches, organizations can create a robust and resilient safety culture that not only meets regulatory standards, but also protects and values its workforce.
TradeSafe is a CFE Media and Technology content partner.