Consider these 5 steps in creating your culture of safety and excellence.
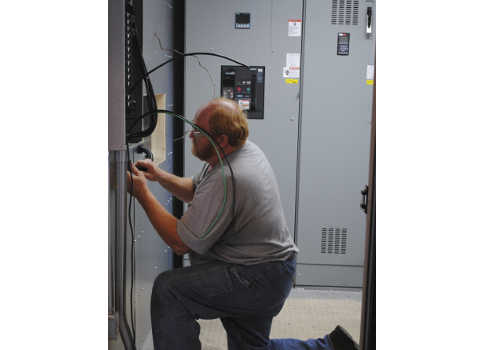
Manufacturing 100 years ago was dangerous. Even 30 years ago, too many people lost eyes, fingers, or their lives. Now, no one should get injured on the job. It is completely preventable. But human beings still get hurt and die while on the job.
Safety is a concern for every manufacturing company, even if it’s only for legal reasons. The heartless drag their feet—and place employees in danger—as they begrudge meeting even minimum safety requirements. Companies like those are why OSHA (Occupational Health and Safety Administration) was created. If everyone was decent, those regulations would be superfluous.
Most manufacturers in developed countries willingly comply with workplace safety rules because they believe the laws appropriate. For some, safety may not be an area of focus, but their intentions are honorable.
Legitimate business leaders care about employees and absolutely want them safe and healthy. The best manufacturers-those committed to total excellence-create a culture of safety. They understand that great processes, products, and people cannot co-exist with an unsafe work environment. A few companies, such as Alcoa, have used safety as a lever to drive outstanding processes. The best also demand safe work environments in their supply base.
Consider these five steps in creating your culture of safety and excellence:
1. Foundational education
Entry-level safety requires compliance with regulatory intent, as well as the letter of the law. OSHA and many factory insurers provide free or very inexpensive education for all your employees. Use it. Failure to support this basic training is dereliction. Those companies still exist, but I wouldn’t want anyone I care about to work for them. Would you?
2. Comprehensive education
Educating employees on all aspects of work-related safety, including ergonomics, can eliminate injuries. Take the time to explain the "why" of all PPE (personal protective equipment) and never make exceptions to it. Too often, I see construction workers performing jobs like sawing wood or pouring cement without protective eyewear. If management at your company allows that kind of irresponsible behavior, find new management or find a new job. Responsible management that cares about employees wouldn’t let that happen. It would say: "Wear your PPE, or find another job."
3. Personal responsibility
Safety is a choice. Management can provide all the education and protective equipment in the world-but an employee committed to violating safety rules will do so. No employee wants to be hurt, but many believe they can do something safely without adhering to safety rules. Every individual makes the decision to be safe or not. Ensure anyone seen acting in an unsafe manner is taken aside, coached, and not allowed to continue that way. Don’t let anyone think you care so little about them that you would let them behave unsafely. That includes office personnel and visitors walking through controlled areas. Anyone repeatedly choosing to be unsafe is choosing a different place to work.
4. Problem solve
Many companies use A3 or 8D or the 5 Why’s to understand and solve production problems, but too few use those same root cause, rigorous problem-solving techniques to prevent future accidents. When accidents or near-misses occur, treat them with a disciplined approach. Instead of saying "the employee was careless," find out why! Were the gloves or eye protection too far away, and he didn’t want to take the time to go get them? You can easily fix that by providing PPE supplies at point of use. Take the time to identify root causes and countermeasures that prevent reoccurrence. Filing government reports is insufficient. Put as much brainpower into problem-solving safety issues as you put into quality or productivity challenges. And don’t wait for someone to get hurt. Use that same thinking to identify potential injury situations and change them.
5. Extend the reach
Safety does not end at the gate. I have visited manufacturing plants in one of Mexico’s more dangerous cities. Management there puts as much emphasis on safety outside the facility as in it. Instead of worrying about nickels and dimes, one manufacturer I know encourages team members to take eye protection home to use when mowing the lawn. Another provides a high quality car seat to every new baby born to an employee. Your coworkers may face health concerns from poor diet, stress, and lack of exercise. You can help them return to work as healthy as they left through positive-lifestyle training and incentives. Is it your job? I don’t know. How much do you care about your employees? If workers are expected to go "above and beyond" perhaps leadership should also.
Accidents may still happen, but an excellent company moves beyond policies and rules to create a culture of safety. It is important to show true caring by preventing potentially dangerous behaviors.
Who are you willing to see get hurt today?
If the answer is no one, then create a culture that demonstrates that and tell every employee nothing else is acceptable.
– Rebecca Morgan is an AME author and president. This article originally appeared on Association for Manufacturing Excellence. AME is a CFE Media content partner.