Safety in manufacturing facilities takes many forms and it is critical companies do all they can to ensure their workers are safe.
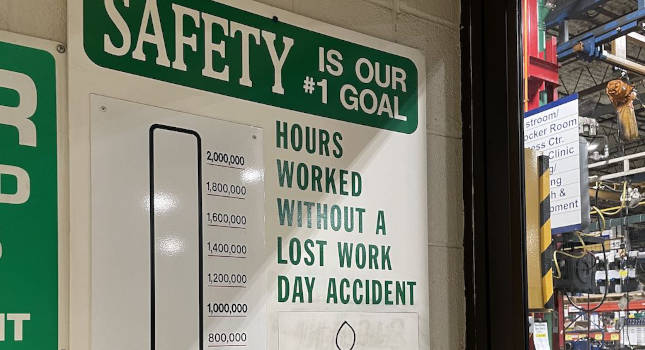
RESPONDENTS
- Jeanie Downs, Environmental, Health and Safety Manager, Hitachi Global Air Power US, LLC, Michigan City, Indiana
- Zack Mitchell, Assistant Corporate Safety Manager, Stellar, Jacksonville, Florida
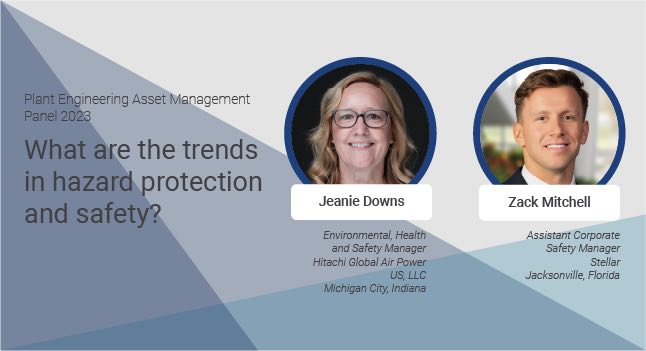
What are some of the current hazard protection trends for industrial and manufacturing facilities?
Zack Mitchell: Training, personal protective equipment (PPE), safety equipment (eyewash, handwash, etc.), housekeeping and ventilation are among some of the trends we see.
What future trends should engineers, plant managers and designers expect for hazard protection?
Zack Mitchell: Fire protection systems will continue to evolve with advanced technologies and improved detection systems. Ventilation systems will see advancements to enhance air quality and remove hazardous substances more effectively. The incorporation of permanent fixtures for constant waterflow, such as eyewash and handwash stations, will become more prevalent to ensure immediate access to emergency decontamination. Additionally, the use of disposable PPE will likely increase, providing convenience and minimizing the risk of cross-contamination.
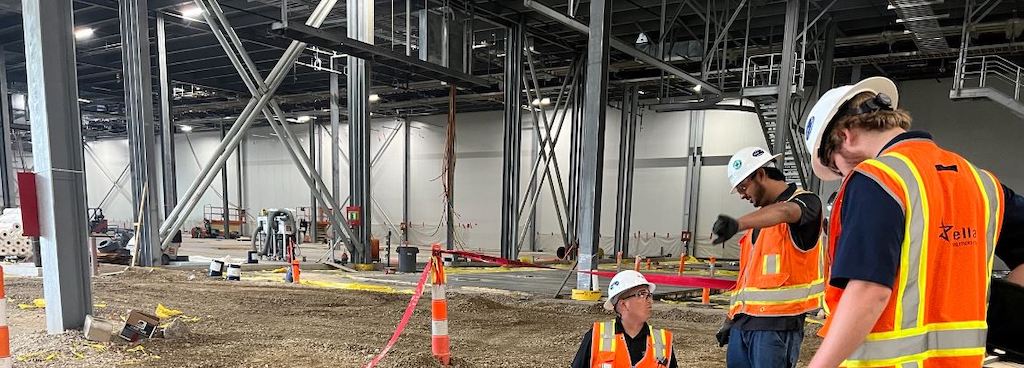
What types of computer applications are in use to support your hazard protection functions?
Jeanie Downs: We use a system that divides our risk categories by module (environmental, etc.) It then assists in tracking our incidents and near misses as well as our corrective actions, requiring completion of the corrective action(s) before we can close out the incident. It also helps us track that our contractors — and their employees — are up to date on safety requirements. The cloud-based software also comes with a compliance calendar that tracks our regulatory requirements and due dates. Everything I need is in one place.
Zack Mitchell: We utilize various computer applications within our enterprise hazard protection systems. These include safety auditing software for regular inspections, a document management system for administrative records, daily activity logs for tracking man hours, and a training credential database to manage employee certifications.
What are some of the key challenges for improving electric hazard protection at your facility and what strategies/best practices have you implemented to help ensure success?
Zack Mitchell: Some of the key challenges for improving electric hazard protection at our facility include the proper implementation of lockout/tagout (LOTO) procedures and ensuring effective communication and awareness among personnel. To address these challenges, we have implemented strategies and best practices. Our policy strictly prohibits a tag-out only system, requiring all power sources to be locked out with a physical lock/barrier before work begins.
Additionally, we hold preparatory meetings with all relevant personnel to ensure proper communication and awareness of potential hazards. Administrative documentation is also in place to account for exposure to hazards, personnel involved, and the necessary steps to follow.
Has COVID-19 accelerated implementation of a hazard protection plan, and if so, how?
Jeanie Downs: The COVID-19 pandemic didn’t really accelerate our hazard protection plan as we already had a robust strategy in place. We added a few protocols, but we were otherwise prepared.
Zack Mitchell: Yes, the COVID-19 pandemic has accelerated the implementation of a hazard protection plan in our facility. In response to the crisis, we have taken proactive measures by implementing a COVID protection plan that aligns with state and federal guidelines.
What tips would you offer to someone newly tasked with hazard protection duties?
Jeanie Downs: Go to the experts that are doing the job. The employees that work in any given work stream know the risks of the job they are doing and can assist a new safety manager with issues the new manager may not see or think of. Current employees can also be instrumental in modeling behavior for new employees.
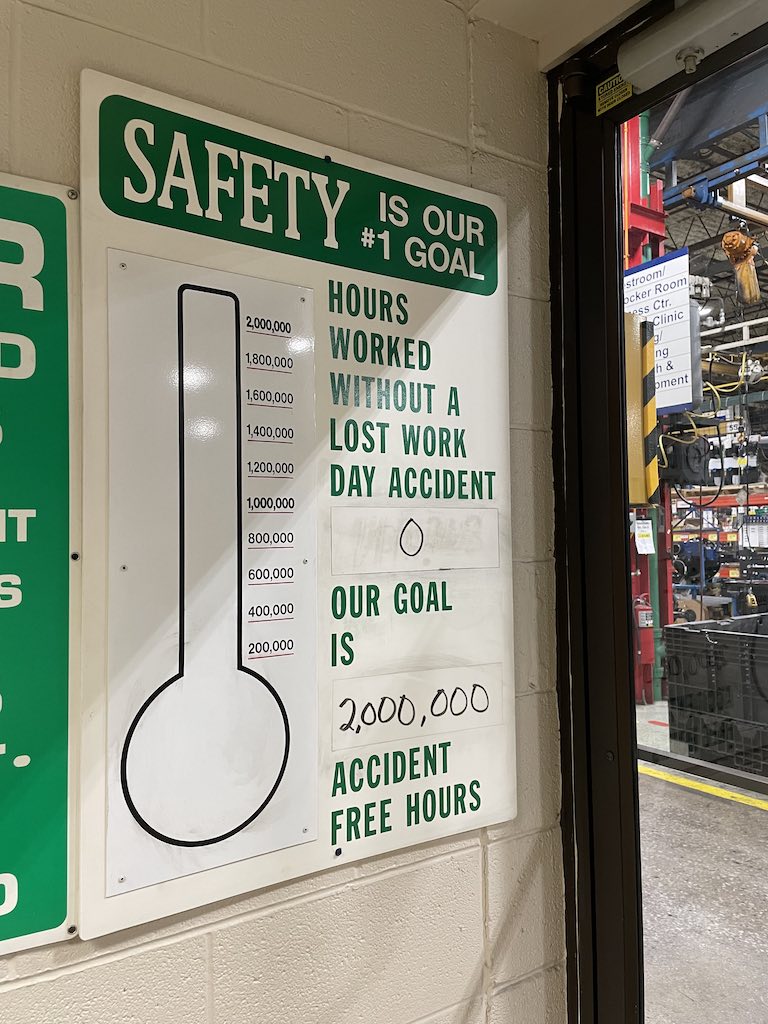
Zack Mitchell: Know what you are working with and associated hazards, SDS familiarization and ensure proper training credentials.
Can you provide an overview of the potential hazards that exist in manufacturing and industrial facilities, and how you prioritize them in terms of risk management?
Zack Mitchell: Unexpected exposure to hazardous chemicals, clear communication with scope of work expectations and ways to mitigate hazards, familiarity with safety programs and procedures.
How do you stay updated on the latest safety regulations and industry best practices related to hazard protection in manufacturing and industrial settings?
Jeanie Downs: I find that webinars, seminars, and safety conferences, are great for keeping up to date with the latest regulations, PPE and the latest safety products. The expo portion of the safety conference allows you to find a vendor to help implement products or tools you just learned about that fits your safety goals and objectives.
Zack Mitchell: We have established a process where our safety programs are reviewed and updated at least annually. This proactive approach ensures that our programs remain compliant with company, state, and federal regulations. By regularly monitoring and incorporating any changes or advancements in safety regulations and best practices, we maintain a high standard of hazard protection in our facility while adapting to the evolving landscape of safety requirements in our industry.
What measures do you take to ensure all employees are adequately trained and aware of the hazards they may encounter in their specific roles within the facility and how often does this occur?
Jeanie Downs: Newer generation workers learn differently. We have begun retooling our training to better equip employees once they get to the shop floor. Originally, we conducted our training in the classroom only. We have since added a hands-on element to appeal to our younger recruits. We also remind employees, not just shop workers of the importance of safety. Everyone receives weekly safety trainings delivered online. This helps everyone be aware of safety behaviors whether they are in the factory full-time or just walking through the parking lot.
Zack Mitchell: All new-hire employees undergo training courses that are specifically tailored to their scope of work. These training courses cover the hazards they may encounter and the necessary safety protocols to mitigate those hazards effectively. Additionally, we prioritize ongoing training and awareness by retraining employees on an annual basis. This ensures that employees stay updated with any changes in procedures, equipment, or potential hazards, fostering a culture of continuous learning and maintaining a high level of awareness throughout the facility.
How do you monitor and assess the effectiveness of hazard protection measures in your facility, and what steps do you take to continuously improve safety?
Jeanie Downs: We conduct an annual review of the safety program to ensure our protection methods are working. We also assess our employees’ safety knowledge. We randomly ask employees in each area of production a series of questions to determine whether we need to conduct a safety refresher for that team.
Zack Mitchell: We employ various methods to monitor and assess the effectiveness of hazard protection measures, while continuously striving to improve safety. Firstly, we ensure compliance with regulations pertaining to safety measures and hazard protection. Additionally, we emphasize the use of proper personal protective equipment (PPE) as a crucial element of hazard mitigation. Moreover, we conduct weekly meetings where hazards are discussed, fostering awareness among employees. These meetings provide an opportunity to gather feedback, address concerns, and identify areas for improvement.
How do you approach the selection and use of PPE in your facility? What steps have you or your company taken to ensure employees have access to and properly use the necessary PPE?
Jeanie Downs: We conduct PPE assessments whenever we update a process. As part of the facility modification request, we review and select PPE according to the hazards in the process. On our shop floor we have PPE vending machines. If an employee needs gloves, they can go to the vending machine without waiting for someone to bring the gloves to them which also helps with efficiency. Additionally, the vending machine tracks the efficacy of our equipment. If employees, for example, are constantly in need of gloves, then perhaps we need to switch to a heavier glove, etc.
Zack Mitchell: We approach the selection and use by mandating “100% PPE” for all employees, which includes hard hats, safety glasses, cut-resistant gloves, hearing protection as needed, fall protection, and respirator use. We conduct hazard assessments to identify the necessary PPE, provide comprehensive training on its selection and use, and supply all employees with the required equipment before they start their work. This ensures that our employees have access to and properly use the necessary PPE, prioritizing their safety and creating a secure work environment.
In your experience, what are the biggest challenges or obstacles in creating and implementing protective environments in manufacturing and industrial facilities, and how do you overcome them?
Jeanie Downs: Safety is part of our culture and our number one priority – and we make sure everyone treats it as a priority at every level. Employee turnover is the biggest challenge to our safety efforts. Manufacturing employees used to stay in a job for 40 years. Employees no longer stay at one company for that long which makes the pool of new employees constant. To keep safety front-of-mind we run a refresher training weekly in addition to in-depth onboarding training and regular safety audits.