Manage increasing data volumes that follow from connected inspection, in-service monitoring.
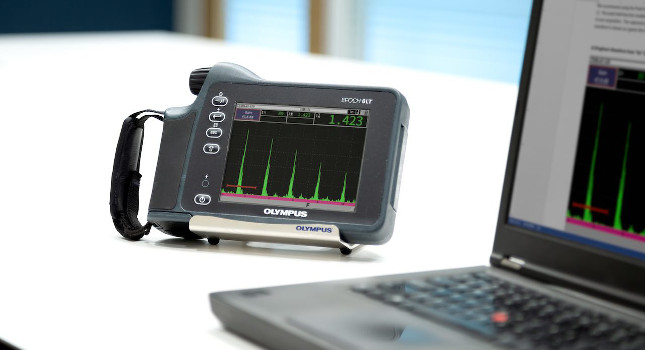
Inspection service companies employ many different tools and technologies. That doesn’t mean a job involving multiple inspectors has to be complicated.
For example, inspectors commonly perform routine nondestructive testing (NDT) on piping, vessels, tanks and other equipment. Ultrasonic thickness gages monitor for corrosion and erosion of in-service equipment. Ultrasonic flaw detectors check for cracking and inspect structural welds for defects that can cause costly equipment failures. Service companies also inspect piping, valves, welds, components and pressure vessels using X-ray fluorescence (XRF) for material compliance and positive material identification (PMI) applications.
Larger jobs can require a whole team of inspectors, each responsible for recording measurements from different facility areas. Typically, field technicians relay the data they collect to a remote office for analysis. Wireless data transfer and cloud connectivity can simplify the task.
Conventional data collection
For large inspection jobs, a supervisor or data analyst usually assigns a portion of the work to each inspector. For example, ultrasonic thickness data typically is collected in one of two ways:
Digital ultrasonic thickness gage with datalogger: Inspection survey files are created with thickness measurement locations (TMLs) that correspond to the assets and locations to be inspected. The inspector transfers the completed survey files using a USB or RS-232 connection. From here, the data is manually imported into asset management software.
Write down results by hand: Each inspector has a sheet of inspection locations corresponding to assets needed to be measured and manually record on paper each thickness reading. Sometimes inspectors work in teams. Inspectors hand the paper to the manager or data analyst, who then inputs the values into a spreadsheet or asset management software. In some cases, inspectors will bring a tablet or PC into the field and manually enter thickness readings into their asset management program.
These processes can be slow, inefficient and have the potential for inaccurate data due to human error. However, they remain relatively unchanged since the advent of digital ultrasonic thickness gages. Digital technologies can simplify this process to make managing results more efficient.
Embrace the digital present
What if all the devices talked to each other? This idea has been around for decades, but technology advance makes it a reality. Manufacturers and inspection companies are taking advantage.
The Industrial Internet of Things (IIoT) enables smart connected devices to communicate and share information. IIoT and cloud functionality are increasingly important for industrial inspection. When inspection equipment inter-connects and also connects to the cloud, it opens up new possibilities that can transform the inspection process.
Any time decisions are made using the most relevant information, it’s an advantage. The flow of information from connected devices about machines, materials, operations and environment entails tremendous amounts of data having strategic value. Properly analyzed, manufacturers can use this data to recognize problems sooner, minimizing downtime and improving quality control. IIoT also can improve efficiency by helping organize the supply chain and the flow of components into and throughout the factory. Even small improvements in efficiency reduce cost.
Manufacturing is reaping the benefits of IIoT. In a modern smart factory, the life cycle of a product can be planned out digitally. As new products are manufactured and come online, they need to undergo rigorous testing to ensure quality. In a smart factory, each instrument can talk to the factory and provide information from a variety of sensors, including instrument health. If there’s a fault in a newly manufactured component, the factory is immediately notified, so the fault can be corrected before going through testing, helping streamline the process.
How the cloud will change industrial inspection
Just like a smart factory, smart inspection is changing the industry. Smart inspection equipment enables easy transfer of information to the manager or data analyst in charge. The question is, what’s done with the information? This is where the cloud comes in.
The cloud refers to software and services that run on the Internet. In the consumer space, there are already many popular cloud products, including the ability to stream movies and TV shows. Cloud also is affecting industry. A study from McKinsey estimates the IoT could have a yearly economic impact of between $3.9 trillion to $11.1 trillion a year by 2025.
For inspectors, the cloud has the potential to provide many advantages, but some of the most useful are data storage and integrity, job management and collaboration, software updates and calibrations and health monitoring and service.
Data storage and integrity: Modern inspection and analysis equipment feature sophisticated onboard reporting tools, reducing the chance of human error during manual data entry. However, the onboard data storage space of some inspection equipment may be limited. Inspections that require saving a large number of image files can be data-intensive and running out of storage space in the field can lead to costly delays.
Cloud storage means that you don’t need to keep a large backlog of data files on your instrument or worry about running out of space. Wireless LAN-enabled inspection devices can automatically upload data to your cloud service. Once in the cloud, the data is immediately accessible. Wireless data transfer adds additional convenience since users don’t have to physically plug their instrument into the computer and use an interface program to transfer files. Because cloud platforms use remote data centers, data storage is inexpensive and scalable. Cloud platforms will seamlessly adjust to meet your data storage needs without the expense of managing onsite servers.
Job management and collaboration: Accessible data facilitates collaboration. The cloud gives users tremendous flexibility in what they do with their data and makes it immediately available to more people. Sharing data with colleagues back in the office helps facilitate discussion and decision making.
Cloud-connected devices enable inspection companies to manage large projects in real time. Large projects can be divided into jobs with individual tasks that correlate to specific inspection areas. Managers can build survey files within a cloud project management tool and wirelessly deploy the survey files to instruments in the field. For thickness gaging applications, once a survey file has been completed, the inspector can upload the file directly from their connected gage to the cloud. This enables the inspector to get the data back to the supervisor or data analyst quickly, so they can review the data sooner and make critical decisions faster.
The cloud can enable real-time collaboration with screen sharing for certain types of inspection equipment. Some modern handheld XRF analyzers, for example, can share their screen over a wireless LAN connection so that field technicians can get immediate feedback from experts in the home office. This facilitates cost savings and efficient collaboration, as it enables someone with technical expertise to provide support for a whole team of inspectors in the field.
Managers can also create and store setup files for a variety of inspection equipment on the cloud and deploy the files to inspectors in the field. This ensures that each inspector’s equipment is properly configured for the job at hand. If the inspector is not within a wireless LAN network, they can even use their mobile phone as a hotspot to connect their gage to the cloud. Managers can remotely monitor job progress across their entire fleet and allocate new tasks to inspectors as previous tasks are completed, efficiently managing their resources in the field. This functionality enables managers to expedite tasks remotely without having to bring inspectors in from the field, helping minimize downtime and ensuring that resources are being used effectively.
Up-to-date instrument software and calibrations: Another advantage of the cloud is wireless software updates. Many digital equipment manufacturers provide regular software updates to add improvements and fix bugs. Rather than having to physically plug an instrument into a computer, download the update and port it over to the instrument, the cloud makes it simple to wirelessly download software updates as soon as they’re available, just like on your smartphone. Managers can view current instrument software information from a cloud dashboard, so they can ensure that their instruments in the field are running the latest version.
Periodic factory calibrations are recommended for certain types of industrial inspection equipment. Depending on the industry, inspectors may be required to provide a calibration certificate in case of an audit. For inspection service companies with a large number of instruments deployed across multiple job sites, keeping track of recommended calibration dates and physical calibration certificates can be an administrative challenge. Instrument calibration certificates, manuals and instructional material can be stored in a central location on the cloud, so that inspectors can always have the required documentation on hand in case they need it.
Health monitoring and service: Sensors in testing equipment can monitor the health of an instrument, such as the number of power cycles, active time, temperature, error logs and drops. With this information, users can track how much each piece of equipment has been used, when it needs to be serviced and when it was last calibrated. By monitoring instrument health data, managers can distribute the workload across their fleet of instruments.
For GPS-enabled devices, including some XRF analyzers, the cloud enables managers to track the physical location of their instruments. Managers can efficiently track and allocate resources as needed from a central location. Technicians can also geo-tag test results for improved traceability and mapping of test information in the field.
Instrument health information also helps inspectors avoid surprises due to lags in servicing and calibration. When you do send your equipment in for service, each component can be tracked in the service center, so service technicians know which component needs to be serviced and you get your device back faster.
Looking forward
These features are just a small portion of the potential that the cloud offers NDT and XRF inspectors. As the related technologies that make up the smart factory and cloud continue to advance, new cloud-based tools will become available that will continue making inspectors’ jobs easier. The volume of data provided by connected inspection, in-service monitoring and manufacturing equipment is increasing, and cloud services are the most efficient way to use that data to your advantage.