Complying with FEB and NRTL standards are vital to ensuring worker safety and standards for electrical products and systems
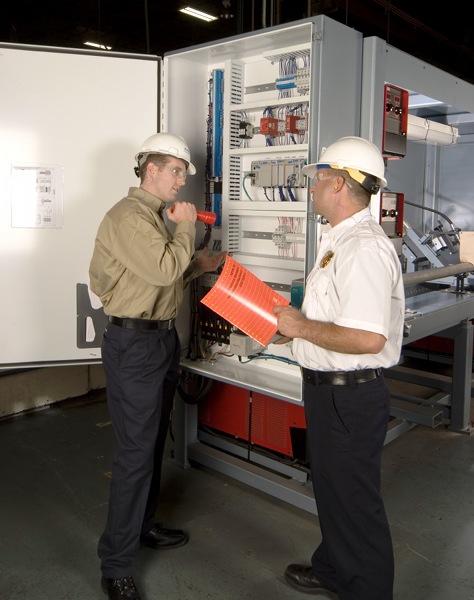
Every day, one person dies in the workplace from electrocution, and the United States averages more than 3,600 disabling electrical contact injuries annually, according to the American Society of Safety Engineers. The risk associated with not evaluating or not ensuring the compliance of electrical equipment is very high. That is why the role of third-party testing organizations is so important.
There are two types of organizations that perform product safety testing—a Field Evaluation Body (FEB) and perhaps the more well-known Nationally Recognized Testing Laboratory (NRTL). While similar in their purpose, there are significant differences. Without qualified organizations like FEBs and NRTLs, there would be no way of ensuring that a particular product or installation meets the necessary safety requirements.
NRTLs and FEBs are part of the U.S. electrical safety system that helps ensure safe installations of electrical products and systems. These organizations are usually accepted by local authorities having jurisdiction (AHJs), manufacturers, and others for showing that equipment is suitable for use in the workplace, in construction, or in the home.
Once equipment is deemed to be in compliance with applicable standards, a label is applied. By looking at the NRTL mark or FEB label, an inspector will have information about the standards to which the product has been listed or labeled. In addition, the inspector can call on the NRTL or FEB with questions regarding equipment suitability when something does not look correct.
The National Electrical Code drives local electrical inspectors (AHJs) to look for labels and listing marks. NEC 110.3 provides a list of considerations inspectors need to make when evaluating equipment:
- Suitability
- Mechanical strength
- Wire bending space
- Insulation
- Heating effects under normal and abnormal conditions
- Arcing effects
- Classification
- Practical safeguards.
While 110.3 alone does not require listing or labeling of equipment, it does require considerable evaluation. Section 110.2 requires that equipment be acceptable only if approved, where approved means “acceptable to the AHJ.” The most common form of evidence considered acceptable by AHJs is a listing or labeling by a third party. Another important point is that the NEC requires that the installation instructions included in the listing or labeling be considered during an evaluation.
When AHJs rely on listed or labeled products, it can make the job easier since the inspector does not need to evaluate all the parts as required by NEC 110.3(A). Use of listed or labeled products provides a minimum level of consistent safety when installed properly. This is NRTLs, FEBs, and inspectors working together!
How an NRTL compares to an FEB
National Fire Protection Association (NFPA) 790 is the U.S. standard applicable to FEBs. The most credible method for certification of FEBs involves accreditation to NFPA 790 by a qualified third-party certifier like International Accreditation Services (IAS). FEBs can perform field evaluation services and equipment labeling. NRTLs must comply with the Code of Federal Regulations (CFR) 1910.7 and are certified by OSHA to perform product listing services. OSHA does not certify FEBs, nor does it certify NRTLs to provide FEB services.
Another important difference between these two organizations is that NRTLs provide product safety testing and certification at the point of manufacture. Their listing process involves rigorous testing of representative samples of a product and the periodic factory follow-up verification and inspection (usually two to four times per year) to ensure new production exactly mirrors the tested samples.
On the other hand, FEBs have the capability to provide product safety testing and labeling primarily in the field for a wide range of products found in the American workplace, while still adhering to stringent national standards from the NFPA:
- NFPA 790 – Standard for Competency of Third-Party Evaluations Bodies (FEBs)
- NFPA 791 – Recommended Practice and Procedures for Unlabeled Equipment Evaluation.
The listings performed by NRTLs and evaluations performed by FEBs are based on product safety standards developed by U.S.-based, standards-developing organizations and often issued under the accreditation of the American National Standards Institute (ANSI). In fact, both testing organizations can determine if an equipment installation is acceptable as defined by CFR 1910.399.
An NRTL would perform the service stipulated in CFR 1910.399 (1), which states that an installation of equipment is acceptable to the Assistant Secretary of Labor if it is accepted, or certified, or listed, or labeled, or otherwise determined to be safe by a nationally recognized testing laboratory pursuant to §1910.7.
Similarly, an FEB can determine acceptability by providing the test data called for CFR 1910.399 (3) which reads as follows: With respect to custom-made equipment or related installations that are designed, fabricated for, and intended for use by a particular customer, if it is determined to be safe for its intended use by its manufacturer on the basis of test data which the employer keeps and makes available for inspection to the Assistant Secretary and his authorized representatives.
Helping inspectors work more efficiently
Occasionally, a listed or labeled product doesn’t look quite right or has obvious violations. This is when electrical inspectors will notify the NRTL or FEB. The testing organization can determine if it is a counterfeit label, if the equipment was modified, or if a manufacturer is incorrectly manufacturing the product. In any case, the NRTL or FEB has a process to review, evaluate, and stop problems in the future.
In those cases, where an item with violations is holding up the opening of a business, working with an FEB that has the ability to nondestructively test in the field can provide significant time savings, especially with equipment that has been modified, refurbished, or relocated. Such changes normally void the NRTL’s approval of that product, and an employer’s use of it in the workplace violates the OSHA standard requiring the approval.
The FEB provides field label services paid for by one of the parties involved—typically the manufacturer or the installer—to determine if the equipment is compliant in the specific installation. Choosing the right FEB during this critical time is essential.
You’ll want an organization that has a geographically dispersed network of highly trained, safety-certified technicians, along with engineers who know the applicable safety standards for your class of equipment and the reasons behind the standards. Working with engineers who are regular participants in the codes and standards-making processes offers added benefits.
It’s important that an FEB is approved by AHJs from around the country and is recognized in the industry. This makes the process of getting final approval of equipment much smoother. Local jurisdictions know that if the recognized FEB’s label is applied, the job was done right. Working with an experienced FEB inspires confidence and assures others that the equipment was properly inspected and that any discrepancies have been corrected.
A good place to start in the search for an FEB is IAS, which is a nonprofit corporation that has been providing accreditation services since 1975. IAS makes sure that an FEB’s experience, practices, equipment, and processes meet the stringent NFPA 790 and 791 standards, as well as other IAS requirements. The accreditation provides objective evidence that an FEB operates at the highest level of ethical, legal, and technical standards.
The importance of ensuring proper installation and operation of electrical equipment cannot be overstated. After all, many organizations already embrace safety compliance and invest considerable resources in order to protect employees, the environment, and the company as a whole.
Keep in mind that not all testing companies have the competency or experience needed to help you properly protect this investment, so scrutiny is needed when choosing the third-party testing organization that is right for you. An accredited FEB that offers the flexibility of field testing may just be the solution you need to ensure safe operation, get an inspector’s “red tag” removed from your equipment, and get back to business.
Evaluating a project’s conformity
Factors that should be considered when evaluating an FEB for a potential conformity project:
1. Objective and Unbiased
- Independent, professional, third-party testing organization focused on conformity assessment services
2. Quality
- Certified by a recognized accreditation body
- Qualified and trained staff
- Appropriate quality system in place
- Financial stability
- Qualified technical supervision and management
3. Methodology
- Documented reference to applicable ANSI or other product safety standards
- Proper sample control/integrity requirements
- Testing/evaluation procedures comply with NFPA 790 and 791
4. Responsiveness
- Complete record keeping system with test data availability
- Professional systems in place to deliver prompt service
Wally Vahlstrom brings more than 40 years of electrical engineering experience to his position as the director of technical services for Emerson Network Power’s Electrical Reliability Services group.