Ubisense VP Adrian Jennings discusses the need to go slow in moving manufacturing away from manual systems to an integrated production system.
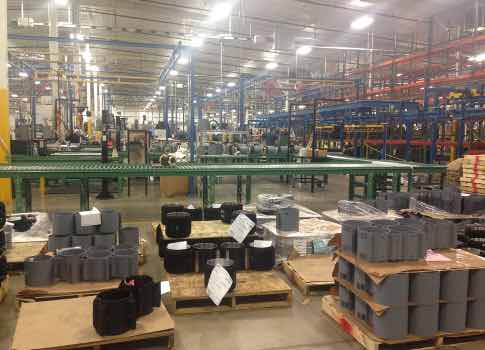
The concept of the Industrial Internet of Things (IIoT) and its European equivalent, Industry 4.0, continues to grow. The promise of these strategies is to bring data together to deliver actionable results and improve productivity, but the reality of plants today is that there is widely disparate use of sensors and monitors. Many other plants simply aren’t that far along in the manufacturing process.
A recent study by Ubisense, a global enterprise software solutions company, found there is a continued use of manual systems in plants. Among the findings of the study (which can be downloaded from this link):
- 40% have no visibility into the real-time status of their company’s manufacturing process.
- More than 80% rely on human observation to support process improvement initiatives.
- 85% of quality issues are caused by worker errors.
- Nearly 10% of manufacturers spend half their day looking for equipment and products.
- Almost 15% of manufacturers don’t prioritize product repairs.
Adrian Jennings, vice president of manufacturing industry strategy for Ubisense, discussed the study’s findings and its implications for discrete manufacturing with CFE Media:
CFE Media: You work with a lot of customers in all areas of manufacturing. Were there any surprises from the results of the study?
Jennings: On the face of it, the survey was somewhat surprising: 10% of respondents waste at least half of their day searching for lost items; 40% have no real-time process visibility; and 50% don’t keep fastener tightening records.However, the reality is that this reflects my experience when visiting all kinds of assembly plants globally.
I think people have a general belief that assembly plants are rather advanced technologically, and that’s just not the case. The picture people imaginetypically involves legions of robots happily welding and spraying in high-volume car plants. But out there on the assembly line, and in other, lower volume plants (tractors, backhoes, street sweepers, Dreamliners) the scene is quite different. The reality is that manufacturing plants are still dominated by manual processes and in that light, the survey results are not surprising at all.
CFE: What are the biggest barriers for manufacturers to implement Industry 4.0? How many of those barriers are human and how many are financial?
Jennings: I should preface my answer by saying that I don’t think anybody in the automotive vertical is implementing Industry 4.0 today, and precisely because there are some formidable barriers. It’s tempting to think of any kind of computer controlled process as “Industry 4.0” since we’ve been persuaded to believe that 4.0 is all about cyber-physical systems. But we are also told that Industry 3.0 refers to the introduction of microprocessors and computerized control—and what is that if not a localized cyber-physical system?
I think it’s critically important to understand that Industry 4.0 is about scale of integration, which is why it is wrapped up with the Internet of Things. The underlying paradigm shift is that people will have real-time, detailed knowledge of the status of the entire value chain—from order to fulfillment—so that production can be agile and reactive to different issues and drivers.
With that definition, I think there are four critical barriers to Industry 4.0 adoption: networks, security, skills and culture. Perhaps networks and security go hand in hand since they are closely related. In terms of networks, in order to crunch data based on widely distributed process sensors, you need the network infrastructure to get all that data to one location.
The first problem is getting it from line side to a server, and that’s no small task. Wireless networks today are not widely used in mission-critical applications since they are not robust enough, and wired networks are costly to install. Many plants just don’t have the infrastructure to distribute data inside the plant, let alone between plants and suppliers on a global basis.
It’s at that level that security concerns become an issue too: Industry 4.0 requires high-bandwidth, low-latency, mission-critical reliability over global, secure networks—networks built and managed by Telecom operators outside of the control of automotive OEMs.
The IT challenge is critical, and it’s not simply financial. The vast majority of plants are shop-floor driven with strategic direction on control systems driven by process engineers on the line. IT is a supporting function and is rarely seen as an area for investment in its own right.
Industry 4.0 is a seismic shift; it is without question the “IT-ification” of manufacturing. If the production process is truly to be driven by real-time intelligence from sensors throughout the supply chain, then IT will take on a central, leading role all the way to the devices on the line. That’s a big shift in thinking for most people and requires a long-term view of IT infrastructure as a strategic investment rather than the incremental cost of any controls project.
The other cultural issue is about willingness to change. Industry 4.0 is truly a revolutionary idea and it will open up huge opportunities for people ready to embrace it. Let’s remember though that it is not about technology adoption; the technology is simply a tool. Rather, Industry 4.0 is about a whole new way to approach production, and the automotive industry is rightly cautious about big new ideas.
When you are pushing out 400 cars in a single shift or bolting wings on an airliner, there’s no room for risk-taking, and that breeds a healthy level of caution. Industry 4.0 will shatter long-held notions about how to control processes and create a level of flexibility that goes against generations of experience. Technology adoption alone cannot change the bottom line unless the potential for change is embraced throughout the organization
CFE: For your customers already implementing Industry 4.0, where have they seen the biggest benefits?
Jennings: I mentioned that I don’t think anyone in automotive manufacturing is fully adopting Industry 4.0 yet, but many are on the path. I want to make a distinction between the end-to-end cyber-physical systems of Industry 4.0, and local cyber-physical systemsthat are adding value to a single process or physically close set of related processes. Let’s call these “cyber-physical islands” and frame them either as advanced Industry 3.0, or embryonic Industry 4.0 depending on your preference.
Ubisense is certainly in the business of enabling cyber-physical islands and our customers are seeing big benefits as a result. There are many examples, so I’ll just pick two to illustrate the point:
One of our solutions virtualizes the product identification process—a common function required at many locations along an assembly line. Traditionally, this is performed either manually, using barcode scanners, or automatically, using RFID or other fixed infrastructure. By removing barcode scanners, our customers have eliminated a significant amount of process waste, enough to actually reduce the number of workstations on the line.
By doing away with fixed ID infrastructure, other customers have been able to significantly reduce the cost of line rebalancing—the continual process-shuffling burden that always has engineers working the weekends.
Another solution completely virtualizes the entire workstation, creating process control zones in software that attach themselves to the product and entirely replace the traditional fixed workstation. Once virtualized, the workstation can vary in real time in reaction to product variation, task overrun and many more of the increasing number of variables in plants.
One customer has benefited from the ability to give workers a few extra seconds of process time when needed, avoiding a large number of short line stops throughout the day. Another has used the idea of a virtual workstation to create overlapping processes, with one new third-row seat process riding on top of three existing processes.
CFE: Talk about the challenges for manufacturers trying to deal with the issues of Big Data. How can they do a better job of managing data to better understand the metrics?
Jennings: Big data analytics is a skill set that simply doesn’t have a foothold in most plants. Until now, data analysis has been at the local level, often constrained to single processes or a small set of related processes. The data analytics tools are also non-specialized – you only have to look at the printouts on most plant notice boards to realize that Microsoft Excel is the leading analysis tool. Finding trends and triggers in a mountain of seemingly unconnected data is a very different challenge, more in the domain of the NSA than manufacturing.
Manufacturers will have to decide whether to outsource their analytics (creating another layer of cybersecurity issues) or hire a whole new skillset from other industries. Both options have their challenges, but probably outsourcing is the farther reach: “software-as-a-service” and “analytics-as-a-service” sound reasonable, but if Industry 4.0 is to be embraced in all its end-to-end, real-time connectedness, then “production-planning-as-a-service” and “process-control-as-a-service” will have to be considered, too. The implications for cybersecurity and performance SLAs under such a model are immense.
CFE: If a manufacturer is looking to implement 4.0, what’s the first thing he should do?
Jennings: Stop! I joke, but only partly. Industry 4.0 comes with a warning: choking hazard. It is a very big thing with potentially huge benefits and my advice is to try to swallow it in bite-sized chunks. I talked about cyber-physical islands and, whether you consider those to be late-stage Industry 3.0 (like I do) or early-stage Industry 4.0, they are absolutely the correct stepping stones that people should be considering today.
You don’t need real-time process data from your Tier 2 supply base in order to make great strides in quality and throughput in the plant. A growing number of available solutions apply sensors to islands within the plant and deliver a strong ROI through process visibility and smart controls. These solutions can be fairly large projects with similarly large ROIs, but they can be managed locally and with no dependence on third parties for networking, cybersecurity and data analytics.
My advice is this: build your cyber-physical islands today, and connect them all tomorrow. Once these islands are running and creating value, the impetus to connect them together will be strong, and the ROI obvious. Before then, the end-to-end-connectedness-of-all-things simply holds great promise and high risk.