Siemens CTO sees U.S., Germany leading the move toward an industrial Internet.
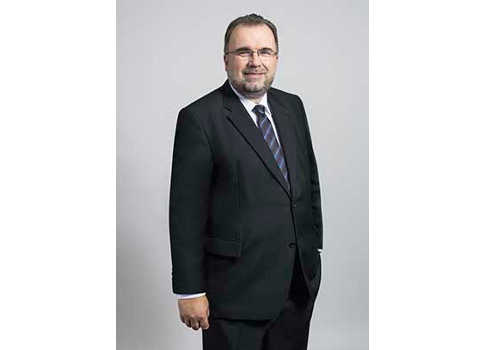
Hannover Messe provided a stage for President Barack Obama and German Chancellor Angela Merkel to press their cases for boosting U.S.-European trade, particularly by advancing negotiations on the Transatlantic Trade and Investment Partnership.
But the world’s largest industrial trade fair revealed yet another partnership that the world leaders can pursue to further economic growth: The United States and Germany can work together to lead a Fourth Industrial Revolution that delivers unprecedented creativity, versatility, speed, quality and cost-effectiveness to global manufacturing.
In Germany, we call this Industrie 4.0. In the United States, the terms heard more often is the Industrial Internet of Things. But while the labels may vary, the definitions are universal. Industrie 4.0 is the digital transformation of industry driven by state-of-the-art information and communication technology.
Early estimates are that Industrie 4.0 can deliver efficiency gains of between 6% and 8% annually to global companies. The global value added of investment in industrial Internet is forecasted to increase from $23 billion in 2012 to an incredible $1.3 trillion in 2020. There is more to this than shop floors filled with smart robots and connected, automated machines. With the rise of increasingly sophisticated industrial software and hardware, companies are now able to merge real and virtual production environments.
New products, even new factories, can be simulated, modeled, and tested virtually. This not only enhances speed to market; it brings new levels of flexibility and efficiency into large-scale production. For the first time, the doors are open to mass customization—something manufacturers traded off long ago to have moving assembly lines.
Merkel and Obama, the first U.S. president to attend the event, were able to see in Hannover that this new digital frontier for manufacturing is not just a concept. Throughout the fair, visitors saw a new wave of products, solutions and services developed both by and for industry.
Our company, Siemens—which now has more than 18,000 software engineers and is already helping customers digitalize their value generation network-provided application scenarios showing how Industrie 4.0 looks in practice.
The United States and Germany are well positioned to push this new industrial age forward. Over generations, our countries have each made important contributions to the development of modern industry, with each of us developing complementary strengths.
Combined strengths
Today, the German economy is guided by a network of major corporations and small and medium-sized companies that nurture highly sophisticated manufacturing technologies. Germany is a world leader, for example, in shop-floor control software, though our real engine is our skilled workforce and innovative strength. (Measured on patent applications per million people, Germany is the world leader.)
The United States economy has been trending towards reindustrialization. Manufacturing activities that had been given up or outsourced have been returning. In light of this, the United States was recognized as the Hannover fair’s partner country for the first time in the nearly 70 years since the inaugural event.
For manufacturers, America offers favorable energy costs, economic incentives such as strong venture capital, and a truly inspiring environment for digital solutions, symbolized best by places like Austin, Boston and Silicon Valley.
Facing challenges
The United States and Germany must all work together to overcome some serious challenges. First, big investments are needed to overhaul our industrial bases. To move to Industrie 4.0, Germany will need to invest $40 billion annually through 2020. In the United States, the average age of manufacturing assets and equipment in operation is more than 35 years old. Currently, only 20% of German companies use connected Internet technology systems to control production processes, while only 5% of American companies have implemented a big data analytics strategy.
Second, Industrie 4.0 nations will need to develop global industry standards for interoperability. As electrification drove forward a second industrial revolution, it took a "war of currents" between the great inventors of the day to settle the question of whether to adopt alternating or direct current. Alternating current won. Yet even today the question is not entirely answered.
As we enter this new revolution, the key to success will be collaboration across national borders and emerging digital platforms. Without global industry standards for interoperability, cross-country and cross-company value chains cannot be achieved.
The United States, with its Industrial Internet Consortium and its National Network for Manufacturing Innovation, and Germany, with our own national effort, Platform Industrie 4.0, must cooperate on both standardization and testing.
Participants in Platform Industrie 4.0 have already developed a framework for competing companies to independently develop networked solutions, while the Industrial Internet Consortium has initiated a comparable effort. These activities are not competing, but complementary. We want to combine the synergies of German and American efforts much more intensively.
No company, country or government will be able to master the complexities of digital transformation in isolation. We will need to pull together our strengths, experience, and expertise instead.
In Hannover, you could hear this new industrial language being spoken.
Siegfried Russwurm is a member of the Managing Board and Chief Technology Officer of Siemens AG.