Offline robot programming platforms are increasingly being used during the COVID-19 pandemic. Four scenarios, key programming features and perks are highlighted.
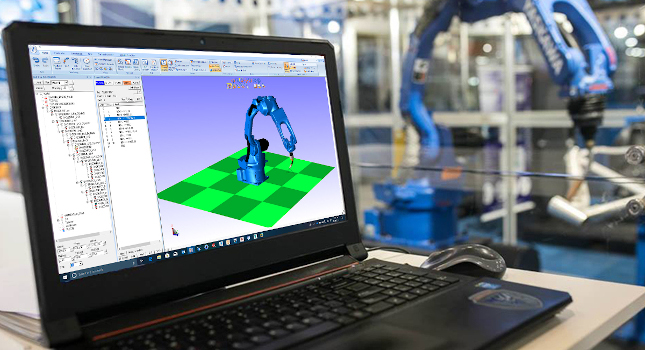
Learning Objectives
- Offline robot programming platforms are increasingly being used to accommodate complex system layouts.
- The COVID-19 pandemic is forcing many manufacturers to use offline robot programming because of workplace restrictions.
- Offline robot programming, when used properly, helps manufacturers address current market challenges.
Robotic automation and other advanced technologies have proven vital for businesses in recent months for sustaining and improving productivity in a demanding, yet uncertain, markets affected by the pandemic. From welding to coating, robots with feature-rich technologies can help businesses achieve greater accuracy and higher quality with increased efficiency.
While robotic automation can accelerate production output, it also can cause significant downtime if a solid robot programming plan is not in place. To facilitate robot uptime – especially for manufacturing companies that cannot afford to interrupt production while a robot program is being written point by point from a teach pendant – offline robot programming platforms increasingly are being used to accommodate complex system layouts.
Four scenarios for robotic offline programming
Using a 3D representation of a robotic workcell that visually demonstrates how a robot moves along a programmed path, offline programming (OLP) can be accomplished through original equipment manufacturer (OEM) -specific software platforms or third-party options. OLP also gives experienced and novice robot programmers the ability to create, test and adjust a robot program or job from the convenience of a PC-based virtual programming environment before it is implemented on the factory floor. Due to events surrounding the COVID-19 pandemic, many manufacturers are finding themselves in one, or more, of the four following situations:
Scenario 1: Restricted access on the floor
The whirlwind of new health concerns and regulations has prompted businesses to implement social distancing, along with work from home (WFH) policies. This has caused restricted access to robots on the factory floor, making it difficult to program/re-program jobs.
Scenario 2: Adapting to changing demand
An uptick in demand for general use products has workers striving to complete high-mix, low-volume runs at a record pace. To deal with the changeover required, a greater focus has been given to smart technologies, such as OLP software, to reduce programming downtime and optimize overall equipment efficiency (OEE).
Scenario 3: Adding automation quickly
Similar to scenario two, the increase in demand for products, especially those important to battling the pandemic, companies need to integrate new robots or redeploy old ones. Either way, to facilitate a smoother transition to the manufacturing of these essential products, using OLP software has been suggested.
Scenario 4: Testing a new approach
Loosening government restrictions have businesses reopening, which results in a new sense of urgency for revitalizing production. As a result, company leaders have decided to tackle tough challenges through creative and collaborative approaches to robotic automation. Either current robots are being redeployed or new robots are being purchased. Quite possibly, robotic automation is being introduced to the factory for the first time. Regardless of the approach, a viable method for setting up new, more complex, robot jobs with offline programming.
Four key features of robotic offline programming
While OLP software is not limited to the following, most users seek offline programming platforms that have an extensive model library and offer these four key features:
1. Robot collision detection
If several robots are working in close proximity, it is vital they are programmed to work as a team. During the offline programming process, the collision detection feature signals potential interference hazards, allowing the programmer to make cost-saving adjustments before the program is introduced to the factory floor.
2. Robot path planning
While a robot is programmed to move from point to point, it is imperative to plan around specific items like fixtures for holding parts. With path planning, programming a robot to maneuver around fixed points is made easier, as it activates collision detection to help avoid interference.
3. Robot conveyor tracking
When parts are in different positions, conveyor tracking can help the robot align those parts, as needed.
4. Robot cam path
If performing a welding application, dispensing application or other complex task, the cam path feature can help automate the process. Instead of manually teaching points to the robot, cam path provide these points automatically.
These features and more work together to help conceptualize possible robot scenarios such as, “How fast can a robot go with a particular application?” or “Can a robot move in a particular fashion to weld a specific part?”and other considerations.
Four robotic offline programming benefits for manufacturers
Aside from addressing the previously mentioned scenarios, the proper and effective use of OLP software can help manufacturers achieve various production goals including:
1. Execute fast integration with robots
Offline programming provides a way of creating a robot job while a workcell is still in the construction phase. This process speeds up integration time, as data files can be transferred once the workcell is complete and installed on the shop floor. While minimal touch-up may be required, having a robot job prepared beforehand is a huge timesaver.
2. Perform quick changeover of robots
If a robot is being used to process multiple parts, offline programming enables the ability to program the robot for “part B” while “part A” is being run. Once “part A” is complete, the programmed files can be downloaded to the robot controller to run “part B.”
3. Set up functional safety for robots
OLP allows for items like arm interference, speed limits and safety zones to be established. This includes the ability to graphically overlay the safety zones (robot range limits) during simulation, allowing visual confirmation and testing with motion in the simulation.
4. Achieve quick cycle times for robots
When extremely fast cycle times are required, OLP platforms can help users monitor the duty cycle of a robot so the life of the motor can be monitored.
The flexibility provided by OLP software offers many perks and enables a higher mix of jobs with a simple transition from one job to the next. Similarly, larger companies with multiple locations and/or workcells may be able to reduce programming time and inconsistencies by distributing the programmed job from a central, controlled source. Furthermore, improvements in sensor technology for tasks such as robotic welding have come a long way in the recent past, providing considerable advantages for end users spanning diverse industries.
Once implemented and properly used, the collective use of software – along with feature-rich sensors –can help manufacturers address current market challenges and the growing needs of a high-mix low-volume production environment.
Michael Castor is product manager, material handling at Yaskawa America Inc. – Motoman Robotics Division. Edited by Chris Vavra, associate editor, Control Engineering, CFE Media and Technology, [email protected].
MORE ANSWERS
Keywords: offline robotic programming, COVID-19
CONSIDER THIS
What benefits would your robots and manufacturing facility gain from offline robot programming?