Companies that are engaged in ongoing maintenance at an industrial facility should implement safe working practices and practice predictive maintenance whenever possible.
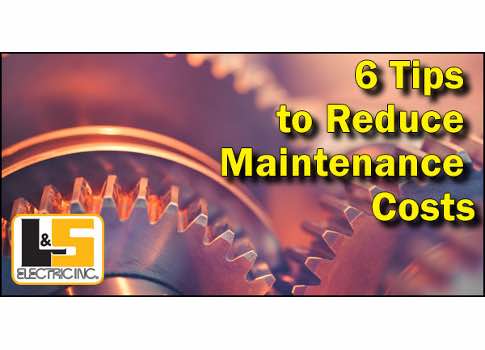
One of the best decision for any facility is to implement a preventive maintenance program. Any ongoing maintenance saves both time and money. That doesn’t mean it is not an expensive part of doing business. One way to increase your return on investment (ROI) in maintenance costs is to reduce what you’re spending.
Consider these six strategies to help you do so.
1. Implement safe working practices. One of the most important things you to do for your maintenance crew and your entire staff is to implement safe working practices. At many facilities, cutting corners to speed up the process opens the door for accidents or injuries. Injuries are going to slow things down and cost you money. Begin regular safety training for your staff.
2. Keep things simple. As the ongoing maintenance continues to grow, you will find certain procedures that improve along with it. These procedures result in redundancy throughout the maintenance process. This redundancy is a drain on both time and finances. Keeping things simplified makes it easier for the maintenance staff to complete tasks. Providing the maintenance staff with a detailed checklist of the necessary steps for each job saves time and money.
3. Practice predictive maintenance. Along with a preventative maintenance program, implementing a predictive maintenance program also saves money. Establish a calendar for many of the regular maintenance tasks. Predictive maintenance saves time by avoiding unnecessary downtime when equipment fails. Predictive maintenance also allows for scheduling necessary downtime during slow hours rather than having an unscheduled downtime occur during peak productive hours.
4. Use available tools. It is always a good idea to supply the proper tools for your maintenance staff. It is also important to have the proper tools running behind the scenes as well. These tools include maintenance software that both tracks ongoing projects and alerts you to any potential upcoming maintenance projects.
5. Get everyone on board. At many industrial facilities, the maintenance staff has the sole responsibility for caring for any maintenance issues. This includes equipment testing through a preventative maintenance program. Often, however, the operator of the equipment works with the program daily. Train the operator to recognize any existing problems. Those issues include changes in the noise or the way that the equipment is operating. Report any of these factors immediately to schedule more tests to determine if a maintenance issue exists.
6. Use an outside service. One way to reduce maintenance costs and increase productivity at the same time is to bring in an outside service to handle the maintenance program.
David Manney is a marketing administrator at L&S Electric. This article originally appeared on L&S Electric Watts New Blog. L&S Electric is a CFE Media content partner.