Switching absorbents can save time and money, and reduce waste
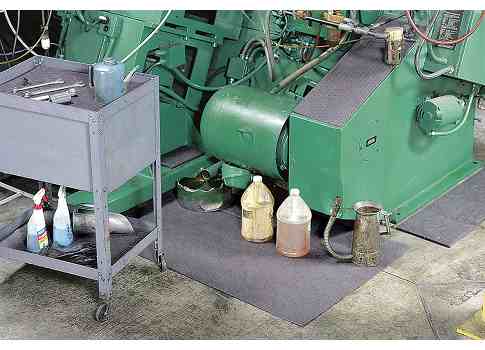
Cleaning up leaks, drips, and spills around a facility can be time-consuming, especially when the absorbents being used are not well suited for the task or don’t work effectively. Using the wrong absorbent can also contribute to excessive waste volume that can be costly to dispose of and doesn’t help the facility achieve environmental goals.
Knowing where leaks and spills are most likely to happen, and having the right kinds of absorbents on hand to quickly tackle nuisance problems, helps to reduce downtime, keep costs in line, and minimize waste volume.
Identifying your problems
Fluid transfer areas, such as dispensing stations and waste collection areas, are common locations for small spills. Overfills from pumping fluids into small containers, and spills from liquids that didn’t quite hit the funnel on a collection drum are almost everyday occurrences at some facilities.
Spills can also happen in warehouses and other storage areas as a result of forklifts grazing containers or from containers that develop leaks over time. Even small areas of the facility like laboratories may also have an occasional spill.
Production areas often have consistent sources of nuisance fluids in the form of overspray, drips from parts being removed from dip tanks, or machinery that leaks as a normal part of its operation. Specific sources of leaks and spills may be unique to a facility, but identifying problem areas and the likelihood of leaks and spills shouldn’t be a difficult task.
It is probably fairly easy for a plant or safety manager to identify these areas on a floor plan. What may take a little more time, however, is noting the most likely volume of liquid that could spill in each area. For fluid dispensing areas, it may only be a few ounces. In a warehouse, it may be anywhere from five to 500 gallons. Knowing the potential volume that could leak or spill helps determine the types of absorbents that will be most efficient and useful in each area.
Choosing absorbents
Like leaks and spills, absorbents come in many shapes and sizes. This wide variety helps keep facilities cleaner and safer, and allows them to select the types of absorbents that best meet their needs without having to spend time adapting something to fit the application, or money on extra absorbency that may not be necessary.
Some facilities still rely on clay-based loose absorbents for leak and spill response, often because the price is perceived to be very low compared to other more modern absorbents. However, when the cost of labor, disposal, and premature engine wear are added to the cost of using these loose absorbents, savings are quickly eroded. Clay-based absorbents can also present a health hazard to employees because clay dust contains crystalline silica, a known carcinogen.
Modern absorbents, such as mats, socks, pillows, and wipers, are task specific. And, because they absorb and retain spilled liquids much more effectively than clay-based loose absorbents, they minimize both the time spent responding to a spill as well as the volume of product used during cleanup.
Absorbent mat pads are engineered to soak up spills quickly and help facilities to minimize both downtime and waste volume. Mat rolls can be used in walkways and entrances to help absorb overspray and other forms of liquid leaks while increasing traction to improve floor safety and help reduce slip and fall hazards. Mats also eliminate the dust and mess associated with using clay-based loose absorbents.
When larger spills need to be contained quickly, socks and booms can be used to create a dike that absorbs liquids while keeping them from spreading and contaminating a larger area. Socks are also commonly used around the bases of leaky machinery to catch nuisance leaks and drips, preventing them from entering aisles and walkways around equipment.
Wipers can be stored in fluid dispensing areas, laboratories, and production lines where small leaks and drips of less than a quart are common. Using wipers instead of absorbent mats for these small, incidental leaks and spills will also reduce waste volume and minimize expenses.
Spill kits help facilities prepare for non-routine leaks and spills in warehouses, fueling stations, loading docks, and bulk-fluid transfer and other areas. Spill kits contain a variety of spill response absorbents such as socks, mat pads, and wipers to help responders quickly contain and clean up spills.
Waste minimization
As the cost of landfilling wastes increases, and as facilities continue to develop sustainability programs to reduce wastes or achieve zero-landfill goals, the use and disposal of spent absorbents can come into question. Fortunately, modern absorbents can help facilities achieve waste reduction and even zero-landfill goals.
Absorbents are commonly made of polypropylene, cellulose, or a combination of these two materials. Both polypropylene and cellulose have high BTU values and produce little ash when burned in a commercial fuels blending or other types of incineration processes.
Fuels blending processes convert wastes into heat energy to make electricity. Even the residual ash from the burning process is useful as part of the base stock for concrete products, helping facilities achieve zero-landfill goals for absorbent waste streams. Because clay-based absorbents are made from earthen materials, they are not good candidates for fuels blending or incineration because they have no fuel value and an extremely high ash content.
For facilities that are looking at waste reduction as a cost-saving measure, switching from clay-based absorbents to mats, socks, and wipers can quickly pay off because less than four mat pads can absorb the same amount as 10 pounds of clay-based loose absorbent. In addition, absorbent mats, socks, and wipers can be compacted into drums to further reduce the overall number of containers that are sent for disposal or recycling.
Teaching employees to use only what they need when cleaning up a spill can help to further minimize wastes. This can be a hard habit to break, because it is very common to grab a handful of mats or wipers to clean up a spill that could easily be handled by one mat or just a few wipers. A waste container full of half-used absorbents is a common sign that this is happening.
Modern absorbents are designed to be used to their full capacity and to stay intact even when fully saturated. Helping workers understand this, and demonstrating the product’s effectiveness during training or drills can help reinforce waste minimization efforts and lower costs.
Even the most efficient processes and systems are bound to have an occasional leak or spill. Being prepared with the correct absorbents and training employees on how to use them effectively will help to minimize downtime and minimize waste.
Karen Hamel is a technical writer at New Pig.