Employers and employees must ensure proper personal protective equipment is in use to keep workers safe and lower risk.
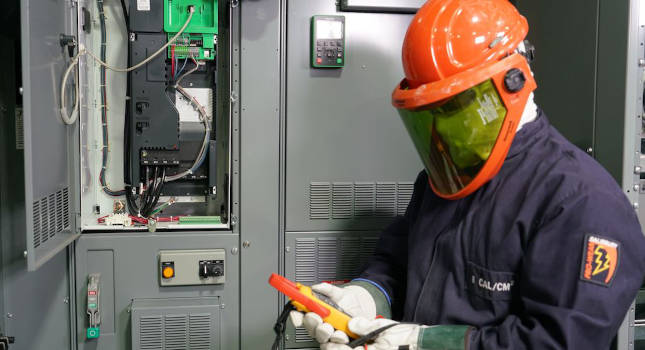
Learning Objectives
- Understand that there are ways to lower electrical risks and improve safety conditions for employees.
- Know that using proper personal protective equipment, such as equipment that includes shock protection and arc-rated protection, the risk to employees is greatly diminished.
- Review the proper shock and arc flash personal protective equipment to wear when working around exposed energized conductors operating at or greater than 50 volts alternating current or direct current.
PPE insights:
- Employers can help protect employees by providing them with the correct personal protective equipment when working on electrical systems.
- By understanding electrical hazards, employees can select the correct PPE for the maintenance project.
Maintenance employees are exposed to more electrical hazards than in the past. Technology advances have caused an increased risk to maintenance employees due to the number of devices using electricity as an energy source. Most of the electrical incidents employers investigate are caused by an employee’s lack of understanding on how to protect themselves from a hazard that they cannot readily see.
According to the most recent United States Bureau of Labor Statistics data from the Census of Fatal Occupational Injuries, 126 workers died due to exposure to electricity in 2020. This was the lowest level since the survey started in 1992. But that is not to say the risk is going away anytime soon.
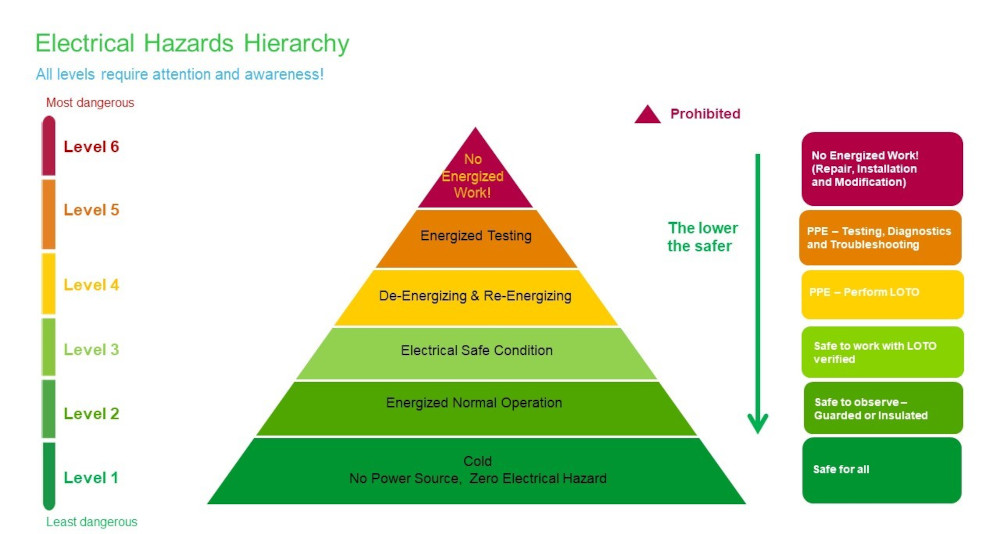
Another factor that increases employee electrical safety risk is the current labor market conditions. Employers rely on our people to work more hours and do more with less. The lack of electrical preventive maintenance programs, fatigue and subsequent human error are factors employers cannot ignore. Employers cannot forgo an equipment PM, qualified employee training, a hazard analysis for the task or situational awareness to recognize when a condition is unsafe just to keep our facilities running.
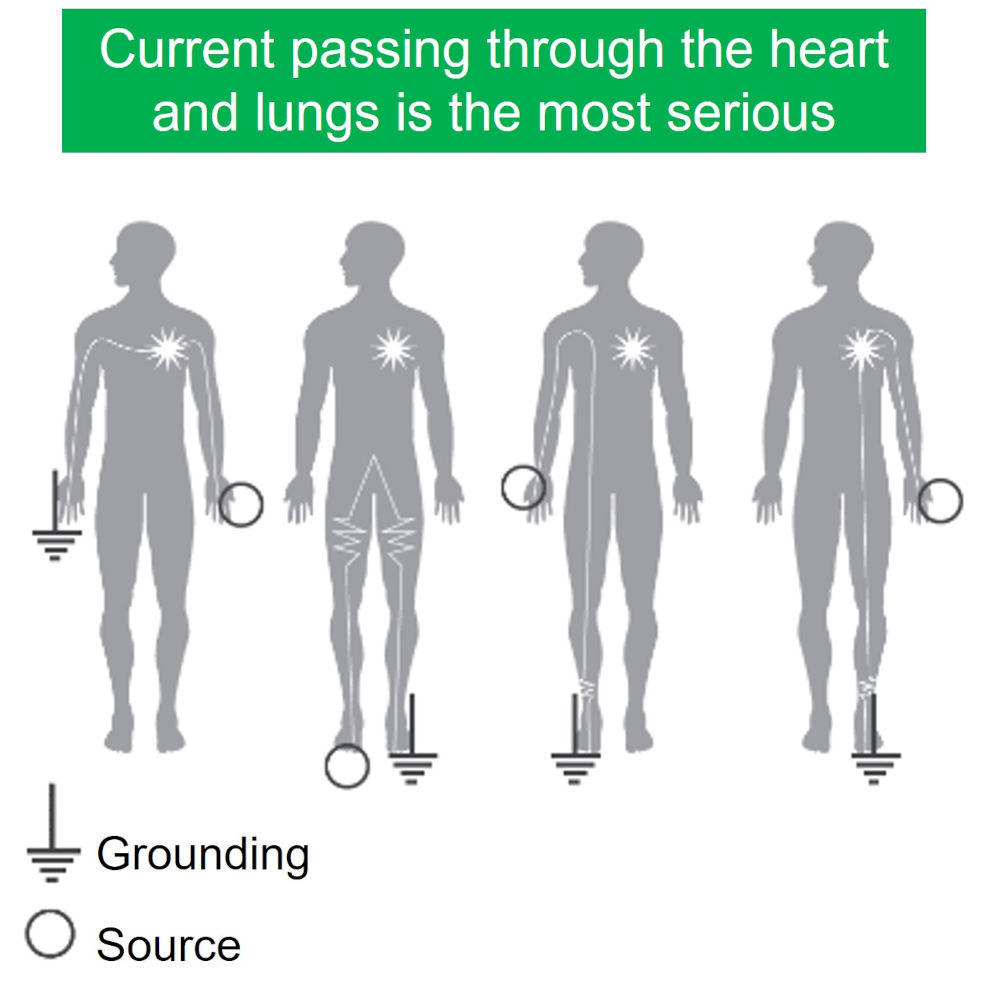
The problem is that electrical energy creates an unseen opportunity for exposure that increases the risk of injury. For example, exposure to electrical shock can range from internal organ and muscle damage to burns and possible death. Arc flash events can cause death due to an explosive projection of molten material, concussive blast, toxic gas exposure, fire or falls.
Consensus standards such as NFPA 70E: Standard for Electrical Safety in the Workplace have been in existence for more than 40 years and have been incorporated by reference into regulations for more than 30 years.
Therefore, it is not enough for a maintenance employee or their supervisor to plead ignorance for not providing or wearing personal protective equipment after an electrical incident. Employees working with electrical systems must understand the proper shock and arc flash PPE to wear when working around exposed energized conductors operating at or greater than 50 volts alternating current or direct current.
Whether an employee is working on a 120 Vac light switch, a 480 Vac heating, ventilation and air conditioning unit, power distribution panels or any other type of equipment with exposed energized conductors, it is imperative that they protect themselves and their co-workers from the hazards of electricity.
Understanding electrical hazards
First, let’s look at the electrical hazards hierarchy to understand when maintenance employees are at a higher risk (see Figure 1). Each step of the electrical hazards hierarchy has equal importance to overall safety, with risk reduction varying between the steps.
For example, levels 1 to 3 are designed to control the risk before it gets in close proximity to the employee. Levels 4 to 6 assume that the employee is already exposed to the electrical energy and needs to be kept safe while he or she is close to the hazard by using the appropriate PPE.
PPE is the least effective risk control method and should only be used as a last resort. Employers should first eliminate the hazard by creating a zero-energy state using lockout tagout (level 3). But even the act of de-energizing to create an electrically safe work condition and reenergizing to return to normal operation (level 4) requires employees to wear the appropriate shock and/or arc flash PPE before performing maintenance work.

Shock protection PPE
Employers know that high voltages are dangerous, and low voltages can be extremely dangerous as well. Shock injuries are dependent on the magnitude, frequency, path and time duration of electrical current through the body. All other factors being equal, the degree of injury increases the longer the body is in contact with the circuit.
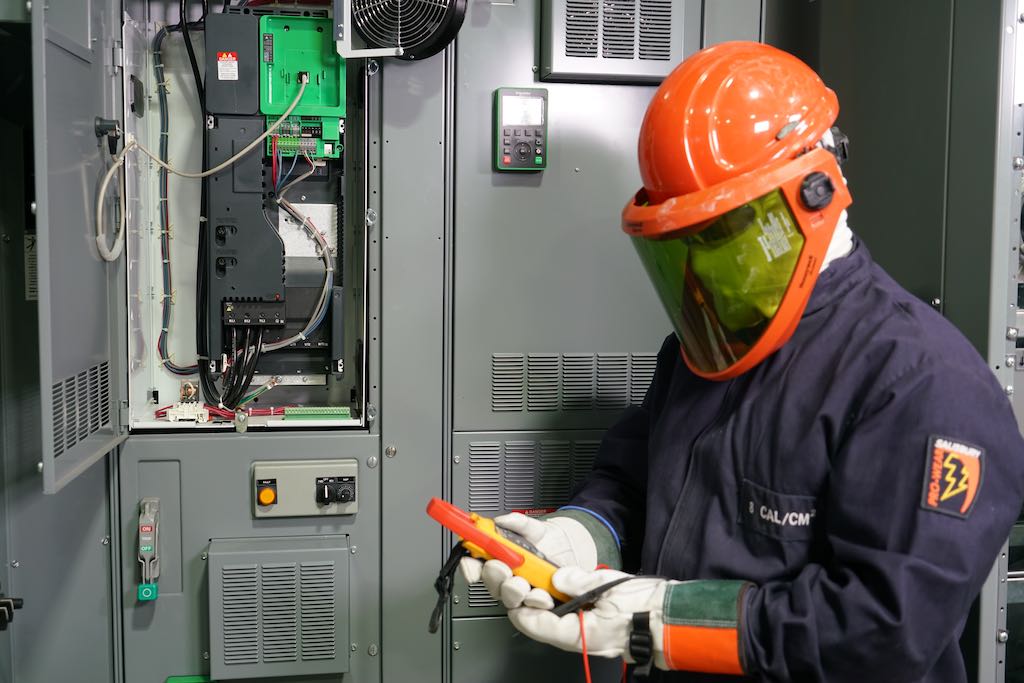
As long as there is voltage present, it will try to push any available current (as low as 5 to 10 milliamps) through the body. When making contact with an energized conductor electricity will travel throughout the body – looking for a path to return to the source, which in most cases is via the ground. (see Figure 2). The path it takes is critical. When it travels through the chest area, including the lungs and heart ventricular fibrillation (stopping of rhythmic pumping action) may cause a very serious injury.
For shock protection PPE, NFPA 70E section 130.7 requires:
-
Rubber insulating gloves (tested up to the voltage the technician is working with) and leather protector gloves (gauntlets) over the top of the insulating gloves.
-
Electrical hazard rated footwear (as needed).
-
Class F or E rated hard hat (as needed).
-
Safety glasses or goggles (as needed).
-
Rubber insulating sleeves (as needed).
In addition, to protect against electric shock, it is important to not wear any conductive items (jewelry, belt buckles, etc.) that could come into contact with exposed energized electrical conductors.
Arc-rated PPE
In addition to the shock protection PPE noted above, if the hazard analysis indicates an incident energy of 1.2 cal/cm2 or more, the use of arc-rated PPE is required. NFPA 70E Table 130.7(C)(15)(a and b) specifies arc flash PPE category 1, 2, 3 or 4.
The higher the category number, the more protective the PPE is to prevent a burn injury. In addition, any underlayers that are worn beneath the arc-rated PPE must also be arc-rated or nonmelting untreated natural fiber. If the risk assessment determines the level of hazard is greater than the available PPE, even if the work is allowed, it should not be carried out.
Why do workers need PPE?
The electrical hazards that exist can cause serious injury or death to maintenance workers. Employers should have very strict expectations and requirements for anyone that is working around electricity. Despite years of experience and training, maintenance workers still suffer injuries related to electricity on the job.
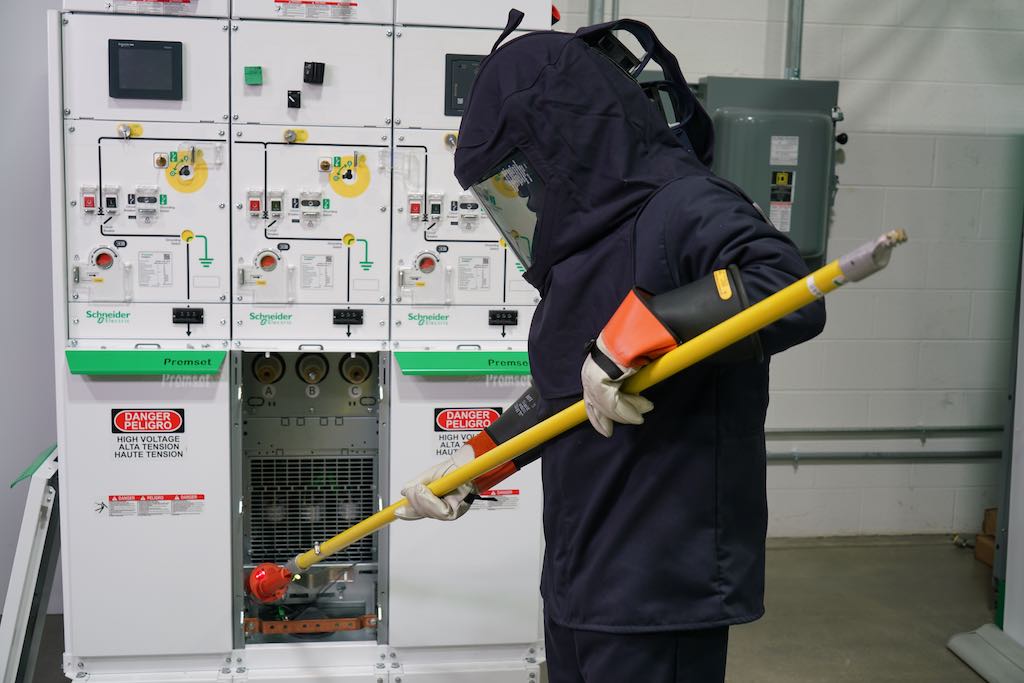
Many employees who work with electricity don’t believe that an accident will happen to them, but records prove otherwise. Employers and employees must work together to make improvements to electrical safe work practices. Automobiles did not always have seatbelts, but because we do, traffic-related fatalities have declined significantly since these inventions have been implemented.