Robotic refueling technology is maturing and expanding beyond the scope of the mining industry and could be used in many applications.
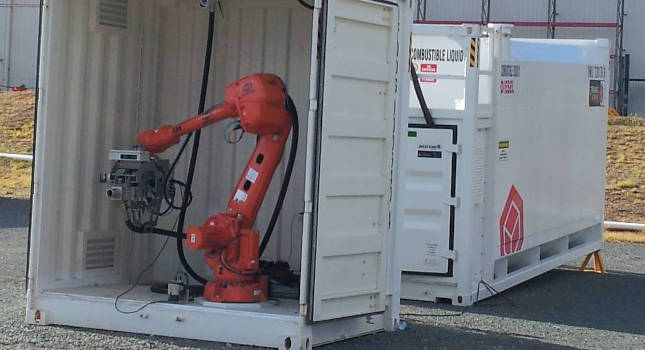
Robotic refueling might seem like a tangent, especially when it pertains to the mining industry, but this technology is worth a closer look as it matures and begins to move into other industries and markets.
SCOTT Technology Ltd. is a 100-plus-year-old engineering company headquartered in New Zealand, with operations in Australia, North America, Europe and China. SCOTT has deep roots in appliance manufacturing systems and automation, but over the last two decades began diversifying into new regions and through strategic acquisitions in everything from sample preparation laboratory equipment for the mining industry, to meat processing technology and logistics automation. Their robotic refueling program developed over the last five years.
The Robofuel system consists of a self-contained industrial robot with a custom end effector, sophisticated sensing systems and proprietary software designed to enable autonomous refueling of massive mining trucks. The mining space provides a structured environment in which to launch and fine-tune this technology, but SCOTT sees broader potential.
“For our sensing systems to be able to locate a vehicle, determine the condition of that vehicle, and then position itself and perform some activity, in this case pumping diesel, most of those same algorithms and solutions can also be targeted at any number of other applications,” said Steve Russell, SCOTT’s director of mining. “Our Robofuel system refueling mining trucks is really the low-hanging fruit and it’s the logical starting point, but there are many other applications that we see in the future.”
Russell cites examples like replenishing railway locomotives, road transportation, or other mobile or semi-mobile vehicles. Instead of diesel, it could be lubricants, coolants or other types of fluids. Or it doesn’t have to be fluids at all. It could be loading railway cars or semitrailers with grain or sand, any applications that require personnel or activities around locating, coupling, connecting and other labor-intensive actions that have an impact on productivity, and more importantly, on safety.
“A lot of what we’re doing when we’re automating and innovating is addressing safety challenges,” Russell said. “When you’re looking at refueling mining vehicles, it’s heavy work, it’s dangerous work in and around large machinery. And with autonomous trucks becoming more prevalent, that is only increasing those safety challenges in trying to use manual operations to serve automated equipment. Safety is front and center in everything we do. However, it can be very challenging to build a business case around safety alone, because a lot of those challenges are difficult to quantify.”
Less refuel time, more production
It comes down to productivity. For this reason, SCOTT is primarily interested in more structured spaces – industrial, civil, mining – applications where they readily see advantages through productivity and safety gains.
“Robotic refueling allows us to improve the time that it takes to refuel by 60 to 70%,” Russell said. “That’s productive time that truck can remain on the circuit. That adds up to more tons of material moved, or the ability to do the same amount of work with a smaller fleet. If we can do the same work of a fleet of 50 trucks with only 49 or 48 trucks, that’s a significant savings over the life of an operation.”
Although less significant, there’s also labor savings because you don’t need a manual fuel attendant standing wait at the fuel farm. Robofuel can also handle heavier hoses, so it can pump fuel faster for even greater productivity, while saving personnel from ergonomically challenging tasks. Another benefit of autonomous refueling is less spillage and less waste.
Robofuel can be retrofitted to an existing fixed refueling facility, or it can be located on the mining circuit or in the pit itself to save transit time between refuels. The system can also be moved around as mining operations evolve.
The entire system is assembled in the shipping container at the factory. Then it’s ready to deploy and redeploy as needed. The door on the container automatically closes in between refueling activities, so the robot and its control systems, which occupy the back-half of the container, are protected from the elements. Russell said they chose an articulated industrial robot for its flexibility to be able to locate and align to the vehicle.
A long-range RFID reader detects a vehicle as it approaches. Laser scanning systems evaluate the local area and are part of the safety perimeter system. Exclusive to SCOTT, the vision-based primary sensing systems assist the robot in locating and removing the fuel cap, inserting the fuel nozzle, and reattaching the cap when refueling is complete.
Robofuel is fully autonomous and doesn’t require any direction from the vehicle driver. In the case of autonomous haulage systems, Robofuel communicates directly with the vehicle. There’s no requirement for remote control.
“Our customers to date have been the large mining operations that have larger trucks and larger fleets. That’s where we see the best payback,” Russell said.
The productivity gains of robotic refueling are readily apparent in this industrial setting. In the consumer market, roboticized gas stations are just starting to emerge in parts of the world.
Robots at the pump
In Finland, pilot programs are underway with robotic gas station attendants. Now Finns can have their petrol autonomously pumped. Developers of this technology expect people with reduced mobility, fueling stations located in areas with very low temperatures, and the autonomous vehicle market to benefit the most. Full-service gas stations could make a comeback.
Tanya M. Anandan is contributing editor for the Robotic Industries Association (RIA) and Robotics Online. RIA is a not-for-profit trade association dedicated to improving the regional, national, and global competitiveness of the North American manufacturing and service sectors through robotics and related automation. This article originally appeared on the RIA website. The RIA is a part of the Association for Advancing Automation (A3), a CFE Media content partner.