Laser scanning and 3D modeling technologies continue to transform engineering and design capabilities, resulting in highly accurate data captures of existing facilities and constructible designs for an integrated view of the design/build process.
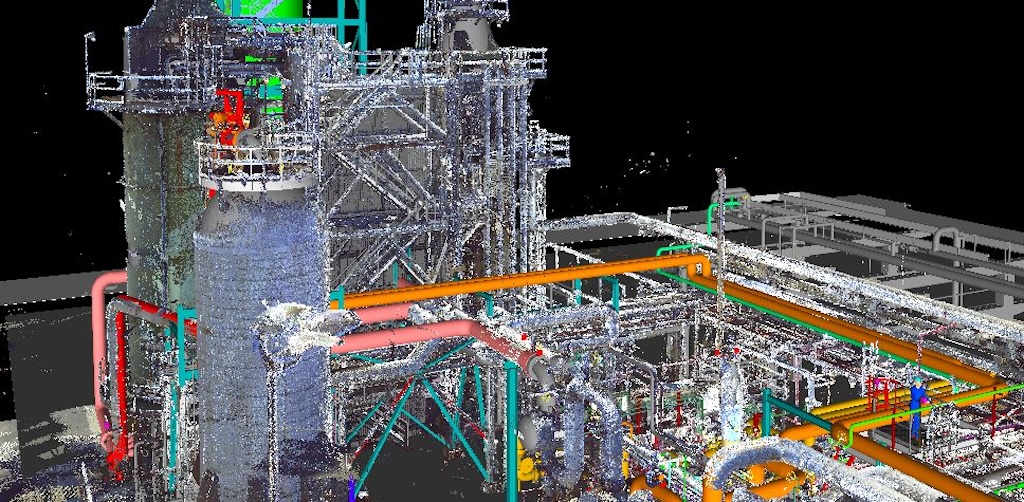
Learning Objectives
- Understand the basic operations and benefits of laser scanning and 3D modeling in the design and build phases of a project.
- Know the three top challenges of performing laser scans in the field and employ the solutions that ensure successful results.
- Discover where laser scanning and multidimensional modeling technologies are going in the future.
Laser scanning insights
-
- Designers and engineers use 3D modeling software to better predict a project’s scope and cost.
- Engineers and designers can use scans to produce 360-degree full-color photographic images to better view a project.
Industrial facilities operators and owners rely on standard engineering design tools. Tools like laser scanners and 3D modeling provide multidimensional, matrixed models of facilities to foresee design conflicts and optimize layouts, reducing project risk.
The virtual models rendered from laser scans, which use millions of intersecting points gathered per second, provide owners with project progression, cost oversight and critical facility layout information to enhance decision-making.
Multidisciplined engineering teams can laser scan as-built facilities, assets and other details that may impact project scope using precise point-to-point measurements at 976,000 points per second for 1/16th of an inch field measurement accuracy (see Figure 1).
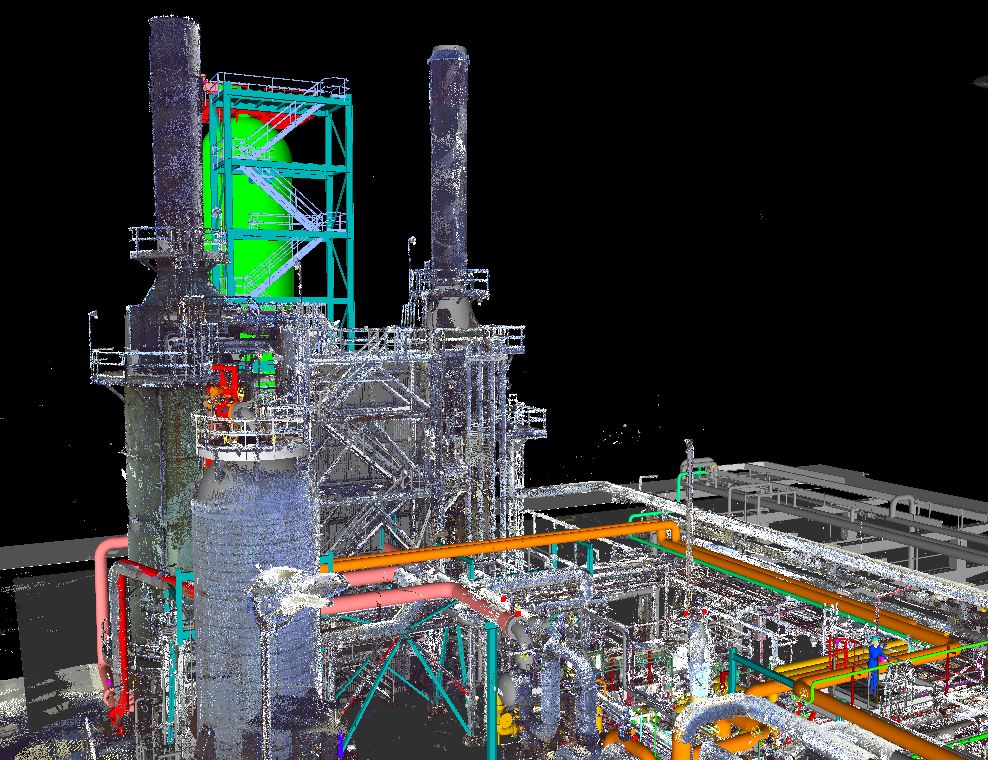
These precise measurements are then used to produce 360 degree full‑color photographic images from each scan location so that engineers and designers can build 3D as-built point cloud design models.
“Our technicians perform thousands of lasers scans a year across hundreds of complex engineering projects in the energy, sustainability and advanced manufacturing sectors,” said Rod VanderWerff, resource manager of piping design at Anvil Corp. “Laser scans give us the ability to safely capture high-resolution images even in hard to access, confined spaces like storage tanks, pipe ways and other process equipment.”
Scanning constricted, underground areas, such as electrical vaults, has traditionally been a difficult and unsafe procedure. With laser scanning, technicians can now lower the scanner in an inverted position to capture the images, maximizing both productivity and safety.
Conducting virtual, 3D model walk-throughs in real-time from anywhere in the world, engineers, designers, owners and constructors can collaborate to:
- Identify line and equipment tie-ins for highly accurate piping and instrumentation diagrams (P&IDs) and to greatly reduce field welding during installations.
- View in real-time the changing conditions in an industrial facility or refinery before, during or after revamps and extensive mechanical work.
- Plan for constructibility and operability to minimize field work.
- Document what has not been documented when facility drawings are inaccurate, not available, outdated or when new designs need to align with old designs.
Using programs like Autodesk 3D Studio Max or AutoCAD video tools, engineers and designers can animate 3D models to produce overlays such as 4D schedule models depicting work packaging and sequence of construction activities on moving timelines highlighting schedule milestones further overlaid with 5D cost models and 6D life cycle models depicting the project’s life cycle after construction (see Figure 2).
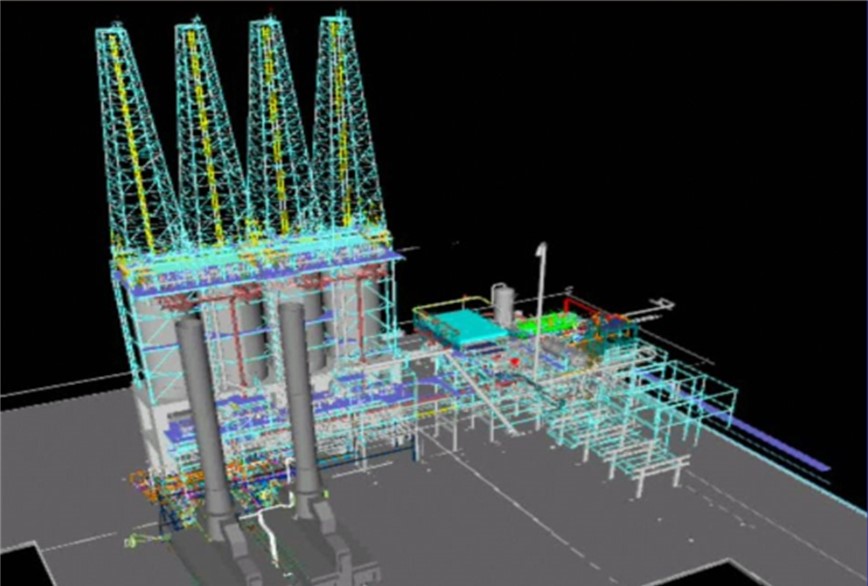
However, there are several factors that can impact the accuracy of the laser scans in the field, such as technician training, adverse weather conditions and motion.
Top three challenges when planning laser scans
Challenge 1: Scan technician training
While advanced laser scanning technologies continue to assist the way facilities are built or revamped, it is still the scan technician who knows how to best capture the scope of each highly detailed job, know the equipment and its parameters, grasp the dos and don’ts of target placement, maintain requirements and calibration schedules and understand the nuances of registration software.
Capturing laser scans in the field is the easy part of their job ¾ knowing how to gather the data while keeping it highly accurate, especially with target-based registration, takes many man hours of training and experience with the product providers to understand how it all works together (see Figure 3).
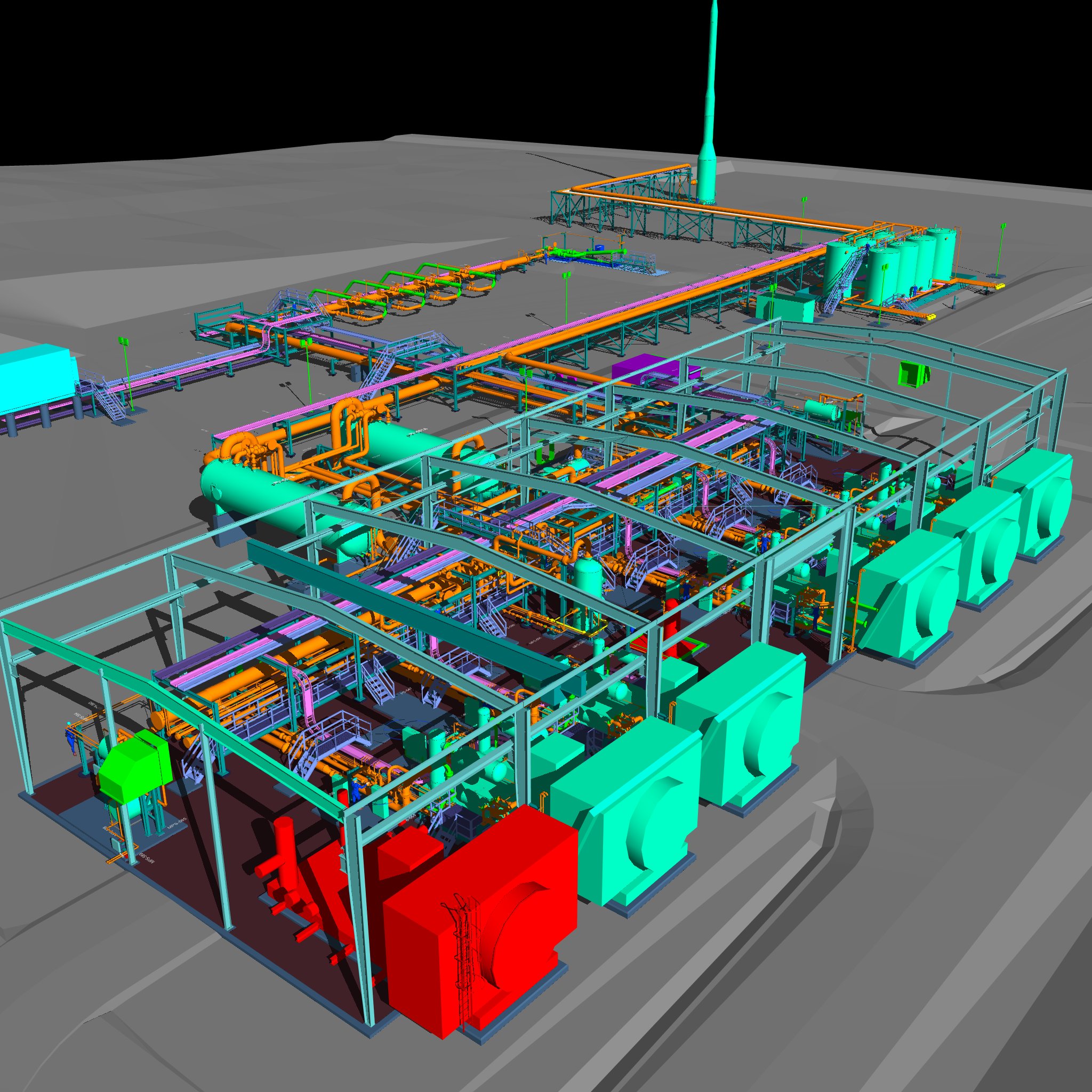
Challenge 2: Adverse weather conditions
Condensation in the air, such as rain, hail, snow, fog or even steam, distort laser scanned images captured in the field. Although water- and dust-resistant, laser scanners still pick up anything they see.
Whether a smudged image from water droplets on laser scan lens, solid condensates from snow or hail that distort light or fuzzy images from reflective and fast-falling rain, precipitation distorts the air and blocks laser scan targets, resulting in inaccurate and unusable scans (see Figure 4).
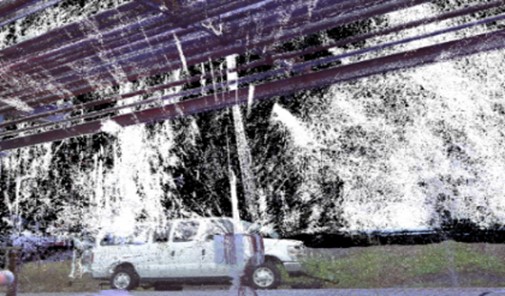
Wind, on the other hand, can also cause issues due to the laser scanner being a precision measuring instrument. A laser scanner spins 36oº on its base while a spinning mirror projects the laser everywhere except 3oº down so it doesn’t scan itself and the tripod area.
As a scanner tries to scan at a precise, steady and slow pace, heavy winds get in the way, moving the head and spinning the mirror faster or slower than the scanner can perform. Even wind gusts at 20 mph have a vibrating or shaky effect on the scanner, distorting the point cloud and producing inaccurate images. For this reason, windy regions of the U.S. require proper tripods that resist shaking and vibrations.
The only way to counter adverse weather conditions and provide the highest quality laser scans, especially during winter months, is to scan locations outside of normal workdays and hours and to scan as much as possible on dry, low-wind days. Locations like Hilo, Hawaii, that experience 276 rainy days a year on average, for example, require more scanning flexibility where it becomes more advantageous to scan indoors on humid, rainy days (see Figure 5).

Challenge 3: Motion
Laser scans are best suited for capturing things that don’t move. However, continual movement of people and vehicles occurs at most industrial facilities.
When laser scanning facilities in continual movement, ghost images can appear in scans. The solution is to keep people from walking and driving in the scanned locations while the scanning process is taking place.
The future of laser scanning and multidimensional modeling
Advanced equipment and innovative techniques. Laser scanning manufacturers continue to upgrade their equipment and software to innovate quicker terrestrial target-based laser scanning techniques that capture greater levels of accuracy over larger distances and over shorter periods of time.
For example, a scan location today can take minutes, to tens of minutes, depending on the level of detail to be captured, but with emerging and more advanced laser scanners those same scan locations can capture the same data in half the time. This is notable when considering that the field portion of a typical laser scan set to density needs, such as scanning a refining unit, can span a week or more.
Cutting the time to scan each location by half will significantly reduce the amount of time in the field, resulting in faster and larger amounts of data capture and saves the owner money in the process.
New registration algorithms. Registering target-based laser scans today is a time-consuming process, using elaborate algorithms to find all the targets (spheres) in the field and then for a laser scan technician to assist and verify the program’s ability to locate and point out the corresponding targets on other scans (i.e., target-based registration).
Engineers and designers hope that one day, they won’t have to carry checkerboard targets or up to a hundred or more spheres with multiple storage cases back and forth to facilities to register the scanned data.
The future will rely on more powerful algorithms to automatically locate and integrate adjacent scans for the overarching virtual view of the facility (i.e., cloud to cloud registration).
Alternative laser scanning technologies. Emerging technologies continue to change the laser scanning landscape, such as attaching a laser scanner to a drone and flying it around areas that are currently hard to reach with a scanner and tripod.
While drones can quickly capture scanned data because of the height advantage, the downside is that it currently is not the ideal method for accurately capturing certain forms of data (i.e., density levels of certain units or areas in a facility).
The future holds promise that both drones and other mobile devices are advancing to capture more levels of detail that can mesh with terrestrial laser scanning data for highly accurate results than what is currently occurring in the field.
How laser scanning and 3D modeling benefit various teams
In summary, laser scanning and 3D modeling technologies continue to transform engineering and design capabilities, resulting in highly accurate data captures of existing facilities and constructible designs.
These technologies significantly reduce field time and exposure to potential risks while greatly improving design efficiency and accuracy, incorporating animated schedule and cost data for an integrated view of the design/build process. In addition, laser scans are useful for onsite and remote site training.
There are benefits across multiple disciplines. Some of these include benefits for:
Industrial facility owners
- Reduces change orders, interface issues, installation adjustments, potential errors and field time calculations
- Enhances decision-making
- Provides project oversight
- Drives down project costs
Engineering/design teams
- Minimizes field work
- Produces accurate P&IDs
- Provides faster micro project response and turnaround times
- Increases efficiency and quality
- Promotes a safety-first culture by reducing field time and exposure to high‑risk activities, such as taking measurements at high elevations
Constructors
- Provides a constructible design
The wave of the future holds a lot of promise as laser scanning manufacturers continue to unlock the potential of point cloud technology and multidimensional modeling by integrating today’s technologies with artificial intelligence and predictive analytics for more speed, precision and automation.