Costs lowered, greater interoperability from module type package standard
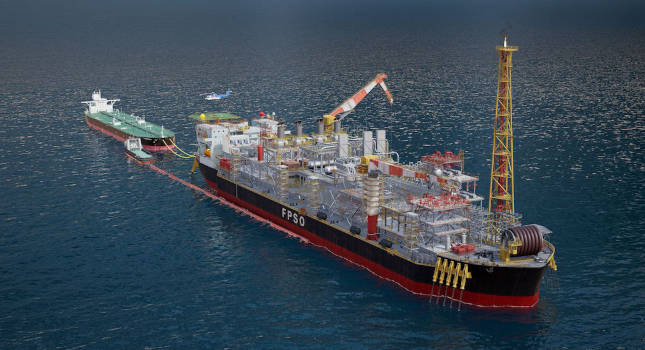
On its face, there’s lots to like about modular automation. Breaking a production facility into modular units – or modules – is a good way to build, maintain and upgrade production systems. At the same time, it can be very industry specific.
In oil & gas, modular automation offers significant savings across the lifecycle of a floating production storage and offloading unit (FPSO). A vessel owner/operator can see up to a 50% reduction in capital expenditures for automation engineering and as much as a 20% reduction in costs to manage an FPSO unit over the course of a vessel’s lifecycle.
However, to realize the potential of modular automation the industry must come together around a common objective. Specifically, vendors need to agree on a standard that enables interoperability across systems and reduces the need for FPSO operators to develop expensive custom interfaces for different vendor systems to speak to each other.
For decades, traditional modular automation systems were built with proprietary technologies connected through customized solutions. But the oil & gas industry is close to having a set of guidelines known as the Module Type Package (MTP) standard that eases integration.
What is the MTP standard?
Modular automation as a concept has been around for decades. Yet COVID-19 reinforced the value of an established industry standard.
When the pharmaceutical industry needed to produce millions of COVID-19 vaccine doses at an unprecedented rate, a traditional automation engineering approach required a series of custom integrations to each OEM module’s automation to speak properly with one another – a solution that would have set global production back by months and put countless lives at risk. The key to bringing vaccine production online quickly was the industry agreeing to a common set of modular automation principles that enhanced interoperability and allowed key automation functions in each module to connect with ease. The learnings from this unprecedented ramp-up in vaccine production are reflected in the MTP standard being developed.
Similar benefits can be realized in oil & gas operations. FPSO vessels typically comprise 15 to 20 major modules that manage essential operations, including water treatment, gas compression, oil separation, power generation and more. The MTP standard could prove invaluable by enhancing operability of system modules.
To understand the profound impact that the MTP standard can have on FPSO vessels, think of what the USB port did for the PC.
Prior to the USB port, PC users had to contend with a wide range of ports and cables for different devices – not to mention tedious installation processes. But now, most devices are on a common cable and port and are essentially plug and play.
A similar principle applies to industrial automation – if the vessel’s master control system can integrate with each module’s OEM-supplied automation system, it simplifies the overall automation engineering of the vessel build process and opens up a world of possibilities for upgrading systems and improving operations over its lifecycle.
The concept of MTP was born out of an industry standards initiative from NAMUR. With over 150 member companies represented across the globe, NAMUR has been a leading voice in hastening the industry’s push toward the next industrial revolution. And a core aspect of this initiative focused on modular automation.
By adopting a standard set of modular automation concepts, companies speed up the process of integrating complex systems from different vendors. By building modules to an industry standard, once plugged into a master control system, each module interoperates efficiently – without custom integrations.
With MTP, the human-machine interface (HMI) of the module – which contains all static and dynamic information for operator visualization – generate automatically within the master process control system. Other key automation content onboard the module – such as process control, alarming, and maintenance diagnostics – also become “plug-and-play” with the master control system. And for floating production vessels – which already rely on a modular approach when being built – adopting this type of vendor-neutral interface language could lead to significant flexibility and cost savings for operators.
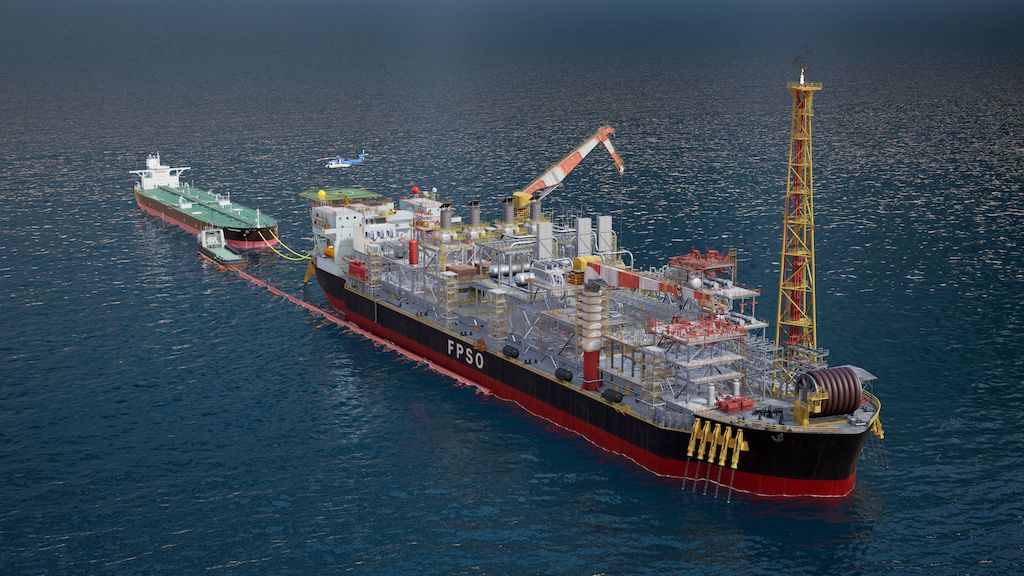
What are the benefits?
The implementation of a standard like MTP is by no means an overnight process – various industry leaders, including Rockwell Automation and Sensia, have been working since 2019 to build out and test the standard. But the effort is undoubtedly worth it. The MTP standard’s adoption will benefit FPSO operators.
Extending the lifecycle of FPSO operations: The typical FPSO vessel has a lifecycle of about 20 to 25 years. To ensure longevity and maintain reliability over time, the automation content on board each module may need updating. Reasons to update over multiple decades are many and compelling and include everything from secure operating systems to significant innovations in vessel automation technology itself.
Adopting the MTP standard will make it easier for operators to integrate packages or skids into a larger master control system, update systems as they age or as new technology becomes available, with relative ease. When modular packages are new or upgraded, the interface investment can be reused for not just “plug-and-play” integration, but less training for vessel operators.
Simplifying vendor packages to better address vessel needs: It’s no secret that vendors benefit from offering proprietary packages, which incentivize vessel operators to work with a single automation provider. And if an operator does attempt to integrate a separate vendor solution, it often requires finding an engineer with specific knowledge of multiple vendor systems to make the different systems talk to one another in the master control system. Skilled labor is already hard to come by and requiring custom solutions can cause backlog.
A single, standardized approach to module interoperability eliminates these issues. With leading vendors taking steps to implement the MTP standard, end users can select the best solutions for a vessel’s custom needs, regardless of the automation content on board, if the OEMs support MTP.
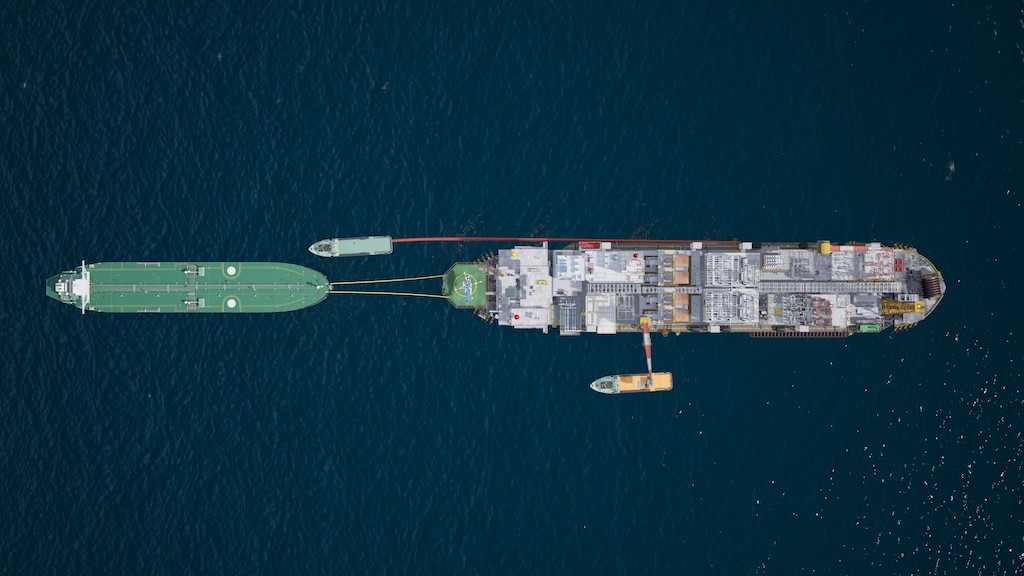
Nearing finalization
When will the MTP standard be a reality for FPSO operators? Unsurprisingly, establishing an industry-wide standard takes time and collaboration from multiple partners, and the standard is still a work in progress. But through the efforts of NAMUR, industry vendors and OEM partners, the MTP standard is taking shape. Parts of the standard are still being refined and tested, but it could be finalized as early as 2023.
Many FPSO operators are used to working with traditional, proprietary systems. However, a proprietary closed automation system on a module drives up engineering costs, limits choice and slows innovation. For suppliers, the vendors that develop those systems, an open automation standard threatens profit margins over a vessel’s lifecycle.
With that said, the impact of MTP is not lost on the industry. Many global energy companies have already issued RFPs for projects that call for the MTP standard. While there may be certain detractors slower to embrace open automation standards, easing adoption of new technologies benefits industry at large.
It’s time to embrace the standard
Developing the MTP standard required significant industry involvement, but will soon be real.
Leading automation vendors, OEMs and end-users – including both owners and operators – are working to develop and vet this standard. As part of this testing process, OEM vendors bring modules to a facility, and participating automation vendors work live to connect all of them into one master control system. These “plug-and-play” tests have been successful so far at each iteration of the MTP standard. Using MTP specifications, the FPSO industry will soon demonstrate that any automation vendor could control all the OEM modules on a vessel, regardless of automation vendor content on board each module.
The MTP standard is still in development, and many in the industry are only just becoming aware of what impact it could have on FPSO operations. But when adopted, the standard has the power to benefit vessel operators and reduce the total cost of ownership throughout a vessel’s lifecycle – and one day, it will be as commonplace on vessels as a USB port on a computer.