You shouldn’t sacrifice productivity—and with a good system, you don’t have to
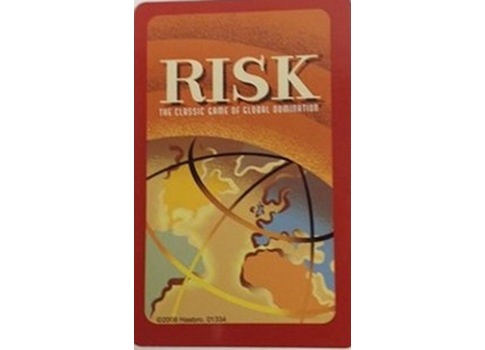
Automated controls require special attention be paid to safety. The most obvious reason is the need to reduce employee injuries, but there are also a wide range of national and international regulations that require attention to safety. Due to advances in technology, networked safety can be easily integrated into existing and aging systems. This is particularly beneficial as knowledge of process and machine safety proliferates.
This article will discuss the steps plant engineers must take to meet global regulations and provide best practices to increase employee safety, improve product quality, and reduce costs in today’s high-performance connected world.
Many safety governing bodies, such as the OSHA and the IEC, have imposed regulations to make automated machinery safer. While these regulations are meant to ensure worker safety, they are forcing machine builders to update their designs in order to comply with these new regulations, even if they are operating outside of the impacted region or country.
In order to meet these regulations, plant engineers must keep employee, machine, and process safety top of mind when installing high-performance automated controls. While safety is of the utmost concern, there are many other factors that can affect an engineer’s ability to properly install machine safety protocols and controls that meet the standards, including aging systems and reduced budgets.
The drive for easy integration
Companies today are certainly seeing the benefits of the risk avoidance protection found in safety systems. However, in some instances they are facing requirements for certified safety systems, from either internal or external drivers, particularly as more and more devices are connected to the industrial Internet. In these cases, easy integration with the right level of diagnostics is the key.
Internal drivers, besides the obvious need to reduce the probability of work-related injuries, are factors that impact productivity and asset utilization. Safety systems can improve the lifecycle of machinery while providing operators greater access to machines under different modes of operation. Instead of powering down a machine to perform maintenance, modern safety solutions allow mode-dependent operation limits such as safe speed, safe torque, and safe position to be established.
Safety function blocks are the safe equivalent of normal application program function blocks used in many high-performance automation controllers such as PLC and PAC controllers under the IEC 1131-3 programming languages. Function blocks are considered a graphical programming method, as opposed to a scripted language, since the user simply drags and drops the desired function block into the workspace and then proceeds to make the various connections and variable assignments to define each block.
Safety function blocks are generally configured to allow easy integration of safety devices such as two-hand switches, light curtains, emergency stop push buttons, etc., into control programs. Safety function blocks can then be connected together using various logical elements (AND, OR, NOT, etc.) to specify which action should be taken by the safety devices under certain conditions. Developing safety control logic using function blocks in a pre-certified safety programmer greatly simplifies the engineering effort required to realize complex safety solutions.
High-speed industrial Ethernet protocols, like PROFINET, allow for these new controls to be installed quickly and easily even when retrofitted to an existing system. PROFINET is a high-speed, high-performance network with the ability to drop large amounts of I/O without compromising performance. Among its strengths is the ability to operate in high-noise areas and cover large distances in real time with an elegant redundancy capability to maximize uptime. PROFINET provides flexible deployment that minimizes hardware and configuration issues, and improves application uptime with minimal cost. The use of media redundancy protocol (MRP) in a ring topology allows customers to take a node down for maintenance, or survive a failure or cut of a wire without ever shutting down the application.
By combining secure network connectivity, certified safety function blocks, and graphical programming, manufacturers can integrate standards-compliant safety capabilities to equipment while simultaneously meeting increasingly stringent regulatory requirements. Networked safety-certified controllers can be integrated easily and cost effectively to new or existing applications by using standard-based protocols like PROFINET. These protocols allow manufacturers the flexibility to create exactly what they need safely and at the right cost.
Taking the next step
Automated safety controls are only the first step in meeting the imposed safety regulations and increasing employee safety. Plant engineers must also implement appropriate safety protocols for the machines and processes themselves. However, there are many differences in machine and process safety, from what, who, and how they affect a plant, to the process they go through to shut down and restart machines.
Machine safety is generally used to protect machines in discrete manufacturing, whereas process safety is related to protecting processes in industries such as chemical plants, oil refineries, nuclear plants, and others, and is governed by IEC 61511.
Manufacturing and other heavy industries like oil and gas, mining, water, and power have many other requirements of their safety protocols, including:
- Machine builders, system integrators, and end users need comprehensive safety solutions rather than purchasing products from multiple suppliers
- Safety solutions that provide the required Safety Integrity Level (SIL) or Performance Level (PL)
- Machines that remain powered when the operator is within the working envelope
- Scalable solutions that can be easily expanded as new requirements are added
- A robust architecture that can tolerate breaks in a network cable or allow devices to be added or removed without shutting the system down
- Solutions that will make it easier to get their machine safety certified.
There are many tools that can help these industries achieve these goals, including:
- Standalone Safety Controllers: Discrete safety relays and safety controllers are added to traditional automation controls to ensure safe shutdown in the event of safety breach
- Safety PLC: Dedicated safety PLC with rack based safety I/O
- Hybrid Distributed Safe I/O and Safety Logic: Safe I/O are distributed via a network with dedicated safety logic for each safety island (work cell)
- Safe Motion: A class of servo and AC drives rated for machine safety applications that allow operators to work more effectively within the work envelope of the machine enabling greater productivity.
These tools can be used in several different application types that span many industries, including:
- Automated assemblies like tires, appliances, automotive, and electronic production lines
- Web applications like printing, lamination, and material conversion
- Producing or forming metals and fabrication machinery
- Conveyance operations like storage and retrieval, airport baggage handling, and product transfer
- Packaging machinery and lines
Heavy industry faces an incredibly large number of safety regulations from both national and international bodies meant to ensure employee safety. While meeting these regulations can be a difficult and time-consuming task, it is of the upmost importance and can be conducted in a way that will also increase productivity and lower costs while keeping employee safety top-of-mind.
Some of the steps plant engineers can take to optimize their safety equipment and procedures include combining secure network connectivity, certified safety function blocks, and graphical programming with proper machine and process safety tools depending on the industry.
If plant engineers and machine builders follow these steps, they will be able to meet the stringent safety regulations while simultaneously increasing operational efficiency, improving reliability and operational metrics, which leads to future costs savings and quickly recouping any installation costs.