Paying more to improve a company's electrical safety in the short-term will provide a tremendous return on investment (ROI) in the long run because companies will avoid paying for workplace injuries and violations.
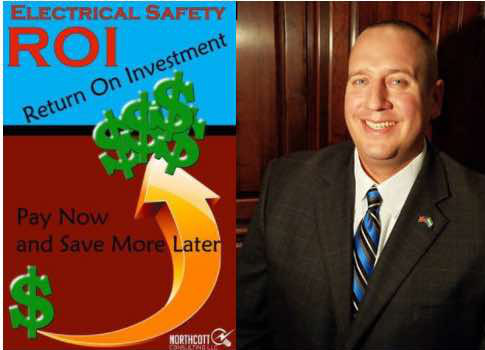
According to the American Society of Safety Engineers (ASSE), a Liberty Mutual poll of executives shows that for every $1 spent on direct costs related to an accident, there are another $3 to $5 worth of indirect costs… putting the actual cost of an accident (with direct medical and compensation costs of $15,000) at somewhere between $45,000 and $75,000.
Most polled executives said that for every $1 their company spent on workplace safety, they saved at least $3. In a recent poll of financial decision makers the participants perceived that on average, for every dollar spent improving work place safety approximately $4.41 would be returned.
Safety’s return on investment (ROI) is dependent on knowing one important thing: How much does an injury actually cost? The various cost factors of an injury fall into two categories: direct and indirect. Direct costs are the more obvious ones such as workers’ compensation insurance, medical expenses, property damage, civil liability awards, and related litigation expenses. Indirect costs include OSHA fines, attorney fees, workplace disruptions, loss of productivity, employee replacement, training, and insurance premium increases.
OSHA has developed an estimator tool that helps to put these costs into perspective. This tool can be used to assess the impact of occupational injuries and illnesses on the company’s profitability. It uses a company’s profit margin, the average costs of an injury or illness, and an indirect cost multiplier to project the amount of sales a company would need to generate to cover those costs. For electric shock, OSHA statistics show the average direct cost of one injury to be $86,528. Based on their data, OSHA’s direct to indirect cost ratio for electric shock results in $95,180 in indirect costs. This means that the average electric shock injury costs the employer $181,708.
The reality is that the amount of the direct cost paid by the employer is going to vary based on the company’s workers’ compensation insurance policy. However, the employer always pays the higher indirect cost. What is even more interesting about OSHA’s tool is that an employer can enter their profit margin and determine what it will take in additional sales to cover the cost of the injury. For an electrical shock injury with a company that has a 3% profit margin, the company would have to have an extra $3,172,693 in product sales to cover the indirect cost associated with the injury. It would take $6,056,933 in additional sales to cover the total cost of the injury.
From a strict business model approach, industry data supports the reality that taking a proactive approach to funding an effective safety program to avoid injuries is a more economical approach than the alternative. The money an employer spends on training, PPE, and other services or tools that promote a safety conscious work culture will more than pay for itself over the tenure of the employees. Let’s look at an example and consider a business with 20 electricians.
We have already learned that there is an average cost of $181,708 if one of those electricians gets injured from electric shock. One action that can be taken to reduce the probability of any of those 20 electricians being injured by a shock would be to have an electrical safety program developed and send the electricians through an electrical safety training course.
Let’s assume that these efforts reduce the probability of the electricians receiving the shock by 75% resulting in the benefit of avoiding $136,281 in injury expense. While many variables drive the cost of an electrical safety program development, a fair estimate would be $25,000 and $4,000 for onsite low voltage safety training for the electricians. The equation for ROI is as follows:
Using our conservative numbers, the ROI of our example is ($136,281 – $29,000)/$29,000 = 3.69. What does this mean? This means that for every dollar your company spends on these safety improvements, you will be saving $3.69 in the future. After evaluating this data, most CFOs would have a hard time finding equally valuable opportunities for investing the company’s money. The challenge is, unless a company is already trending injury rates, it is difficult to dogmatically validate the avoidances through improved safety culture. But even more savings beyond the simple ROI calculation exist.
One tangible savings opportunity comes from a reduction in lost-workday accidents lowering the experience modification rate (EMR), which can decrease a company’s workers’ compensation premiums.
Some intangible benefits exist as well. The NFPA 70B Recommended Practice for Electrical Equipment Maintenance identifies one of these benefits: Improved moral comes with an employee awareness of a conscious management effort to promote safety by reducing the likelihood of electrical injuries or fatalities, electrical explosions, and fires.
Finally, the most significant and typically overlooked return on your investment toward electrical safety culture is peace of mind. This comes from knowing that your employees have the knowledge, tools, and encouragement needed to execute their work safely and return home to their loved ones at the end of the day. One of the worst tasks a manager or business owner can do is make a phone call to an employee’s emergency contact to inform them that their loved one has been injured and on their way to the hospital. While this concern for fellow humanity should be sufficient to justify the capital investment needed for maintaining a proper safety culture, it is encouraging to know that there is also factual financial evidence to support spending money on safety now in order to save money later.
Has your company made the right investment in electrical safety?
Tommy Northcott earned a BS Degree in Electrical Engineering with an emphasis in Power Systems from Tennessee Technological University. He is a Professional Engineer licensed in the State of Tennessee and a Certified Maintenance and Reliability Professional. Tommy has well over a decade of experience working with one of the largest electric utility systems in Tennessee as a Systems Engineer, Arc Flash Project Manager, Operations and Maintenance Manager, and Reliability Engineering Manager. Currently, Tommy is the President of Northcott Consulting LLC and specializes in Electrical Safety Training and NFPA 70E and OSHA compliance. For more information visit www.northcottconsultingllc.com and feel free to email questions or comments to [email protected].