Replacing seats and valves, a costly expense for oilfield operators
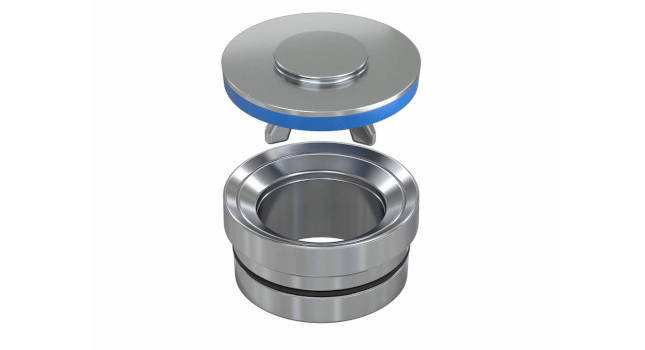
The oil and gas industry has witnessed intense disruption due to multiple factors, including oil and gas companies’ declining revenues, increased competition from renewable energy, growing environmental concerns and lower oil prices due to excess supply. The global pandemic has added greater complexity and pressure into the mix. Operating cost containment is always an important consideration for businesses in the field, but as crews’ pumping schedules continue to be interrupted it’s become even more imperative to find new ways to lower those costs.
Oilfield service providers are pushing their frac fleets harder than ever, leading operators to focus on improving pump utilization and reducing downtime for pump maintenance. Valves, seats and packing are the largest maintenance expenses on a frac site, and companies are naturally focused on reducing costs related to fluid end maintenance and downtime. In the current climate, it is especially crucial that operators improve the efficiency and reliability of their fleets.
Lowering operating costs and reducing unplanned downtime is an ongoing challenge for oilfield service companies. Pushing costs from good to better is possible as technology evolves and offers companies a competitive advantage if continuous improvement is a perennial primary objective. Even in once-in-a-lifetime circumstances, it is possible to leverage technological advances to reduce costs and nonproductive time (NPT).
An oilfield service provider operating pumps in the Permian wanted to improve operational efficiencies on its multi-well pads by reducing maintenance expenses and NPT. The resource-rich Permian Basin is one of the most active plays in North America. Unlike other shale plays, the Permian has greater geologic complexity, which can put increased pressure on equipment and increase consumables costs. When pumping 550,000 to 650,000 pounds of 100-mesh sand per stage at 8,000 to 11,000 psi, standard steel seats were only lasting 60 to 100 hours for the provider. The company was replacing seats every 80 hours, resulting in high materials and labor costs.
To improve operational efficiency as well as worksite safety, the company wanted to find a way to stop pulling seats in the field. If there’s one maintenance protocol crews would like to eliminate, it is pulling seats. Replacing seats and valves is one of the costliest expenses an oilfield service operator incurs, and also one of the most frustrating.
To help achieve their goal, Weir Oil & Gas’ team recommended the company use a new technological advancement, SPM EdgeX Carbide Seats. The EdgeX Carbide Seat offers greater resistance to wear, cracking, and washout – even with large particles present. Extensive lab and field testing showed the EdgeX Carbide Seat provides an average of six times longer life than a conventional steel seat. The carbide-reinforced seats were designed to protect high-wear areas while fitting standard taper fluid ends to eliminate installation error sensitivity.
Note: Weir Oil & Gas recently was acquired by Caterpillar Inc. and operates as SPM Oil & Gas.
Weir’s patented SPM EdgeX Valve and Carbide Seat sets a new industry standard by increasing seat life an average of six times and doubling valve life compared to conventional options. It is a timely solution for operators focused on pump utilization and reducing pump maintenance downtime.
Engineered with the nuances of the entire frac site in mind, the EdgeX enables oilfield service companies to push their frac fleets harder while significantly reducing maintenance costs for valves and seats. This dramatic increase in longevity enables operators to eliminate field changeouts and reduce expenses for a costly consumable.
For the oilfield service provider in the Permian, the EdgeX produced substantial results and helped the company achieve its goal. In actuality, the EdgeX Carbide Seats lasted eight times longer than the previous seats. The company ran the EdgeX Carbide Seats an average of 655 hours—delivering approximately 720% longer life than the steel seats previously used which lasted the provider an average of 80 hours. One of the EdgeX seats ran 760 hours, setting a record for the longest-lasting EdgeX Seat in North America.
Maintenance and downtime eat into valuable pumping hours and changing seats in the field can be extremely disruptive. In addition to being a hassle for companies, it also leads to extended NPT and can be dangerous for personnel. Consumables are the single-largest expense for all frac service companies, which is why embracing technological changes that reduce this cost prove valuable.