Select the right management technologies for modernization.
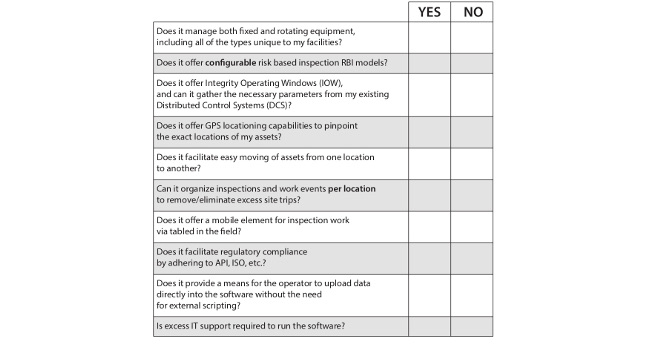
By harnessing the Industrial Internet of Things (IIoT), industrial companies can digitalize their asset integrity management (AIM) processes. This is especially true for the upstream oil & gas sector, where operators must manage a wide variety of equipment types ─ both fixed and rotating ─ across many remote sites.
Most companies aren’t up to date. Instead, they rely on dated technology to manage assets, placing safety and integrity at risk. Further, as other companies around the world embrace digitalization and modernize their plants, it is easy to fall behind – impeding overall profitability.
Technology advance can make a remarkable difference in production capability, profitability, and optimized inspection and maintenance scheduling. It’s possible to garner actionable intelligence from asset data – in real time, all the time – which changes the game for decision making. It significantly reduces unplanned shutdowns and inspection costs, while paving the way for machine learning (ML) and artificial intelligence (AI).
Understanding AIM
The upstream sector of the oil & gas industry faces unique, inherent challenges just by the nature of operations: having to manage a wide variety of equipment types across an equally varied distribution of location sites. Installations that include compressor or pumping stations, filter skids, well batteries and pipelines entail a wide range of typical fixed and rotating equipment. Often the installations are cookie cutter in nature with the same equipment and the same equipment numbers at each location.
It is common for equipment to be moved frequently from one location to another. With facilities often spread out over many remote sites, often hundreds of miles apart, it’s a challenge to track equipment at all locations. This makes it difficult to find assets quickly when they need to move to another location. It also impedes the efficacy and efficiency of inspection planning.
Traditional and dated AIM processes preclude improvement areas that owner-operators might not be aware exist; for example, time-based inspection planning methods as opposed to risk-based. Time-based methods rely on a calendar alone to establish inspection frequency, without factoring into consideration the unique profile of the asset, its condition and associated inherent risk. Owner-operators could be wasting capital resources on unnecessary inspection frequencies.
Using intelligent analytics such as risk-based inspection (RBI), all asset data is assessed for the probability of failure versus the consequence of failure – generating intelligent inspection schedules that allocate resources to the most critical equipment, while reducing inspection frequency for non-critical items.
Another tendency is to be reliant on a multitude of different tools to manage asset data. It’s common to have different programs for different asset types, or different programs at different facilities. This creates unnecessary chaos in data retrieval and assessment. It’s difficult to readily access key information for any given asset in a timely fashion – impacting both daily decision-making and inhibiting generating an audit trail. Communications and operations suffer if the left hand doesn’t know what the right is doing.
That is where IIoT comes in. It connects all the physical variances into one “brain”– managing all data, equipment types and locations from a single continuously updating data source.
Harness a solution
Digitalization addresses these challenges by closing the gaps among physical assets technology. Operators then address the following:
- Organize inspections per location to eliminate unnecessary site trips
- Smart planning of asset inspections
- Allocate capital to the most critical assets, without wasting budget resources
- Predict and prevent equipment failure or unplanned shutdown
- Organize and retrieve asset data from multiple locations instantly, at any time
- Garner useful intelligence from asset data in a timely manner to maximize business decisions for optimal production capability and long-term profitability
For AIM, this comes to fruition as a single tool – typically a software as a service (SaaS) application focused on comprehensive mechanical integrity management. When it comes to a solution, however, one size does not fit all. Especially when factoring in challenges unique to oil & gas. Key features to look at include:
RBI for improved scheduling and planning. Look for configurable RBI, with the ability to create a unique risk model that fits the company’s profile. It should also offer pre-configured models to choose from. Quantitative, qualitative, semi-quantitative, or combination models should be available. Moreover, it should include the flexibility to choose one model for equipment/piping, another for tanks, yet another for pipelines, and so forth. OPEX and CAPEX resources are maximized while ensuring greater integrity and operational safety.
Integrity operating windows (IOW) continuously monitor asset conditions, providing early alert notifications if those conditions approach or breach pre-defined corrosion boundaries. This technology can be used in tandem with distributed control systems (DCS) and data historians. IOW can analyze the operational parameters to provide feedback on asset conditions in real-time. This enables operators to quickly step in when an asset is approaching risky operating conditions, allowing them to utilize predictive maintenance instead of far costlier reactive repair after the asset has already failed.
A single, robust database can manage all equipment types across all locations simultaneously – to keep track of where the assets are and quickly find them when needed.
GPS capabilities for pinpointing the exact, accurate locations of all equipment at any given time. Save time and effort that would otherwise be spent organizing and managing where installations are and tracking their movement.
Smart inspection planning capabilities to know what equipment needs to be inspected reduces returns to a remote site due to equipment being missed. Look for a software with the ability to organize inspections per location, to create an inspection plan prior to arriving to save time and money.
Mobile technology for field data management includes the ability to manage field inspection management via mobile tablet. It allows inspectors to download work to their tablet and then synchronize results immediately from the field – facilitating communication and collaboration, expediting the ability to make business decisions.
Ensure regulatory compliance by having all data pertaining to equipment, work, scheduling, and inspection results continuously allocated and updated on a single database. Look for a software that is already configured to populate data according to major regulatory requirements, such as API, ASME, ISO, etc. In the case of audit, the operator should be able to generate a customized, tailored report with the simple click of a button.
Use the checklist specified in table 1 when vetting technologies for these purposes.
In addition, look for a company that provides real implementation, training, and ongoing technical support. At a minimum, they should offer professional consultants with proven experience who will support implementation at every level. This includes coming onsite, assessing your current program, assisting in locating and filtering all legacy data, and developing a plan of action. They should help establish the implementation plan and support your company through the process. They should also provide robust training to ensure that all personnel are best equipped to utilize the software effectively. Finally, ongoing technical support should always be available to manage the profitability of the software moving forward. Pay attention also to whether the company provides regular software updates, as you’ll want to remain on the cutting edge of this technology as it continues to rapidly evolve.
Final words
IIoT changes the game for those in the upstream oil & gas sector. It eliminates the challenges inherent with so many varying physical assets by connecting them digitally. For AIM, the benefits of digitalization are exceptionally apparent, as it empowers operators with the ability to gain actionable intelligence from data. Constant awareness of the full picture at any time supports key business decisions in a proactive manner. This is made more possible with the latest advances in mobile technology.
More and more companies are embracing the technological revolution and digitalizing processes for rapidly improved profitability. The sooner companies digitalize, the more competitive they’ll remain – and the more ready for future advancements like machine learning and artificial intelligence.