Cover story: Industrial Internet of Things (IIoT) technologies, applied for monitoring valves in a refinery, used wireless acoustic transmitters to improve regulatory compliance and reduce hydrocarbon losses by $3 million annually due to timely detection and repair of faulty valves. The project paid for itself in five months, with an estimated annualized return on investment (ROI) of 271% annualized over 20 years. See four IIoT benefits.
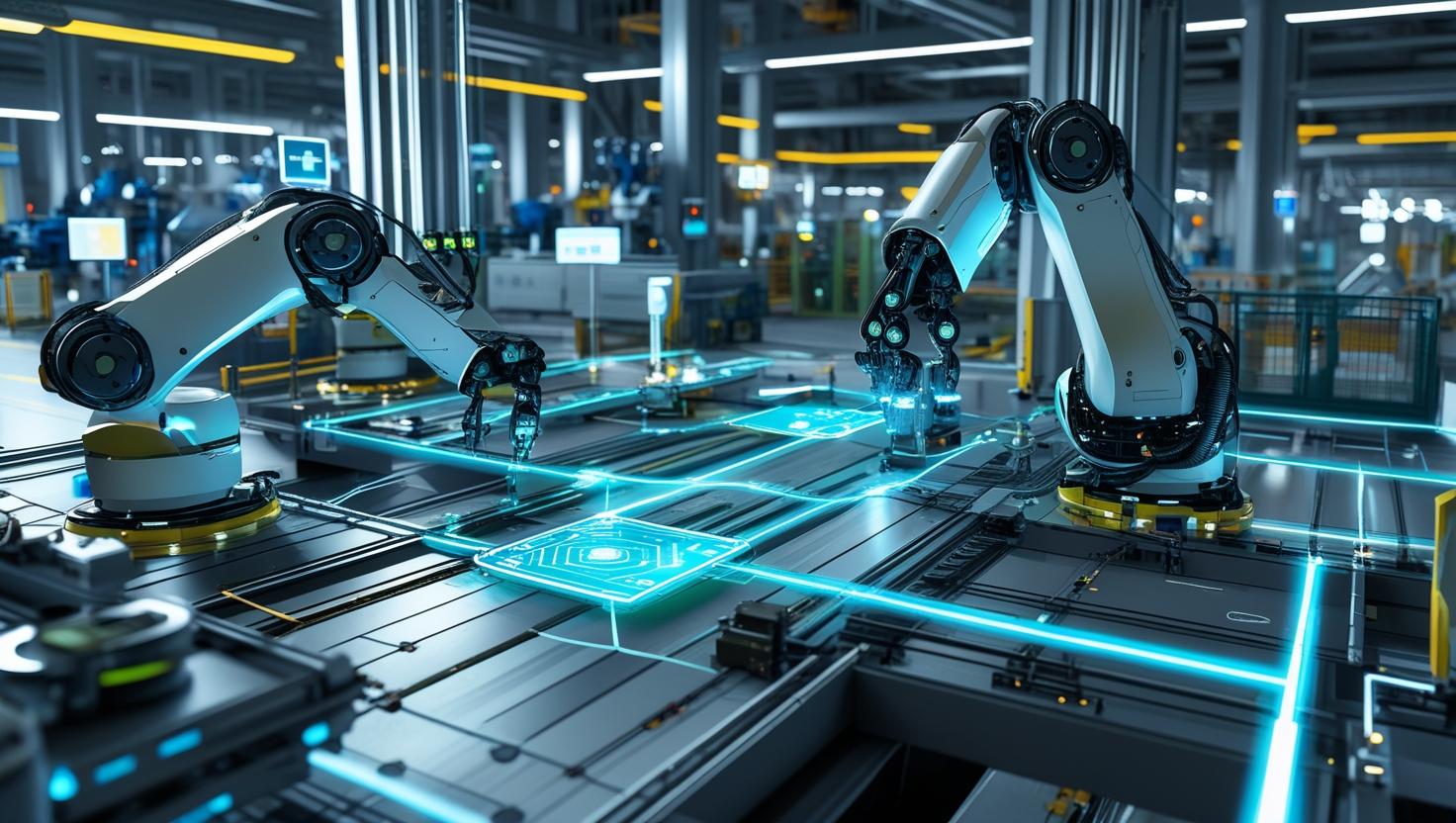
IIoT insights
- Many sensors already in place make the IIoT more advanced than the IoT.
- Interconnectedness and analysis augments value.
- IIoT examples now in place show very fast ROI, less than half a year.
The Industrial IoT (IIoT) is much more advanced than the commercial IoT, primarily due to the prevalence of connected sensors in the industrial world, which are the “things” in the IoT. Hundreds of millions of connected wired and wireless pressure, level, flow, temperature, vibration, acoustic, position, analytical and other sensors are installed and operating in the industrial sector, and millions more are added annually, increasing value with additional monitoring, analysis, and optimization.
These sensors connect to a variety of higher level software platforms, both on- and offsite. On-site connections are often via a local intranet, creating an Industrial Intranet of Things. Offsite connections are usually made through the Internet, often via a cloud-based storage system.
These higher level software platforms include control and monitoring, asset management, and specialized data-analysis systems. At remote data-analysis centers, sophisticated big data analytics are performed by dedicated experts to reveal patterns, problems, and solutions.
Four IIoT benefits
The IIoT connects sensors to analytic and other systems to automatically improve performance, safety, reliability, and energy efficiency by:
1. Collecting data from sensors (things) much more cost effectively than ever before because sensors are often battery-powered and wireless
2. Interpreting this data strategically using big data analytics and other techniques to turn the data into actionable information
3. Presenting this actionable information to the right person, either plant personnel or remote experts, and at the right time
4. Delivering performance improvements when personnel take corrective action.
Here are some of the ways the IIoT is moving from concept to reality.
IIoT in action
IIoT technology was implemented at Ergon Refining’s Vicksburg, Mississippi, facility. This IIoT implementation connects vibration, acoustic, level, position, and other sensors to an asset management system via both a wired fieldbus network (Foundation Fieldbus) and a wireless network (WirelessHART). [Foundation Fieldbus and Highway Addressable Remote Transducer Protocol (HART) protocols are governed by FieldComm Group.] The wireless network connects instruments to the plant’s control and monitoring systems via a wireless mesh network consisting of wireless instruments and access points.
Sensor data is sent to asset management software with specialized data-analysis applications for valves and smart meters. The software analyzes sensor data and transforms it into actionable information. Control room operators view this information on human machine interfaces (HMIs), and mobile workers view it on handheld industrial PCs connected to a plant-wide Wi-Fi network.
Capital expenditures were reduced because wireless cut sensor installation costs, and ongoing operational benefits included increased capacity and avoided capital investments through wireless tank monitoring. The asset management software allowed consistent setup and reduced commissioning costs, along with reduced call-outs through the use of alarm management software. Safety was improved by automating vibration monitoring in hard-to-reach locations which were previously checked via manual rounds, and energy was saved with wireless steam trap monitoring.
Ergon now has wireless infrastructure in place for data collection, analysis, and distribution. This existing infrastructure makes it quick and inexpensive to add more wireless sensors to deliver further operational improvements.
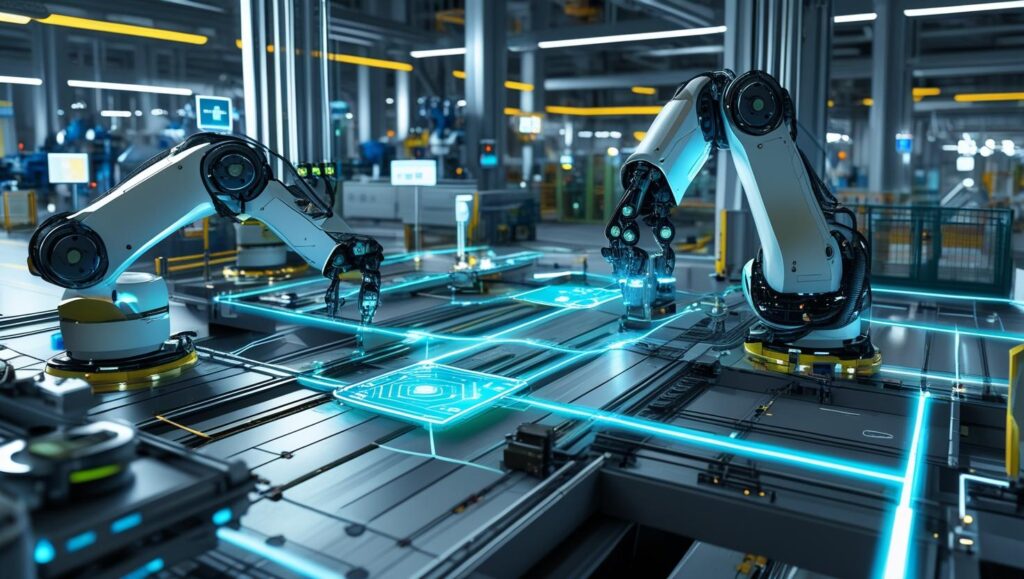
Steam trap savings
Steam trap monitoring via wireless acoustic transmitters is a leading IIoT application.
When traps fail to open, high-pressure steam leaks out, so more steam has to be produced by boilers.
Depending on the price of steam at a facility, a single failed-open steam trap can waste $30,000 worth of steam each year.
When traps fail to close, they don’t remove water droplets from the steam. These water droplets, moving through piping and equipment at a high rate of speed, can rupture steam lines and cause turbines to throw blades. Repairs are very expensive, and downtime is often significant.
Most plants monitor their steam traps manually via annual checks. This is very costly in terms of labor, misses many problems, and in the worst case can allow failed traps to operate for years.
Acoustic sensors and specialized software systems detect steam trap problems automatically and alert plant personnel so they can take action. In the past, these sensors were wired back to software systems, but the preferred modern method is to use wireless acoustic sensors connected back to software systems via a wireless mesh network, creating an IIoT.
These wireless sensors are battery-powered and can operate for up to 10 years between battery changes. Compared to wired sensors, installation takes place much more quickly at significantly lower costs, and required plant downtime for installation is greatly reduced or eliminated.
One corn milling plant was experiencing a 15% annual steam trap failure rate, with 12.5% of the plant’s steam traps responsible for 38% of the steam loss. The plant addressed this issue using wireless steam trap acoustic sensors and accompanying analytics. The payback period was just a few months, and the annual savings were $301,108.
Flare gas monitoring
Another IIoT example is monitoring valves controlling gas flows to flare stacks in refineries. Using wireless acoustic transmitters, one refinery improved regulatory compliance and reduced hydrocarbon losses by $3 million annually due to timely detection and repair of faulty valves. The project paid for itself in five months, with an estimated annualized return on investment (ROI) of 271% annualized over 20 years.
The IIoT is here today, and plants are using it to realize value from the hundreds of millions of connected sensors currently installed and the millions more coming online each year. Many of these sensors are wireless because they can be installed more quickly and at less cost than their wired equivalents, often with no required downtime. These low-cost wireless sensors and accompanying analytics can dramatically improve plant performance, increase safety, and pay for themselves within months.
– Bob Karschnia is vice president of wireless, Emerson Process Management.
Consider this
Are you taking advantage of sensors now in place, making real-time corrections to the process, and taking advantage of IIoT benefits?