Proper gearbox mounting, lubrication and regular maintenance are crucial to prevent failures and extend equipment life span, ensuring reliability and optimal performance in diverse applications.
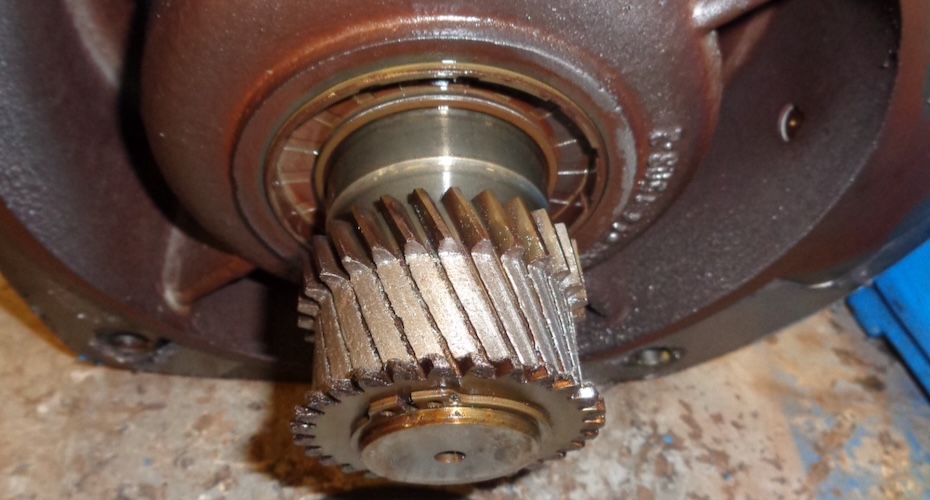
Learning Objectives
- Learn how proper gearbox mounting and lubrication practices can prevent common failures, ensuring optimal performance and extended equipment life span.
- Gain insights into the importance of routine oil analysis, the role of various oil-level monitoring methods and the benefits of using recommended accessories and protections for gearboxes.
- Understand that these critical aspects will empower them to make informed decisions for reliable and efficient gear drive operations.
Gearbox insights
- Learn how proper gearbox maintenance and lubrication can prevent failures, improve performance and extend equipment life span.
- Delve into the crucial role of routine oil analysis and maintenance accessories in ensuring gearbox reliability and efficiency.
Gearbox failure can occur from various factors such as misalignment, lubrication problems, thermal instability, oil seal issues, ventilation, breather complications, vibration and bearing issues. Some of these issues could result from improper installation or insufficient knowledge regarding optional accessories and mounting requirements, which can profoundly influence the overall reliability and life span of the equipment.
Many gearbox manufacturers provide their products with a range of mounting options and designs to be installed for different applications and orientations without requiring additional gearbox component modifications.
However, some consideration is necessary for any mounting position to avoid common failure modes associated with gearbox orientation. The mounting position of the gearbox determines the optimal oil fill level and vent location. Additionally, certain mounting positions may require special accessories in the final assembly as well.
Placing a horizontally designed gearbox in a vertical or angular position without considering proper precautions increases the likelihood of lubrication ineffectiveness, misalignment and potentially resulting in elevated vibration and temperature within the gear drive. Moreover, improper selection and installation of the gearbox can adversely impact oil levels and lubrication quality as well.
Understanding the specifications for each mounting position of the gearbox and considering manufacturer recommendations are crucial for achieving correct installation and maintaining optimal lubrication and gearbox performance.
Understanding gearbox challenges
1. Maintaining optimum lubricant levels: Maintaining and monitoring correct oil levels in gear drives is crucial for effective maintenance, particularly challenging in systems without enough instructions regarding oil capacity in each mounting position and improper oil level monitoring. The are several types of oil-level monitoring methods in a gearbox:
Sight glasses: Oil sight glasses work by giving a real-time snapshot of the oil inside machinery without having to shut anything down.
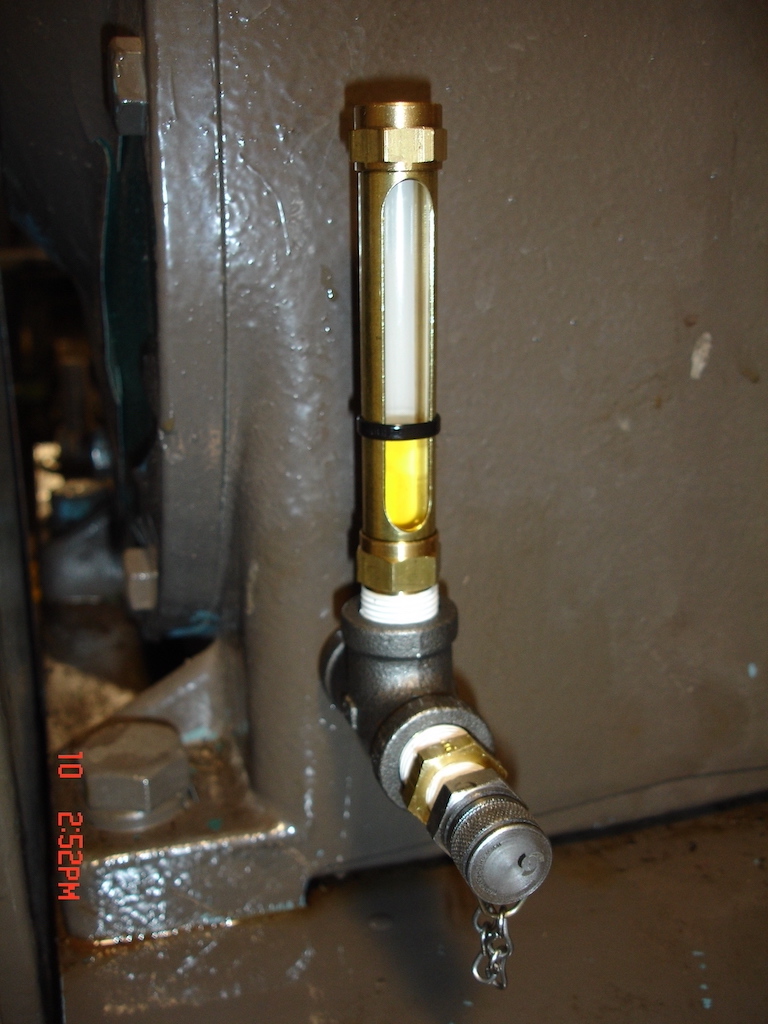
This live inside look plays a critical role in condition monitoring and early failure detection. There are some risks associated with dirty sight glass and leakage (visible and invisible), which may create some hidden failure modes.
Drawbacks include needing cleaning and replacement due to weather and sunlight or ultraviolet light, which can make level reading impossible.
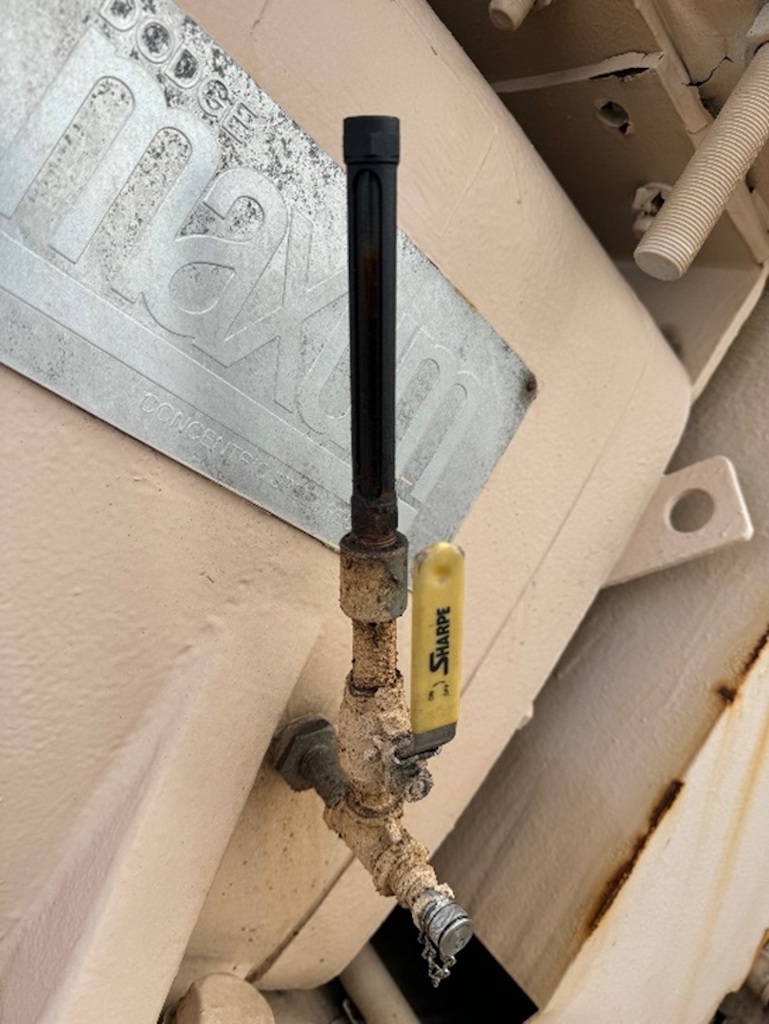
Oil level plugs: Oil level plugs (see Figure 3) enable oil level checks, but certain factors require attention. This option does not give a live inside look. Hidden oil leaks (invisible leaks) will not be detectable with oil level plugs until the plug is opened and the level is verified.
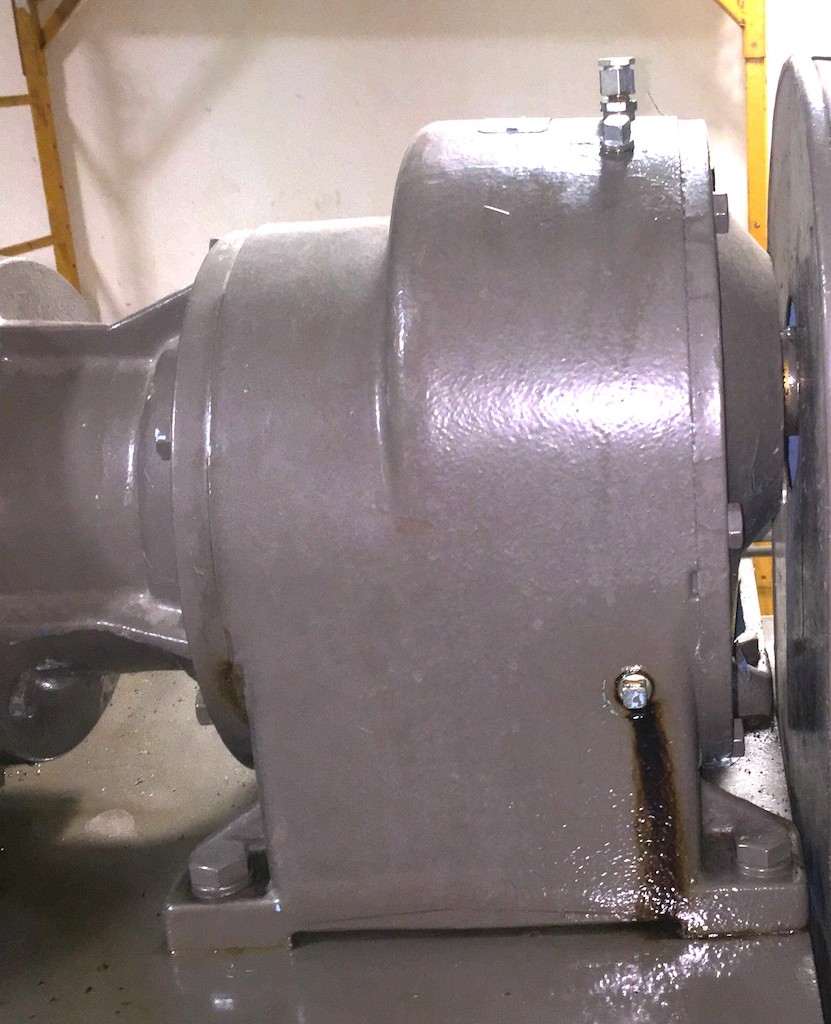
Dipsticks: These do not offer a live inside look. They are not suitable for humid environments since most of them are not airtight and humidity can penetrate inside the gear drive.
Oil level sensors: Installing oil level sensors/switches is a great option in locations with low accessibility during operation like cooling tower gear drives, or in gear drives installed in a deep or high location with low operator accessibility. There is a high cost associated with these.
Lubrication-related failure occurs when there is too little or no lubricant in the system. This can be the result of gearbox mounting. The best lubrication performance will occur when the gear drive is mounted in the most common mounting orientation which the primarily what the gearbox is designed for, a gearbox needs a set level of lubricant and other accessories. The same gearbox assembly needs to be mounted in the other orientation, which requires additional lubrication.
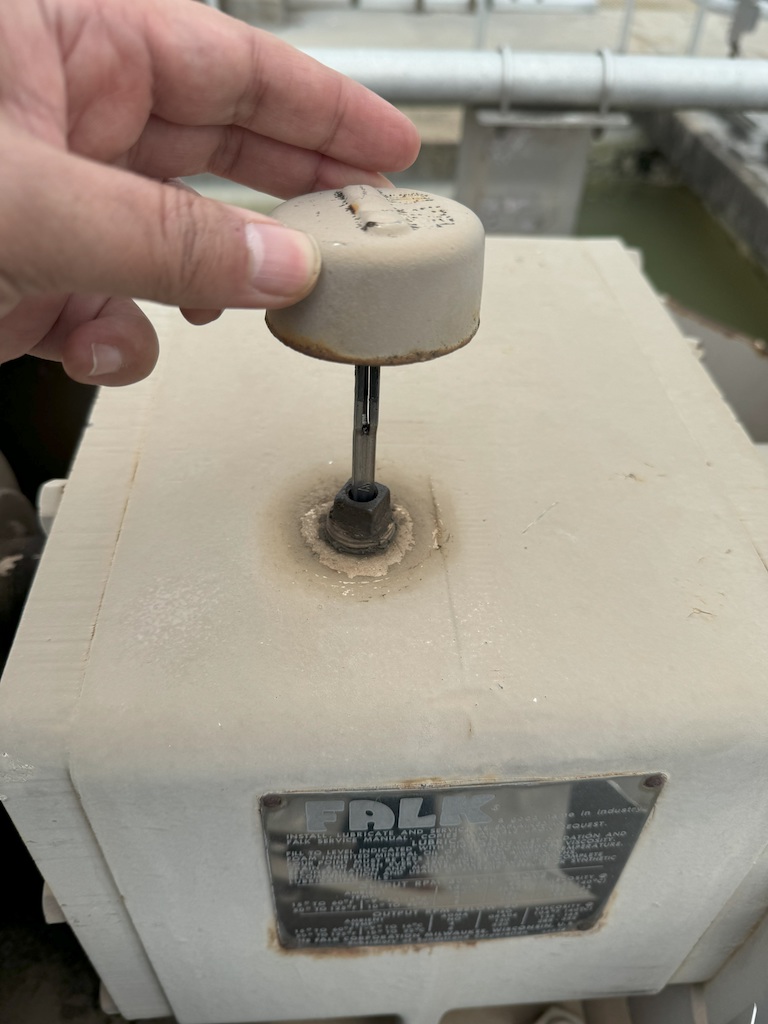
2. Increased oil churning or splashing losses and additional heating: This is for vertically mounted and horizontally designed gear reducers with the motor or input on top. They will need a higher oil level to ensure the lubrication of the first-stage gearing. These operating conditions result in increased oil churning or splashing losses and additional heating inside the gear unit. For these applications, it is critical to consider whether an accessory like oil expansion chamber is required.
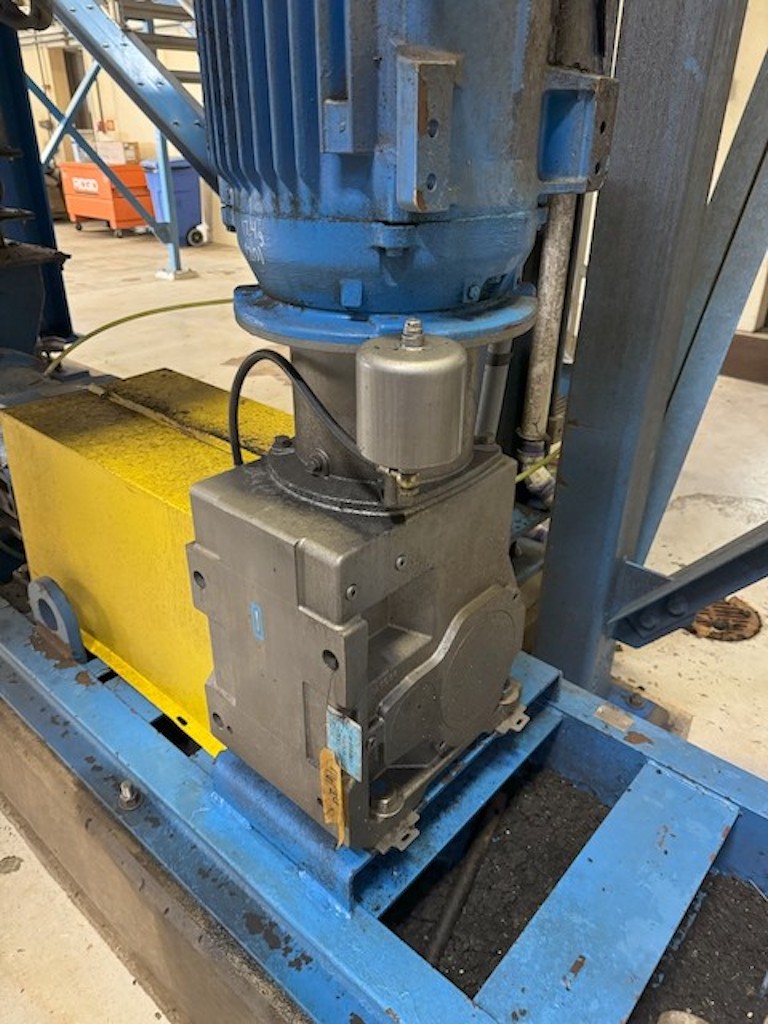
3. Ventilation: Many gear reducers come with a vent designed for the primary position to equalize air pressure variances between the gear unit’s interior and the surrounding atmosphere. Before starting the reducer, it’s crucial to ensure the vent is correctly positioned relative to the mounting orientation.
The importance of routine oil analysis in gearboxes
Regular oil condition monitoring and tracking oil performance trends for each piece of equipment are crucial for establishing optimal lubrication maintenance schedules and replacement intervals. It is recommended to change the gear oil if oil analysis reveals any of the following:
-
A viscosity shift of approximately 10% or more (applicable for ISO viscosity grade at 40°C).
-
The presence of debris particles (such as silicon, dust, dirt or sand) exceeding 25 parts per million (ppm, ISO 4406:99).
-
Iron content surpassing 150-200 ppm.
-
Water content exceeding 0.05%, or 500 ppm (ASTM D6304).
-
Acid number tests indicate significant oxidative breakdown of the oil and a consequent decline in performance, as per ASTM D664
Possessing adequate knowledge of proper mounting techniques and optional accessories will enhance the gear drive’s reliability, inspection and monitoring. Insufficient lubrication can result in critical components like gears and bearings metal-to-metal contact leading to friction and eventually breakdown of these components and ultimately, gearbox premature failure.
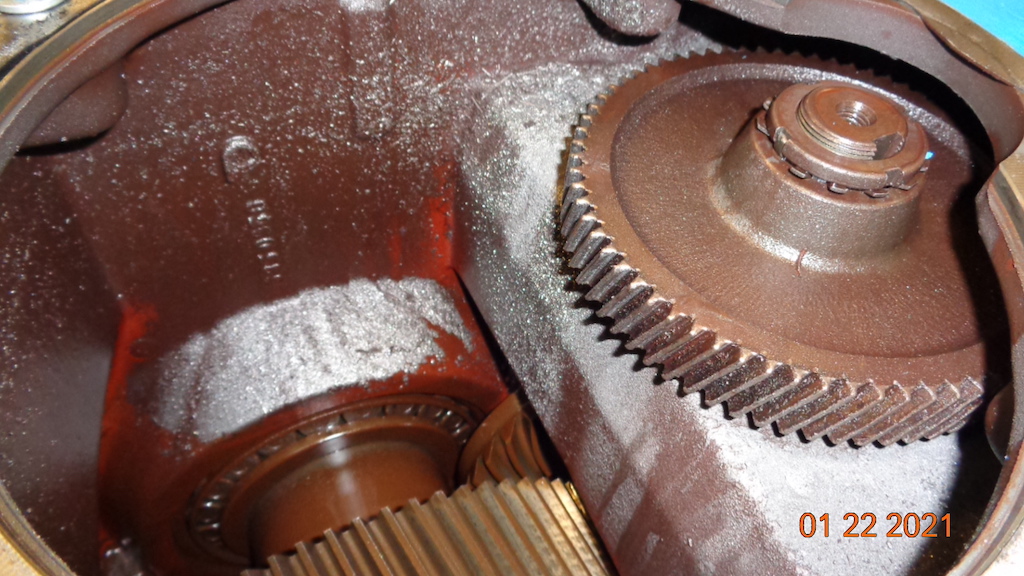
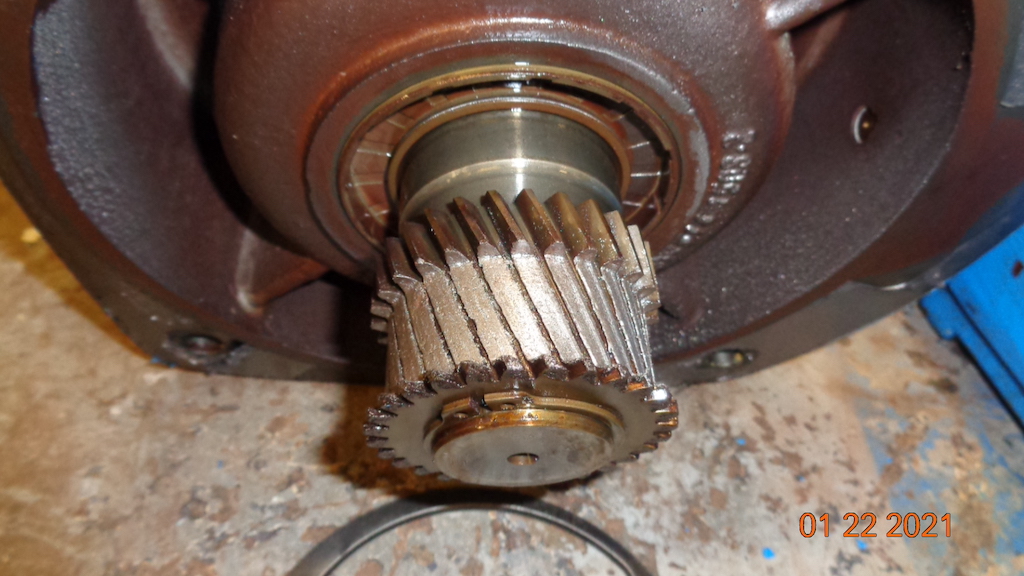
Conversely, excessive oil can lead to thermal instability and may restrict space for thermal expansion during operation, thereby exerting excessive pressure on seals and causing them to fail.
Recommended protections and accessories for gearboxes
-
Temperature switch.
-
Vibration switches.
-
Oil level indicators/switches.
-
Desiccant filters on the breather.
-
Motor overload/underload protection.
-
Oil expansion chamber.
Ramin Safikhani, MLE, CMRP, VCAT-II, is a Reliability Specialist at Upper Occoquan Service Authority. He has practiced rotating equipment condition monitoring and maintenance reliability for more than 24 years in petrochemical and wastewater treatment industries.