Safety is a major part of manufacturing and there are many facets to consider, but how companies approach it is quite different, even if there are universal truths all should abide by.
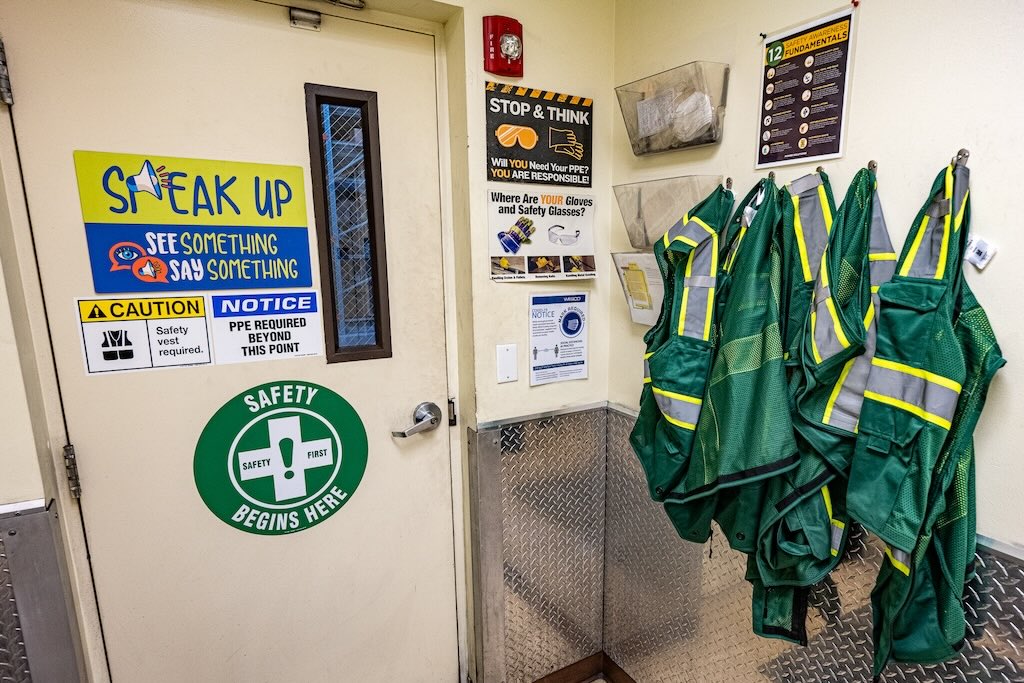
Respondents
- Shawn Gregg, vice president, global safety, Wesco, Pittsburgh
- David Kennedy, business development manager, VAC-U-MAX, Belleville, N.J.
- Dave Opheim, business development manager, flame & gas detection, MSA Safety, Cranberry Township, Penn.
- Dustin Schneider, channel sales director, Diversified Fall Protection, Westlake, Ohio.
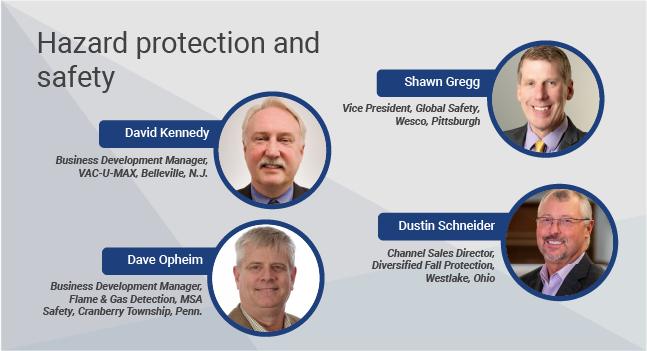
Question: What are some of the current hazard protection trends for industrial and manufacturing facilities?
Shawn Gregg: One of the main trends we’re seeing is greater utilization of the Internet of Things (IoT) – especially when it comes to connected safety solutions. The ability to facilitate communication between devices and the cloud, as well as between the devices themselves, is having a major impact on safety. For example, confined space air monitor readings can be read real-time by a safety manager hundreds of miles away, and alerted in real-time if an alarm is going off. Surveillance cameras, wearable devices and other connected safety solutions can document unsafe work movements and create a database to help with accident trends.
David Kennedy: Continuing awareness of combustible dust explosions because incidents continue to occur, automation and mechanization of lifting/bulk material handling to avoid ergonomic hazards.
Dave Opheim: Due to increased global competition there is higher pressure on industrial petrochemical producers than ever before. This is particular true for process operations that utilize flammable and/or toxic gases, liquids or solids. Three examples of evolving life safety hazards within industrial petrochemical operations include:
-
Alternative fuels including hydrogen, compressed/liquified natural gas, and synthetic fuels
-
Specialty chemicals and related production processes
-
Renewable energy sources using advanced lithium-ion battery energy storage systems.
In addition to these flammable and toxic hazards there is often increased pressure on production operations caused by supply chain bottlenecks, workforce shortages or lack of proper training. Stakeholders should consider routine re-evaluation of their facility hazards, processes, stressors and operator training requirements to maintain safe production operations in this evolving market.
Dustin Schneider: An emerging trend in fall protection is the increased use of drone technology for inspecting and maintaining elevated structures. Drones equipped with high-resolution cameras and sensors can access hard-to-reach areas without exposing workers to the risk of falls. They can perform detailed inspections of roofs, scaffolding, and other elevated workspaces, identifying potential hazards such as structural weaknesses or loose components. This technology not only enhances safety by reducing the need for workers to perform these risky tasks but also improves the efficiency and accuracy of inspections, leading to more timely and effective maintenance interventions.
Question: What future trends should engineers, plant managers and designers expect for hazard protection? Looking ahead one to two years.
Shawn Gregg: As the landscape continues to evolve, connected safety solutions will play a greater role in helping plant managers keep their workers safe. These technologies – from wearables that provide haptic feedback to cameras with integrated sensors – can identify and monitor potential hazards, and help prevent incidents before they happen. Artificial intelligence (AI) will become more prominent as well, and will be a powerful extension of the safety manager. Also, onshoring and more mega projects could create additional safety management constraints for the high-demand safety professional group. And of course, the need for safety doesn’t end once those projects are completed.
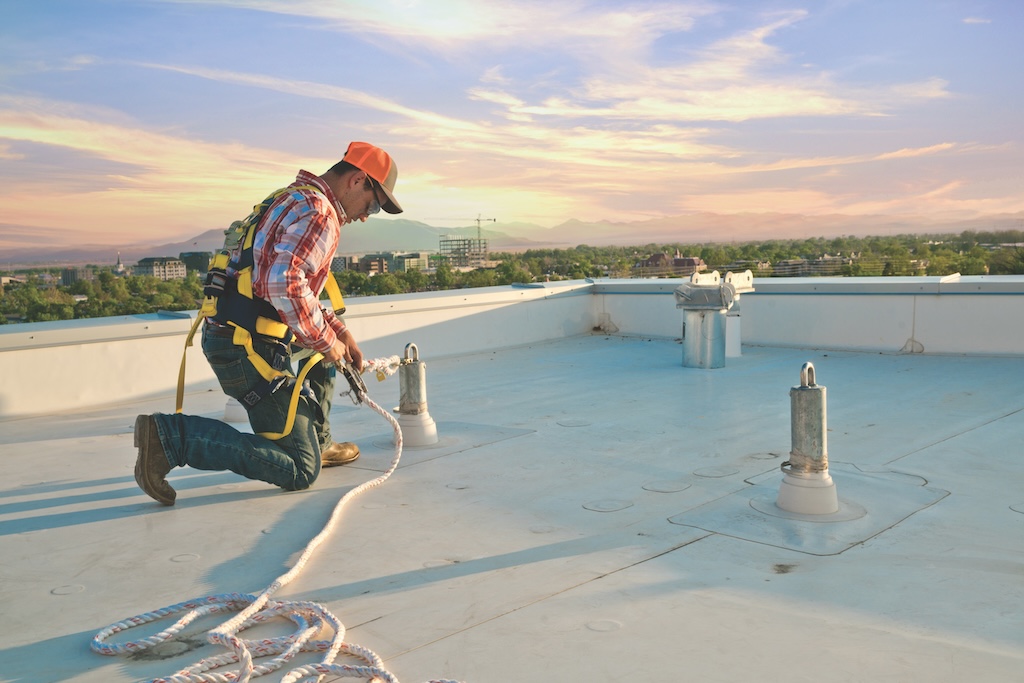
David Kennedy: Labor shortage in manufacturing continues so automation is needed to avoid overexertion and repetitive motion injuries. Combustible dust explosions still occur today, which expose the failure in awareness of material hazards, or neglect of proper SOP. Focus is needed on improving industrial hygiene and housekeeping with solutions like continuous duty and central vacuum cleaning systems, and dust-free methods of bulk powder handling such as vacuum conveying.
Dave Opheim: Future trends expected include significantly higher productivity goals usually with the same or even less overall resource availability. In addition, customers will expect a higher level of renewable and/or green energy utilization in their suppliers. This is likely to mean changes in hazardous operations depending upon the specific nature of the business. The ability of safety managers to rapidly review, validate, and revise their work procedures and safety systems to evolving fire and life safety hazards will tantamount.
Dustin Schneider: Looking ahead, the integration of the Internet of Things (IoT) devices in hazard protection is expected to grow. IoT sensors will provide real-time monitoring of environmental conditions, equipment status, and worker health, allowing for immediate responses to potential hazards. Advances in wearable technology will offer more sophisticated and personalized safety solutions, such as fall protection components that can sense a fall, smart helmets and vests with integrated communication and monitoring systems, enhancing worker safety and operational efficiency in industrial settings.
Question: Describe a project in which you had to design or modify systems to protect from a hazardous environment. What were the challenges and solutions?
Shawn Gregg: To begin with, it’s essential to clearly document and communicate that maintenance is a core part of your inspection safety management program. Its also important to note that safety professionals simply don’t have the option to manage the safety inspection process with paper and clipboards. They need to have systems in place to automate and streamline that process as much as possible. And even though NFPA 70B has been in place for nearly a year, the shift from “recommended” to “mandatory” means that safety professionals will need to take a proactive mindset when it comes to maintaining their electrical equipment.
David Kennedy: Metal powders used in additive manufacturing can be reactive requiring NFPA-prescribed explosion protection techniques such as oxidation concentration reduction. This technique requires addition of an inert gas such as argon in the vacuum conveying system to reduce the oxygen concentration below the level where combustion can occur.
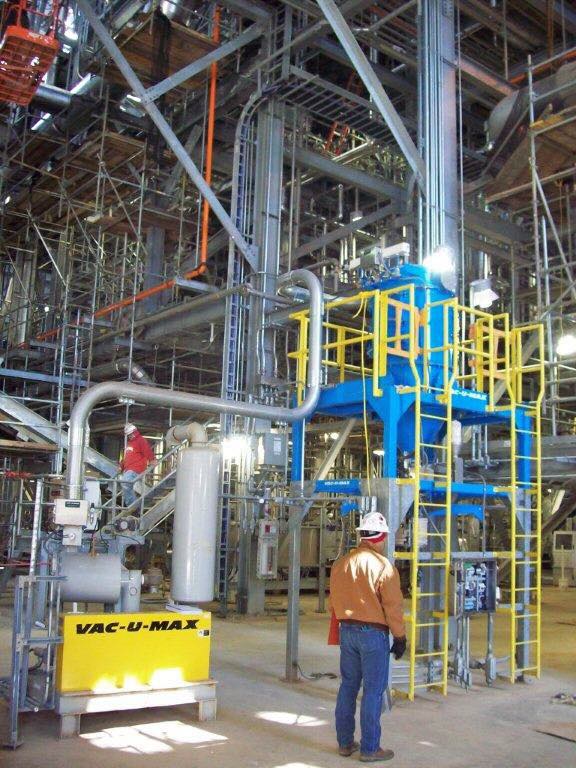
Dustin Schneider: We have several instances where we had to modify machinery or structures around machinery to integrate fall protection into equipment that wasn’t initially designed with it in mind. The challenges we encounter include adding structures capable of supporting the systems without hindering the equipment’s functionality or blocking access for repairs. The cost of all these modifications and securing capital budget are common obstacles we face. Finding solutions often requires innovative engineering and strategic budgeting to ensure both safety and operational efficiency.
Question: What types of computer applications are in use to support your hazard protection functions?
Shawn Gregg: We utilize two main technologies to enhance our safety programs: connected safety solutions and visual intelligence. Connected safety solutions have had a significant impact in our facilities. Wearables can provide haptic feedback when a worker enters a hazardous area, or send alerts when certain stressors, such as heat or exposure to hazardous fumes, reach dangerous levels. They can also help minimize ergonomic injuries caused by repetitive motion or improper lifting. Visual intelligence, which combines cameras and AI software, has helped improve fork truck safety, and can identify and monitor for potential hazards before they turn into safety incidents.
David Kennedy: Many of our computerized control systems for bulk powder handling include a ground circuit monitor. Grounding and bonding of the vacuum conveying system is critical in the safe handling of combustible powders. This monitor prevents convey system operation unless the grounding/bonding circuit is completed.
Question: Tell us about a recent hazard protection project you’ve worked on that’s innovative, large-scale or otherwise noteworthy. Please tell us about the location, plans your team engineered, key players, interesting challenges or solutions and other significant details.
Shawn Gregg: To start, make sure you implement a safety management inspection program if you’re not doing that already. Also, look for opportunities to ensure those practices are efficient. Connected safety solutions and other advanced technologies can help reduce inspection-related labor time, prevent compliance-related violations and ultimately save lives. I’d also recommend reviewing the duties your workers are performing and the portfolio of safety products and solutions you utilize to see if there are opportunities for improvement. And don’t hesitate to reach out to partners who can help guide you through the digital transformation process.
David Kennedy: Submerged recovery is a technique used to render combustible powders inert by “wetting” the powder with an inert liquid. This technique is used on portable and stationary vacuum cleaning systems and process conveying systems for powders that are designed/intended to explode under controlled conditions.
Question: What are some of the key challenges for improving electric hazard protection at your facility and what strategies/best practices have you implemented to help ensure success?
Shawn Gregg: Two of the most common hazards we see in the manufacturing and industrial areas are related to fork truck safety and environmental stressors. Blind corners can lead to injuries and other safety incidents. Without the proper monitoring or training, workers can wander into areas where those machines are operating. Depending on the industry, we also see hazards tied to heat and noise exposure, volatile compound exposure or moving machinery.
David Kennedy: A key challenge today is controlling static electricity. We use techniques to prevent operator errors such as lack of hazard awareness, distractions, neglect or incomplete circuits. We interlock the system controls with a ground monitor. We utilize static-conductive compressed air hose, static-conductive filter media and ground straps across all gaps between conductive components such as gaskets.
Question: What new or advanced technologies do you plan to implement at your facility?
Shawn Gregg: Safety training, including fall-protection training and PPE training, is critically important. But safety professionals are pressed for time, and need ways to make that training more efficient without sacrificing its effectiveness. Augmented reality (AR) and other advanced technologies provide valuable opportunities to satisfy those needs. For example, it can allow workers to train remotely, which saves time and resources by eliminating the need to travel. Additionally, augmented reality lets workers train in a non-hazardous environment.
Question: What tips would you offer to someone newly tasked with hazard protection duties?
David Kennedy: Be aware of bulk material and dust hazards from those materials used in your facility. Review SDS sheets and communicate diligent with workers about those hazards. Remove equipment that is not rated for combustible dust environments such as shop-type vacuums and eliminate compressed air blow-down practices. Facility cleanliness is not a matter of pride, it’s a matter of safety.
Dave Opheim: After you have reviewed existing workflows, standard/detailed operating procedures and hazardous operation summaries, spend some time observing and interviewing personnel directly involved with performing the hazardous work job functions. Consider performing the job function yourself for a half or full day to gain first-hand insights.
Make a point of talking with your operations personnel regularly for their input on safety protocol, and don’t forget that regular formal reviews of your hazardous operations are required. Seemingly small changes in the way workflow is performed, or changes in equipment, layout or materials used in the standard work can often have a significant impact on how a worst-case event scenario plays out.
Dustin Schneider: Start by thoroughly familiarizing yourself with industry safety standards and best practices. Regularly review and update your knowledge to stay current with new developments. Secondly, establish a proactive approach to hazard identification and mitigation. Implement regular inspections and maintenance schedules, and use technology like IoT sensors for real-time monitoring. Lastly, cultivate strong communication and training programs. Ensure all employees understand the importance of hazard protection and are trained in emergency procedures, creating a collaborative environment focused on safety.
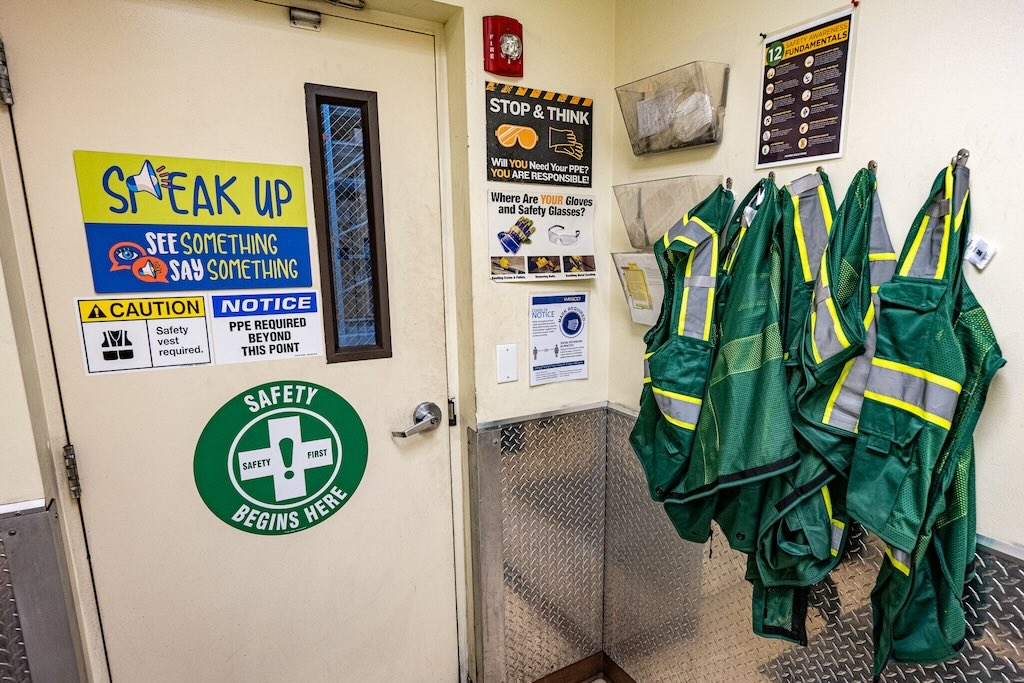
Question: Can you describe any incidents or near-miss situations related to hazardous environments that have occurred in your facility, and how you addressed them to prevent future occurrences?
Shawn Gregg: We commonly work with customers using utility knives in a warehouse and have seen a drastic reduction in cut-related injuries when going to an ANSI cut-level A4-rated glove. By setting a minimum cut rating to be used when handling utility knives, we can greatly reduce the severity of a cut if one were to occur. If we were to set the cut rating too high – say, for example, a cut level A9 – the gloves would be too bulky to work with the product and employees might tend to simply not wear them. A compromise of comfort, usability and protection is warranted.
Question: What measures do you take to ensure all employees are adequately trained and aware of the hazards they may encounter in their specific roles within the facility and how often does this occur?
Shawn Gregg: At its core, integrating smart technologies will help fill in the gaps caused by persistent labor shortages by giving safety professionals an extra set of eyes and monitoring for compliance across the plant floor. However, they also provide opportunities for enhanced safety that never existed before. They offer improved ways to detect volatile substances in the air; they can monitor noise and heat exposure and send alerts before they reach dangerous levels; they can help prevent ergonomic injuries and they can reduce fork truck incidents. As these technologies evolve, we’ll see even more exciting new use cases.
David Kennedy: Hire a Safety or EHS manager whose focus is identifying hazards and training employees and correcting deficiencies. Safety is a full-time job; not part-time.
Question: What role do engineering controls play in creating protective environments? Can you provide examples of engineering controls implemented in your facility to mitigate hazards?
Shawn Gregg: Safety audits should be considered annually, but not be communicated to the workflow when they will be scheduled. While some companies find it very useful to include line workers in the audits, you want to replicate a true daily workflow when assessing the work processes and PPE usage in a normal scenario of daily production. Also, written safety policies are commonly not viewed by employees, so having them readily available and discussion with the team is critical.
David Kennedy: In the petrochemical industry, “training” is not an acceptable safety method, because operator error can still occur. HAZOP studies should identify devices or instrumentation to eliminate operator errors.
Question: What role do you foresee for augmented reality (AR) in future PPE and fall protection training programs?
Shawn Gregg: Greater utilization of connected safety solutions can significantly enhance an organization’s PPE and fall-protection efforts – especially for lone workers. Wearables with integrated sensors can detect slips, trips and falls, and send alerts when an incident occurs. For lone workers, this type of technology can be lifesaving. Visual intelligence solutions and other types of wearables can also monitor for PPE compliance and proper utilization. All told, incorporating these solutions is an easy way to help keep workers safe.
Dustin Schneider: In the coming years, augmented reality (AR) will significantly enhance PPE and fall protection training programs. AR can simulate complex scenarios, enabling workers to experience and react to potential fall hazards in a virtual environment. This hands-on approach increases engagement and retention of safety procedures.
AR also allows for customizable training modules tailored to specific job roles and environments, providing targeted and effective learning experiences. By integrating AR into training, organizations can ensure employees are better equipped to handle real-life safety challenges, reducing the risk of accidents and improving overall workplace safety.