Machine asset analytics can help a manufacturing facility learn far more about how its operations are performing.
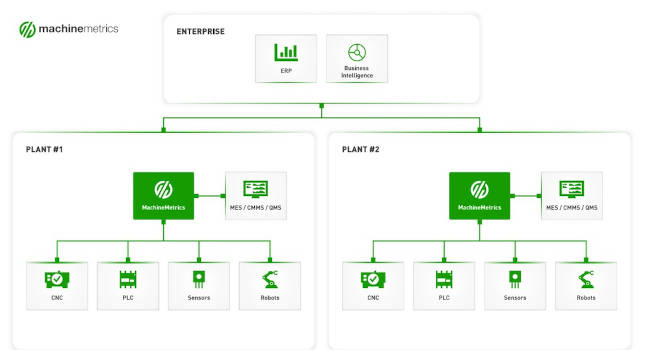
Learning Objectives
- How to manage machine assets to deliver the most value.
- The critical roles of scalability, extensibility, multi-level insights.
- The importance of extending insights to the machine, plant and enterprise levels.
Asset management insights
- Companies that invest in a good asset management program will not only be able to learn why something is happening, but they will be able to make informed decisions to improve.
- Using advanced analytics in machine assets is a good start for gaining insights, but it has to go beyond the plant floor and extend to every part of the enterprise so companies get the full picture.
Machine assets are one of the most expensive aspects of manufacturing. Managing them effectively can reduce operational blind spots and increase operational efficiency that delivers bottom-line improvements.
Effective machine monitoring solutions provide flexibility and adaptability so manufacturers can scale across legacy, modern and custom equipment, extend insights to other systems throughout the enterprise, and offers actionable and prescriptive information for multiple levels of a facility.
Scaling assets effectively
In a rapidly evolving manufacturing landscape, the challenge of scaling effectively is crucial to sustaining growth and maintaining a competitive edge. This challenge reveals the need for a system to manage a company’s assets digitally. With a scalable solution, organizations can avoid drowning in the complexity of data generated by a growing asset base.
Machine assets can range from simple to complex, each producing varying volumes of data. As a business scales horizontally, adding more assets, the volume of data increases. Vertical growth, defined by integrating more sophisticated assets into the operations, adds another layer of complexity.
Scalable asset management system benefits
Successfully navigating this growth calls for a robust, scalable asset management system. Such a system ensures seamless operation and data utilization, managing the ever-increasing volumes of information. Here, the essence of scalability is twofold: managing more assets (horizontal growth) and handling more complex data from sophisticated assets (vertical growth).
Managing number, complexity growth
By adopting a machine data platform, businesses can track performance, anticipate potential issues, and implement preventive measures to optimize production processes and equipment health.
Scalability isn’t just about handling growth in numbers but also about managing growing complexity. It’s about having the right tools to capture, analyze, and leverage the data generated by these assets to create a foundation for intelligent decision-making and strategic planning. It also can automate operational data collection, enabling context to explain the why behind key events.

Three places to develop multi-level insights
One of the primary benefits of an effective asset management system is its ability to deliver insights at multiple levels – from individual machines to entire plants and across the whole enterprise. This multi-level analysis uncovers patterns and trends at various operational levels, providing a comprehensive picture of asset performance and enabling strategic decision-making.
1. Machine level
Let’s start at the machine level. Each machine in a manufacturing facility is a rich data source capable of revealing granular insights into its performance, efficiency and potential issues. An advanced asset management system can extract this data, analyze it and present actionable insights. This granular level of understanding allows for proactive maintenance, performance optimization and improved machine life span.
2. Plant level
Scaling up, we come to the plant level. Collecting and analyzing real-time data from various machines makes trends and patterns apparent across all levels. These insights can highlight areas for improvement, promote operational efficiency and enhance overall plant performance.
3. Enterprise level
At the enterprise level, the scope expands to include multiple plants and even different geographical locations. Here, the asset management system aggregates and analyzes data from the entire organization. This comprehensive view can help identify strategic opportunities, harmonize operations and optimize resource allocation.
By fostering a deeper understanding of patterns and trends at different operational levels, asset management becomes more than a tool for monitoring machines. It becomes a strategic asset that significantly enhances everything from operational efficiency to reduced costs.
Delivering capital asset value
Modern asset management has evolved to encompass much more than basic machine monitoring. Today, it’s about delivering value for capital assets throughout their lifecycle, leveraging advanced analytics and predictive insights to drive optimized asset utilization, maintenance and overall operational efficiency.
Leveraging advanced analytics
In traditional models, machine monitoring has been paramount, providing critical real-time data on the operational status of machinery. While this function remains essential, contemporary asset management has broadened its scope to include predictive and prescriptive analysis, thus taking a more proactive approach to asset management.
Solutions are moving from basic data collection to advanced analytics and actionable insights shop floor and management can act on.
Predictive analysis uses historical and real-time data to forecast future machine performance. It can anticipate potential issues, downtime and maintenance needs, allowing timely interventions. This shifts the maintenance paradigm from reactive to proactive, helping to prevent breakdowns before they occur and extending the lifecycle of the machine assets.
The prescriptive analysis goes a step further by suggesting actions to optimize outcomes. It provides specific, actionable recommendations on mitigating potential issues, optimizing performance and maximizing asset value.
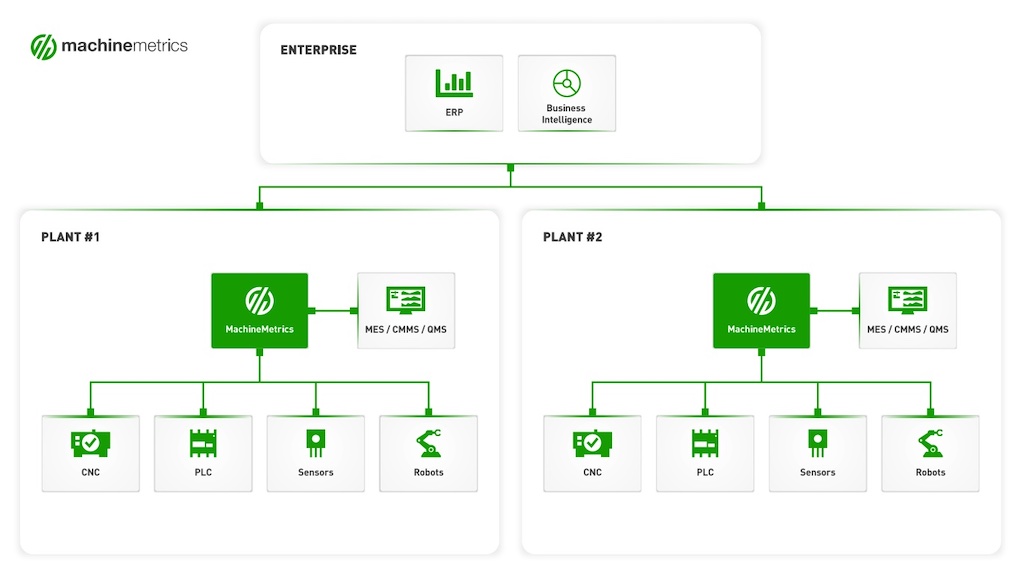
Scalability and asset management
Scalability refers to the capacity to manage an increasing number of assets and the growing complexity of data they generate. As an enterprise expands, adding more assets and integrating sophisticated machines into its operations, a scalable asset management system becomes indispensable.
Extensibility across the enterprise
To unlock data’s true value, manufacturers must consider extensibility, which is the capability of a system to integrate with other systems across the enterprise. These systems could range from simple applications like Google Sheets to more sophisticated enterprise resource planning (ERP) systems. The goal is breaking down data silos and enabling other systems to rely on accurate production data.
With an extensible system, manufacturers are no longer restricted by the confines of their asset management platforms. They can analyze data in different contexts and through various lenses. This expanded perspective gives rise to new insights and use cases.
Extensibility is also about maximizing the value of asset data by making it work in concert with the entire enterprise ecosystem. Manufacturers can uncover deep, actionable insights that propel their business forward by enabling data to flow across systems, improving overall efficiency, productivity and profitability.
Taking a proactive asset management approach
Delivering value for capital assets is about evolving from basic machine monitoring to leveraging predictive and prescriptive analysis. Data-driven machine analytics eliminates operational blind spots, enriches strategic decision-making and promotes operational efficiency, enhancing the value of machine assets.