Mobile interfaces facilitate convergence of operations and maintenance.
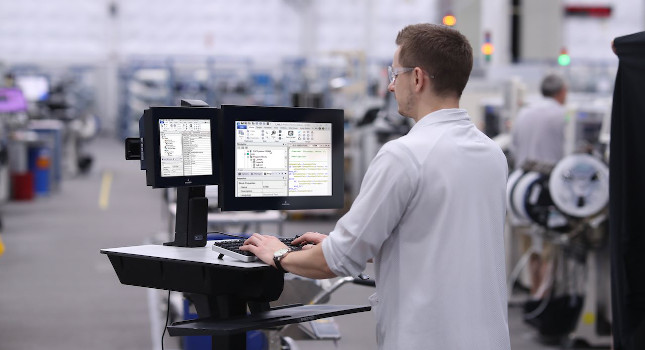
On a luxury cruise liner or large naval vessel, the bridge is where the officers and crew can command all operations. In a similar way, traditional manufacturing facilities have often relied on one or more main control rooms or consoles staffed by operators who monitor the status of all systems and issue commands as needed.
Most production plants also have maintenance personnel available who can respond to problems in the field, take appropriate actions, and report results back to control room operations personnel. Coordinating actions between these two groups often presents problems and can introduce delays, but a solution is at hand, driven by need for plant performance improvements in environments energized by digitalization improvements.
A more modern, effective and efficient approach is for operations and maintenance personnel to function in multiple roles with some overlapping responsibilities, sometimes acting as operators and other times as maintenance workers. Newer mobile human machine interface (HMI) technologies are enabling this transformation and providing innovative ways for operations and maintenance personnel to collaborate.
This shift in operating and collaboration methods is facilitated by mobile HMIs which have become convenient and functional enough to get workers the information they need when they are out where the action is on the plant floor. The changing role of HMIs made possible by handheld devices is improving the operating efficiency for these companies by enabling and empowering collaboration between operations and maintenance personnel.
HMIs anchored in place
Conventional control room operators typically work via fixed HMIs, which are usually PC-based systems (Figure 1). There are often other local HMI options in the field, ranging from pushbuttons to smaller displays, but these are typically also fixed in place, with very localized and limited functionality.
When operators detect trouble, the next step is often for them to contact maintenance mechanics and electricians who are dispatched to the field to resolve the problem. The operator remains at their station and may communicate with maintenance via radio to coordinate their actions with what remote personnel are seeing on their local screens. This is a tried and true approach but cumbersome as it introduces delays and opportunities for errors. Plants are thus searching for a better tactic, one where these two areas converge.
The other convergence
Within the field of industrial automation, there has been significant discussion and coverage of the ways that business information technologies (IT) are converging with plant floor operational technologies (OT).
The IT/OT convergence is enabled as IT-based hardware, software, networking, and protocols become integrated and more compatible with OT-hardware such as PLCs and HMIs, which have historically been much more specialized and dedicated products. This convergence is a story not just of merging technology, but also of the personnel in each of those areas gaining greater visibility, along with improved coordination. The result is more efficient operations and other improvements.
But there is another lesser known convergence occurring at manufacturing plants, and it is located out in the OT production area. This convergence involves the roles of operators and maintenance personnel, and it is made possible by the aforementioned IT/OT convergence.
One result of the IT/OT convergence has been the proliferation of highly capable mobile HMI options (Figure 2). End users are already thoroughly experienced with the use of mobile devices in their everyday lives, and many prefer the same experience in industrial settings, as long as the device durability and performance are acceptable.
Some facilities may use mobile phones for certain HMI functions, even enabling employees to bring their own devices (BYOD). Others provide site-specific commercial or industrially hardened tablets. The devices can be configured so operators can initiate control, although oftentimes BYOD devices are used for read-only access.
Regardless of the device format, mobile HMIs release operators from the control room and provide extended information for maintenance personnel at field locations. In some cases, a single person working in a converged operations/maintenance role can quickly identify a problem, physically go to it, troubleshoot it, and resolve it.
Rising tide of capabilities
Perhaps some form of fixed HMI will always be needed, but many types of operations can benefit from adding mobile HMIs into the mix (Figure 3). Mobile HMIs provide crucial operational information to operators on the production line. When issues occur, mobile HMIs are changing the two-step operator and maintenance interaction process into a more collaborative and streamlined effort.
Operators can carry HMIs right out to the production line, identify problems faster, and in some cases resolve the issue immediately, for example by adjusting a setpoint and observing its effect. If maintenance personnel are needed, they can be called to the spot, often by receiving a message via a mobile HMI. When they arrive, they can collaborate with the operators to troubleshoot the problem. Using fixed and mobile HMIs, maintenance personnel can take on some of the roles formerly restricted to operators, such as reacting to alarms, often by working in concert with operators.
Mobile HMIs are also improved by other underlying technologies resulting from the IT/OT convergence. One prominent example is that the latest OT controllers include not only traditional programmable logic controller (PLC) control, but also seamlessly merge PC-like computing abilities. This enables system designers to include advanced processing out at the PLC, such as real-time analytics, without disrupting the basic automation functions. The latest PLCs can even serve up graphics directly to mobile devices. This type of enhanced information helps operations and/or maintenance personnel run the plant at peak efficiency.
Operators walk the line
Food and beverage production facilities, like many types of manufacturing sites, operate a distributed mix of equipment, so these plants naturally fit well with mobile HMI use. These locations typically include areas such as:
- Raw material receiving and bulk storage
- Processing and blending systems
- Bottle conveyors
- Fillers
- Carton machines
- Robotic palletizers.
Each of these unique areas uses equipment and systems that are largely standalone, other than upstream/downstream handshakes. The automation products and programming for each system is likely to have been provided by different vendors, each a specialist in their area.
Even so, the many disparate systems may report back to an overall HMI application in a central control room for monitoring, alarming, setpoint/recipe settings, and control commands. When there are problems, such as backups on bottle conveyors, or insufficient cartons arriving at the robotic palletizers, it can be difficult to determine the root cause from the control room. It is often helpful for an operator or maintenance person to “walk the line” so he or she can inspect the condition directly and discover what is wrong.
The best of both worlds is possible when operators and maintenance personnel are each outfitted with mobile HMIs they can take to the field, enabling them to correlate the HMI-supplied information with actual conditions they can see firsthand. Operators can determine if production stoppages are due to a simple blockage of bottles they can correct, or if the problem appears to require maintenance attention. Maintenance personnel can use the information delivered by their mobile HMIs to work more efficiently.
In either case, personnel become more effective because the time between recognizing and resolving problems is minimized when mobile HMIs are combined with a firsthand perspective in the field.
Changing how work is done
Mobile HMIs are changing the way industrial users work, in many ways and for various reasons. There is a generational shift because many younger workers are comfortable and even prefer working with mobile devices. These workers feel empowered when they know more information, and mobile HMIs can be the best way to bring real-time knowledge into their hands, even out on the factory floor. The technology helps close the experience and skills gap between the control room and the field. Future mobile developments such as augmented reality will improve the collaboration further as field workers can act as remote experts and share their view with others.
The industrial IT/OT convergence has arrived at just the right time to effectively combine established industrial methodologies with the latest IT technologies, resulting in full-featured mobile HMIs able to break out of the traditional control room. This has led to a secondary convergence of operations and maintenance personnel at operating plants resulting in the best use of all available expertise. These workers now have the tools at hand to provide additional information, enabling them to be more efficient and improving operations productivity.
This article appears in the IIoT for Engineers supplement for Control Engineering and Plant Engineering.