The COVID-19 pandemic is exposing the vulnerability of our food supply chain to disruptions. While there are no major shortages (yet), supply chains are still facing challenges.
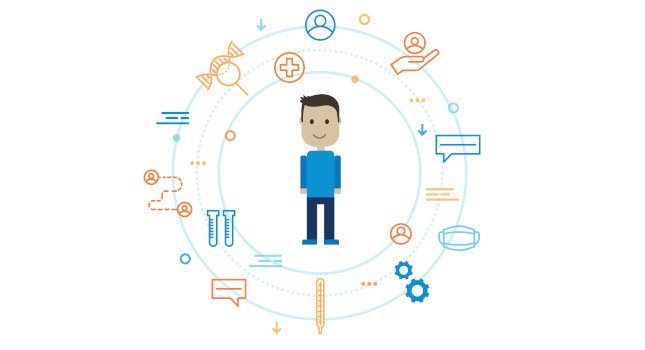
Our supply chains are facing unprecedented conditions. Most notably, the initial wave of panic-buying at the outset of this pandemic led to a sudden spike in demand for several food and household items. Though manufacturers for essential items typically carry several days’ worth of stock at their distribution centers and many facilities are operating continuously to meet these demands, immediately replenishing the empty grocery store shelves nationwide is a very difficult task.
Furthermore, once the current situation returns to “normal,” what do we do with this excess capacity? Demand uncertainty due to the longevity of the current situation can result in excess inventory accumulating within supply chains, known as the bullwhip effect. These are just a few potential supply chain disruptions we may face due to COVID-19. Fortunately, there are proactive measures manufacturers can take.
Four ways to reduce gaps between demand and supply in the food supply chain
Implementing these operational strategies can help manufacturers reduce demand vs. supply gaps or the impact of bullwhip effect in their supply chains.
1. Implement product rationalization
Product rationalization is an evaluation process to determine if you should make changes to your products. It can help manufacturers reduce their number of products/SKUs, thereby freeing-up production capacities. Be aware that ineffective rationalization can lead to increased overhead costs, lost sales, or customer migration. Successful rationalization requires top management directive and buy-in coupled with a thorough process. First, use mathematical and clustering techniques to identify and create product families. Then perform modeling and simulations to quantify the improvement in throughput for a defined set of product families. This will help you determine which products should be eliminated unless they can be justified through the business case.
2. Reduce product, process and packaging complexity
Product variety can help increase a company’s competitive advantage, but it also adds to the overall complexity. Complexity impacts several areas including planning and scheduling, purchasing, equipment/tooling required, inventory management, changeover/cleaning philosophies and quality. Reducing this complexity generally results in cost avoidance and better control of operations. It can also improve the effectiveness of your product rationalization program.
3. Balance manual vs. automated operations
While automation helps improve repeatability and quality while reducing costs, humans still remain the most adaptable, and in some cases, economical means to overcome unplanned events. The right balance between automation and manual activities can provide production flexibility, especially when food supply chain disruptions occur. Investigate unit operations on the line to identify which operations are the best candidates for automation. However, avoid overly customizing automation or it may become a bottleneck when demands increase or when serving different workflows. If tasks do not pose ergonomic challenges or other safety issues, personnel can intervene to support/increase bottleneck operations.
4. Manage safety stock
Increasing raw material safety stock seems like a straight-forward solution to mitigate risk; however, it can become expensive and ineffective, especially when food supply chain disruptions are longer than anticipated. To find the right safety stock balance, you need an adaptive inventory strategy supported by simulations. An adaptive inventory strategy pairs your risk profile, based on occurrence and severity, with ongoing detection of potential threats to supply continuity. This informs the realignment or adjustment of your existing inventory strategy. Also, be aware that in the case of perishable goods inventory, additional variables come into play, making the detection and severity ranking even more complex.
Regardless, it can be very important to increase your finished goods inventory (assuming you have the capacity to make more). This strategy, though counterintuitive, can prove very useful if the plant must be closed in the event that any employees are infected. A special case of Monte Carlo simulations, i.e., discrete event simulations (DES) can be used to asses and adjust variables influencing safety stocks. DES has the capability to model uncertainty and variabilities inherent in process times and perform ‘what-if’ analysis.
Is your equipment healthy?
Focusing on production is important during the current pandemic, but continuously running production lines raises another question: what about equipment maintenance? Without proper maintenance, unplanned equipment downtime or stoppages are likely to increase, impacting throughput and resulting in missed shipments. This can hurt your company’s bottom line. But the consequences would be even more severe if it impacts customers and end-users at a critical time in recovery. The resulting dissatisfaction can further negatively influence your brand value.
It is important to understand and implement the right maintenance philosophy that works for your facility in this situation.
At a high-level, a maintenance philosophy might include the following:
- Corrective maintenance (maintenance that happens in reaction to a fault)
- Frequency-based maintenance (general maintenance performed on a frequent basis)
- Risk-based maintenance (preventive maintenance performed to assets that are most likely to fail)
- Condition-based maintenance (monitoring conditions for failure to determine when to perform maintenance in advance).
Given the focus on making and getting product out the door, several manufacturers are implementing corrective or frequency-based maintenance policies. However, consider moving towards a risk or condition-based maintenance strategy, or a true predictive maintenance strategy, when the current pandemic abates. Implement data mining and machine learning techniques to predict with a higher accuracy when the next ‘perfect storm’ will occur. Avoiding any downtimes, planned or unplanned, is critical right now.
Protecting human capital in the food supply chain
One of the bigger problems that our supply chains are facing is a shortage of human capital. Food, beverage and consumer goods supply chains rely heavily on human involvement. Telecommuting is not an option. Production operators, delivery truck drivers, agricultural workers, meat processing employees, etc., all are needed to run operations, but because their presence is required, they have an increased chance of exposure to the COVID-19 virus. Additionally, an increase in operator absenteeism due to actual infections, childcare issues associated with daycare and school closures, or even fear of contracting the disease, has a severe impact on production and transportation capabilities.
Food processors must carefully consider the safety of their employees. Besides reducing the number of employees present onsite at a given time, manufacturing companies should also strictly enforce precautionary measures and guidelines as outlined by CDC:
- Implement employee distancing or erect dividers between workers inside plants
- Take employees’ temperatures when they enter the facility
- Make face masks and social distancing during breaks mandatory.
Though the general cleanliness and personal protective equipment (PPE) requirements in food and consumer goods manufacturing facilities may not be as stringent as biotechnology or pharmaceutical manufacturing, it is worth considering higher cleanliness and safety standards during a pandemic. Finally, it may seem contradictory but slowing down production lines can also be an option to better protect personnel. Employee safety should be our utmost priority.
Responding to food supply chain disruptions is most effective when done proactively.
While all plans will face some level of inaccuracy or fall-outs, manufacturing companies should constantly strive to find the best strategy that works for them. There is no ‘one size fits all’ solution to disruption management. In order to find which strategy works best, look at your existing business processes, as well as operational and compliance requirements.
This article originally appeared on CRB’s website. CRB is a CFE Media content partner.