As manufacturers face rising global demands for efficiency and environmental responsibility, they encounter a dual challenge: how to boost output while minimizing energy consumption.
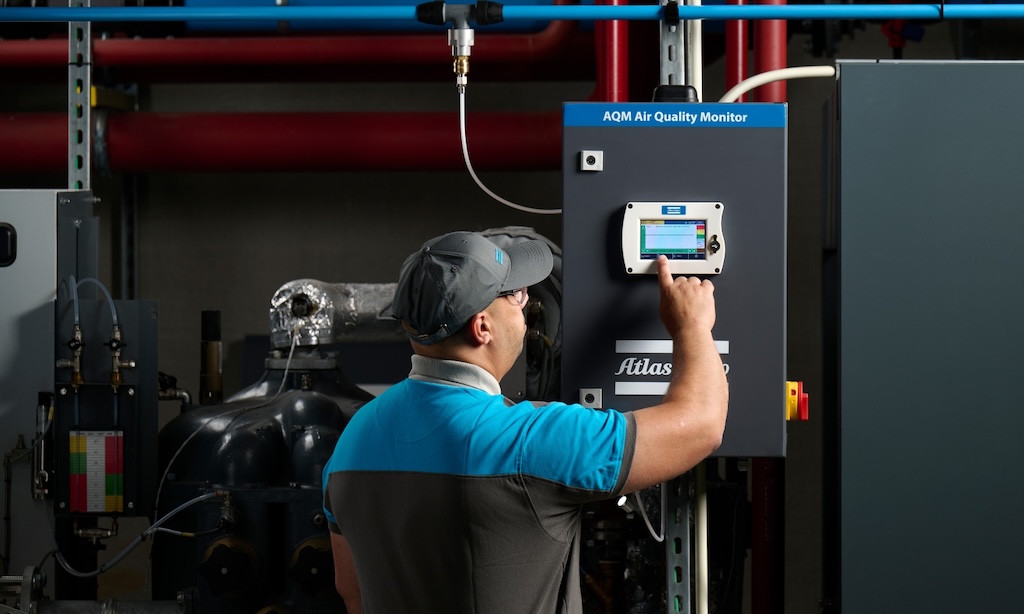
Learning Objectives
- Understand the role of energy efficiency in manufacturing. Identify key areas of energy consumption in manufacturing facilities, with a focus on air compression systems and recognize the environmental and financial impacts of reducing energy use.
- Explore advanced technologies for sustainable manufacturing. Analyze how automation, data analytics and IoT-enabled smart factories contribute to energy efficiency and sustainable productivity within manufacturing settings.
- Examine regulatory and financial incentives for energy efficiency. Discuss government regulations, incentives and common barriers to implementing energy-efficient practices and understand how these influence sustainable practices in the manufacturing industry.
Energy insights
- Meeting energy goals requires integrating advanced technologies and sustainable practices that not only streamline operations but also contribute to long-term savings and compliance with climate-focused regulations.
- Learn strategies to balance high-output manufacturing with low energy consumption for overall sustainable productivity.
 In manufacturing, companies are under increasing pressure to enhance efficiency and productivity while simultaneously minimizing energy consumption. This dual challenge is driven by the need to stay competitive in a global market and comply with stringent environmental regulations. As the world grapples with climate change, energy conservation has become a critical component of both environmental and economic sustainability.
Global energy and climate initiatives, such as the Paris Agreement, are pushing industries to reduce their carbon footprints and adopt more sustainable practices. For manufacturers, this means finding ways to maximize output while reducing energy usage. This is not only important for compliance but also for gaining a competitive advantage in an increasingly eco-conscious market.
One of the most significant energy challenges in manufacturing is managing energy-intensive processes like air compression, which powers pneumatic tools, conveyors and assembly equipment. These systems often account for a substantial portion of a facility’s energy expenses, particularly if they are not optimized for efficiency.
To address these challenges, manufacturers are turning to advanced technologies, process innovations and renewable energy sources. By embracing these strategies, they can achieve sustainable productivity that benefits both their business and the environment.
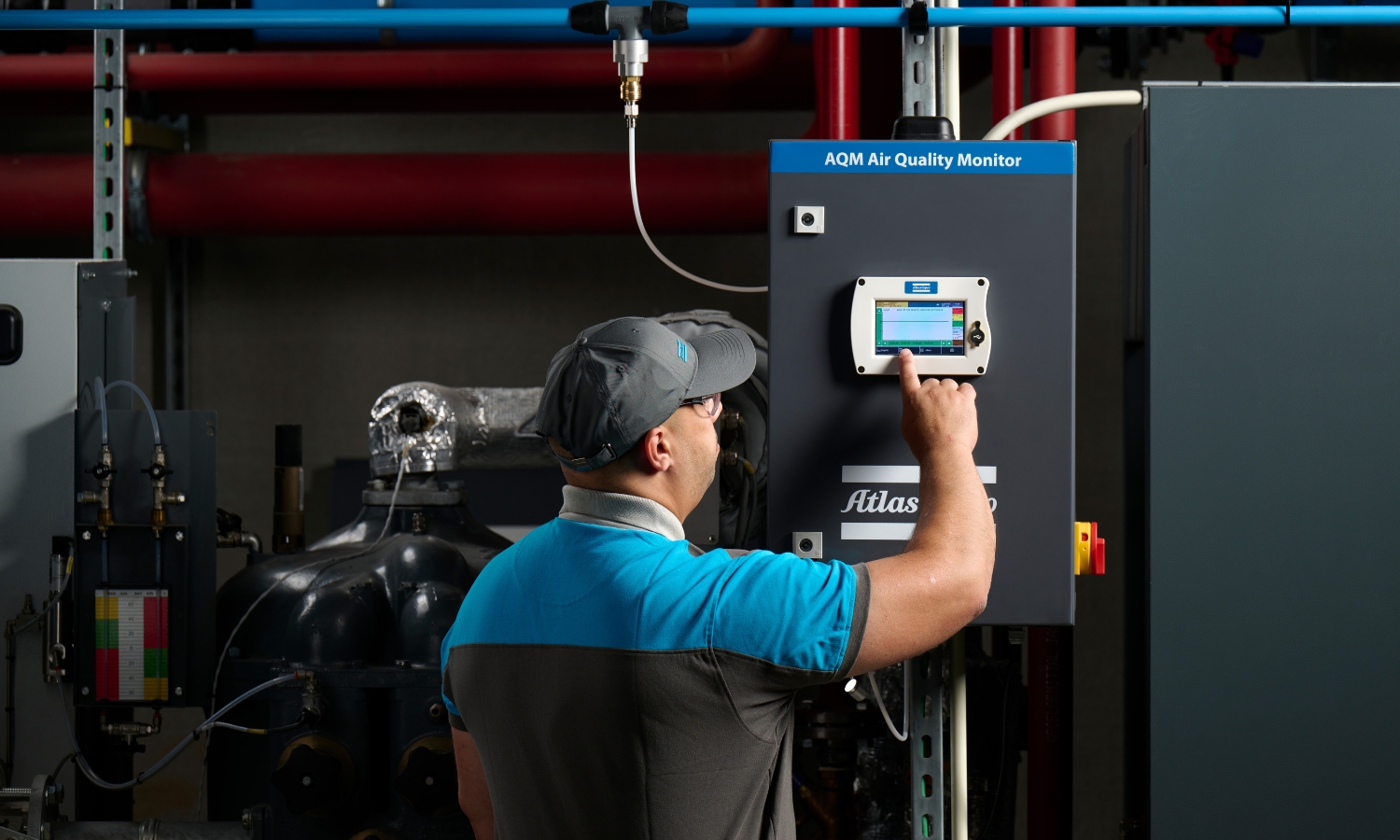
Understanding energy consumption in manufacturing
To effectively minimize energy usage, it’s essential to first understand where energy is being consumed across the manufacturing industry. In manufacturing facilities, energy is typically directed toward several key areas, including machine operations, lighting, climate control and compressed air systems. Among these, air compression alone can represent 10% to 30% of a facility’s energy costs, depending on the sector and scale of production.
According to the U.S. Energy Information Administration (EIA), the manufacturing sector consumed approximately 19,436 trillion British thermal units (Btu) of energy in 2018. This consumption is distributed across various subsectors, with chemicals, petroleum and coal products, paper and primary metals being the top energy consumers On average, manufacturing facilities use 95.1 kilowatt-hours of electricity and 536,500 Btu of natural gas per square foot each year.
High energy consumption in manufacturing not only leads to increased operational costs but also has significant environmental impacts. The manufacturing industry accounts for about 20% of global greenhouse gas emissions. Reducing energy consumption is critical for both financial savings and environmental sustainability. By implementing energy-efficient practices and technologies, manufacturers can lower their energy bills and reduce their carbon footprint, contributing to global efforts to combat climate change.
By identifying these high-energy areas and deploying targeted solutions, manufacturers can establish more efficient workflows and reduce unnecessary power consumption.
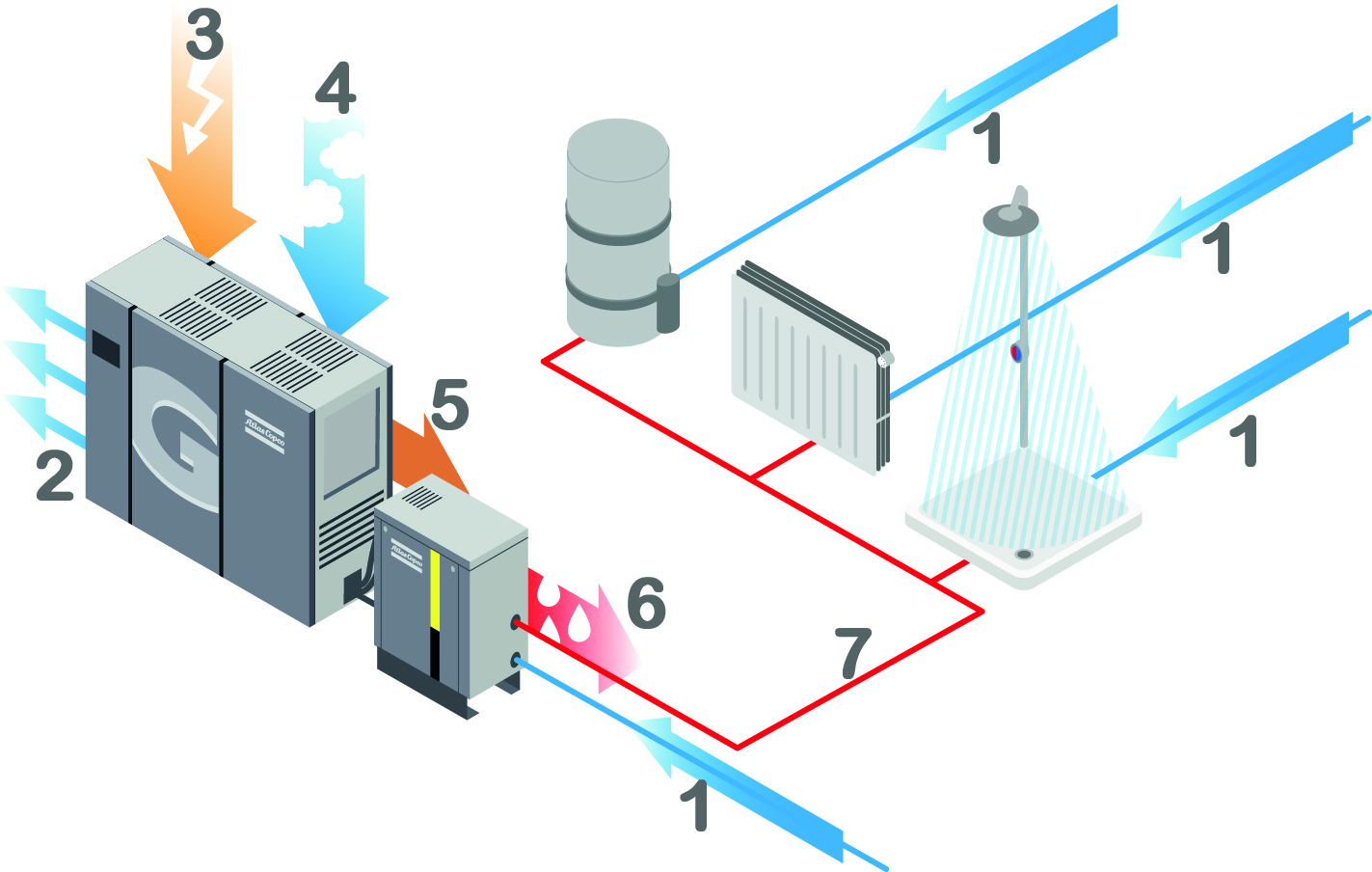
Advanced manufacturing technologies: pathways to efficiency
Technological advancements have enabled manufacturers to boost productivity while reducing energy demands. By combining automation, data analytics and smart systems, facilities are now able to achieve precise control over energy consumption, tailoring use to real-time production needs. Key technologies in this domain include:
Automation and robotics
Modern automated systems and robotics have transformed assembly lines, offering faster production with greater accuracy. These systems can operate only when needed, conserving energy during idle periods.
For example, integrating compressors with automation allows them to function only when tools are active, reducing unnecessary energy use. Automation also helps reduce human error, streamlining production and conserving power by minimizing unnecessary processes.
Data analytics and machine learning
Data-driven insights are invaluable in detecting inefficiencies, predicting equipment failures and optimizing schedules. In compressed air systems, for example, data analytics can highlight periods of peak usage, detect minor leaks and identify points where system pressure may be unnecessarily high. These insights allow facilities to adjust, lower pressure or schedule maintenance before energy losses accumulate, leading to cost savings and improved compressor longevity.
Additive manufacturing
In sectors that have adopted 3D printing and other additive manufacturing technologies, there is a noticeable reduction in both energy and material waste. By creating parts layer by layer, these methods eliminate the need for complex tooling and excess material, which traditionally require significant energy for processing and handling. Additionally, additive manufacturing often reduces reliance on air-powered equipment, contributing to lower overall energy consumption.
IoT and smart factories
Internet of things (IoT)-enabled factories use connected devices, sensors and smart equipment to monitor energy use in real-time. Air compressors equipped with IoT sensors can monitor their own performance, adapting pressure levels based on demand fluctuations. This dynamic control results in significant energy savings, especially during periods of low activity. Moreover, IoT data can be aggregated and analyzed to fine-tune equipment settings and identify further optimization opportunities across the facility.
By leveraging these advanced manufacturing technologies, companies can significantly enhance their energy efficiency while maintaining high levels of productivity. These innovations not only help in reducing operational costs but also contribute to a more sustainable manufacturing process.
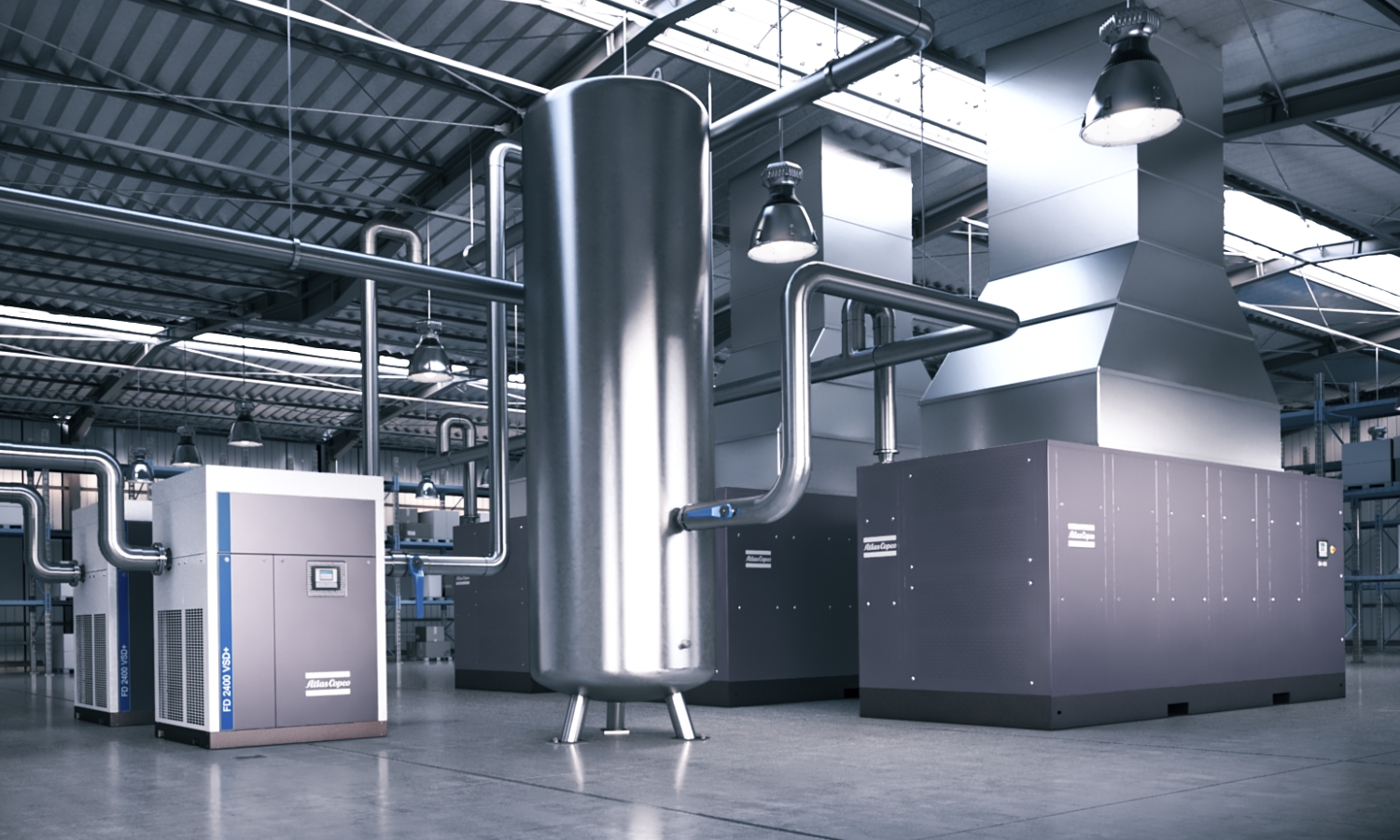
Efficient production processes
A well-designed workflow is essential for achieving sustainable productivity. By examining and rethinking how processes are structured, manufacturers can find multiple points of improvement that reduce energy use while maintaining output levels.
Lean manufacturing focuses on waste reduction, aiming to cut out unnecessary steps and resources, including energy. In lean environments, equipment such as air compressors are programmed to operate only when required, reducing energy usage during inactive periods. By setting parameters around operational needs, lean manufacturing eliminates unnecessary energy consumption.
Air compressors and other heavy equipment generate substantial heat, most of which goes to waste. By capturing and redirecting this heat, facilities can warm office spaces, pre-heat water or use it for other on-site applications. Heat recovery is particularly beneficial in colder climates, where offsetting traditional heating costs can make a notable difference in energy costs. Manufacturers can install heat exchangers to funnel compressor-generated heat into facility-wide heating systems, creating an efficient loop that repurposes waste energy
Continuous production processes generally consume less energy than batch processes, as they reduce the need for frequent start-ups and shutdowns. For air compressors, this approach means maintaining a steady, lower-pressure output rather than continually ramping up and down.
By implementing these efficient processes and redesigning workflows, manufacturers can significantly reduce energy consumption while maintaining high levels of productivity. These strategies not only help in lowering operational costs but also contribute to a more sustainable manufacturing process.
Renewable and alternative energy sources
Renewable energy adoption is a powerful strategy in the quest to reduce energy costs and environmental impact. By harnessing solar, wind or geothermal power, manufacturers can power their facilities and processes sustainably.
Solar and wind energy
Facilities equipped with solar panels or wind turbines can offset energy used for lighting, climate control and even air compressors. In this setup, smart control systems can prioritize renewable energy sources, switching to grid power only when renewable generation is insufficient. For example, a study by the National Renewable Energy Laboratory highlights how advanced manufacturing technologies can integrate renewable energy to power processes, thereby reducing reliance on traditional power sources.
Biomass and geothermal energy
Biomass and geothermal energy are also viable options for manufacturing facilities. Biomass can be particularly useful for energy-intensive industries that require high-temperature heat, such as the chemical and metal sectors. Geothermal energy, while less common, provides a stable and continuous energy source that can be used for both heating and electricity generation.
Benefits of renewable energy integration
Integrating renewable energy sources into manufacturing processes offers several benefits:
- Cost savings: Reducing reliance on traditional energy sources can lead to significant cost savings over time.
- Environmental impact: Lowering greenhouse gas emissions contributes to global efforts to combat climate change.
- Energy security: Diversifying energy sources enhances energy security and reduces vulnerability to energy price fluctuations.
Smart equipment and high-efficiency machinery
The development of smart equipment and high-efficiency machinery marks a significant shift in the manufacturing industry, enabling companies to reduce energy consumption while maintaining or even increasing productivity. These innovations are driven by advancements in technology, including the industrial IoT (IIoT), artificial intelligence (AI) and robotics.
Industrial internet of things
The IIoT involves a network of interconnected machinery, tools and sensors that communicate with each other and the cloud to collect and share data. This connectivity allows for real-time monitoring and management of equipment, leading to improved efficiency and reduced energy consumption. For example, IIoT-enabled air compressors can adjust their operation based on real-time demand, minimizing energy waste during periods of low activity.
AI and machine learning
AI and machine learning algorithms analyze data collected from IIoT devices to optimize production processes and predict equipment maintenance needs. This predictive maintenance approach helps prevent unexpected breakdowns and reduces downtime, ensuring that machinery operates at peak efficiency. AI can also identify patterns and trends in energy usage, allowing manufacturers to implement energy-saving measures more effectively.
Robotics and automation
Robotic process automation has revolutionized manufacturing by taking on repetitive and dangerous tasks, improving product quality and reducing defects. Robots can perform tasks faster and with greater precision than human workers, leading to increased productivity and lower energy consumption.
For instance, robots integrated with IIoT sensors can optimize their operations based on real-time data, further enhancing energy efficiency.
By adopting smart equipment and high-efficiency machinery, manufacturers can significantly reduce their energy consumption and operational costs. These technologies not only enhance productivity but also contribute to a more sustainable manufacturing process.
Energy regulations and incentives
Government regulations and incentives play a crucial role in promoting energy efficiency in the manufacturing sector. These are designed to incentivize companies to adopt energy-efficient technologies and practices, thereby reducing their environmental impact and operational costs.
Environmental regulations set standards that manufacturers must meet to reduce their energy consumption and greenhouse gas emissions. These regulations often include mandatory energy audits, efficiency targets and reporting requirements.
For example, the European Union’s Energy Efficiency Directive requires member states to achieve specific energy savings targets through various measures, including improving industrial energy efficiency. Similarly, the U.S. Department of Energy has established energy efficiency standards for industrial equipment, such as air compressors, to ensure they operate more efficiently.
To support compliance with these regulations, governments offer various incentives and subsidies. These can include tax credits, grants and low-interest loans for companies that invest in energy-efficient technologies.
For instance, the U.S. federal government provides tax incentives for businesses that implement energy-saving measures, such as upgrading to high-efficiency motors and installing renewable energy systems.
The benefits of these regulatory measures and incentives are manifold:
- Cost savings: Companies can reduce their energy bills and operational costs by adopting energy-efficient technologies.
- Environmental impact: Lower energy consumption leads to reduced greenhouse gas emissions, contributing to global climate goals.
- Competitive advantage: Companies that invest in energy efficiency can gain a competitive edge by reducing costs and enhancing their sustainability profile.
- Innovation: Regulations and incentives drive innovation in energy-efficient technologies and practices, fostering a culture of continuous improvement.
By leveraging government regulations and incentives, manufacturers can enhance their energy efficiency, reduce costs and contribute to a more sustainable future.
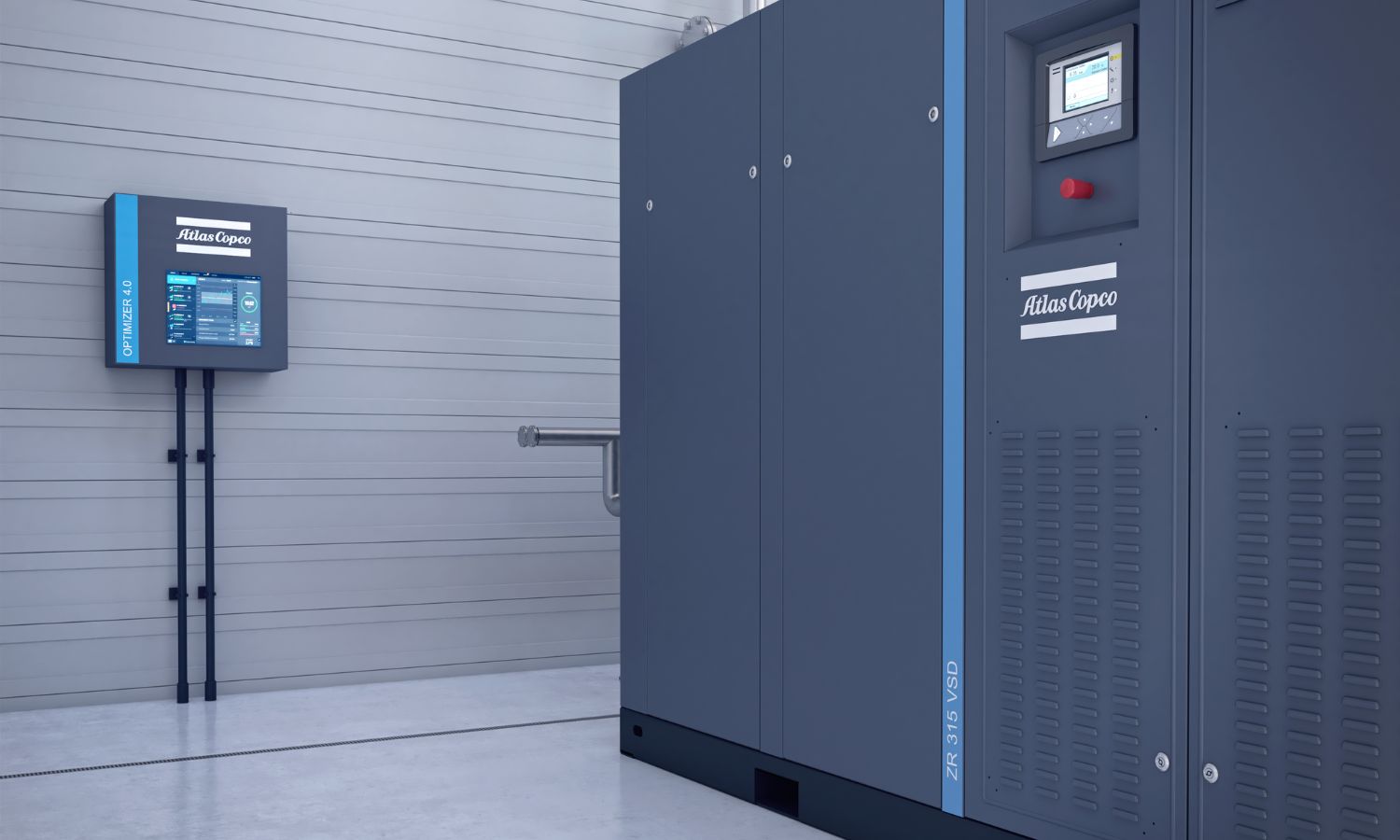
Challenges in implementing energy efficiency regulations
Implementing energy efficiency regulations in the manufacturing sector presents several challenges. These obstacles can hinder the adoption of energy-efficient practices and technologies, despite the potential benefits. Here are some of the key challenges:
Financial barriers
One of the most significant challenges is the high upfront cost associated with energy-efficient technologies. Many manufacturers are hesitant to invest in new equipment or upgrade existing systems due to the substantial initial cost. Although these investments often lead to long-term savings, the immediate financial burden can be a deterrent, especially for small and medium-sized companies.
Lack of awareness and information
Another major barrier is the lack of awareness and information about the benefits of energy efficiency and the available technologies. This knowledge gap can prevent companies from taking the necessary steps to improve their energy performance.
Technical challenges
Implementing energy efficiency measures often requires specialized knowledge and technical expertise. Manufacturers may lack the in-house capabilities to assess their energy use and identify opportunities for improvement. Additionally, integrating new technologies into existing systems can be complex and may require significant modifications to current processes.
Market and economic barriers
Market conditions and economic factors can also pose challenges. For example, fluctuating energy prices can impact the perceived value of energy efficiency investments. When energy prices are low, the financial incentive to reduce energy consumption diminishes. Additionally, the availability of financing options for energy efficiency projects can be limited, making it difficult for companies to secure the necessary funds.
Balancing high productivity with low energy use is a critical challenge in modern manufacturing. As industries strive to meet increasing production demands while minimizing their environmental impact, the adoption of energy-efficient technologies and practices becomes essential. This balance not only helps companies comply with environmental regulations but also enhances their competitive edge in a market that increasingly values sustainability.
While the initial investment in efficient technologies and processes can be substantial, the long-term benefits far outweigh the costs. Financially, companies can achieve significant savings through reduced energy consumption and lower operational costs. Environmentally, these practices contribute to the reduction of greenhouse gas emissions and the conservation of natural resources, aligning with global climate initiatives. Competitively, manufacturers that prioritize energy efficiency can improve their market position by demonstrating a commitment to sustainability, attracting eco-conscious consumers and partners.
The journey toward energy-efficient manufacturing is not without its challenges, but the rewards — financial, environmental and competitive — make it a necessary and worthwhile endeavor. By embracing advanced technologies, optimizing production processes and fostering a culture of continuous improvement, manufacturers can achieve sustainable productivity that benefits both the business and the planet.
Jayme Leonard is a Digital Marketing Specialist at Atlas Copco Compressors.