Exoskeletons can make workers safer on the manufacturing floor, and they will become more common as mobility and cost concerns become less of an issue.
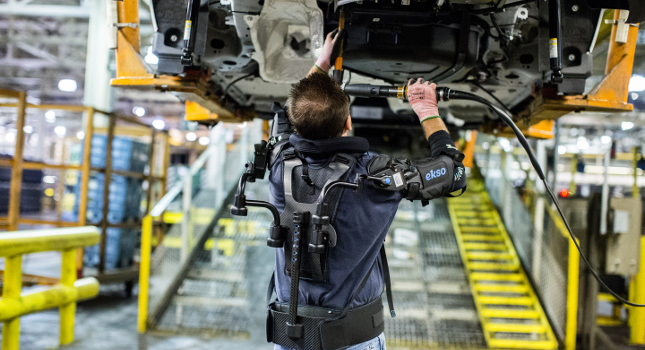
Manufacturing industries are turning to exoskeletons to help their workers perform tasks safely, more efficiently, and smarter. Once only seen in futuristic sci-fi movies, the exoskeleton is now finding its way into both industry and the everyday life of consumers.
Injuries associated with lifting and moving heavy workloads are a principal concern of labor unions, human resources departments, and government regulators. Lightening the workload, improving ergonomics, and reducing the time spent moving heavy items have been viewed only as band-aids, as worker injury still occurs. But exoskeletons could be a game-changing solution.
In the past, exoskeletons were wearable, high-precision braces. Recent advances in robotics have helped to create intelligent solutions that take heavy loads off the backs of human workers. Some designs allow a wearer to pick up and move hundreds of pounds without any stress on their body.
A wide range of industries are using exoskeletons. The medical field has been able to provide patients with exoskeletons that allow paraplegics, amputees, and others to walk again. Military personnel can use exoskeletons to move heavy supplies and equipment in the field. The agriculture industry involves significant manual labor, so farmers can use exoskeletons to lighten the load. Logistics firms see workers who move faster and more efficiently for warehousing and fulfillment applications.
Overcoming challenges linked to exoskeletons
Although exoskeletons allow for enhanced ability, mobility has long been a design challenge. Powering the exoskeleton often requires the worker to be tethered to a power source. But newer designs with lower power requirements can now be powered by a small battery unit for up to eight hours on a single charge. Batteries can also be hot-swapped, so little to no downtime is required.
Not long ago, exoskeletons improved the wearer’s capabilities but often slowed their movements. Workers would be trained on how to get the exoskeleton to move as desired. But predictive algorithms and artificial intelligence now allow for nearly no latency between the worker’s movements and the exoskeleton’s response. As a result, exoskeletons now function intuitively in real-time based on the worker’s movements, nearly eliminating the learning curve.
The initial investment associated with exoskeletons has kept many manufacturers out of the market. In response, exoskeleton producers have started implementing fee-based, robotics-as-a-service (RaaS) pricing models that let production facilities implement exoskeleton solutions without the upfront cost. When coupled with rising healthcare costs and claims associated with injury, exoskeletons are beginning to make fiscal sense.
This article originally appeared on the Robotics Online Blog. Robotic Industries Association (RIA) is a part of the Association for Advancing Automation (A3), a CFE Media content partner.