Leveraging an asset performance management (APM) system to digitize workflows Increased asset reliability and reduced environmental flaring for an oil and gas company in Oman.
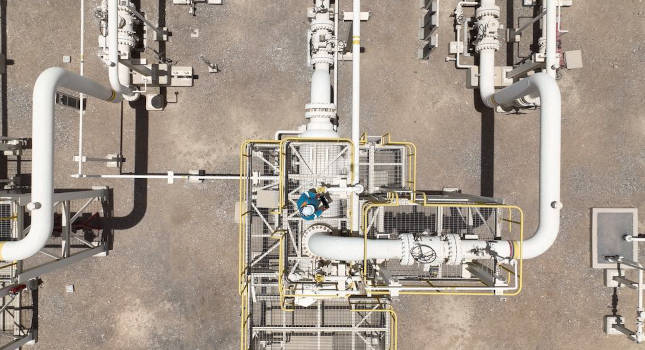
Learning Objectives
- Understand OQ Upstream’s main priorities for attaining operational excellence and how they were implemented.
- Learn how the asset performance management (APM) software solution they selected was the best fit in overcoming their challenges and meeting their needs.
- Learn about the significant benefits they achieved across their network of plants.
Asset management insights
- OQ Upstream used an asset performance management (APM) system to improve their operations, which had been paper-based and inefficient, leading to shutdowns and missed opportunities.
- The plan involved identifying the issues that had been plaguing them and streamlining their reporting, data and asset maintenance workflows.
- The results included greater plant efficiency and reliability and greater safety for the workers.
OQ Upstream is a global strategic management company based in Oman. It operates in 17 countries around the world and cover the entire value chain from exploration and production to marketing and distribution of end-user products. Its fuels and chemicals are sold in over 80 countries, making them a key worldwide player in the energy sector. The OQ Upstream business unit focuses on hydrocarbon exploration and production and operates almost all of Oman’s gas transportation networks.
The company currently produces 220,000 barrels of oil equivalent per day and transports natural gas for 150 connected parties in Oman via a large-scale network of high-pressure gas pipelines. Committed to operational excellence and a low-carbon future, OQ is working toward maximizing value for Oman energy and ensuring a sustainable future through asset optimization and digitization.
Managing more than 110,000 maintainable assets, more than 44 plants and stations and over 4,300 km of pipeline across Oman, OQ understands the importance of optimizing asset reliability and performance, and the role digitization plays in achieving sustainable, world-class operations. From the early OQ years, all reliability aspects were paper-based, scattered and treated in reactive mode.
“Digitalization is a key enabler in our journey toward operational excellence,” said Mansoor Al Abdali, managing director at OQ GN. With an eye on strategic asset management, the company initiated a project to digitize asset maintenance and reliability processes, ensuring asset integrity, cost efficiency and optimal plant operations.

Streamlining data, reporting and asset maintenance workflows
Asset performance optimization is a big concern in the energy industry. Failed assets result in shutdowns, and shutdowns lead to a loss of production, repair costs, environmental impacts and flaring as well as safety risks.
“We need to avoid shutdowns and failures,” said Hussain Al Naamani, reliability management team lead at OQ EP.
To avoid shutdowns, OQ needed to implement preventive maintenance and corrective action plans. To begin, they needed to identify and understand four key aspects:
-
Asset failure mode identification — to understand an assets’ failure modes in a way to design it out or eliminate it.
-
Discipline integration — to enhance data collection, storage, analytics, and data correlation among different disciplines.
-
Maintenance practices — to optimize total maintenance costs and to improve strategy and quality.
-
Reporting practices — to identify reporting workflow and tools, to enhance data quality and quantity and to develop dashboarding, visualization and automated key performance indicators (KPIs).
Once identified, these principles were applied to four main areas of operation: Reliability, operations and maintenance, integrity and chemistry and labs.
To address these issues, OQ wanted to develop a centralized digital system to access, share and analyze asset data. “We need to have one single source for data management, and we need to have the data reported to us,” Khulood Al Maawali, asset performance engineer at OQ EP.
To facilitate collaboration, establish reporting workflows and enhance data quality and quantity, OQ required a digital platform capable of providing dashboarding and visualization and automating key performance indicators. The expected outcome of their digital efforts was to end up with better decision-making to extend asset life and achieve proven reliability growth.
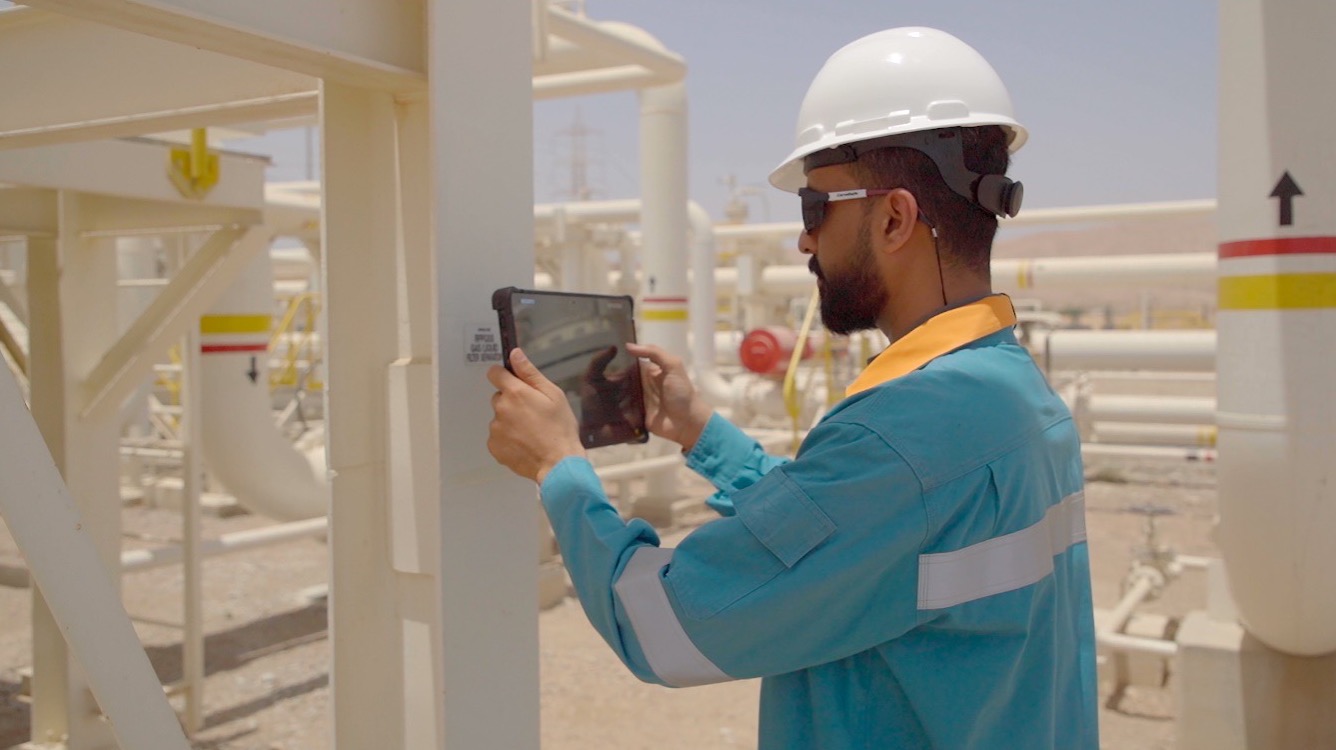
Providing a centralized digital solution
To manage asset integrity, reliability and maintenance, OQ selected Bentley Systems’ AssetWise APM, which provided a central digital platform for data integration and analysis, accessible to the internal team, field operations, and stakeholders.
“AssetWise APM first allowed us to solve the problem of data management; it is a powerful tool to store and analyze data. In addition, it is customizable to meet the business needs,” said Faisal Al Noumani, senior reliability engineer at OQ GN.
Using the APM offered OQ a flexible data environment capable of aggregating asset data from multiple sources, including mobile uploads from field inspections and the company’s internal computerized maintenance management system (CMMS). The software facilitates multidiscipline and stakeholder collaboration and data coordination, as well as serves as a single source of truth for asset data management and analytics, enabling proactive decision-making.
The interoperability and automation features of the APM’s streamline reliability management information for OQ by digitally calculating asset availability and maintainability and digitizing condition monitoring activities. By collecting, analyzing and managing accurate asset information, OQ gained valuable insights into asset health and has developed a failure reporting, analysis and corrective action system.
“Using the link between APM and the CMMS, all failures and downtime from assets are reported to us,” said Amran Al Aamri, reliability engineer at OQ EP. The APM technology also provides the foundation for OQ’s asset integrity management program and risk-based inspections.
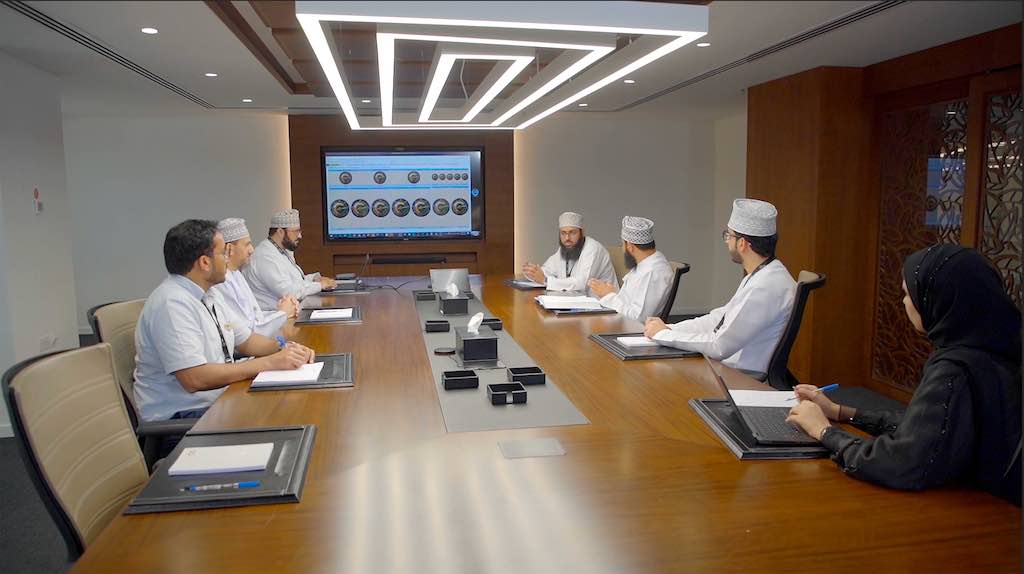
Improving business operations and sustainability
The APM has helped OQ overcome the challenges related to asset reliability management, monitoring and maintenance. It helps ensuring corrective action measures are in place, optimizing lifecycle asset integrity, performance and plant operations. Using the APM to digitize OQ’s lifecycle asset activities has allowed them to recognize the impact on reliability growth, reduction in failures and unplanned downtime and less flaring impact on the environment.
OQ’s strategy has resulted in several have achieved significant benefits including:
-
A single platform for all data reporting, storage, analysis and visualization.
-
Going from one plant in 2016 to 44 plants in 2022 with more growth on the horizon.
-
Digitizing site activities using handheld devices and barcoding.
-
Increasing plant reliability 25.7% within five years.
-
Maintenance optimization, resulting in 14.8% savings in total maintenance costs.
-
Uptime maintained at 98% as per company target over the last five years.
-
Zero Tier 1 and 2 Process Safety incidents since 2021.
-
Environmental emissions reduction by reducing flaring by 82.6% in the last five years.
Based on implementation at one compressor site, the digital solution saved 14.8% in total maintenance costs and reduced functional failures by 50% to achieve an annual operational reliability growth of 4.3%. Within the last five years, OQ has seen asset reliability increase by 25.7%, plant uptime operations maintained at 98% and flaring reduced by 82.6%, resulting in safer, more efficient, and, ultimately, optimal operations.
“After all these initiatives and technologies in which we end up with proven benefits in safety, production, reliability, availability and reduction in environmental impact, the next step is a digital twin,” said Khalid Al Fahdi, head of technical services at OQ EP.
Dedicated to driving continued business excellence and operational efficiency through digitization, OQ has already started a digital twin pilot project, incorporating smart technology applications and artificial intelligence.
The plan is to have a complete digital twin platform by 2024 where the APM will feed the model with asset performance data along with the data from digital monitoring devices to enable real-time, intelligent and sustainable operations.