Effective improvement of preventive fire protection.
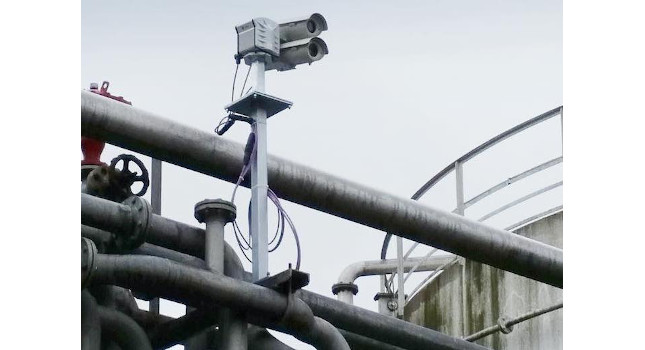
On the premises of a tank farm in Bavaria, Germany, defects were found in the fire extinguishing equipment. The operator commissioned TÜV SÜD Industrie Service to draw up a fire-protection concept for the refurbishment.
Deviating from the technical regulations, a more cost-effective variant was proposed, coordinated with the responsible authorities and implemented. Early fire detection with thermal imaging cameras was introduced as an essential part of damage control.
Fire protection must achieve protection goals. But not all measures that appear reasonable from a technical point of view are necessary. What is considered a “generally recognized rule of technology?”
What must be considered when renovating existing buildings? The central challenge in fire protection is to coordinate reasonable engineering services with the application of law and develop and implement a conclusive and economically justifiable fire-protection concept. At the same time, fire protection requires a high degree of technical knowledge and legal know-how.
Classification under building law
Tank farms are facilities of special kind and use. Their operation is associated with the handling and storage of materials with explosion or increased fire hazard. As with other special structures, preventive fire protection plays a central role in technical safety. Protective measures and safety precautions are therefore not only the responsibility of the operator but are also of public interest.
For this reason, the local building code (BayBO) contains, among other things, material requirements, which serve as “general clause of fire protection” for the protection objectives defined in Article 12. According to § 3, para. 1, however, deviations from the technical building regulations may be granted if an alternative solution meets the general requirements of paragraph 1 to the same extent. This means that if the generally recognized rules of architecture and technology are observed, the requirements and regulations laid down in law are deemed to have been complied with.
For the redevelopment planning of a tank farm in Bavaria, an engineering office presented a catalogue with extensive measures for the renewal of the fire extinguishing equipment. Total volume: 1.7 million euros. Independent TÜV SÜD engineers validated the plans. The part of the tank farm in need of rehabilitation and located on a harbor basin comprises 24 tanks with a capacity of between 600 and 2,000 m3, which serve as interim storage facilities for highly flammable liquids with a flash point (FP) of < 21 degrees Celsius according to the hazardous substances legislation.
At the time of the assessment, the following fire protection infrastructure existed: a non-automatic foam extinguishing system with a total foam agent supply of 10,500 liters, two submersible pumps in the harbor basin with a capacity of 180 m3 per hour each for the extinguishing water supply as well as the shell and roof sprinkling of the tanks, manual triggering of the shut-off valves and a separate transformer station with feed from the regional energy supplier. Emergency power supply was provided by the fire brigade.
Complete renewal of system
During the assessment of the proposed renovation concept, the TÜV SÜD engineers noticed that the engineering office’s catalogue of measures was, in fact, geared towards the complete renewal of the fire extinguishing system. It demanded a DIN-compliant solution, which provided for the mobile installation of three extinguishing agent centers in container form. These were to ensure remote irrigation and foaming of the tanks. This also included the necessary electrical, operating and control systems for the remote-controlled operation of the extinguishing agent control centers and the installation of new pipeline routes from the fire extinguishing control centers to the extinguishing equipment in the tank fields. For the three extinguishing agent centers alone, including the complex infrastructure, approx. 1.2 million euros were estimated.
Due to the large number of identified defects, TÜV SÜD engineers drew up a list of priorities with essential measures to be implemented about the protection goals. The main parameters for achieving the protection goals with the alternative solution were three sets of measures that are described below:
- Installation of an early fire detection system consisting of a fully automatic infrared measuring system from DIAS Infrared, which detects a possible fire event via temperature changes on the surfaces of different materials even before a fire can occur. In particular, the safety devices of the tanks, various pumps and motors, as well as the refueling systems on the factory premises are monitored. The system consists of seven thermal imaging cameras mounted on pan-tilt heads. If a certain temperature value is exceeded, this is immediately reported to the control room of the tank farm and to the local fire brigade. The cameras are surrounded by a weather-proof housing with ventilation and heating (fig. 1). Thus, they are well protected against external influences. This set of measures also includes remote triggering of the extinguishing agent supply from the control room and automation of safety equipment.
- Refurbishment of the piping system of the foam extinguishing and sprinkler system by replacement of leaky and corrosive pipe sections. In addition, three permanently installed foam extinguishing systems in the form of foam monitors shall be integrated for fire fighting. Additionally, a mobile and thus flexible foam monitor must be provided.
- Securing the power supply for early fire detection and fire fighting: According to the regional energy supplier, the maximum duration of a power failure is at least 30 minutes. As redundancy, an independent emergency power supply shall be provided for a period of two hours in the form of battery buffering and additionally by means of a diesel-powered emergency power generator.
The alternative fire protection concept was agreed and implemented with the operator of the tank farm, the responsible municipal authority and the local fire brigade. Early fire detection with thermal imaging cameras in conjunction with additional measures to optimize the fire protection infrastructure is now a central component of damage control. The operator is thus well equipped to face possible fire scenarios early and effectively in cooperation with the professional fire brigade – even in the event of a power failure and blocked access by a freight train (see fig. 2 and fig. 3).
Around one-third saved
Existing weaknesses in the fire protection infrastructure could be compensated with the help of the here presented measures. Compared to the previous, the TÜV SÜD fire protection concept with the fully automatic early fire detection of DIAS Infrared saved the tank farm operator around one third of the originally budgeted refurbishment costs – while still achieving the protection goals and the same safety level.