Social distancing guidelines are a challenge for manufacturers, but linear displacement transducers (LDTs) and plastic molding production lines can help improve automation while maintaining safety.
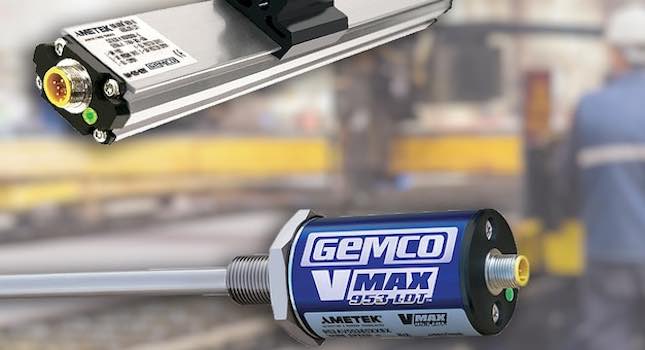
Many production line automation manufacturers are working to comply with COVID-19 social distancing recommendations without compromising work safety and production stability requirements. This is a delicate balancing act.
Two areas often cause the COVID-19 recommendations to be compromised: manual material handling, and service performed due to downtime. Industries such as metal forming, lumber, and plastics molding are very vulnerable for downtime, and COVID-19 has caused a renewed focus on how to minimize downtime and service needs, thereby securing the personnel from working closely together while still abiding by social distancing recommendations.
Linear displacement transducers (LDTs) improve production and personnel safety as it features high accuracy, ruggedness, longevity, programmable zero and span. They can withstand a lot of shock and vibration, which can help reduce or eliminate maintenance in rugged applications. An improved automated workflow helps companies to comply with the COVID-19 social distancing recommendations:
Plastic molding production lines can achieve improved automation using linear displacement transducers, which are designed to replace linear potentiometers.
The lumber industry can achieve flawless control of the production line with a reduced risk of downtime by installing LDTs instead of classic potentiometers or low-budget LDTs, which can cause more frequent downtime. Downtime leads to loss of production, and, perhaps more important in regard to COVID-19, it leads to service time which makes it difficult to keep the social distancing recommendations.
Metal forming applications provide the vibration or shock exposure LDTs are specially designed to handle. Stamping presses equipped with an LDT often experience very little downtime, which also reduces the need for service on the machine.