Wireless sensors can help discover maintenance issues with machines before they happen and give users access to real-time information. See four methods and four steps.
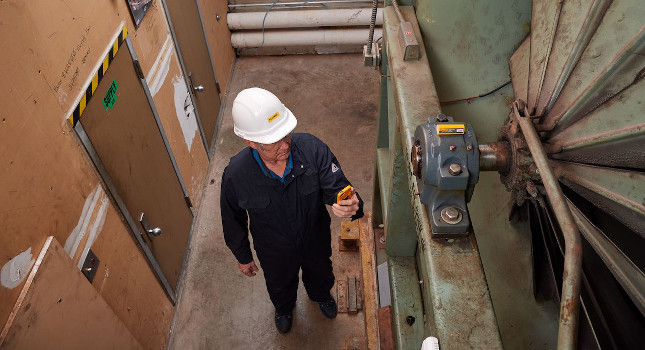
Condition monitoring is the best way to proactively determine when machines need maintenance. Collecting real-time data on an asset’s condition provides an accurate, up-to-date picture of asset health. This lets companies use resources more efficiently instead of relying on a calendar for planning maintenance actions.
For assets that often fail at random, such as rotating machinery, calendar-based maintenance is ineffective. Regardless of the type of asset, condition monitoring is the best bet for reducing unplanned downtime and production gaps and helping boost a company’s bottom line.
Condition-monitoring systems often start with wireless sensors, which are screening devices similar to blood pressure cuffs. While blood pressure cuffs do not solve blood pressure problems, they can provide readings to indicate if a problem exists. Machines monitored by wireless sensors can let a user know the machine needs to be inspected or maintained.
When equipment is continuously monitored with wireless sensors, users are alerted to changes or deviations from the norm. Once installed, they monitor assets 24/7 and trigger alarms when conditions reach certain thresholds.
In addition to providing real-time updates and making it possible to trend historical data, wireless sensors increase safety and efficiency. They are easy to install, even on assets in dangerous or hard-to-reach places. Once the sensors are installed, maintenance team members can avoid repeated trips to take regular measurements from these assets.
Once an identified asset has been downgraded from healthy to abnormal, the next steps are to diagnose the potential fault and its severity so users can plan the best corrective action.
Numerous technologies can detect machine faults and identify their severity. The method or methods used should be based on factors including asset types and budget. Choosing the wrong method can be akin to using a sledgehammer when a flyswatter would do—overkill.
By matching the asset and the company’s needs with available technologies, users can boost reliability and maximize maintenance dollars and resources.
Condition-monitoring methods
Predictive technology methods that detect potential faults the earliest aren’t always the best choice for every situation. Early detection technologies are typically both sophisticated and complex, meaning companies will need more expensive diagnostic tools and the maintenance team will need training on using those tools and interpreting the data.
Striking the right balance between the amount of warning a user has about the fault and the amount of time and money needed to spend to diagnose the fault is key. The most advantageous time to act isn’t always the earliest possible time.
So what condition-monitoring methods might fit the company’s needs? Here are some technical considerations for four common methods.
1. Oil analysis
Oil analysis is capable of detecting faults early. Monitoring lubricant, wear, and contamination offers a multifaceted look at asset condition and can alert users to potential issues before any actual damage occurs. Oil analysis also can be useful for low-speed machinery (<5 rpm), where it may be difficult to apply vibration analysis.
Oil analysis also can save money by eliminating time and materials spent on premature oil changes. However, obtaining oil samples and interpreting oil analysis data can be complex, and using a lab brings additional costs. Moreover, not all assets have oil that can be analyzed.
2. Ultrasound analysis
Ultrasonic analysis can discover things oil analysis can’t. It can detect bearing wear or fatigue early on—so early, in fact, it is often too soon to replace the bearings, and they should just be greased instead. Decibel readings reflect friction, and increased decibel readings can indicate a potential fault resulting from too much friction.
Ultrasound also can detect leaks — such as compressed air or steam — by identifying sounds at frequencies that wouldn’t be heard over a plant’s ambient noise. Like oil analysis, ultrasound also can be useful for low-speed machinery.
3. Vibration monitoring analysis
Vibration analysis has been established for decades, so vibration patterns and anomalies are well documented. They are easy to follow, which means extensive training or experience is generally not required.
Vibration analysis also can identify the most common mechanical faults: imbalance, looseness, misalignment and bearing issues. It identifies faults 12 to 18 months in advance, which allows plenty of time to react while there is still life in the asset, but without the waste of replacing or repairing them too early.
Because faults can be detected before they an asset’s performance is impaired, there is time to diagnose the fault’s severity and plan the necessary maintenance action without impacting production.
4. Thermography
Thermography can uncover electrical hot spots, faulty connections, overheated bearings, pipe blockages, issues with tank levels and more. It is best to use vibration combined with thermography for rotating machines because asset damage has often occurred by the time a problem is detected by thermography alone.
Wireless sensors can communicate real-time information related to all of these methods. By monitoring measurable conditions, such as capacity, temperature, pressure, or sound, and sending a signal when the relevant quality changes or reaches a certain threshold, wireless sensors make it possible to users to know about potential faults right away.
Four condition-monitoring steps
There are several steps to establishing a successful condition-monitoring routine. When making changes to a maintenance program, a best practice is to start with a small pilot program and grow it over time, rather than attempting to change everything at once. This allows the maintenance team and the organization’s leadership to buy in as they see the positive impacts of the changes.
Condition monitoring provides warnings about faults and makes it possible to schedule repairs without unplanned downtime and lost production. Here are four recommended steps:
- First, conduct a criticality analysis. It makes sense to keep the closest eye on the assets that have the most significant impact on the bottom line. If they aren’t being continuously monitored already, these assets are good candidates for wireless sensors.
- Second, identify probable failures the assets will experience.
- Third, decide on the technology best suited to identifying these failure modes, keeping in mind the team’s training and experience and the budget.
- Finally, trend and analyze the data from the wireless sensors to plan and execute maintenance actions at the most advantageous times, reducing unplanned downtime and extending the life of the assets.
Ready to get started? Make the most of maintenance resources by selecting the best condition-monitoring tools and technologies for specific application needs.
John Bernet, CMRP, mechanical application and product specialist, Fluke Corp. Edited by Chris Vavra, production editor, Control Engineering, CFE Media, [email protected].
MORE ANSWERS
Keywords: condition monitoring, wireless sensors, maintenance
Wireless sensors can provide real-time information for condition monitoring applications.
Condition-monitoring tools include oil analysis, ultrasound, vibration and thermography.
Steps to implement condition monitoring include performing a criticality analysis and identifying potential failures.
Consider this
What machines in your plant would benefit most from wireless sensors?