Will the COVID-19 pandemic accelerate the speed adoption of robotic and automation across the industrial sector? There are many factors at play.
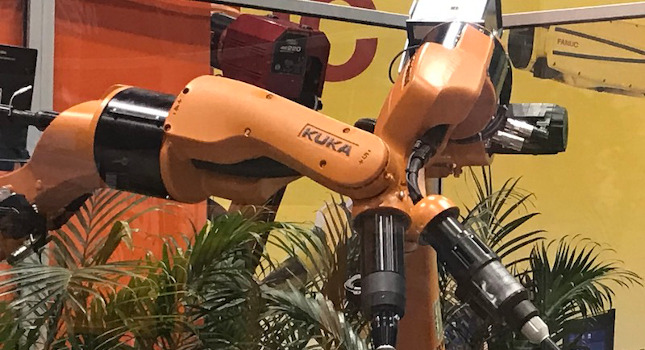
The current COVID-19 pandemic has shown just how dependent on people power many manufacturing operations still are.
Successive reports continue to confirm that for repetitive tasks, or those needing to be performed in hazardous environments, robots can offer the best solution. Moreover, robot deployment can lead to greater productivity and, in some circumstances, can continue unabated and remain largely untouched by the effects of a global pandemic such as we are currently experiencing.
“Robots and factory or function automation is enabling some manufacturing operations to remain largely untroubled by the need to shut down, restart or recover production simply because they are not susceptible to medical infection,” confirms Ian Hensman, sales manager at Kawasaki Robotics (UK).
Hensman argues that even in everyday, straightforward applications, robots and automation can massively boost productivity when the trading situation is normal. “Add in an unexpected event, such as the current pandemic, and the robots suddenly become the only part of a process which can continue to function and produce.
“Because robots and automation systems are programmed to perform their tasks perfectly every time, they can deliver increased efficiencies from the moment the ‘start’ button is activated: but in the event of a pandemic their ability to keep working can provide some businesses with a lifeline.”
Hensman goes on to point out that while the introduction of robots might displace workers from a production line, they can often be redeployed elsewhere in the plant, where they can add more value, leaving the repetitive, arduous and potentially dangerous tasks to the robots.
“Used in context and with careful contingency and continuity planning for the future, I believe that robots and automation will be the key to continued production during a people-related crisis, as well as a route to cost reduction, improved productivity and increased profitability,” concludes Hensman.
Lessons learned on use of automation, manufacturing productivity
In recent weeks, the narrative for many manufacturing sectors has started to shift from locking down to reopening. However, employers first have to ensure their workforce can return to a safe environment. “Shift patterns have to be revised and new processes have to be implemented. These are challenging scenarios for manufacturers, who are trying to regather lost ground without the means at their disposal at the start of the year,” said Andy Armstrong, sales & marketing manager at FANUC UK. He believes that the manufacturing sector is already looking to learn lessons from the pandemic.
“The manufacturing industry is renowned for its ability to innovate, and its resilience is second to none,” he continued. “Due to the uncertainty that surrounds the long-term implications of COVID-19 for businesses I believe that many will have already started to analyze the short-term impact, and ask themselves ‘what if this happens again?
“While some still hold the view that automation is a threat to jobs, that is not something FANUC has ever found to be the case. Industrial robots are eminently capable of doing a number of labor-intensive, menial, repetitive, and in many cases, dangerous tasks. In short, they are ideally suited for doing jobs that humans shouldn’t be doing.
“It is important to remember that an industrial robot will always be at a disadvantage to a human, as it does not have what we do – a brain – and it will only ever do what it is programmed to do. In the short-to-medium term climate of social distancing, industrial automation can certainly be used to maintain productivity during staggered shifts. However, it also provides an opportunity to upskill and redeploy employees into positions where they can add more value.”
As well as helping to maintain a degree of productivity, Armstrong believes that one of the other long-term benefits of automation is the ability to remotely monitor and control production via IIoT-enabled devices. “If we were to find ourselves in a similar lockdown situation, or if more strict social distancing measures need to be reinstated in the future, those sites which have a degree of remote control and operation should be able to remain productive without significant human presence on site,” continued Armstrong. “That is not to say that human involvement is not required, merely that greater connectivity increases the amount of work that can be undertaken further away from the factory floor.”
Localization: local agile manufacturing, automated manufacturing
While the full impact of the COVID-19 outbreak on manufacturing will probably not be known for a number of years to come it has become clear that the use of long distance and complex supply chains is not resilient to the challenges that we are currently facing. Mike Wilson, chairman of British Automation & Robot Association (BARA), believes that our ‘new normal’ will be a key driver for a move towards more local manufacture, equipped with agile, flexible automation to provide consumers with the choice, variety and speed that they now demand.
“The closing of factories, travel restrictions and general uncertainty across the world caused by the pandemic has certainly highlighted issues about the way our manufacturing sectors currently operate,” said Wilson. “Complex and long distance supply chains have been stressed or broken by the impact of the virus in different countries. Further, a dependence on manual operations is making it difficult to maintain productive capability given the restrictions on movement of people and social distancing requirements.
“Before the pandemic there was already was a growing trend towards mass customization which requires local, agile manufacturing. The increased cost of transport and the environmental concerns regarding carbon footprints were also already adding to the drive towards more local manufacturing operations.”
According to Wilson, the impact of the pandemic is accelerating the need for change. He said: “The application of automation and robotics technologies provides the opportunity to build highly productive manufacturing operations that are resilient in the face of future global challenges. One key benefit from the greater application of robot automation is to provide the opportunity to utilize work forces much more efficiently and productively.” Wilson advocates using the skills and attributes of staff to add value to the products and not simply having them perform mundane, repetitive or dirty and demanding tasks. He argues that this reduced dependence on labor will provide greater flexibility of capacity and resilience in times of labor shortages. “If a factory is largely automated it is much easier to scale production by varying operating times,” he said.
Wilson goes on to explain that the application of robot solutions also provides the agility to achieve the goal of mass customization. “Cost-efficient operations will no longer require mass production in large factories, often located in lower cost labor countries. Smaller local operations, with the capability and flexibility to meet local needs, can also be cost efficient. Being local it is not only more responsive to customer requirements but also not subject to issues that may arise in other parts of the world.”
Conclusion: Robots save manufacturing jobs
The increased use of robot automation should not be seen as a threat to jobs. Instead it should be seen as a way to build strong manufacturing businesses that are able to provide stable employment in roles which are both interesting and challenging. Achieving this objective will result in a manufacturing sector which is able to provide a strong contribution to our economies and well-paid employment for generations to come.
This article originally appeared on the Control Engineering Europe site. Edited by CFE Media.