Data-driven effort should focus on goals, not problems.
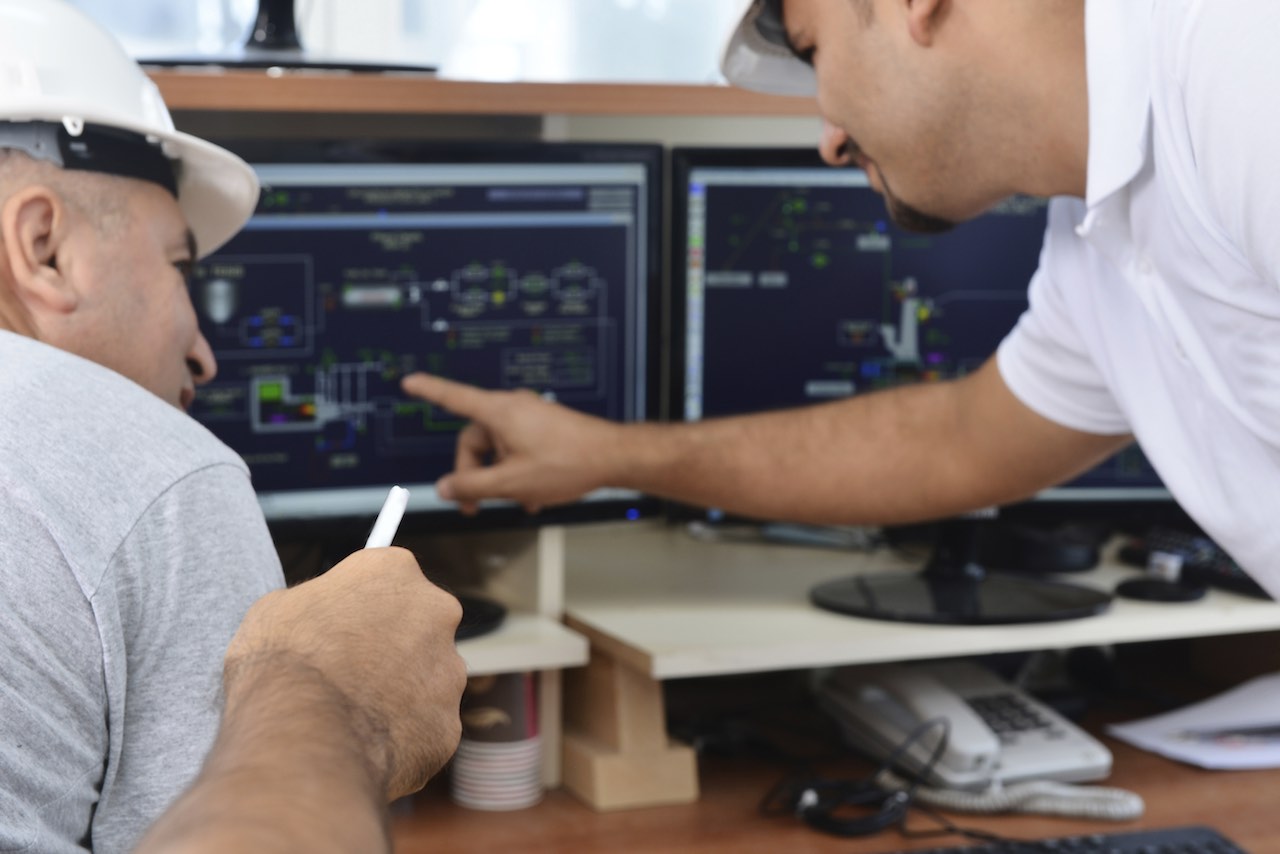
Assessing the viability of plant processes and equipment is a critical investment. Being proactive with an assessment is important. By using data, industrial leaders can estimate when a piece of equipment or process may fail due to incorrect scheduling, over-utilized equipment, or other factors.
Industrial leaders may hesitate to re-engineer a process, replace an old piece of equipment, or keep a larger supply of spare parts, but they either compromise optimal productivity and throughput or run a considerable risk by not preparing for the long-term or future vision.
If a piece of equipment fails, the impact can cause the entire production line to come crashing to a halt. If parts required to repair it are not readily available, the shutdown could last long enough to result in lost revenue. Depending on the criticality of the scenario, this could mean significant financial loss. History demonstrates that the time and costs of assessment services are worth the investment.
Focus on goals
When engaging in an assessment, stakeholders and project leaders do not want to be unnecessarily overwhelmed with details, no matter whether the assessment pertains to process or to equipment. The focus is for the project team to avoid making assumptions and instead to allow project leaders to articulate what their issues are. Keeping an open mind and emphasizing the goal of making improvements over identifying problems is also central to success. By involving stakeholders in the process and allowing them to highlight their ideas for improvement, project teams guide the exercise toward a positive outcome.
Project teams discuss their goals and objectives and talk about specific ideas and strategies. They find out whether there is a specific metric they want to achieve and get their buy-in for achieving those goals. Success in assessments means active participation by all the parties. This, in turn, means assuring that everyone is aware of the process in advance. Meeting with plant workers and key stakeholders early to explain what is going on fosters acceptance and cooperation. Â
Preparation and insight
Project team leaders prepare for an assessment by providing an overview of the process and the criteria of the assessment. As a result, participants know what data they will need. Explain why the audits and/or studies are happening and what the expected outcomes will be. In a new project there is always a defined scope, but the people who are agreeing to that scope are not necessarily the people working in the plant.
Early communication avoids surprising project leaders with unexpected questions or requests, allowing the additional time needed to prepare properly.
In one example, a stakeholder was asked to provide input on a series of assessment assumptions. A study was carried out based on those assumptions and this approach to communication proved successful. The project leaders understood the objective, received input, and reviewed assumptions and study findings ahead of the meetings and while the analysis was taking place. An effective input and feedback cycle minimized unnecessary rework of project assumptions and the study.
Early stages of the assessment process set the stage for success. Open communication becomes critical, especially as project teams explain why the data is needed and how it will be used in the study.
In many manufacturing businesses, different facilities within the same organization do things completely differently. This underscores the importance of understanding protocols and ensuring that everyone can provide data for their aspect of the project. Understanding the participants and their roles can be complicated, so it is essential to identify and involve the right people from the beginning. They need to understand both the process and the desired outcome as well as what data and information is needed to get there.
Proactive value
An assessment doesnât necessarily have to be precipitated by a problem. There are always opportunities for improvement, and an assessment can be a proactive way to improve the facility or a process.
In another example, a project decision maker had rated equipment at a certain age, factoring that it had several years left before the equipment would need to be replaced, although he acknowledged it was only in moderate condition. In the proactive assessment, the project team asked about spare parts and found that, while the equipment was in acceptable running condition, the industrial group did not have the appropriate spare parts. So if the line went down operators could not immediately make the repair and keep the equipment running.
Data from assessments, along with information in the equipment manual, help the team decide the requirements for a spare-parts inventory. Efficient inventory management practices ensure that project leaders know exactly which parts are available at all times and will preclude purchasing multiples of the same part. A proactive assessment provides a comprehensive study.
If a full inventory of spare parts is not feasible, there can be a quick reference for how to get the parts when needed, including the lead time to receive the parts, so operators are prepared for an equipment failure. When equipment becomes obsolete or an equipment manufacturer goes out of business, spare parts become even more critical. Proactive assessments help clients stay ahead of such situations.
Consider additional assessment questions to understand what the capability of the process is and what impact future forecasts and demands will have on the process. Will it require an additional piece of equipment or does the current process have the ability to achieve the future rate? Are there opportunities to improve the current processes in order to avoid the potential cost impact of buying a new piece of equipment?
Making better decisions
In the case of newer equipment, failure to follow the manufacturerâs recommended guidelines for preventive maintenance causes premature wear and tear. The resulting delays can be avoided with a solid understanding of the equipment and an effective maintenance plan. Equipment assessment can include downtime data and maintenance reports. This helps project leaders and operators to make decisions about how much to invest in each piece of equipment. And this information is especially useful if the equipment is under warranty. The data can be sent to the manufacturer for review and discussion.
Much of the value of an assessment is the data that it generates. For a new process or system, a before and after comparison can show the benefits of the assessment and understand the resources needed to achieve those benefits. It also helps to have a fresh set of multi-disciplinary, multi-market experts for an assessment. This is typically something that can take a process to its next level.