Businesses are looking to remote management strategies where they leverage smart technologies, mobile devices, remote access connectivity and communications tools.
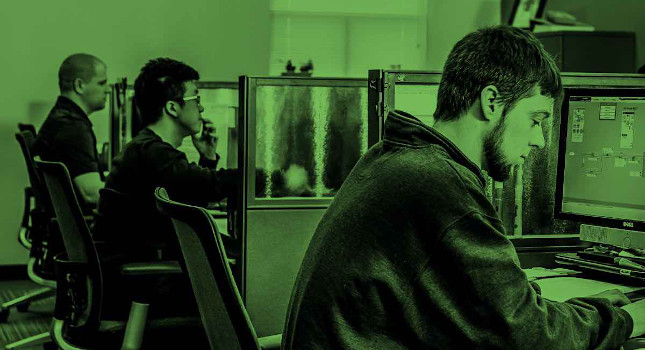
Amidst the current world COVID-19 pandemic crisis with shelter-in-place orders and imposed travel restrictions, many industrial facilities continue to feel the strain from both a business and resource perspective. They are having to adapt to a new norm and look for alternative ways to do business as usual. As they persevere and move forward to meet overall business goals and objectives, they look to remote management strategies where they leverage smart technologies, mobile devices, remote access connectivity and communications tools. All to ensure personnel and any third-party partners can help keep their critical infrastructures up and running efficiently.
A remote and secure infrastructure
The team of control system analysts at MAVERICK’s PlantFloor24 global operations center understands the remote management shift facilities now face and the platforms, technologies, application tools and services required to run from several locations. For them, it’s pretty much business as usual, but it’s by no means easy. They have had to adapt along with everyone else.
“For years, we’ve been able to access network servers and work remotely from any location to provide sustaining services and remote monitoring support for companies running on multiple platforms,” said Eldin Dilberovic, senior control system analyst. His colleagues Jordan Clark, Sean Pass and Brad Carrico concur. To them, the biggest impact is not being able to collaborate and work alongside colleagues and customers at a central location.
“Remote management support is what we do on a daily basis,” said Clark, sustaining services team lead. “The difference is in how we collaborate. Our team is now communicating more via mobile devices, standard communication tools, such as Microsoft Teams or Skype for Business, and cloud-based applications like OneDrive with the proper security in place to share information, keep all on schedule and get whatever project we’re working on done.”
For Carrico, a control system analyst, who is currently working on a Microsoft Windows patching project updating computers and servers on industrial process control networks, the transition to working remotely has been a matter of changing his physical location. “Fortunately, with this type of work, I can do everything remotely from the PlantFloor24 office with the same efficiency and productivity as working at the customer site,” he said.
In performing the patching work, Carrico follows specific procedures to verify and ensure all systems are compatible and any updates are approved and tested in a virtual lab environment. “From there, I coordinate with the customer plants to schedule a day to execute the update installs and reboots,” he said. “We then discuss which servers could affect production while they are being rebooted. Communication with the plant manager and lead engineers is the most important aspect, making sure they feel comfortable with the process.”
If a facility already has secure remote system access in place, they can take advantage of various types of third-party services immediately, the team explained. Otherwise, if they are starting from scratch, it can take about two to three weeks for them to set up and establish remote access capabilities. “Time is of the essence for many facilities, so setting up a remote access infrastructure in advance is key to avoid delays and lost productivity,” Dilberovic said. “That way, when companies call us for an emergency or need other assistance, we can access their systems and help them get the job done right away.”
For the team to gain remote access, it must connect to a facility’s systems via a secure and dedicated network infrastructure. “Each company is different in its approach to securing the system,” said Pass, sustaining services team lead. “We work with the client IT teams to follow all required security protocols.”
Onsite projects go remote
Beyond the day-to-day remote monitoring service offerings, the team also combines its expertise with senior control systems specialists, project managers, engineers and senior consultants to perform onsite maintenance activities, legacy control system migrations, high-performance human-machine interface (HP-HMI) storyboarding, alarm monitoring and more. For many of these essential workers, much of the onsite project work is now being done remotely.
For example, Dilberovic was initially working on a startup for a large project where they were replacing and checking a variety of instruments, valves, motors, network servers and more. Once the travel restrictions were imposed, the project came to a temporary halt as he and some of the onsite team had to switch gears and work remotely.
“The facility had to validate remote access network capabilities before we could start work again,” Dilberovic said. “Once the client had its remote infrastructure set up, we could securely perform the typical startup tasks, including programmable logic controller (PLC) and distributed control system (DCS) testing, HMI programming and remote device checkout tasks like alarm and loop checks.” The team was able to successfully finish the job on schedule. A few team members remained onsite to help facilitate the process while providing line of sight during instrument checkout.
Clark had a unique experience working onsite for a large brewing company where they were migrating from one platform to another. “For critical areas in the facility, some workers stayed onsite while others traveled home to work remotely,” he said. “Under the circumstances, we experienced new challenges in terms of equipment delays to the site and performing simulation and factory acceptance testing (FAT) prior to startup. Typically, we have customers come to the office and sit down with us to do testing on simulation stations that we set up. It’s hard to do now.”
Despite the challenges, the team worked through their project. They discovered collaboration was more essential than ever and communication tools were a necessity as they set up customer access to simulation environments remotely to continue working on the project.
During these challenging times, the team learned a valuable lesson: You can have all the technology in the world to make you run better and more efficient, but clear communication, collaboration and working together as a team is the key to success. Remote business as usual is possible for manufacturers if they have the right partner to collaborate in an efficient manner.
Ram Ramamoorthy is operations manager, strategic manufacturing solutions at MAVERICK Technologies, a CFE Media content partner. Edited by Jack Smith, content manager, Control Engineering, CFE Media and Technology, [email protected].