The electrical system is sometimes overlook at food processing facilities. Here are three ways to maintain the plant's electrical well-being and prevent potential malfunctions and safety hazards.
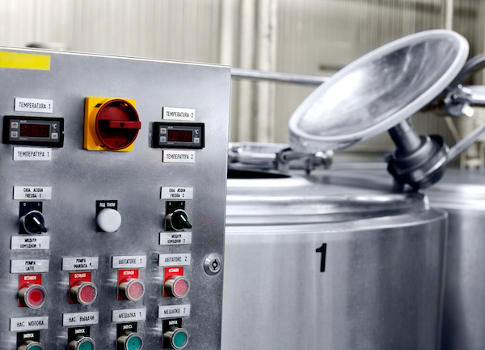
Do you give enough care and consideration to your food processing facility’s electrical equipment? The electrical system often is taken for granted until it’s time to upgrade or replace a major component. Consider these three tips to prevent food plant electrical system malfunctions along with factors that impact the plant’s electrical well-being.
1. Reduce arc flash hazards with maintenance mode switches
An arc flash occurs when flashover of electric current deviates from its intended path and travels either through the air or to the ground. These incidents are extremely dangerous and can cause not only injuries, but death. According to OSHA, an arc flash can result from a variety of factors including:
- Dust
- Dropping tools
- Condensation
- Material failure
- Corrosion
- Faulty installation.
Reducing these incidents is crucial, which is why arc-flash hazard analysis has now become a part of every project. These hazard studies include specification of proper overcurrent protection equipment and settings.
While most manufacturers offer arc-resistant switchgear, the equipment is very expensive and takes up a much larger area than traditional switchgear. However, manufacturers are also offering circuit breakers with a maintenance mode, allowing maintenance staff to flip a switch on the circuit breaker, greatly reducing the arc-flash hazard during the maintenance operation. Maintenance mode switches are much more cost effective than arc-resistant switchgear.
2. Locate your electrical equipment in proper spaces for optimal longevity
As long as it’s not overloaded, well-maintained electrical equipment can last more than 20 years. However, the location a plant’s electrical equipment can greatly affect its lifespan.
Locating electrical equipment either in production spaces or adjacent areas with little protection typically results in failure at one point or another. This primarily applies to wet-type process areas with heavy washdown requirements.
Understand that there are also consequences for locating electrical equipment in dry, dusty areas of the plant. If you don’t perform routine maintenance and cleaning on the equipment, a plant manager can expect a line or plant shutdown.
There was one particular incident where a main piece of switchgear was in a room with mechanical ventilation near product silos. It eventually accumulated enough dust inside to cause a large circuit breaker failure, shutting down part of the production for more than 24 hours.
3. Take advantage of modern electrical system advances to monitor energy usage
Though the makeup of the basic parts of electrical distribution systems aren’t much different than they were 30 to 40 years ago, all manufacturers now offer larger circuit breakers with electronic tripping and metering systems.
For example, switchboards now can be specified with all circuit breakers, which have electronic metering to include main and distribution breakers.
With proper design, such as segregating loads into lighting, process, HVAC, refrigeration, etc., owners can review different building loads at any time and determine where the largest energy users are.
– Jud Walker is a senior electrical engineer at Stellar. Walker has over 20 years of experience in engineering and construction of commercial, institutional, and industrial facilities. This article originally appeared on Stellar Food for Thought blog. Stellar is a CFE Media content partner. Edited by Joy Chang, digital project manager, [email protected].
Stellar is a CSIA member as of 7/20/2015