Our panel of experts dives into the complexities of maintenance, repair and operations (MRO) for strategic success.

MRO Insights
- It’s critical to eliminate data gaps for optimal MRO, but achieving that requires shifting perspectives.
- Facilities can reduce unplanned downtime, extend equipment lifespan and maintain peak operational efficiency by combining manufacturer guidance with a structured, consistent approach.
- Every investment in maintenance technology is made with the goal of keeping machines operational for as long as possible, minimizing disruptions.
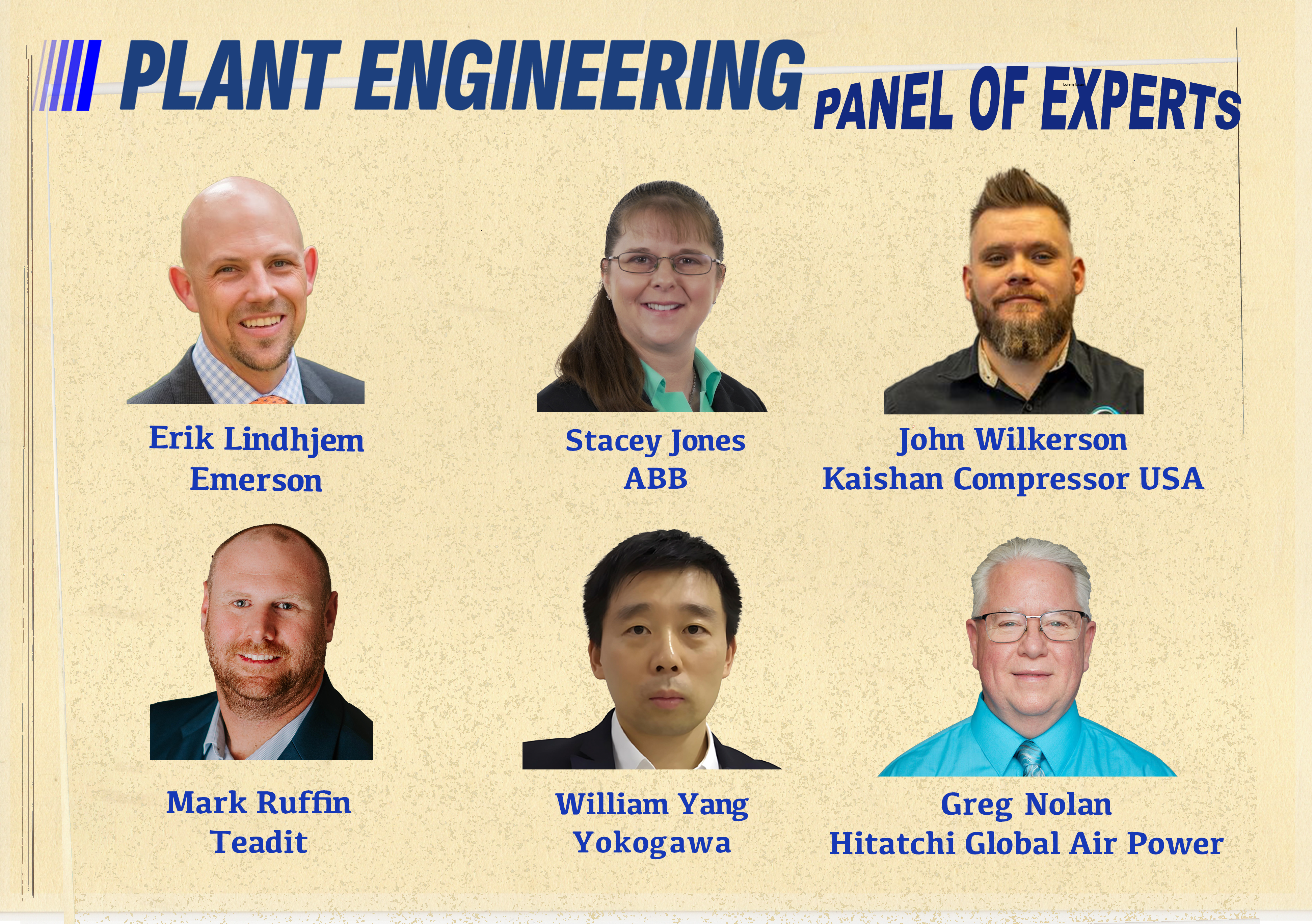
What are the key challenges faced by organizations in managing maintenance, repair and operations (MRO) activities effectively?
Mark Ruffin: The effectiveness of predictive maintenance (PdM) depends on high-quality input data. Incomplete or inaccurate information can lead to unnecessary interventions or missed failure risks. Accurate data collection is, therefore, a top priority.
Erik Lindhjem: Often, we talk about data silos as the primary roadblock to better maintenance and reliability. That’s true — if data cannot be brought into higher level systems for visibility and analysis, teams struggle to provide efficient and effective maintenance to their sites.
However, one issue that is less commonly discussed is data gaps. Many facilities are decades old with aging assets that simply aren’t instrumented. While modern technologies like wireless vibration monitors and edge analytics devices make it easier to bring these stranded assets into the fold, prioritizing that work can often be a struggle. Navigating the complexity of eliminating data gaps is often a matter of shifting perspectives.
In many cases, even plants with a wide array of continuous condition monitoring tools are still performing manual rounds on some low priority assets. Even that won’t stop the plant if they fail can contribute significantly to production losses and performance degradation. Taking the time to build a business case around instrumenting stranded equipment can go a long way to closing those data gaps and increasing visibility into holistic plant health — a key driver of operational excellence and competitive advantage.
William Yang: Lack of visibility into inventory and spare parts. Integration issues among systems like computerized maintenance management systems (CMMS), enterprise resource planning and procurement platforms. Inconsistent maintenance practices across teams. Skills shortages for handling advanced MRO tasks.
How do you prioritize maintenance tasks to ensure optimal equipment performance and longevity?
Greg Nolan: By understanding the individual component’s operation and relationship to the operation of the whole compressor, a technician can learn which components are likely to cause down time and/or erratic operation. For example, in a dirty production environment, filters and coolers will need more attention.
Yang: Use a risk-based approach focusing on critical assets with the highest operational impact. Leverage condition-based monitoring data to schedule predictive maintenance. Align tasks with production schedules to minimize disruptions.
Ruffin: Maintenance teams can improve their skills by focusing on reliability engineering principles, root cause failure analysis and best practices for material selection and installation.
John Wilkerson: Prioritizing maintenance tasks effectively begins with following the manufacturer’s guidelines. Manufacturers possess unparalleled knowledge of their equipment, making their recommendations the gold standard for ensuring optimal performance and longevity.
A well-designed checklist, developed in collaboration with the manufacturer, is an essential tool. This checklist should outline daily, weekly and periodic tasks to ensure that critical components are inspected and maintained on schedule. For example, certain parameters may require daily attention, while others can be checked less frequently based on the equipment’s operating conditions.
Additionally, having trained personnel on-site who understand both the technology and the specific requirements of the equipment is vital. Engaging directly with the manufacturer’s technicians or engineers to validate maintenance priorities and ensure alignment with the checklist can further enhance the effectiveness of maintenance practices.
By combining manufacturer guidance with a structured, consistent approach, facilities can reduce unplanned downtime, extend equipment lifespan and maintain peak operational efficiency.
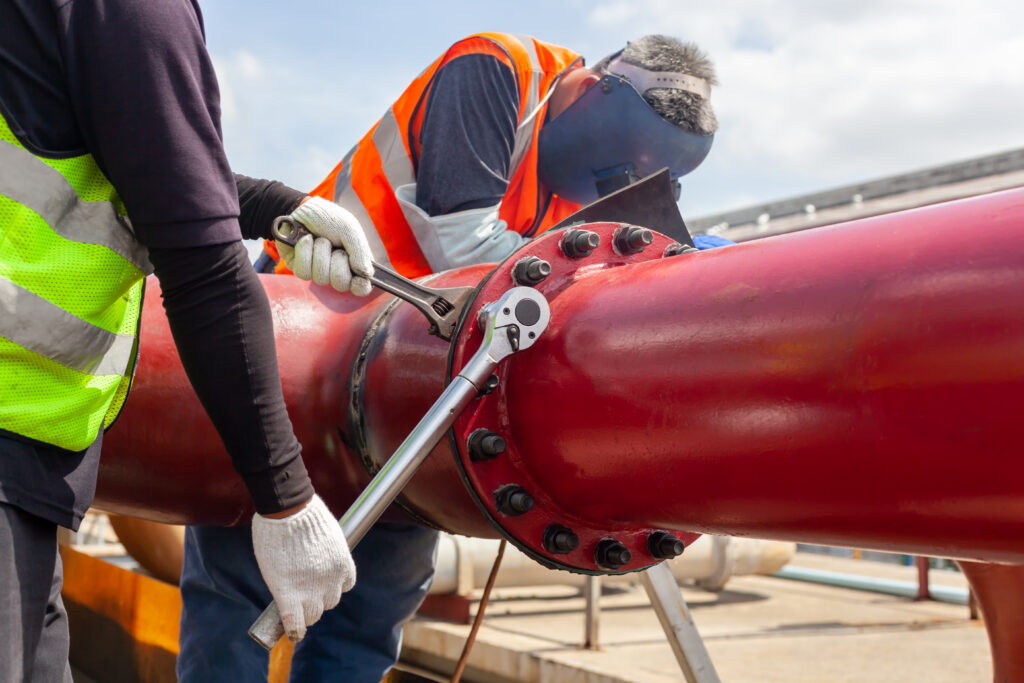
In your experience, what role does technology play in streamlining MRO processes and reducing downtime?
Yang: Internet of things (IoT) devices enable real-time monitoring of equipment health. Artificial intelligence/machine learning (AI/ML) analytics predict failures and optimize repair schedules. Digital twins simulate scenarios for proactive decision-making. CMMS streamlines task scheduling and inventory management.
Ruffin: Managing MRO across diverse assets requires a strategic approach that integrates asset criticality assessments, optimized inventory levels and the adoption of durable, long-lasting materials to reduce overall maintenance frequency.
Nolan: In addition to advancements in compressor instrumentation, compressor fluid analysis provides valuable insights into the health of a compressed air system. For instance, detecting metal particles or debris in the fluid can indicate issues such as bearing wear or other potential breakdowns. Similarly, vibration analysis offers a window into the system’s condition by monitoring the vibrations emitted by the machine. This technique is especially effective when baseline measurements are taken at installation, allowing users to track changes in the vibration profile over time. These changes can provide experienced analysts with critical clues about underlying malfunctions or emerging problems. In aggregate, these tools help with predictive and preventive maintenance that reduces unscheduled downtime.
What metrics do you consider most important for measuring the effectiveness of MRO operations and what role do analytics play?
Nolan: Minimizing unscheduled maintenance. By far the most expensive aspect of a compressor being down is lost production and compressor rental.
Yang: The key metrics that are the most important for measuring the effectiveness of MRO operations are meant time between failures, mean time to repair, equipment uptime percentage and maintenance cost per unit of production.
The role analytics play is that they identify trends and root causes of failures and provide actionable insights for optimization.
What challenges do you encounter when managing MRO for a diverse range of equipment and assets?
Ruffin: A well-balanced maintenance strategy integrates proactive maintenance, predictive analytics and material advancements to minimize unexpected failures and optimize asset life.
Yang: The challenges we encounter for our customers include training technicians to handle a wide array of systems and technologies, standardizing maintenance practices for varied equipment types and managing the compatibility of spare parts across brands.
What are the primary drivers for your organization’s investment in maintenance and repair technologies?
Wilkerson: The primary driver behind our organization’s investment in maintenance and repair technologies is maximizing uptime. Equipment is purchased to perform a specific job and ensuring it runs reliably and efficiently is the goal.
To achieve this, we prioritize investing in high-quality, reliable parts and skilled personnel — whether they are in-house team members or external vendors. Additionally, having a third-party perspective to oversee the maintenance process adds an extra layer of assurance and accountability, helping to identify areas for improvement.
Every investment in maintenance technology is made with the goal of keeping machines operational for as long as possible, minimizing disruptions. Scheduled downtime becomes an opportunity for proactive adjustments rather than reactive repairs. By focusing on uptime, we can ensure that our equipment not only meets performance expectations but also delivers long-term value.
Ruffin: The highest return on investment in maintenance improvements comes from predictive diagnostics, enhanced material performance and optimizing maintenance schedules based on real-world failure trends.
Yang: For our customers, supporting digital transformation initiatives for operational excellence, reducing operating downtime and costs, improving safety and regulatory compliance and achieving sustainability goals through energy-efficient operations.
How do you ensure effective communication and collaboration between maintenance teams and other departments?
Ruffin: Regular meetings, metric reviews and quantifying results through actual data are three activities that help maintenance teams and other departments to align on similar goals. Once similar goals are established, the activities of the individual teams better align.
Yang: Use centralized digital platforms (e.g., CMMS) for real-time updates and task management. Leverage dashboards for transparent performance monitoring and decision making. Hold regular cross-departmental meetings to align priorities and schedules. Foster a collaborative culture with shared goals and KPIs.
Lindhjem: One of the key barriers to effective collaboration, both within the maintenance and reliability department itself and between maintenance and reliability and other departments, is the reliance on people to communicate what is happening in the plant.
Today’s plants are often running lean teams, and those people are busy nearly all the time. It’s not uncommon for a team to focus on a repair and then immediately move one to the next one, leaving little or no time for documenting activities or effectively handing off the torch to another person or shift. While that process helps them get a lot done, it also makes it very difficult to close the loop on reliability across the plant.
Other groups — such as operations — are equally pressed for time. If an operator has hundreds or thousands of alerts coming in and must sift through them to identify what needs to be done, they will struggle to communicate critical data to the maintenance team to help them address the root causes and start focusing on bad actors around the plant.
The solution is to build workflows that automate recording and analysis of maintenance activities to curate knowledge for continuous improvement. Asset monitoring and predictive maintenance software solutions help teams make better decisions, record their activities and track and trend root cause to eliminate defects more effectively in assets across the plant.
These software solutions also provide built-in collaboration tools to help teams build a knowledgebase of maintenance activity tied to each asset, so every repair doesn’t have to start from scratch. The more teams can systematically record information and document what they’re doing and the more tools they must connect that information for analysis, the faster resolution will occur each time an event recurs.
Additionally, teams need configurable, personalized and action-oriented interfaces tailored to various user personas at their sites — typically delivered through a lifecycle maintenance portal. Such technologies enable users to effortlessly access role-specific information and collaborate effectively with their peers. For example, a call support module will enable a maintenance manager to assign calls to any member(s) of the internal MRO team for follow-up on reported issues. The lifecycle maintenance portal should support this workflow by providing automatic updates throughout the resolution process. Teams using a lifecycle maintenance portal can also leverage modules to assist both maintenance teams and business decision-makers in tracking the renewal status of their services or software subscriptions. This coordination ensures uninterrupted support.
With the rise of AI and ML technologies, there has never been a better time to begin regularly documenting maintenance activities. The failure, cause and response data teams collect will be a critical cache of data to feed the generative artificial intelligence tools just over the horizon. Building that data store today will give teams a critical advantage as they deploy the technologies that will drive the future of maintenance and reliability.
Wilkerson: Effective communication and collaboration between maintenance teams and other departments are critical for ensuring smooth operations and minimizing disruptions. At our facility, we achieve this through daily Gemba walks — structured, collaborative walkthroughs where key personnel from various departments come together to share updates and align on priorities.
Each morning, a designated leader, typically the plant manager or operations manager, facilitates the Gemba walk. During the walk, department heads present updates using visual tools such as dry erase boards placed in their respective areas. These boards provide an at-a-glance view of daily tasks, planned downtime and ongoing maintenance activities. This practice ensures that all departments — maintenance, production, engineering and warehouse — are informed and can coordinate resources effectively. For example, a planned maintenance task requiring a scissor lift is communicated in advance, avoiding conflicts with other departments that might need the same equipment.
The Gemba walk process also extends to departments outside the plant, such as finance and human resources. Open communication channels and accessible visual tools help bridge the gap between operational teams and office staff. For example, finance teams benefit from understanding maintenance schedules and unplanned expenditures, as downtime directly impacts budgets. Regular updates on dry erase boards or informal check-ins ensure that office personnel stay informed and engaged.
Additionally, we emphasize training key personnel in effective communication to facilitate cross-departmental collaboration. By empowering individuals with the tools and knowledge to share critical information, we create a culture of transparency and teamwork that supports operational efficiency and minimizes logistical conflicts. This approach has proven invaluable in aligning maintenance efforts with broader organizational goals.