Perhaps the best opportunity for a quick payback in improving a steam system is evaluation and improvement of the condensate return system. Returning as much of the condensate as possible to the boiler feedwater stream pays rewards in two ways.
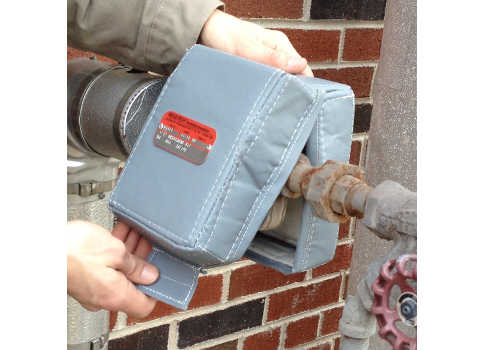
Perhaps the best opportunity for a quick payback in improving a steam system is evaluation and improvement of the condensate return system. Returning as much of the condensate as possible to the boiler feedwater stream pays rewards in two ways. First, condensate is distilled feedwater that has already been treated, thus reducing the need for expensive treatment of makeup water. Secondly, condensate contains a significant amount of heat energy. As preheated feedwater, it offers a significant reduction in fuel use for the same boiler output.
Opportunity for Saving
Steam is the main energy source for many plant operations. Steam heats water or other liquids, rotates turbines to generate electric power or mechanical energy, and is used for dozens of other process purposes. Whenever the steam gives up its energy, hot condensate is produced, and should be captured.
In some older steam systems, condensate return piping is incomplete and condensate simply drains away. In these situations, there is a clear need to extend return lines wherever possible. Older systems will also benefit from an evaluation of existing steam traps, and owners should replace or repair them as needed. Many newer steam trap designs are more efficient and have increased reliability. A steam system expert can help owners select the correct trap for each situation.
Return System is Critical
Armstrong International is a supplier of a wide range of supplies and services for steam systems. Armstrong’s Nevena Iordanova is a Senior Utility Systems Engineer, and a DOE-qualified steam system expert. She emphasizes the importance of the steam trap in collecting and delivering hot condensate for return to the feedwater cycle. She states "The purpose of any steam system is, first, to deliver steam to a user that needs heat and, second, to return condensate back to the boiler." Most boiler system operators know that this second function often does not receive adequate attention. A review of the entire system is needed.
System Overhaul Needed
A complete overhaul of the plant condensate system usually requires the assistance of professionals that are seldom present on the plant staff. Iordanova advises, "With time, there are many changes in the plant that can have a negative effect on the condensate return system. Main header lines and central receivers normally stay the same, but the amount and quality of the condensate discharged to them changes all the time." Plant equipment is changed out, processes change or are abandoned, and new processes are added.
She notes, "These changes can accumulate to the point where condensate piping is no longer adequate, resulting in high back-pressures, water hammer conditions, and ruptured or freezing valves and pipes, with accompanying leaks."She points out, "Not only is hot condensate wasted, but the safety, integrity and reliability of the entire system goes beyond the plant’s control." At this point a system study is the needed step. Companies such as Armstrong and others offer these services.
Role of the Steam Trap
Iordanova points out that steam traps, located on the border between the steam and the condensate, make condensate recovery possible. She notes, "Every trap makes sure that the condensate is removed at the moment it is formed, and is discharged downstream to the boiler house for reuse. When the steam traps are properly sized, installed and maintained, there is no need for the operators to intervene in the system to "fix" it by opening drain valves, wasting condensate, or bypassing them, wasting not only condensate but steam, too. Properly functioning steam traps are essential."
The first step is to establish a steam trap management program with a clear objective. It is essential to have frequent inspections to establish the status of each trap, and a commitment to correct indicated problems promptly. This approach sounds effective, but too often the inspections are postponed or incomplete.
Inspections Often Deteriorate
Commonly when a program is established, inspections are carried out as scheduled for a few months, then other priorities create postponements. Inspections can be tedious, and may require personnel crawling into tight, wet, hot spaces. The schedule begins to slip, and the number of failing traps increases. These failures are periodically corrected, but it might be months or years before the next complete inspection. The collection of condensate plummets.
One solution to this problem is to install a steam trap monitoring system with an understandable reporting output. As individual valves malfunction, maintenance workers can quickly schedule corrective actions. Iordanova says, "Armstrong suggests installing an automated monitoring system to all traps, with a priority for the high pressure and medium pressure steam traps, as they are the ones that waste the most energy. Armstrong monitoring will show an alarm for failed traps as soon as a failure occurs, minimizing the potential energy loss if the trap is repaired as soon as possible."
Steam Trap Monitoring Solutions
Iordanova explains that Armstrong has two solutions for wireless steam trap monitoring, SteamEye® and AIM®. Both systems are non-intrusive and monitor the trap operation with acoustic and temperature readings. Both systems operate on systems ranging from 15 to 1500 psig and are installed upstream from the steam trap. She notes, "The main difference between the two Armstrong solutions is that SteamEye is a proprietary system and AIM is a WirelessHART® system. WirelessHART is an open protocol which is being implemented in plants worldwide and is backed by many manufacturers."
Insulating Lines and Traps
Another important aspect of improving the condensate return system is insulating pipes and traps. High quality insulation should be used, and insulation on traps should be the type that can be removed for inspection or service. A trap monitoring system can still be used on insulated traps. According to Armstrong, only a small area on the trap is needed to attach the sensor, and this can be surrounded by insulation.
Upgrading and maintaining the condensate return system is one of the fastest paybacks possible in improving the efficiency of an industrial steam plant. Managers can start by upgrading inspection and repair schedules for steam traps. A wireless trap monitoring tool makes this job easier. It is also valuable to assure that the return piping systems is as complete as possible, and the system is adequately insulated. Expert help is available for taking all of these steps.
This article originally appeared in the Gas Technology Winter 2015 issue.