Review inventory, assess space and customer needs before making changes.
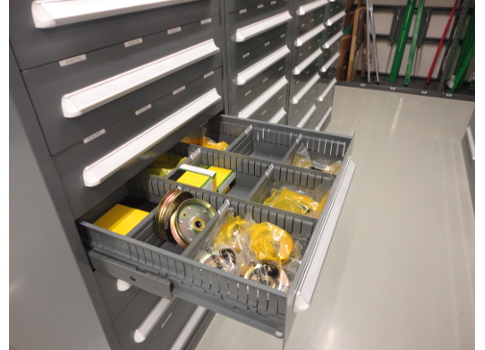
As Premier Equipment Ltd. prepared to move into its new 55,000-sq-ft warehouse in Elmira, Ont., last year, it gave everyone a chance to take a fresh look at how to improve operations. That included the parts crib, which managed everything from a small O-ring to a large combine for the John Deere agricultural and landscaping distributor. "It gave us the chance to start fresh and do things the way we wanted to," said Leon Brubacher, the parts lead at Premier. The Elmira location is the hub for 10 centers throughout the area, which serves an agricultural community growing corn, wheat, and soybeans as well as a thriving landscaping region about 75 miles west of Toronto.
One of the first decisions was to scrap the legacy bin system and replace the bins with drawers and cabinets to store all of the smaller parts. That allowed Premier not just to better organize the space, but to do it in about two-thirds of the footprint of the previous location. "We didn’t want to spend more on square footage than we needed," said Brubacher.
"We found the cabinet route was beneficial as we were consolidating into a smaller space."
By going from smaller bins to deeper drawers and cabinets, they were able to reconfigure not just the space the parts were in, but also the aisles around the parts. "The main change was really that we had a lot more cabinets," Brubacher said. "We purchased 56 cabinets and had the shelving on top of cabinets. The big gain was less aisles. All of our little parts had been in 12-in.-deep bins, and now they were in drawers that were about 30 in. deep. That meant a lot fewer aisles with deeper cabinets. It’s very neat and tidy, less walking."
The logistics of the process is important, because Premier is both a parts distribution and repair center. That means it has both internal and external customers looking for parts. "We have quite a bit of walk-in traffic as well as shipping out to customers," said "Brubacher. "We also have various people picking for own service department. We just get a printout from our business system with the bin number and fill orders."
The company had implemented a new back-end management system in January 2014, so workers had to learn both the new bin system and the new order system at the same time. "I’m glad it’s all behind us," Brubacher said with a small laugh.
Planning is crucial
One key reason the process went relatively smoothly, Brubacher noted, was the emphasis on pre-planning. "We don’t have too many regrets after the move, but it took of planning," he said. "You’ve got to plan aisle widths, bin labeling. It’s easy to just push that out and worry about it later."
And rather than wait for the move to switch from the bin system to the cabinets, Premier decided to start the moving process well before the actual moving day. "A huge things for us, and we’re glad we did it this way, is that we set up all cabinets at the old location and then filled them before the move," he said. "We actually filled all the bins with the parts at the old location. It was a tight squeeze for a while. We had to find room for our existing bins and then fill 56 cabinets. We worked three-quarters of the year having one to two people gradually fill cabinets. Then when moving day came, we just moved all the cabinets in an evening and we were ready to go the next day.
"We were filling orders in the old space, but we had all the new aisles laid out," Brubacher said. "We had the new bin locations even in the old building. The guys learned the bin system and when we got into the new location, it was just in different physical spot."
Know your inventory
An emphasis on planning and understanding inventory levels is critical to the success of a project like Premier’s, said Brent Mitchell, the territory sales manager for Vidmar, which provided the drawers and organization for the Premier project.
"Before you begin, ideally you should have your inventory up to date," said Mitchell. "If 30% to 40% of your inventory is obsolete, you’ve got to clear out the obsolete inventory prior to doing a survey to understand your inventory levels. You need to have a good handle on current inventory." He noted that includes making sure which parts are obsolete. If 30% of motors are obsolete, for example, that’s a much different inventory issue than 30% of screws being obsolete, and calls for a much different inventory system.
It also includes knowing what time of the year or what part of your manufacturing cycle you are measuring. "In the first part of survey, you really need to be to have a good handle on whether these are good inventory levels. If you look at an agricultural dealer like Premier, their inventory level in January is different than May or June."
Tying the cabinet system into a back-end inventory management and ordering system is part of that planning process as well. "The beauty of what Premier Equipment did is to barcode cabinets prior to moving," Mitchell said. "This way you have lots of time well in advance to sort out, organize, and assign bin locations. If you have proper pre-planning like Leon did, there’s no loss of productivity or any inconvenience to the service department or to customers requiring parts. You always know where everything is."
Companies such as Vidmar are consultants as much as equipment providers in the inventory management space. "When I first meet a customer, before I even look at a storage solution, I want to understand his business," Mitchell said. "Does he have a lot of walk-in trade? It’s important when you set up the storage cabinets that the high-volume parts are close to where the customers are."
Mitchell noted that in manufacturing shops, the customer is the maintenance staff and manufacturing line worker. "With the tool crib, you want to have high-volume parts close to the issue area," Mitchell said. "If fasteners are some of the main things maintenance needs, you want to have fastener cabinets as close to the issue area as possible.
"We do a lot of CNC machine shops with a lot of benching and cabinet storage," he added. "We specifically lay out the drawers for machines at the point of use. This system also helps with the 5S programs."
The Bottom Line:
- Whether moving your parts crib from building to building or from place to place, it’s important to plan your move and understand your inventory.
- Such a move is a good time to examine how parts are distributed to internal and external customers, and where new cabinets, drawers, and shelves should be located to ensure efficient distribution.
- A further efficiency is tying any back-end inventory management system into the new parts management process.
Key Words
- Implementing inventory management policy, procedures
Inventory management requires much more than just knowing the numbers. Knowing the relevant formulae is the easy part. Successful inventory management, and the achievement of true inventory optimization, requires a focus on people, policies, procedures, and with that, behaviors. The requirement for improving the management of this interaction is even stronger in a maintenance environment where operations rely on the timely supply of spare parts to minimize the impact of equipment failure and provide efficient maintenance activities.
By Philip Slater
- The long road to maintenance parts-management success
When Dennis Marcucci arrived at Gonnella Frozen Products in 1997 to head the company’s information system department, he already knew the company and its mission. He also knew that the breadmaker needed a fresh approach to its maintenance inventory management system. "I was familiar with what was going on, and in seeing what needed to be done, I knew the road to success was not going to be quick or easy," Marcucci told a seminar at the 2005 Computerized Maintenance Management Summit in Indianapolis in July. "Reducing downtime was the most important issue we faced. We knew we had a parts issue, and there were several attempts at a solution."
Bob Vavra, CFE Media
- A well-run storeroom preserves capital, saves time and money
An inventory that doesn’t have the parts when needed is an indication that the stocking levels are not adequate to support the maintenance requirements to perform the needed repairs. Conducting an annual review of the item stocking level to evaluate the reorder point, minimum and maximum stocking levels, safety stock requirements, and annual item usage provides insight into future stocking requirements to prevent item stock outs. Reviewing stocking levels and monitoring inventory usage reports also identifies obsolete and excess inventory that consumes inventory dollars and robs valuable space in the storeroom.
Wally Wilson, Life Cycle Engineering