To use a flowmeter to its full potential, always focus on knowing the flow application parameters and requirements long before deciding to use one type of flowmeter versus another.
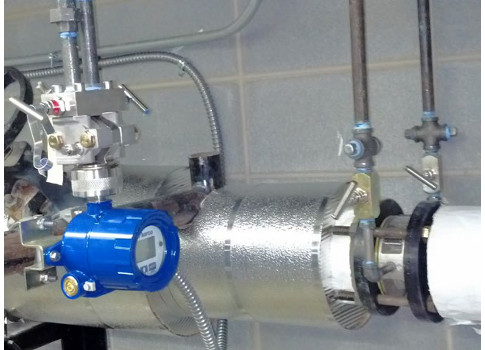
Do the terms Vortex, Magnetic, Differential Pressure, Thermal Mass, Variable Area, Orifice, Coriolis, Ultrasonic or Turbine keep you up at night? If you are in the business of Energy Monitoring and Management, these terms are certainly in your vocabulary when it comes to knowing more about the flow rates of your system or process. These terms also describe the majority of electronic and mechanical based flowmeter sensor types that are available today.
Each sensor type has its strengths and weaknesses, which can be debated. Regardless of the debate, market sector definition, or the sensor technology used, a flowmetering device produces the system data you need to support your fiscal, control, and energy management decisions. All of these sensor types have been developed to meet the needs of customer’s flow application characteristics. Whether that application is water, natural gas, heavy crude oil, steam, liquid nitrogen, air, or many more, it is the “Application” consideration that comes first. There is no perfect flowmeter type that fits all applications and if a company makes that statement, they are selling a product and not a solution.
A solutions-oriented flowmeter company will first understand the flow application completely. Before any flowmeter type is recommended, the fluid type, pipe size, expected flow rates, temperature, and pressures associated with the application must be fully understood. Other application requirements which must be known include: mechanical installation concerns, straight run limitations, a history or familiarity with one type flow sensor over another, and how the flow sensor data will be communicated to the customer. Based upon this complete understanding of the customer’s application, a good flowmeter company will recommend the best sensor type for the job. But sometimes upon careful review of a particular application, it is decided that one of the wide array of flow sensors currently available will not provide the customer with consistent and accurate data from which they can make Energy Monitoring and Management decisions.
When a flowmeter is properly applied for a given application and installed correctly, it generally works as expected year after year. However, when a flowmeter is misapplied it can quickly become the “bad actor” in the plant. So to avoid flowmeter problems, always focus on knowing the flow application parameters and requirements long before deciding to use one type of flowmeter versus another.
Content provided by Spirax Sarco. Originally published in Steam News Volume 5 Issue 1. Edited by Anisa Samarxhiu, Digital Project Manager, CFE Media, [email protected]