A look at hydrogen, from generation to injecting it into gas networks to the role it plays in decarbonizing the steel industry
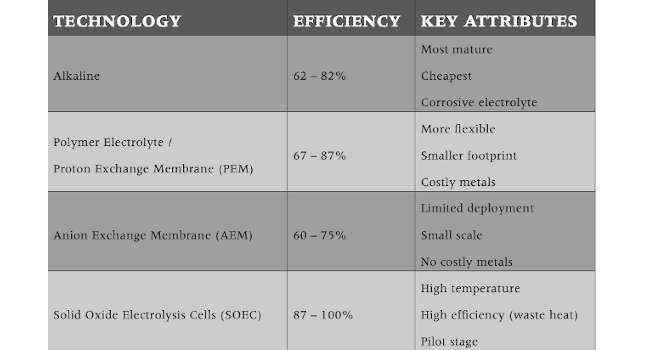
The industrial sector is one of the most difficult parts of the economy to decarbonize, and it’s on track to becoming the largest source of U.S. greenhouse gas (GHG) emissions within the next 10 years, according to a Dec. 2020 report by the Rhodium Group titled “Clean Products Standard: A New Approach to Industrial Decarbonization.”
Emissions from manufacturing comprise more than 60% of total industrial emissions in the U.S. Though manufacturing is a diverse subsector, a majority of emissions come from the production of a small set of GHG-intensive products, including basic chemicals, iron and steel, cement, aluminum, glass and paper. While these products/industries are significant, only steelmaking is covered in this article, which also discusses hydrogen generation and its injection into the natural gas network.
Hydrogen generation
Common hydrogen generation methods include steam methane reforming (SMR), electrolysis and biomass gasification. The most common process is steam methane reforming in which natural gas is converted to hydrogen and carbon dioxide in the presence of steam and a catalyst. More than 95% of the world’s hydrogen is produced from fossil fuel, not only from the SMR process. In this reaction, natural gas is reacted with steam at an elevated temperature to produce carbon monoxide and hydrogen. A subsequent reaction — the water-gas shift reaction — then reacts additional steam with the carbon monoxide to produce additional hydrogen and carbon dioxide.
In his November 2020 presentation titled, “Hydrogen decarbonization in Steel,” Roman Grosman, national business development director at Linde, describes the conventional SMR process as mature efficient and reliable. However, the process produces high carbon emissions — “100% of the CO2 is emitted. But there is potential for carbon capture and storage (CCS), which can produce so-called Blue Hydrogen with reduced carbon intensity. Production of hydrogen in SMR using renewable gas feedstock and ultimately with an Electrolyzer powered by renewable electricity will further reduce Hydrogen carbon intensity to an ultimate net-zero or green status. The above two methods of production are commercially available and are practiced by Linde today.”
Another process is gasification, which converts biomass, coal, natural gas or waxes into a synthesis gas. This gas is primarily composed of hydrogen and carbon monoxide, but also may contain smaller amounts of methane, ethane, propane, ash and tars. “In-well gasification” converts oil and gas inside a well into hydrogen and CO2. The hydrogen floats to the top for extraction; the CO2 stays in the well. Again, it produces zero carbon hydrogen from fossil fuel.
Green pathways. Electrolysis and gasification are the most advanced technologies, but promising research is being carried out on other pathways, according to a presentation titled “Green hydrogen: a way to decarbonize gas networks,” by Nicolas Bombard, project engineer at the Natural Gas Technology Centre (NGTC) in Boucherville, Québec, Canada. This presentation was given at the Technology and Market Assessment Forum (TMAF) Webathon on Feb. 25, 2021.
Electrolysis works by connecting a dc electrical power source to two electrodes placed in an electrolyte solution. This causes hydrogen to appear at the cathode and oxygen at the anode. Electrolysis technologies include alkaline, polymer electrolyte/proton exchange membrane (PEM), anion exchange membrane and solid oxide electrolysis cells (SOEC) (see Table 1) (see Sidebar “UCI and SoCalGas to lead DOE green steel effort”).
Biomass gasification. Gasification was mentioned in the previous subsection, which states the process converts biomass into a synthesis gas or syngas. Syngas is made mainly of H2, CO and CO2, but also some CH4 and water vapor.
The steps in thermal conversion of biomass into syngas include drying, pyrolysis, combustion and reduction. Drying eliminates moisture in the fuel. Pyrolysis is the chemical decomposition of organic materials by heating in absence of oxygen at temperatures from 200°C to 600°C; gases and charcoal are produced. Combustion is the oxidation of the charcoal at high temperature (1,200 to 1,500°C); heat is released (used in the other steps). Reduction is where the combustion products (mainly CO2 and water vapor) react with high temperature carbon (the charcoal) to produce CO and H2.
Other processes are needed after these four steps because syngas is only 30 to 60% H2; the H2 yield depends on the biomass used. A reaction of CO with water in the presence of a catalyst increases H2 yield. This is known as a water-gas shift reaction. Then H2 is separated from the syngas by pressure swing absorption, amine wash, membranes or cryogenic distillation. Other post-treatments instead can be used to make synthetic biomethane (methanation) or biofuels.
Injecting hydrogen into gas networks
Blending hydrogen into the existing natural gas pipeline network has been proposed as a means of increasing the output of renewable energy systems. However, this is easier said than done.
Benefits of injecting H2 into gas networks include:
- “Greening” the gas network
- Decarbonizing parts of the economy
- Storing electricity from intermittent renewable energy sources.
However, doing this could have consequences for the gas networks themselves, some end use cases and safety. Potential issues with H2 injection include:
- Material integrity: under certain conditions, H2 can make steel more brittle, and it can pass through plastics.
- Leakage: H2 is a smaller molecule than methane and leaks easier through joints.
- Combustion: H2 has lower energy content per cubic foot of gas, plus different behavior of hydrogen affects burners; more critical for industrial equipment (narrower tolerances).
- Gas engine/turbine (powerplants/industries): even more sensitive to H2 than combustion equipment.
- Flammability: broader ignition range (4 to 75% in air versus 5 to 15% for natural gas).
- Leak detection: conventional leak detectors are not sensitive to hydrogen. Flame ionization detectors use a hydrogen flame and infrared (IR) laser detectors are specifically tuned to methane, so the leak will be underestimated.
- Other issues: Gas metering (affects billing/different energy content), compressor station, liquefied natural gas (LNG) and underground storage.
Material issues notwithstanding, what would be the ideal blending rate of hydrogen in gas networks? The easy answer is “research is still ongoing and there are lots of knowledge gaps,” according to Bombard. With what is known, modification to the network (pipes) or end-user equipment (burner adjustment, H2-ready equipment) is recommended.
Due to the complexity of natural gas delivery systems, and the wide variety of the components, materials and equipment, it is not possible to specify a limiting hydrogen value that would be valid for all parts of the natural gas infrastructure. Seasonality of gas demand also will have to be considered: If H2 injection is constant, the blending rate will increase when gas flow decreases in summer. Thus, the following things must be considered:
- How to keep the blending rate steady?
- Possible blending rates (general conclusion based on current existing research):
- 1 to 2% hydrogen possible as is.
- Up to 5% with minor modifications.
- Up to 20% with significant modifications.
- Above 20%: major modifications required(complex and costly).
- Not possible to set a universal limit.
- Site specific analysis might be needed.
Despite these issues, blending hydrogen into the existing natural gas pipeline network shows promise toward reducing greenhouse gas (GHG) emissions.
Decarbonization and H2 in steelmaking
In addition to discussing H2 generation methods, Grosman also covered hydrogen decarbonization and H2 in steelmaking in his presentation. He said there are three major routes to reaching net-zero CO2 emissions from steel: Decarbonization technologies, demand management and energy efficiency.
Decarbonization technologies include:
- H2-based direct reduced iron (DRI), H2 blast furnace (BF), electric arc furnace (EAF), H2 reheating
- Scrap-based EAF
- Gas-based DRI (transition fuel)
- Charcoal in BF/basic oxygen furnace (BOF)
- Carbon capture
- Electrolysis of iron.
DRI is the product of the direct reduction of iron ore in the solid state by carbon monoxide and hydrogen derived from natural gas or coal. The process involves the removal of oxygen from iron ore or other iron-bearing materials in the solid state, i.e., without melting, as in a blast furnace. The reducing agents are CO and H2, coming from reformed natural gas, syngas or coal. Iron ore is used mostly in pellet and/or lumpy form.
Demand management efforts involve better scrap recycling, redesigning products for more efficiency and circularity and more intensive use of steel products. Energy efficiency involves using high-pressure leaving the furnace for power and coke dry quenching, according to Grosman.
Steel making and potential H2 demand:
- 100 kg of H2 is estimated to produce 1 metric ton (MT) of hot iron with DRI technology.
- 1 ton of H2 can replace 5 tons of coke.
- If all imported steel — 35 million metric tons (MMT) of steel — is replaced with U.S. production via DRI, demand for H2 would be 3.5 MMT.
- If all steel is produced via DRI in the U.S. in 2040 (120 MMT steel), demand for H2 would be 12 MMT.
- In the near term, DRI in a mix of 30% H2 by energy is feasible.
Decarbonization paths. Grosman also pointed out the DRI-electric arc furnace route is the most commercial-ready path to full decarbonization. But, industrial-scale H2-DRI production will not be possible before 2030. The operating expense increase would be around $75 to $100 per ton.
The blast furnace with H2 injection route is a lower capital expenditure. However, this option is limited to a maximum of 20% decarbonization. A 5 to 10% CO2 reduction results in a $20 per ton operating expense increase. An alternative is to substitute/augment with coke oven gas (COG), syngas or biomass.
Grosman said fuel switching and oxy-fuel combustion for reheat furnaces are incremental yet lower-cost steps to decarbonize. Fuel switching involves either blending or replacing natural gas fuel with H2 while oxy-fuel combustion entails full or partial substitution of combustion air with oxygen. Since H2 is around 10 times the cost of natural gas per MM BTU, combine H2 with oxy-fuel combustion for maximum benefits.
UCI and SoCalGas to lead DOE green steel effort
The U.S. Department of Energy (DOE) has awarded UC Irvine’s Advanced Power and Energy Program $5.7 million to lead efforts to develop manufacturing processes for producing green steel — steel manufactured without greenhouse gas emissions. The collaboration with Italy’s Politecnico di Milano and Laboratorio Energia Ambiente Piacenza (LEAP), U.S. companies FuelCell Energy and Hatch and Southern California Gas (SoCalGas) will employ solid oxide electrolysis cells (SOEC) as a way to decarbonize steel production.
The UCI team is led by Jack Brouwer, mechanical and aerospace engineering professor and APEP director; and Luca Mastropasqua, APEP senior scientist.
The project seeks to prove renewable hydrogen, produced via high-temperature electrolysis using SOEC powered by wind and solar resources, can successfully be integrated into steel manufacturing processes. Researchers will develop the technological basis, build and demonstrate a small-scale prototype unit and study the feasibility of future scale-up and commercialization.
Traditional steel manufacturing plants, known as integrated cycle steel mills, use blast furnaces that employ coke- and coal-derived gases to convert iron ore into metallic iron. Direct reduced iron (DRI) plants, which currently do not exist in the U.S., produce metallic iron from natural iron ore without melting it. The DRI process uses shaft furnaces with temperatures below 1,200°C to chemically strip oxygen from the iron ore — a more energy-efficient approach.
The newly funded three-year project seeks to integrate hydrogen produced through electrolysis — an electrochemical process that uses electricity and heat to split water into hydrogen and oxygen — into the DRI process. In this case, the electrolysis will be powered by wind and solar resources, producing renewable hydrogen. Hydrogen will be used as the reducing gas that strips oxygen from iron ore to form the metallic iron.
“The process we propose uses a high-temperature electrolysis system that can be directly coupled with the high temperatures of the shaft furnace where the iron ore conversion occurs,” Mastropasqua said. Since the only byproduct of the process is water, that water can be used at high temperatures to produce more hydrogen, closing the loop and allowing it to be thermally integrated back into the DRI furnace.
Along with its partners, the UCI team will demonstrate its hydrogen production technology is more efficient and produces lower emissions than current technology. The project will prove steel can be produced with zero greenhouse gas emissions at a cost comparable to current state-of-the-art technologies. Finally, the project will verify that its new process can easily be coupled with other industrial sectors, including transportation, to further reduce greenhouse gas emissions.
FuelCell Energy, a U.S. fuel cell and electrolyzer manufacturer, will build and operate an electrolyzer prototype for the project at its manufacturing site in Danbury, Conn. The prototype is expected to produce approximately 10 kg per day of hydrogen, enough to produce one ton of steel per week.
Hatch, an engineering consulting firm with expertise in novel steel production technologies, will provide a detailed design for the large-scale plant that will use the demonstrated technology while SoCalGas will help with technology transfer.
“We will prove our process results in higher steel production energy efficiency compared to state-of-the-art technology,” Brouwer said. “A blast furnace steel mill uses 11 gigajoules of fuel to produce one ton of steel. We aim to reduce that value to 8 gigajoules/ton, and those 8 gigajoules won’t come from coal anymore, but from sun and wind.”
– This article appeared in the Gas Technology supplement.
More info
Energy Solutions Center
Linde
www.linde.com
Natural Gas Technology Centre
Rhodium Group