In many cases, digital twins can be implemented to help improve asset performance with advanced visualization in a manufacturing setting.
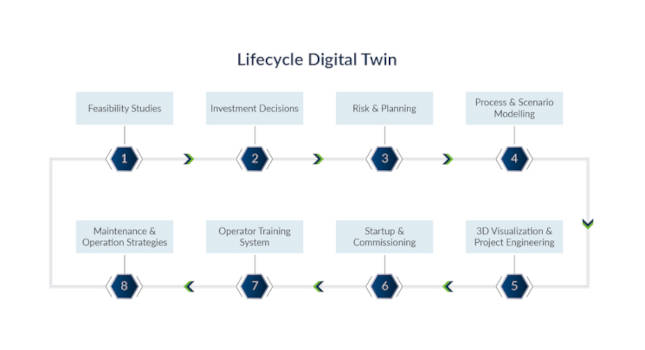
Learning Objectives
- Learn how digital transformation can update the process within asset-intensive industries.
- Understand how a digital twin can improve a plant’s sustainability.
- Review how digital twin models can enhance carbon capture.
Digital twin insights
- Manufacturing facilities that employ a digital twin may achieve more sustainable outcomes.
- Carbon capture, use and storage is a process that captures carbon dioxide emissions from sources like coal-fired power plants and either reuses or stores it so it will not enter the atmosphere.
Most companies fall short of their capital project expectations. The industry is faced with unpredictable market requirements and stakeholders are finding their projects chronically behind schedule or over budget; therefore, seeing missed market opportunities and decreased asset profitability.
Asset-intensive industries are investing in digital technology solutions to create contingency plans, manage execution, optimize construction sequences and prevent budget and material overruns. In addition, they are reviewing assets from a sustainability outlook, garnering support from the public and financial institutes as they promote sustainability in the design and work process to increase energy efficiency while reducing waste and emissions.
To achieve a more effortless execution, the solution method must be simple and frictionless. The common issue facing engineering, procurement and construction (EPC) companies and process industry owners is that the current digital solutions do not focus on the overall project life cycle aspects, necessitating the need for multiple digital technology solutions to achieve sustainability and profitability goals during an asset’s life cycle.
Digital twin technology
The manufacturing industry needs a holistic solution that starts in design and is used throughout start up, commissioning and operations. It can become the cornerstone for the implementation of more digital solutions to support predictive maintenance, spare part inventory, advanced process control and supply chain optimization.
Digital twins provide a solution from a bird’s eye view that’s necessary for different applications and use cases, whether greenfield or brownfield. No matter where in the digital transformation journey a company is, digital twins can easily be implemented to help improve asset performance with advanced visualization. An offline digital twin during the early project phases allows engineers to design the most optimized, lowest capital expenditure process. An online digital twin delivers previously unattainable critical insights to idealize operations while dealing with ever changing environmental regulations.
As the industry pivots to meet their ambitious net-zero targets, the energy transition projects are bringing in new opportunities for technology licensors and EPC firms.
Licensor and EPC firms can help owners secure the benefits from a holistic digital twin model by transferring this digital twin from the feasibility stage to final investment decisions to operations and maintenance.
Life cycle digital twin for carbon capture process
Carbon capture is one of several imminent technologies helping organizations meet their sustainability goals faster as we transition to a decarbonized economy. Leading companies are looking for solutions that can help support tactical, strategic and business decisions through key phases of design and operations.
Organizations supporting greener and newer technologies such as carbon capture, utilization and storage (CCUS) can alleviate growth pains through implementation of a life cycle digital twin. This holistic approach helps with increasing project feasibility and risk mitigation.
A life cycle digital twin can support organizations by providing insights into new technologies and making informed decisions for each phase of the asset life.
Investment decisions​: Technology evaluation takes place during the initial conceptual design of a project to assess potential technologies available for adoption. Based on future energy and renewables prices and emissions targets, an appreciable number of capture technologies are available in the market. Low-carbon hydrogen production is also accelerating momentum toward carbon capture projects. With a diversified mix of available technologies, investors are challenged with evaluating trade-offs between the return on investment and total carbon dioxide (CO2) captured.
Digital solutions help investors look at different system configurations to identify the conditions where risk across the entire CCUS system is minimized including the efficiency gained through scale and integration of system components. In the case of carbon capture employed to achieve low-carbon hydrogen, there are more energy and process efficiencies to be gained.
Risk and planning: Models can provide insights to compare available technology options quickly for technical and economic feasibility, reducing and quantifying the risk associated with capital expenditure ​ investment. In addition, better insights enhance collaboration between investors and other key stakeholders, aiding with informed selection of the best technology to support organizations with their long-term profit and sustainability goals​. For example, amine-based absorption for carbon capture is a mature technology, but it is energy intensive, hence necessitating new solvents innovation to find the balance between energy and capital expenditure investments.
Scenario analysis for conceptual design: Scenario analysis is crucial for exploring possible financial outcomes based on different factors. With the business environment being ever-changing and filled with uncertainty, conducting regular what-if scenario analysis will allow organizations to see how different internal and external inputs might cause business key performance indicators to change. This can help organizations make proactive planning decisions that account for a range of possibilities in design, both positive and negative.
Most projects involve engineers using multiple files to represent various scenarios with topological differences, which requires them to manually change inputs in a series to better understand the system. All these steps are time consuming and error prone.
Process simulator models integrated with economics can help to perform techno-economic evaluation through rigorous modeling of the carbon capture process. Robust process simulators (and associated integrated workflows incorporating safety and layout) help innovate and drive down capital expenditure by up to 20% and operating expenditures by 15%-30%.
In addition, ​offline digital twin models offer agile workflow to quickly run thousands of scenarios in parallel while leveraging high performance computing or better, cloud-based parallel computing, artificial intelligence and visualization tools for data analysis. Scenario analysis can provide early visibility into how design decisions may constrain feedstock selection, environment and climate impact, equipment availability, reliability and maintenance strategies. These early insights into identification of process operation strategies enable stakeholders to make better decisions for profitable and sustainable operations.
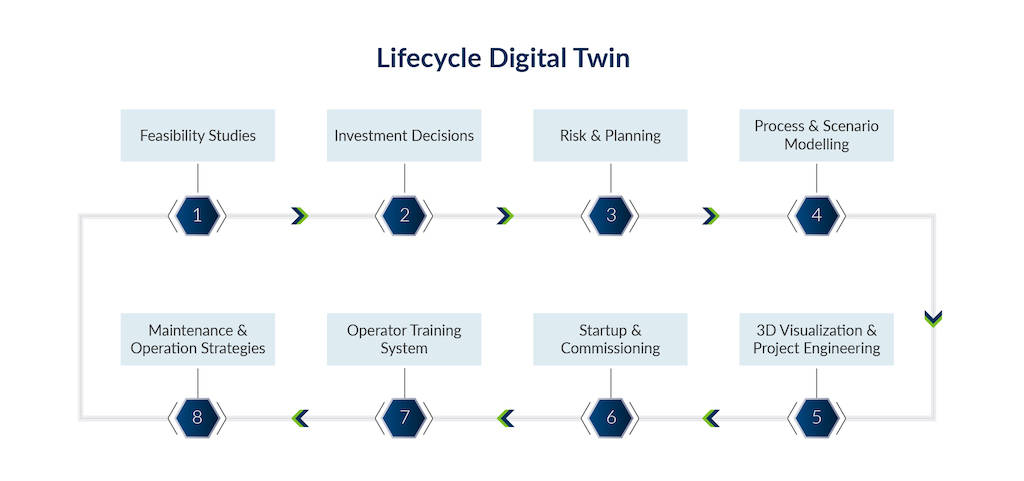
Moving digital twins to 5D
Front-end and detailed design​: Once the technology has been selected and finalized, a robust design becomes essential for seamless startup and operations.
As process decisions made early on lock in capital costs, a collaborative front-end tool that digitalizes front-end engineering deliverables lowers the risks of late design changes through transparency across disciplines, ensuring communication of each change made.
Front-end digital twins let organizations visualize five dimensions (5D) of the project early in the design phases. Early visibility into 3D layout plus cost and schedule at design stages allows organizations to make informed decisions to improve sustainable outcomes, avoid project risks and estimate the impact of proposed changes in the design. This visibility can be obtained through conceptual layout, conceptual cost and schedule modeling. These early insights prevent and mitigate change orders and project overruns, hence eliminating financial risk associated with upcoming high value sustainability projects.
Eliminating the delays early in the design have helped companies accelerate the project duration by nearly 20%. In addition, 5D visibility with front-end digital twins have helped organizations select the design concepts 87% faster.
Startup and commissioning​: ​ During start up and commissioning, already prepared robust digital twin models validate the process control system and the operating guidelines, enabling faster operator training. Running a digital replica in parallel with the actual plant operation creates a valuable means of training operators and technicians to familiarize them with the control schemes and processes in an offline and risk-free environment before startup. Hence, the operations team is better equipped to successfully control any process upsets or abnormal operational situations by rehearsing such events. For newer, complex processes such as both point source and direct air capture technologies for carbon capture, which have fewer than 30 operating facilities, proficient training and expertise is crucial in creating a risk-free environment.
Operator training system: With the industry struggling to attract talent and much of the experienced workforce heading to retirement, ensuring operators can practice in the safety of an office environment or remotely if they choose, is essential to reducing risk, enhancing production and attracting a new generation of skilled workers. Furthermore, adding technologies such as carbon capture require experienced operators to revise and update their training.
Companies are also looking for dynamic ways to train their employees quickly and efficiently. Software simulator based digital twins have been expanded into using augmented and virtual reality to speed up learning through an immersive and scenario-based virtual environment. Operators can perform multiple scenarios in a simulation environment, which mimics high-stress conditions and allows for object recognition. In addition to helping companies close the talent gap, advanced technology and digital twins allow for a seamless approach to reducing training costs and mitigating operator-driven risks.
Ongoing plant operations and maintenance
Operations and maintenance​: Once the plant is operational, the accuracy of the digital twin can be continuously enhanced with plant data taken directly from the process as it becomes available. This real-time online digital twin model provides critical insights into operations for continuous monitoring of equipment and increased plant performance. Greater insights into equipment health supports operations to avoid risks associated with unscheduled downtime.
In addition, online digital twin models can be used to optimize process control targets to maximize captured CO2 while minimizing energy consumption to reduce total capture costs based on the current process inputs.
Capital project success is critical to keeping companies competitive and profitable, especially during trends of market instability or volatility. Digitalization is the key to meeting these business goals, making new and sustainable technologies easily accessible and cost friendly. Using digital twins from feasibility to operations organizations can align quickly on goals of sustainability and operational excellence while reducing risks to production.
Digital twin is more than just a visual, virtual representation of process, operation or system. It is an approach that aligns with the industry need to enable collaboration, transparency and improvements across an asset’s life cycle.
A life cycle digital twin then becomes a holistic solution for new and sustainable technologies, including but not limited to carbon capture, hydrogen, biofuels, bio-feedstocks and process improvements associated with circular economy.