Real-time data provides business insights into sustainability and digital transformation gains in three key areas and can help companies realize their goals.
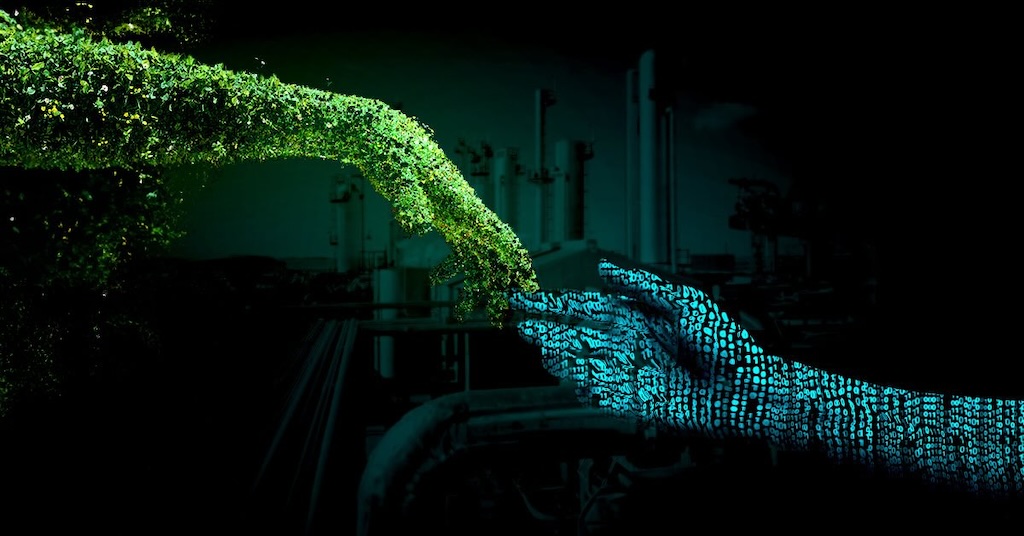
Learning Objectives
- Learn how manufacturers are striving to evolve and become more efficient.
- Learn how big data can help companies be more sustainable and achieve digital transformation.
- Learn how energy management, waste management and regulatory compliance can help manufacturers be more sustainable and efficient.
Sustainability insights
- Technological advancements enable manufacturers to innovate, meeting consumer needs, yet the unintended consequences demand a balance for sustainability and innovation.
- Leveraging big data through digital transformation helps manufacturers optimize energy, reduce waste, ensure compliance, and achieve sustainable operations.
Technological advancements have evolved at a rapid pace, enabling manufacturers to innovate and change operational processes to satisfy consumer demand for new products that enable how people live and communicate. In turn, society has fully realized the potential benefits these advancements provide thanks to manufacturers’ innovation and investment. From mass production of automobiles to personal cell phones and customized medicines, manufacturing has changed the world by making modern products affordable, safe and available to consumers.
It is hard to imagine modern daily life without the foundational products and services provided by the manufacturing community. However, over time, the success manufacturers have achieved in delivering these desired commodities to consumers also has come with the unintended consequences of long-term production, including a higher level of waste, more demand for resources and increased carbon emissions.
A real-world example is the “pop top,” an invention of the early 1960s. An aluminum tab was developed so people could easily pop open canned beverages without a can opener or “church key.” They could detach and discard the tab. The pop-top can was pervasive on into the 1970s, but by then, the aluminum tabs were being discarded on beaches and in other community areas, which created a litter problem and safety concerns. Not only could people “step on a pop top” and cut their heel as Jimmy Buffett said in his song “Margaritaville,” but they also faced a more serious medical issue. Consumers would sometimes push the loose tab back into the can and inadvertently swallow it. Innovators and manufacturers stepped in to change the mechanism used to open canned beverages. They developed the “Sta-Tab,” a safe opening device that remains attached to a recyclable can after opening.
Technological advancements are great, but no one wants to harm people or the environment in the production process. That is not the kind of change manufacturers set out to make in the world. When a company first sets up production, personnel safety and environmental impact are top of mind.
The processes are defined and constrained based on current industry knowledge, best practices and available technologies. For example, a plant or mill built in the 1970s does not have the same technological advantages of a modern-day greenfield plant. However, it still must continue to operate and meet production goals.
Balancing sustainability and production strategies can be a tall order for manufacturing facilities that were not initially designed nor equipped to support a circular economy. Modern digital transformation (DX) solutions enable these companies to strike a delicate balance by harnessing the power of big data to achieve environmental, social and governance (ESG) initiatives.

Three ways to harness the power of big data
In this era of smart manufacturing, the accessibility and visualization of complex data supports integrated production and sustainability planning. The convergence of information technology (IT) and operational technology (OT) allows access to real-time process and enterprise data, prompting new business insights and revealing opportunities for sustainability gains in three key areas: Energy management, waste management and regulatory compliance.
1. Energy management
A knowledge-driven management strategy is a big step along the path to net zero emissions. Viewing operational data and how it relates to energy and resource data provides valuable energy efficiency insights. Aligning process control with energy consumption information will reveal areas with higher or lower usage of resources like steam, electricity and water. With data available down to the machine level, analyses can be conducted by asset, product or process. System modifications can be implemented to automate optimization procedures to streamline energy use based on real-time control parameters. Using advanced tools such as model predictive control (MPC) also allows operators to see resource usage and tighten up parameters or make necessary adjustments to save energy or reduce waste.
2. Waste management
Using the digital thread early in the design and development phases can help manufacturers bring new products to market with less production waste and lower anticipated consumer waste. Digital twin technology enables manufacturers to design products that are environmentally friendly and profitable. Digital twinning shows the virtual product and processes, helping to identify and correct environmental impact issues and other problem areas before production ever begins. Artificial intelligence (AI) technology also enables the control system to learn about the process and adjust during continuous operation. This saves resources, reduces waste and supports optimization. In the same way, machine learning (ML) technology helps machines learn how to be more efficient over time, using less energy or producing less waste.
3. Regulatory compliance
DX provides the right data to the right people at the right time across the enterprise, supporting faster, more accurate emissions reporting. The intelligence derived from the overlay of production and emissions data will reduce non-compliance risks by indicating areas with potential compliance gaps so corrective action can be taken quickly. Using real-time data ensures compliance information is always up to date and accessible. Required reports can be automated using verified traceable data to lower the risk of non-compliance. As regulations become more complex and pervasive, programming compliance parameters into the system will help companies keep up with compliance reporting and required procedures. It also frees operators so they can perform higher level knowledge-based tasks.
Manufacturers have always wrestled with the complicated engineering and operational challenges of reaching compliance and productivity. Companies must digitally transform operations now to meet customer demands for personalized and recyclable products while becoming more sustainable for the future.