Measure the problem, then set out on a repair journey
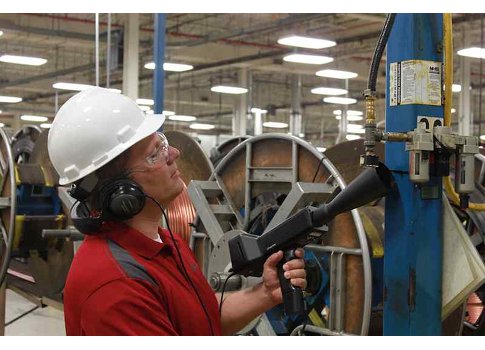
With increasing market expectations associated with energy efficiency and sustainability, most corporate business reviews include a summary of energy conservation projects and performance. When the decision is made to identify additional savings opportunities, fixing compressed air leaks is flagged as an opportunity to deliver savings quickly with minimal investment.
The desire to eliminate air leaks is echoed in discussions with customer focus groups and market research projects that seek to identify unmet needs of the industrial consumer. If it is generally accepted that compressed air leaks are a waste of money and easily repaired, why do they still exist?
As an organization with dedicated engineering resources focused on the assessment of compressed air systems to help customers improve efficiency, reliability and productivity, compressed air leaks are a routine topic of discussion among assessment engineers and compressed air users. Working with customers in North America, Ingersoll Rand developed a new leak assessment service-offering designed to help industrial customers manage air leaks more effectively.
As part of an ongoing effort to iteratively advance the efficiency and effectiveness of our leak assessment program, data from every recorded leak is collected and compiled in a central database. After collecting data from several hundred leak assessments, an analysis of thousands of recorded leaks identified trends and opportunities in the battle against compressed air leaks. These results are segmented into two areas—recorded leaks and the process of leak repair.
Identifying common leak locations
The data analysis revealed the majority of leaks—by volume and frequency—occur at the point of use, as illustrated in the Pareto chart (Fig. 1).
As shown in Fig. 1, the filter-regulator-lubricator (FRL) is the largest culprit of compressed air leaks, closely followed by the threaded joints along pipe drops and connections to pneumatic equipment. The point-of-use valves used to control actuation of single or multiple pneumatic devices is a close third.
On average, these three leak categories represent over 80% of the leaks identified in an industrial facility. The quick-disconnect type fittings, push-lock tube fittings, and hose/tube leaks are considered by many to be the most common components prone to leaks. They are identified as unique leak types segmented in the data. Contrary to common belief, these three applications combined represent only 16% of all identified leaks.
It is important to note that the analysis is based on data recorded and observed during leak assessments. The data does not differentiate between recurring leaks that are repaired frequently from a leak that has grown over time. Any application located very close to an operator has an increased probability of being identified and repaired. Therefore, the recorded data suggests that FRLs, control valves, and point-of-use threaded joints represent the largest source of leak repair opportunities that are not addressed.
Technicians use ultrasonic leak detection equipment to estimate leak volumes during assessments. To deliver consistent results, technicians train to use a standard process and tools. Technicians record the pressure at each location and utilize it to calculate leak volume with improved accuracy over more common methods that assume a constant pressure for all locations.
The data was compiled and summarized graphically in Figs. 2-4 by leak category, and then segmented according to leak volume and weighted frequency of occurrence.
According to the recorded data in Figs. 2-4, the average leak volume is 3 scfm for all leak categories. This implies there is no advantage to targeting one type of leak in hopes of delivering improved results relative to the number of leaks repaired. The number of leaks less than 1 scfm is very low, but this is influenced by the leak assessment process.
The cost to repair a small leak can exceed the savings potential beyond a site-specific financial threshold. Consequently, the majority of customers chose to not record these smaller leaks during the leak assessment. Another issue is being able to physically detect the leak. When a leak is less than 1 scfm, it is difficult for maintenance personnel to feel the leak and isolate the area that needs repair. There is no value in identifying and tagging leaks that will not be repaired.
Prioritizing leak repairs
To be efficient, leaks scheduled for repair should be prioritized by measured volume and ease of repair. This prioritization delivers the best return on time and effort. Referencing Figs. 2-4, the number of leaks larger than 6 scfm for all categories is very low, but this can be attributed to two influences: larger leaks are more audible, increasing awareness and accountability to repair the obvious energy waste; and as a leak increases in volume, so does its potential to negatively influence the application. As a result, many larger leaks are repaired to correct a performance issue, not to deliver energy savings.
Pareto law, often referred to as the 80/20 rule, is frequently quoted in regard to compressed air leaks. The assumption states that 80% of the total volume of air being wasted through leaks can be eliminated by repairing 20% of the identified leaks. The recorded data suggests that leaks do not adhere to this assumption.
To provide a simple prioritized summary of leaks from each assessment, recorded leaks are sorted by volume and summarized graphically using a Pareto chart. The data compiled by individual leak assessment and total recorded leaks for all assessments consistently follow an 80/70 relationship, where 80% of the total volume can be eliminated by repairing 70% of the leaks. This is very different from the 80/20 assumption that many follow.
As the summary of leak categories in Fig. 1 illustrates, almost half of all leaks could be reduced by implementing an FRL maintenance program. Considering most facilities use standard FRL models and sizes across an entire facility, a maintenance technician equipped with several repair kits and replacement filter elements could easily fix a large number of leaks while simultaneously minimizing pressure variance and losses at each FRL station. This can be accomplished by segmenting FRLs by location or application, then scheduling annual filter replacements and leak inspections. Valves and threaded joints adjacent to the FRL should be included as part of the annual FRL preventive maintenance.
Using a SMART process to repair leaks
It is common to have a disassociation between desired results and the interpretation of cascaded actions executed in industrial facilities. For example, most facilities want to save money by eliminating or minimizing the energy consumption associated with compressed air leaks. In order to achieve this goal, most facilities will invest in an ultrasonic leak detection tool maintenance personnel can use to locate and tag compressed air leaks.
Some organizations will contract an outside service organization to perform a leak survey to identify and tag all of the leaks. However, placing a tag on a leak has no impact on the monthly utility bill. Energy savings cannot be realized until field-level actions are aligned with the desired results. In this situation, finding all of the leaks becomes the interpreted objective, with leak repair an assumed result. It is important to note that identified leaks must be converted to a reduction in compressed air demand with a measurable decrease in compressor supply energy to produce energy savings.
Industrial facilities should employ the SMART planning process to achieve energy conservation from compressed air leaks. SMART is an acronym used by many organizations to create objectives with a high probability of success. A SMART objective should be:
- Specific
- Measureable
- Agreed-upon
- Realistic
- Time-bound.
Whether the intention is to develop an ongoing leak management program or attack leaks as a specific project, incorporating these SMART attributes will help ensure efforts are converted into desired results.
Setting specific objectives
Every successful project starts by setting specific expectations and desired outcomes. Defining specific goals at the beginning of the leak management process will help ensure other aspects of the project deliver desired results. To achieve energy conservation and monetary savings associated with fixing leaks, it is imperative that the project specifically state the desired outcome.
If leadership assigns a formal goal to reduce energy consumption, the project scope must state “to reduce a targeted amount of air compressor energy consumption by repairing compressed air leaks.”
Measuring the impact on energy savings
Accurately defining how progress is measured has a significant impact on energy conservation and final results. Most efforts to manage or minimize compressed air leaks fail or deliver marginal results because of insufficient details regarding how progress and results will be measured and documented up front.
Depending on the significance of the compressed air savings relative to the facility’s total monthly energy consumption, the most basic measurement is based on the change in the monthly electrical bill. For many systems, energy savings from repaired leaks are only a fraction of a percent of total facility power, making it difficult to pinpoint a change in energy consumption directly attributed to leaks.
Conducting a leak assessment that provides a prioritized leak list, sorted by leak volume, introduces another level of accuracy. Using the prioritized list, maintenance personnel can focus on the larger, most accessible leaks first, and then work their way down the list until achieving the desired reduction in air volume. This facilitates more efficient use of maintenance personnel since they do not waste time hunting all leaks.
A leak assessment process that incorporates a before-and-after measurement of repaired leaks validates that leaks are repaired properly and compressed air demand is reduced.
The level of accuracy relative to hard savings increases with the measurement detail. Since the objective is energy conservation, another option is to measure compressor operation before and after leak repair. This can be accomplished with online/offline compressors by simply recording loaded, unloaded, and running hours per week for several weeks before and after repairing leaks. A reduction in loaded hours represents energy conserved. To improve the accuracy of energy reduction results, conduct a non-intrusive compressor assessment and summary of compressed air and energy consumption before and after leak repair. Many organizations provide simple compressor energy assessments for a reasonable cost or include it within their contractual service agreements.
Ideally, leak repair should be part of an ongoing effort to sustain and improve compressed air system efficiency, not a periodic event. To maintain operating efficiency, a facility must have sufficient instrumentation and trended data to establish a baseline associated with compressed air demand and energy consumption.
Expectations can be defined based on established performance metrics or performance indicators. This level of detail includes kW, flow, and pressure instrumentation for the compressed air system, and the ability to summarize and analyze system performance.
Some systems trend flow data at the sub-header or production cell level, so total leak volumes can be pinpointed for specific areas. This level of detail is limited to facilities with resources committed to operational excellence and best-in-class performance. For most systems, instrumentation is limited to hours and pressure from the compressor control panel and an assortment of pressure gauges of varying quality. A plethora of measurement methods can be applied with level of accuracy being a function of complexity and cost.
It is important to note that a reduction in compressed air demand can only influence compressed air power consumption. The largest error made when attacking leaks is assuming that a system consumes 0.18kW/scfm and every 100 scfm of leaks repaired will reduce power 18kW. Depending on the installed compressors and how they operate as a system relative to production demands, actual savings can be very different. There are many examples where savings can vary from several times greater to no savings at all. In some operating conditions, repairing leaks can actually increase energy consumption. This is a more complex issue potentially presented in a future article.
Armed with an increased understanding of how compressed air demand reduction and saving energy are related, repairing compressed air leaks can be part of an inferred energy savings project or an investment grade project. If there is no requirement to validate savings or directly impact the budget, then inferred savings is the easiest project.
Many large corporations are only looking at rolling averages based on total annual energy across several hundred facilities. For these situations, simplicity and cost to execute are more important than validated results. This is a reasonable approach for projects that do not require capital expenditure and are expected to deliver small returns relative to total consumption. If this is the case, the easiest measurement plan is based on number of leaks repaired.
Leveraging the statistical data provided and a simple 0.18kW/scfm conversion, every leaking FRL repaired represents a 3 scfm reduction and an annual savings of 540 kWh/1,000 hours of operation. Using an electrical rate of $0.10/kWh and a 6,000-hour year, each FRL leak repair infers a $324 savings. A measurement plan for this project could be a simple list indicating location, type of leak repaired, and how the repair was made.
Agreeing on goals
It is essential to get everyone who is involved with a leak repair project—and their direct supervisors and other company leaders—in agreement with the expectations and measurement process, in order for the project to be successful.
Many repair efforts never go beyond the leak identification stage because maintenance leaders are not accountable for—or aligned with—the project goals. Consequently, they will reallocate maintenance resources for other issues, potentially abandoning leak repair expectations over time. It is just as important to be aligned with production leaders, since many leaks require access to production areas and may require downtime to repair.
Identifying realistic goals
Engaging team members who are familiar with the facility and knowledgeable about its compressed air use will help to ensure set goals are realistic. Consulting with someone knowledgeable about the installed compressors and their control configurations will help to determine if energy savings goals and measurement plans are realistic.
Setting time-bound repair goals
Without setting project milestones and completion dates, it is easy for resources to get engaged and committed to other projects. Fixing leaks is not exciting, and any excuse is a good enough reason to put the task aside. Pick a date, allocate the time, and get it done.
Addressing leaks during routine maintenance activities
There is no magic solution to rid an industrial facility of compressed air leaks, but an increased understanding of leaks and a proven process to address them will help deliver energy savings. If addressing leaks is part of routine maintenance without a need to deliver visible energy savings, the statistical data will assist in setting simple goals with the greatest potential return.
When leak mitigating actions must deliver hard savings, following the SMART steps will help ensure desired results can be achieved and validated.
Mark Krisa is Director, Global Services Solutions for Ingersoll Rand