Sustainability remains a hot topic in manufacturing throughout, but what does it mean for plant automation and how does it affect operations?
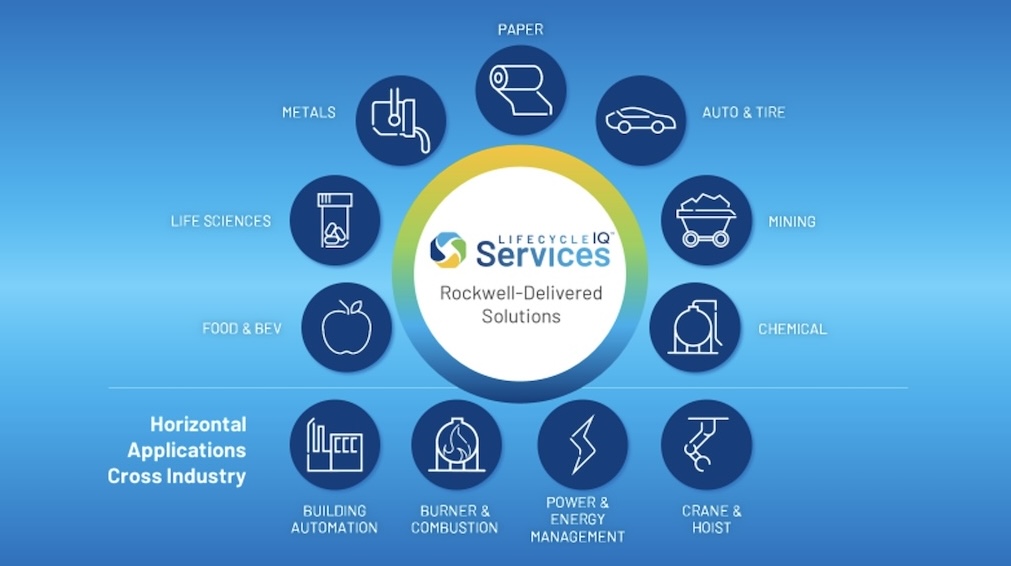
Respondents
- Mithun Nagabhairava, senior manager, data science and AI, Kalypso, Austin, Tex.
- Daniel Pender, global manager, markets and strategy, Rockwell Automation, Milwaukee
- Joe Wagner, MS, field application engineer, Red Lion, Sacramento
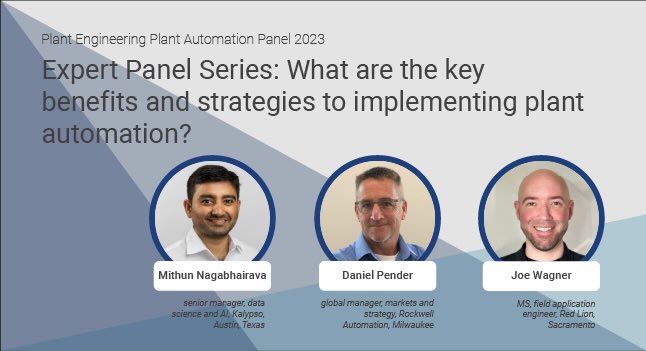
Daniel Pender, global manager, markets and strategy, Rockwell Automation, Milwaukee
Joe Wagner, MS, field application engineer, Red Lion, Sacramento. Courtesy: Kalypso, Rockwell Automation, Red Lion
Question: What are the key benefits of implementing automation in a manufacturing or production plant from a sustainability standpoint?
Mithun Nagabhairava: The benefits of implementing automation and digital capabilities in a manufacturing plant from a sustainability standpoint are significant. Manufacturers are increasingly focused on expanding smart metering infrastructure and empowering their teams with energy management capabilities. To enhance the value further, there is tremendous untapped potential in leveraging automation and AI/ML capabilities to achieve energy optimization capabilities.
In the manufacturing settings, advanced algorithms can help to determine the optimal decisions to effectively optimize energy usage, lower peak demands, and reduce costs while maximizing the overall throughput of the manufacturing processes. Additionally, they proactively identify and address equipment cycling issues through energy signature analysis, extending the lifespan and reducing maintenance requirements of equipment. This holistic approach not only improves sustainability but also drives efficiency and cost savings in manufacturing processes.
Daniel Pender: Automation enables companies to move toward more sustainable operations because of its ability to track and reduce their energy, water, and waste. Producers and operators can benefit from working with a partner, like Rockwell Automation, who can help drive energy reduction through implementation of intelligent, natively integrated variable frequency drives (VFDs) to EPA-approved soft-sensor continuous emissions monitoring (CEMs). Energy monitoring and management systems are an important first step to safely realize sustainability objectives.
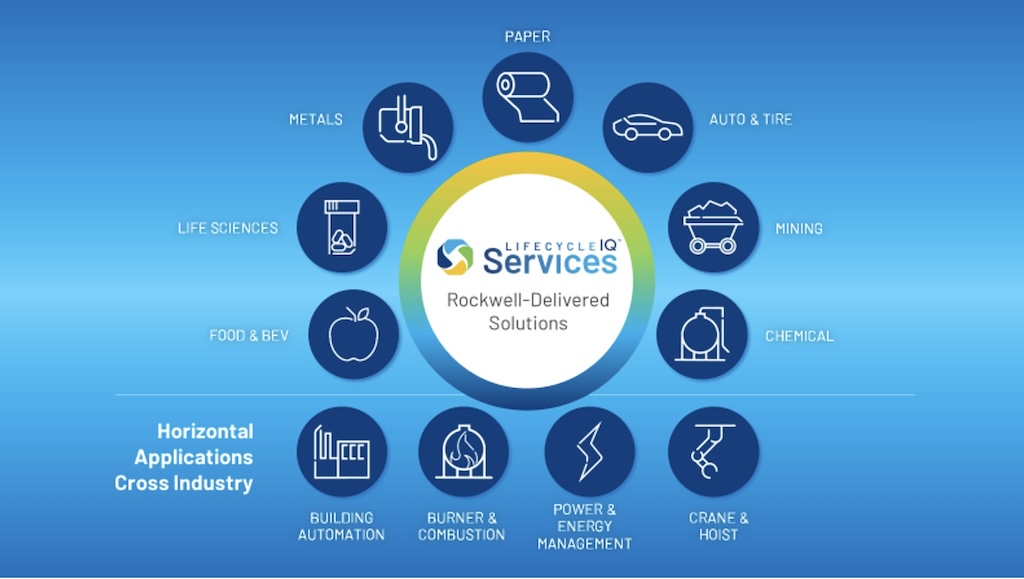
Question: How can automation technologies support sustainability and environmental initiatives within a manufacturing plant?
Joe Wagner: Automation technologies can support sustainability and environmental initiatives within a manufacturing plant in many ways, with one of the most powerful ways being potential increases efficiency. Automation technology typically involves data logging and analyzing historical data which can be used for all kinds of system improvements and even automatic real-time adjustments that increase efficiency. These efficiency gains can sometimes be realized in ways such as lowering scrap rates and reducing the raw materials needed for a process, making an entire process more sustainable while simultaneously reducing waste. As users continue to adopt advanced automation technologies and harness the power of their own data, these efficiency gains are likely to continue.
Question: What are some successful case studies or examples of plants that have effectively leveraged automation for sustainability improvements? Describe the challenge and solution.
Daniel Pender: Our customers have benefited in many ways to become more sustainable via automation projects. We partnered with a California recycled water provider to apply TuneAI to Aeration Basin operations to reduce required treatment chemicals and process air for a daily 2,500 kW reduction, or 50% reduction in energy costs. Similarly, a leading global tire manufacturer, implemented e-mobility capabilities to optimize transportation and handling systems to enable a 50-ton reduction of carbon emissions. This supports their zero-emissions goal. Properly implemented automation provides direct positive impacts to a variety of sustainability metrics. Better process control results in a reduction of scrap and waste, consumed energy, water, and emissions.