Warehouse, manufacturing and logistics facilities need engineering experts to specify various systems
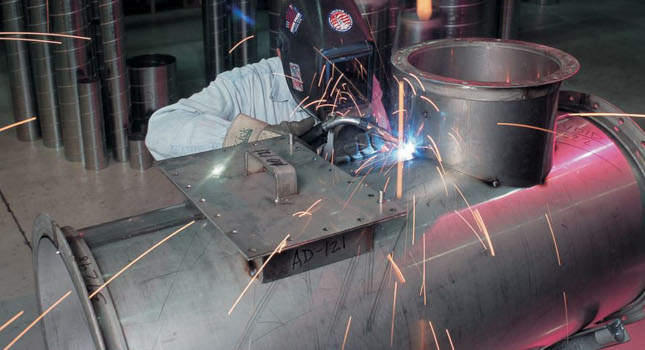
Respondents:
- Jarron Gass, PE, CFPS, Fire Protection Discipline Leader, CDM Smith, Pittsburgh
- Mike Morder, PE, CPD, Design Engineer II, Southland Industries, Dulles, Va.
- Bryce Vandas, PE, Mechanical Group Lead, CRB, St. Louis
- John Gregory Williams, PE, CEng, Vice President – Design Studio, Harris, Oakland, Calif.
What’s the current trend in warehouse, manufacturing and logistics facilities?Â
Jarron Gass:Â Automation is the largest trend I am seeing at the moment, particularly for order fulfillment.Â
Bryce Vandas: The industry is moving toward denser automated storage facilities and warehousing. Removing the need for manual storage and retrieval allows the warehouse space to be used to its maximum capacity. This is reducing the space allowed for the mechanical, electrical and plumbing disciplines to install heating, ventilation and air conditioning systems coordinated with lighting, fire protection and plumbing designs. It also reduces the space allowed for maintenance access to these warehouses causing the design engineers to focus on not only the operation of the system, but how it is potentially serviced if needed in the future. The denser racking will also inhibit airflow causing a need for higher air change rates and wider spread distribution to guarantee full temperature uniformity.Â
John Gregory Williams: We have seen an increase of potential work in this sector. Â
What future trends should engineers and designers expect for such projects?Â
Bryce Vandas: The move toward denser storage facilities opens up a few different obstacles for the engineering team to overcome. The first is general routing. The space for routing ductwork, plumbing, fire protection and lighting is becoming increasingly squeezed. This combined with more robust HVAC requirements leads to the need for more coordination where previously warehouses could have been generally open spaces. HVAC systems meeting temperature uniformity through a warehouse are now requiring new and creative approaches to air distribution. Computational fluid dynamics modeling of warehouse spaces to accurately predict the flow of air through racking is becoming key to guaranteeing a suitable storage facility.Â
Jarron Gass: Anticipating the cost benefit analysis of square footage (area) versus cubic footage (volume) when assessing best solutions.Â
John Gregory Williams: These projects are increasingly faster track. Â
With the boom of fulfillment and logistics facilities due to COVID-19, what can engineers expect for future buildings?Â
John Gregory Williams: We’re finding that for speed of construction — lightweight, often existing tilt–up superstructures — are the norm. With that, limited equipment or heavy distribution equipment can be placed on or supported from the roof. Â
Bryce Vandas: Future facilities will have to identify up front what their strategy will be in regard to fulfillment and logistics. Some companies will maintain on-site facilities, while others will move toward off-site or rental spaces. The engineers will have to stay flexible with their approach. COVID-19 facilities have exposed a need for large refrigerated or freezer storage areas that weren’t readily available. This wasn’t completely apparent up front and a lot of facilities had to be adjusted midstream to meet this need. Understanding the approach to this and what the product needs either long term or short term until it can be shipped to an off-site location are crucial to the success of a project.Â
Tell us about a recent project you’ve worked on that’s innovative, large-scale or otherwise noteworthy. Â
Mike Morder: On a recent project for a confidential consumer goods manufacturer, we implemented many innovations to deliver the overall best value for the client, taking into consideration first cost, life cycle costs and maintenance. I was responsible for the utility piping, ductwork and overseeing the fire protection systems and this project was integrated delivery with the process piping partner. We used multisystem, or multitrade, pipe racks that integrated into the building access and structure. Â
The racks were made from wide flange structural steel beams and shipped to our fabrication shop to be populated with piping. We also integrated walkable mezzanine for access to valves and equipment that would be placed after the racks were hung. Incorporating multitrade racks on this project was critical to getting the systems up and running for production and was a significant effort involving the structural engineer, trade partners, the plumbing engineer, mechanical engineer, fire protection engineer and process piping engineer. The racks were delivered in sections as large as one single column bay, lifted into place in under working day and included access areas on either end to allow crews to perform the interconnection work. As innovative and multidisciplinary this strategy was on this project, the IPD team continued to drive innovation on a subsequent project by creating racks that were double and triple the length of the original multitrade racks. We optimized the overall structure to be more modular for future expansion by decoupling the structural steel and using a modular piping support system. This involved a close relationship with the support manufacturer, their in-house engineering, the structural engineer, contractors and piping engineers. This iteration allowed for a safer installation and allowed the team to streamline the project by reducing schedule durations and modularizing to allow for repetition in the field.Â
Bryce Vandas: Project delivery has been constantly updated to meet recent COVID vaccine manufacturing demands. Designing manufacturing facilities to be as flexible as possible to get a head start on whatever requirements the COVID vaccines may have needed. At the time when many of these projects were getting underway, nobody knew storage or formulation needs. General guidelines for past vaccines were used as a basis to get started and the design teams had to be agile along the way to adapt their facilities. Low–temperature processing in storage means low humidity in filling rooms, which can change the overall approach of an HVAC scheme. Â
How is the growth of immediate-delivery services impacting warehouse and logistics facility projects?Â
Jarron Gass: The need/demand seems to be increasing faster in this segment than simple stock replenishment for traditional brick and mortar and identifying when or how to modify existing space versus adding additional space to meet this need in both a timely and cost-efficient way has been challenge.Â
John Gregory Williams: We’ve been involved in a project recently for healthy home-prep meal delivery. This market is growing with the ongoing pandemic. Though similar to other food preparation and packing facilities, the clients are less knowledgeable around construction and they need more assistance in understanding what their requirements may be to ensure a successful delivery. Â
Bryce Vandas: Working primarily in pharmaceutical and food facilities, the immediate-delivery service has not been an issue. The delivery methods in these industries have not been changed because of the consumer need for expediency. Storage, product staging, dock number and locations, access and other considerations have been optimized to meet client specific needs, but this is based mostly on business goals and metrics rather than consumer need.Â
What are professionals doing to ensure such projects meet challenges associated with emerging technologies?Â
Bryce Vandas: Approaches to meeting the challenges can vary wildly, specifically in pharmaceutical manufacturing plants. It’s important for the engineer to understand the needs of the client and the facility. A lot of new technology is great and can be used immediately. Some new technologies require a give–and–take approach. You have to be sure that you are not compromising part of your facility or operations to use these new technologies. This requires an engineer to dive into the details and make sure everything is understood before making a recommendation or specifying anything new for a facility. Â
Jarron Gass: From a fire protection perspective, it is encouraging to see the continued investment in research to try and keep up with the ever-changing built environment that continues to emerge around us. It seems that every time an acceptable protection scheme is developed, the envelope once again gets pushed into a new nonstandard situation. Research, combined with the computer-based fire and smoke modeling is helping to speed up the overall development process and decreasing the frequency and cost of performing full-scale fire testing to validate theories. Â
In what ways are you working with information technology experts to meet the needs and goals of a warehouse, manufacturing or logistics facility?Â
Bryce Vandas: In many cases, the owner has specific IT requirements and their internal groups will provide the purchase and install. It is key to understand whether the client plans to self-perform this work. It can affect design and overall construction schedules and needs to be incorporated into the bigger picture. When the client does not have this capability, it falls to the engineer to understand the needs of the client. Working with their preferred system vendor to make sure they are comfortable with approaches to security and access control, information transfer, operator work stations, general building automation system controls, etc. In some cases, the owner will have no preference and it will fall on the engineering team to make recommendations and stand behind them.Â
Describe a high-tech industrial manufacturing facility project. What were its unique demands and how did you achieve them?Â
Bryce Vandas: In a recent manufacturing project, there were multiple vial filling lines. These lines required product segregation. The nature of the project required higher air change rates, as well as active space pressurization. Waste streams also required segregation and treatment processes. All the while, the energy consumption and recovery had to be designed such that it could satisfy the latest energy codes. Conservation of energy can be difficult in a facility like this where the process space requires a high level of use. The design team had to be creative about water usage as well as overall utility energy consumption to maximize reuse and to appropriately redistribute that energy elsewhere in the plant.Â
John Gregory Williams: We have been working on a number of confidential projects in the advanced manufacturing area. One of the challenges we are constantly up against is the advancing technologies of the manufacturing processes themselves to deliver a new mechanical system. The selection of the equipment and machinery is generally happening in real time as the needs for heating, cooling, ventilation, water and plumbing are being defined.Â
It is increasingly important that the teams work together to ensure that the designs are consistent and functional to match the requirements of the processes and the building’s occupants. One area we are pushing to explore is adding modularity in the design through creative layouts to allow flexible future expansion while minimizing first costs and maintaining resilience and redundancy needs. Â
How are engineers designing these kinds of projects to keep costs down while offering appealing features, complying with relevant codes and meeting client needs?Â
John Gregory Williams: The design-build approach is a big plus to meet the demands of these projects. Our approach of adding modularity in the design through creative layouts and having the team collaborate throughout is critical to limit initial investment. Â
Bryce Vandas: The engineer has to approach these types of facilities with the mindset that things will be changing and that the flexibility may be needed. Knowing the big gaps and making sure that those topics are being approached with the clients in the beginning is the best way to proceed. Many companies are looking to their consulting engineer to tell them what they need or to prompt them to look into questions that may become a concern down the road. By coming to the table armed with areas of concern and required data, it streamlines the process to truly understand what is needed so time and money don’t get wasted on the front end (and eventually down the road) making incorrect assumptions.Â
Jarron Gass: Conducting in-depth stakeholder meetings with all interested parties and finding common ground helps to anticipate potential stumbling blocks, particularly for preparing justifications or alternative means and methods requests and not holding up progress. Â