Make the best long-term decision
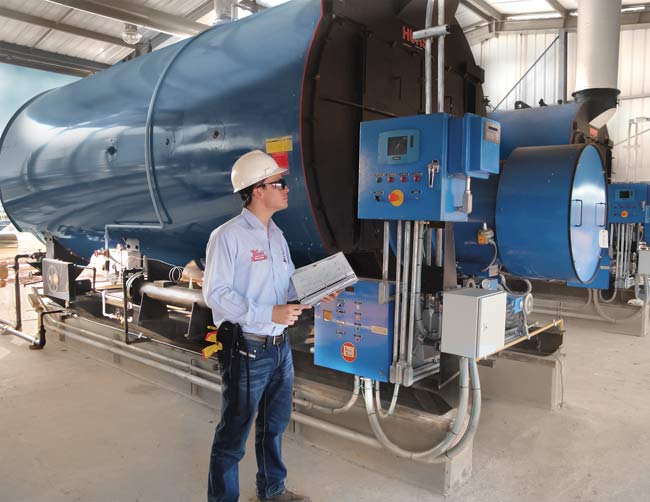
Few purchasing decisions for your facility have larger and longer-term energy consequences than purchasing a new or replacement boiler. Yet this purchase is often undertaken without complete consideration of all the options and possibilities. A typical industrial boiler, if properly maintained, has an operating life measured in decades. Thus, operating efficiency and suitability for the intended application are usually more significant considerations than just the first cost of the unit.
Emissions Rules Change the Game
Increasingly, air quality
regulations are causing operators of coal- or oil-fired boilers in industrial and institutional applications to switch to natural gas-fired replacement boilers. In the U.S. in 2012, the EPA promulgated the final rulemaking titled National Emission Standards for Hazardous Pollutants for Major Sources: Industrial, Commercial and Institutional Boilers and Process Heaters, commonly known as “ICI Boiler MACT.”
This rulemaking has made natural gas the fuel of choice (and often the only option) for these boilers. Fortunately, it comes at a time when natural gas is being produced in increasing abundance, at prices that are attractive. Further, many existing natural gas-fired boilers must be brought up to more rigorous emission standards. Thus many owners are studying the options in natural gas-fired equipment.
Look at Lifetime Costs
In a recent presentation at a Technology & Marketing Assessment Forum sponsored by the Energy Solutions Center, Ron Polidori from Clayton Industries stressed the importance of beginning with selecting the right boiler from the very beginning. He indicated, “I would say 30 years is a reasonable life expectancy. Many boilers will last much longer if they are well maintained. Sometimes, however, they will not last long at all if they are not properly maintained.”
He noted that in examining the total cost of typical natural gas-fired boiler systems over ten years, fuel cost typically represents 94% of the total expense, while the initial cost of the boiler represents only 4%, and upkeep and maintenance of the system is only 2%. It is important to select a high-efficiency boiler that is well-suited to the application, and to maintain it to operate at its peak efficiency with compliant emissions.
Detailed Evaluation Needed
Polidori emphasizes the benefit of doing a complete analysis of your steam or hot water needs before committing to a new or replacement boiler. This means an evaluation of your steam pressure and volume needs, the daily, weekly and annual cycle of boiler loads, and having a full understanding of special steam quality characteristics.
Polidori says, “Steam quality is important, as it describes the amount of water droplets that are present in the steam. Dry, saturated steam should contain no droplets, and 99% saturated steam would contain 1% water droplets. Steam with a high amount of droplets will have substantially lower heat content, and reduced heat transfer capability and therefore, results in lower efficiencies.” If the boiler is only producing 95% steam quality, the boiler will need to make 104-105 lbs. of steam rather than the 100 lbs. with a boiler at 99% steam quality.
Polidori adds, “Wet steam can also have detrimental effects on the steam distribution system – valves, controls, etc. If the droplets of water are not removed, you can experience premature replacement of these elements.” This is costly not only because of the direct expense, but also the loss of boiler use while this maintenance is being done.
Requirements May Have Changed
Industrial and institutional steam usage patterns often change over time. It may be today that your existing boiler is too large, too small or operates at the wrong temperature or pressure for current heating or process requirements. Modern package boilers are available in a wide range of sizes, and offer very good efficiencies even in the smaller sizes. It frequently is valuable to specify multiple boilers rather than a single larger unit to allow unit redundancy for greater plant reliability. This approach also allows owners to operate boilers in a modular fashion to stay near the peak boiler efficiency with varying loads.
Strategies for Seasonal Loads
Certain applications have a large steam or hot water requirement for only part of the year, but keep a large boiler operating at low load (and low efficiency) the rest of the year for water heating or other minimal demand applications. Often the large boiler cycles off and on during these low-load periods, further reducing its efficiency. For these situations, it is often beneficial to install a single, small “pony” boiler, allowing the large main boiler to be shut down seasonally.
In many parts of the country, particularly in the Northeast, in California, and in parts of Texas, air quality regulations require the use of ultra-low NOX burners as well as more rigorous exhaust gas monitoring. It is anticipated that some other areas will have these requirements in the future. Ask your engineer to include these considerations in your boiler installation or replacement plans.
Condensing Boiler an Option
For some applications, particularly comfort heating and low-temperature process applications, condensing boilers have become an important option. A condensing boiler offers very high efficiency by recovering the latent heat of vaporization from the boiler exhaust.
In natural gas-fired boilers this is accomplished with a feedwater return at temperatures below 135° F. If your feedwater return is usually above this temperature, there is no efficiency benefit with the condensing design, and in fact there can be a cost penalty because condensing boilers necessarily use more expensive stainless heat exchangers for the wet condensing portion.
Economizers Often Make Sense
Even if you do not have an application suitable for a condensing boiler, there are often major efficiency improvements possible with the use of a boiler economizer to extract more heat from the boiler exhaust. Economizers are available in both condensing types and non-condensing designs, and in some cases are offered by boiler manufacturers as integral elements of the boiler.
The economizer is most frequently used to preheat feedwater, but can also be used for potable hot water, process water, or to heat makeup water for applications where there is significant utilization of live steam in a process. Ask your engineer and boiler manufacturer for the information on the appropriate size and type of economizer. Paybacks on a boiler economizer can be as short as six months in many cases.
Combine Conventional and Condensing Systems
Chad Fletcher from Hurst Boiler was recently a presenter at a Technology & Market Assessment Forum sponsored by the Energy Solutions Center. In his presentation, he discussed the merits of both conventional (non-condensing) and condensing economizers. He pointed out that conventional economizers have lower investment cost, easy installation and very low maintenance. Condensing units have the potential for a higher level of energy recovery, but can be more costly to purchase and install.
He offered the possibility of a hybrid economizer solution, with a conventional economizer collecting most of the sensible heat from the exhaust stream, then a smaller condensing unit for the final stage of heat recovery. Fletcher indicated that economizers make the most sense in boilers sized larger than 50 hp.
Burner Choices
Get Help with the Decision
Combustion on the surface of the burner for optimum radiant energy with very low NOX creation. These burners typically are available with turndown ratios down to 4:1. The boiler burner can be purchased as part of the boiler package, or can be sourced separately. Especially in smaller vertical, horizontal and tubeless package boilers, it is important to match the burner to the geometry of the heat exchange surface. Often these boilers are equipped with high-efficiency factory-specified burners.
Obviously the process of selecting the right boiler is complex, and very dependent on the application. Tools for scoping and modeling boilers for your specific plant configuration are available from DOE’s Division of Energy Efficiency and Renewable Energy (EERE). Look also for help from energy consultants, especially if you are in an ultra-low NOX area.
Boiler manufacturing companies also offer valuable help in sizing and finding a boiler with the ideal steam characteristics. If your boiler is due for replacement, and particularly if you are changing from another fuel to natural gas, it is important to begin with choosing the right boiler. It’s a decision you’ll live with for decades.
MORE INFO:
Cleaver-Brooks
DOE Boiler MACT Assistance
Energy Solutions Center Boiler Burner Consortium