Ginolis Ltd. in Qulunsalo, Finland, has converted existing rapid testing equipment lines to produce COVID-19 testing kits using automation technology and PC control.
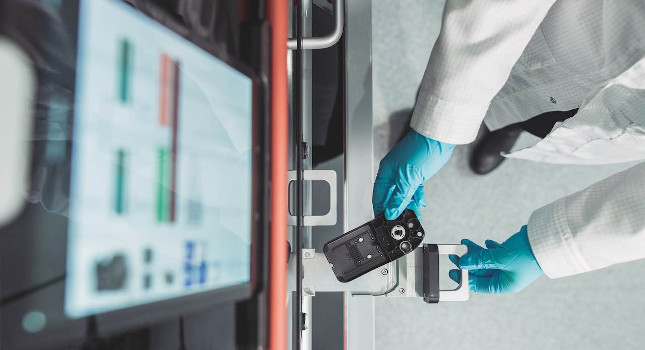
To fight the coronavirus pandemic, Ginolis Ltd. in Qulunsalo, Finland, has converted existing rapid testing equipment lines to produce COVID-19 testing kits. Automation technology from Beckhoff contributes significantly to the production equipment’s modularity, flexibility and high quality.
Since its foundation in 2010, Ginolis has offered high-quality automation solutions for the production and assembly of medical devices such as point-of-care diagnostic equipment, micro-fluid devices, insulin pumps, medication dispensation devices and test cartridges. Rapid diagnostics is a quickly growing field in health technology, according to Ginolis CEO Teijo Fabritius, but the need became even more urgent with the spread of COVID-19.
“At its core, our business involves automating the manufacture and inspection of rapid diagnostic products. Such medical consumables are currently in high demand around the world,” Fabritius says. “Our high-quality automation solutions don’t just lower the production costs of these consumables. The faster and more accurate tests also simplify their handling and increase their reliability.”
Modular production lines adapt to COVID-19 testing
All of Ginolis’s production lines are modular, scalable and tailored to customers’ specific requirements, which was crucial for the changeover to COVID-19 rapid testing. “Through our modular approach, customers do not need to worry about future volume requirements when they invest, because to increase capacities, they only need to add more modules,” Fabritius says. “The various standard modules for things like assembly and inspection provide a huge competitive advantage since they are usually available and can ship very quickly. We have lead times of only a few months, which is very unusual in our industry.”
An embedded PC with controlled the individual production modules. Most production lines have several hundred axes of motion and hundreds of input/outputs (I/Os). The individual modules generally have 50 to 100 EtherCAT I/O connection points and multiple drive axes controlled via servomotor terminals, stepper motor terminals and BLDC motor terminals. The intelligent eXtended Transport System (XTS) added high-end mechatronics technology to Ginolis’s high-capacity assembly lines.
PC-based control is integrated, compact and powerful
“PC-based control from Beckhoff allows us to seamlessly integrate multiple software-based functions into the automation system,” Fabritius said. “In addition, the embedded industrial PC systems are very compact and powerful. Particularly where automation components are concerned, compactness is critically important since space is usually at a premium, especially in cleanrooms. And the more functions we can integrate through software, the more compact, flexible and easily upgradeable we can make our solutions. In addition, Beckhoff has developed many additional products that fit well into our automation concept, such as the software-based TwinCAT Vision real-time image processing system and the compact EJ-series EtherCAT plug-in modules that speed up installation considerably.”
– Edited from a Beckhoff press release by CFE Media.